Executive summary
The effect of contaminants affecting workers is an issue of global concern. Tremendous efforts have been advanced to govern standards of exposure to risks at the work place.
This paper analyzes the contaminants formed in an environment where bitumen is being used. The use of Control banding technique in managing risks also investigated.
The effects of heat stress and methods to combat this problem at the work place are discussed herein. Finally, the paper investigates noise, causes of hearing loss and audiometric testing.
Developing an assessment strategy for bitumen (asphalt)
The health of an employee is directly proportional to his productivity in any firm or working environment. Thus, it is imperative to ensure that proper care of the working environment is emphasized.
There are many hazards or risks that may interfere with the health of an employee in the working environment, reducing their viability. Heat stress, lack of protective safety-gears, and exposure to toxic substances forms some of the core health hazards (Tilman 2007).
These may impair the entire body or part of the body especially the eyes or ears. For a mine that produces asphaltic fumes and odors, the following strategy can be employed.
- Assessing the magnitude of the fumes produced- finding out the level of available hazard will enable the determination of the relevant combat technique.
- Reducing the time of exposure for the workers and establishing first aid measures.
- Engage engineering controls to lessen the fumes.
- Providing workers with the relevant safety gears such as helmets, goggles, apron, and other necessary protective equipments.
- Prioritizing the tests aimed at establishing any emerging effect on the health of the workers.
- Coming up with programs to educate the workers on the risks involved
- Encouraging protective measures that will reduce the chances of risk-since the fumes are flammable in nature, request workers to avoid issues like cigarette smoking at the site.
To develop the strategies above using AREC i.e. anticipate, recognize, evaluate and control. In using asphalt for road construction, we expect production of fumes and odors. Production of carbon dioxide, carbon monoxide and hydrogen sulphide during the operations may be a health hazard.
Therefore, we ought to be set to combat the fumes and have available water sinks for workers to wash their eyes in case of irritation. The flammability of the fumes should also be anticipated, hence ensure that the working area is free from any irrelevant fires such as cigarettes fires.
The contaminants identified in this case are particulate in nature. Since the impact of the fumes may not be observed by the naked eyes, use of control banding would be an acceptable method for this hazard.
The amounts of toxins in the fumes are analyzed using the control bands, and compared against some set standards (ACGIH, 2011). If the toxicity exceeds the acceptable limits, then the relevant measures would be incorporated to minimize health hazards.
Before taking any measure, it is decent for a person to evaluate the magnitude of the action required. This will help in proper planning. The evