Executive summary
This paper looks into the general concept behind the LCC analysis, its importance and purpose of such an undertaking in any organization setting.
The analysis is based on the case study of a chain store company, which specializes in the sale of household goods such as furniture, electronics, kitchen appliances and furnishing items. The chain store has more than 2000 products that are distributed in different outlet stores throughout UK (Chandler 2004).
The analysis entails the introduction of a new inventory system for the company with the intention of streamlining record keeping in the organisation.
The rationality of the system lays on its ability to monitor all entries, hence ensuring that the company’s data is up to date at all times. This makes it easy for the company to compile reports, and further serves to boost accountability.
The focus of the analysis is on the alternative support options that are likely to improve on the sustainability of the system. For this study, three options were identified which included corporate management, insurance and manufacture’s support.
To come up with the most efficient method in terms of cost, the three options were analyzed. During analysis, the author identified the pros and cons of each identified option.
The life cycle cost for the options spanning a period of 8 years was also taken into consideration. Based on the results of the analysis, manufacturer support was identified as the most appropriate approach because of the costs and effectiveness of the support instrument.
Introduction
According to Langford (2007), the Life Cycle Cost (LCC) analysis is a tool used to evaluate the overall cost of a system or a specific product over its entire lifespan.
This method allows one to identify with the elements entailed in the lifespan of the system and thus helps in the calculation of the costing of each incorporated element.
The main purpose of employing the LCC analysis is to identify the most cost effective approach that caters for all the required resources over the entire lifespan of the system.
This therefore provides an essential systematic approach for identifying the required elements and quantifying them thus accessing the available alternative options before employing the most qualified option in terms of cost effectiveness (TAM, 2004).
Ghoshal and Greeff (2004) assert that it is essential for all companies to employ the LCC analysis on any new systems that they need to incorporate in the organization. Such an action would allow the company to identify any substantial costs that the business is likely to incur in future.
As such, Ghoshal and Greeff (2004) recommend the LCC analysis should be implemented right from the design phase of any new project that a company intends to undertake.
By using such an analysis, the company would be in a good position to comprehend the extent of costs related to research and development, production, operation and support and product disposal as illustrated in figure 1.
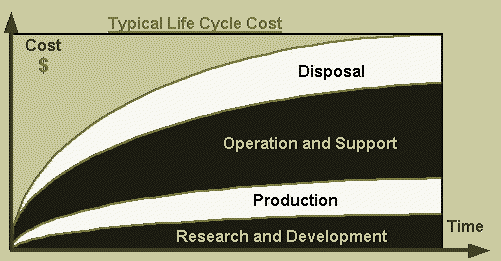
With reference to LCC analysis, this research work looks into the acquisition of a computerized inventory system for a chain store. The main purpose of this inventory system revolves around managing the acquisition of merchandise and the sale of the same.
This system will therefore concentrate on managing procurement records for the different outlet stores of the chain store. The study partially intends to verify claims by JTC (1999) that alternative support options can be utilized to improve on the sustainability of the system.
Background information
According to Müller (2003), an inventory is as a representation of a company’s raw materials, work in progress or finished goods that are ready to be dispatched into the market.
An inventory can be simple or complex depending on the companies mandate and the amount of goods received or activities that take place in the company’s premises per day.
This therefore indicates that the bigger the company in terms of production, the more complex the inventory system. The amount of money invested in the system determines the nature of the inventory.
An inventory system is important for organizations that face the quagmire of poor cash flow, poor management of information, poor communication between different departments or units within the organization, and poor management of lead times (Toomey, 2000).
Highly efficient inventory systems help organizations to meet their objectives especially in regard to meeting customer satisfaction, and realising a return on invested capital.
The case study in this case is a chain store, which has 260 outlet stores within the UK market. The mandate of the company is to supply household furniture and related appliances.
Among the items stocked in the different stores include household electronics, kitchenware and in house furnishes. The chain store range of products is more than 2000. With this high number of products and outlet stores, inventory management is quite a daunting task.
Over the years, the chain store has heavily relied on a computerized system of inventory. Notably however, different stores uphold different inventory keeping method, hence meaning that the outlets are not synchronised.
As such, compiling this information into one system located at the headquarters has brought about many discrepancies and conflicts since different outlets have employed different systems.
Further, it takes a lot of time before the company can come up with an annual report on sales due to the high number of sales units arising from the different stores that need to be incorporated into the headquarters database.
Based on the aforementioned reasons, it is imperative that a centralized inventory system is put in place in order to stream line all the inventories entered in each outlet store. Thus, the main objective of setting up an efficient computerized inventory system lies in the ability of the system to be predictable.
This will actualize the ideal situation of any given company by building capacity on proper planning based on the inventory records (Müller, 2003).
Further, the system will improve the chain store ability to study the trends of how the goods are selling at specific outlets and thus making it easy to predict market trends without necessarily succumbing to fluctuations in demand for the products.
This will also help the chain store to manage all its inventories from a central place and thus reducing on the cost of inventory systems as opposed to establishing different systems for the different stores (Toomey, 2000).
The systems will encompass a high-tech version of the inventory. This type of inventory system allows the headquarter to monitor the inflow and outflow of goods at all the outlet stores like an online stock exchange market through a centralized system.
The rationality of the system works on an instant entry basis meaning that every entry entered in the inventory system from any outlet store reflects immediately on the main system located at the headquarters.
All that is required is some support computers in the outlets and scanners that are used to read the codes of the items being stocked into or out of the stores. The support computers will then be networked with a main server at the headquarters.
This will ensure that all information scanned in the different stores is sent directly to the server, with the store retaining a copy of the data of the items. This way, the chain store will have inventory data for all the outlet stores at any given time.
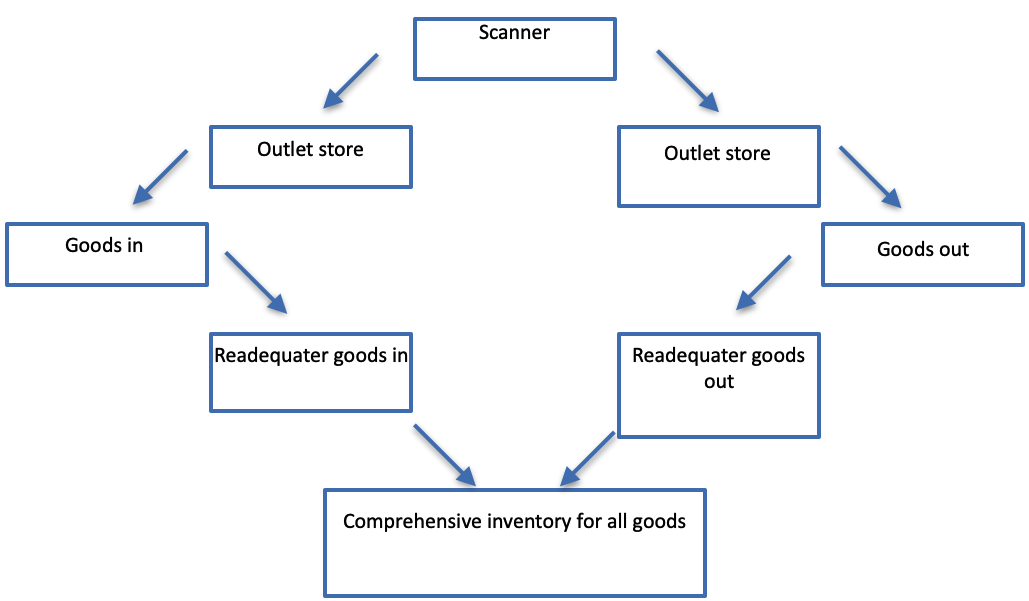
The implementation of an inventory system is anticipated to incur costs for concept and definition, design and development, manufacturing and installation, operations and maintenance and finally disposal costs.
All this costs are calculated based on all outlets included and on the anticipated lifespan of this system, which is set at 8 years.
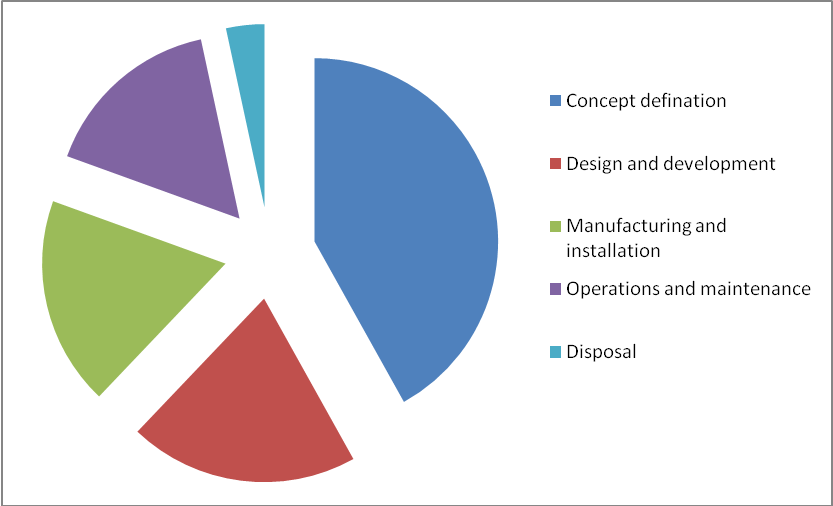
Sustainability of the system
According to Bell and Morse (2008), sustainability of a system refers to the ability of a given system to maintain its production capacity at a level that is equal or greater than the average output associated with the system.
With reference to this inventory system, sustainability refers to the capacity of the system to streamline the inventory of the chain store.
Bell and Morse (2008) illustrate that it is important to define the space and time over which sustainability of the project can be met. In this case, space is defined as the overall perimeter that includes the area covering all the outlet stores affiliated to the chain store.
Time on the other hand refers to the lifespan that the system is expected to serve the company efficiently. In this case, the time estimation is approximately eight years.
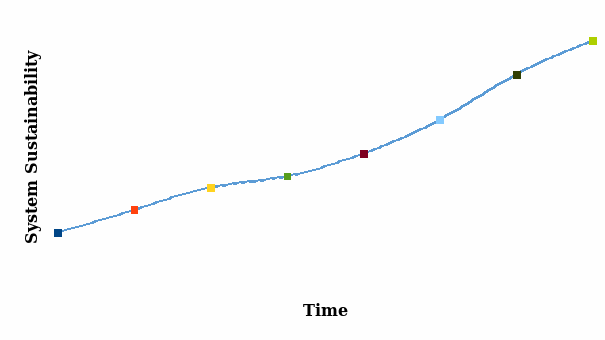
The main purpose of this research is to conduct an LCC analysis on the support services that can be utilized in ensuring the sustainability of the project. Among the identified support services include insurance, manufacturer support and the use of corporate management.
These support systems are essential for the continuous monitoring on the system performance. Ideally, close monitoring will enable the company to remedy any situations that may compromise the optimal performance of the system.
Corporate management
Bhatia (2000) asserts that cooperate management involves the organization and functioning of a given management team to meet the goals and objectives of the organization.
It involves proper planning, designing, outsourcing implementation and evaluation of projects in progress. This in house initiative can work to towards enhancing the sustainability of the system.
The advantage of this approach includes its capacity to promote proper planning and designing of the system. This can be achieved by employing specialists in the designing, implementation and evaluation phases of the project.
The amount of time and innovation employed in the realization of the system project will dictate the extent of opportunities and threats depicted by the whole system.
Thus, the management should ideally to maximize on improving efficiency and sustainability by dealing with any anticipated difficulties before the onset of the project.
The success of cooperate management in ensuring system sustainability is determined by the attitudes and dedication of the respective decision and policy makers in the organization (Bhatia, 2000).
Therefore, the success or failure of the project is highly dependent on the type of leadership in the organization and the effectiveness of communication strategies within the organization.
Insurance Services
According to Outreville (1998), insurance refers to the protection/cover from a threat that would otherwise jeopardize the functioning of the system. There are many risks associated with such a system.
They include the risk of loss of data, system malfunction, lack of coordination from the outlet systems with the headquarter system, among others. For purposes of protecting the overall mandate of the chain store, it is important to insure the system against obvious or unforeseen risks.
The main disadvantage of this approach is entailed in the fact that the organisation will have to guard itself from major losses in case the system malfunctions.
While as the insurance cover guarantees compensation should such an occurrence materialise, it is worth noting that the company will have to pay monthly premiums to the insurer. As such, the setback of this support service is the expense incurred in the event of insuring the system.
This is attributed to the fact that most insurance companies charge a lot of money to insure such systems. Further, in the event that the system functions properly without any malfunction, it is not possible to get a refund of the already paid out money to the insurance company (Albertini & Barrieu, 2009).
Manufacturer’s Support
Manufacturer’s support can be realized through after sales services that can either be provided by the manufacturing company on a free arrangement, or at a subsidized price. Such services are intended to maintain the system and support its running.
The support services can be in form of spare parts, repairs, servicing, or system buffers among others (Hill & Jones, 2008a). Most manufactures offer such services as an incentive to entice their clients while others view this as a business opportunity to further the mandate of the manufacturing company.
The advantages of this support strategy involve the subsidized fee for spare parts and any needed repairs. This is attributed to the fact that most manufacturers tend to retail spare parts and their services to loyal consumers at a lower price as compared to the market price.
Further, manufacturers are better placed to deal with emerging issues of their own innovations thus improving on the internal validity of their services and thus the improved sustainability of the system (Hill & Jones, 2008b).
The limitation of this approach is that working with one specific manufacturer can compromise the efficiency of the system. This would especially be the case when the manufacturer service provider is not fully conversant with the functioning of the system.
The fact that some manufactures retail their spare parts and support systems at a very high price, presents yet another disadvantage. According to Hill and Jones (2008b), high prices discredit the rationale of out sourcing the purchase of spare parts or repair services.
Accessibility to manufactures support may be limited by distance difference especially when the manufacture is not able to access all the chain store outlets.
Conclusion
From the LCC model developed for the analysis of the life cycle costs of the different processes and activities involved in the acquisition, implementation and management of the new system, it was clear that there were different costs to be taken into consideration for the whole system to be effective and worthwhile (JTC, 1999).
Since the system would spare the company losses previously incurred due to miscalculations and lack of proper records, it would serve as a major milestone to the company’s performance.
As such, the system is highly recommendable since the disadvantages associated with its implementation do not surpass the benefits the company would earn from it.
Notably however, the investment alone cannot help solve the problems of the company. Hence, there is a need for the company to invest more into the maintenance, management and operation of the system in order increase the life cycle of the system.
The analysis has shown that the manufacturer support, method of maintenance, and support are all appropriate since the system is relatively cheap and involves fewer risks (Chandler, 2004).
Recommendation
The company should implement the system and use the manufacturers of the system to provide the required maintenance and support services. This way, the system costing will be free from unplanned costs and cushioned against frequent economic changes.
As TAM (2004) observes, systems that are cushioned from unnecessary running costs and needless market forces stand a higher chance of providing their implementers with optimal benefits spanning their (systems) entire life cycles.
References
Albertini, L., and Barrieu, P. (2009) The handbook of insurance-linked securities. Sussex, John Wiley and Sons.
Bell, S., and Morse, S. (2008) Sustainability indicators: measuring the immeasurable? 2nd edition. London, Earthscan.
Bhatia, R. (ed) (2000) Encyclopedia of corporate management, New Delhi, Anmol.
Chandler, F. (2004) Life- Cycle Cost Model for Evaluating the Sustainability of Bridge Decks. Web.
Ghoshal, R., and Greeff, G. (2004) Practical E-manufacturing and supply chain management, Oxford, Elsevier.
Hill, C., and Jones, G. (2008) Strategic management: an integrated approach, 9th edition. Ohio, Cengage.
Hill, C., and Jones, G. (2008a) Strategic management theory: An integrated approach. Boston Houghton Mifflin.
JTC (1999) Life cycle costing: an application guide. Web.
Langford, W. (2007) Logistics: principles and applications. New York, McGraw-Hill.
Mtain, A. (2009), Life Cycle Cost Analysis. Web.
Müller, M. (2003) Essentials of inventory management. New York, Amacom.
Outreville, F. (1998) Theory and practice of insurance. Massachusetts, Kluwer Academic Publishers.
TAM (2004) Life Cycle Costing Guideline. Web.
Toomey, J. (2000) Inventory management: principles, concepts and techniques. Massachusetts Kluwer Academic Publishers.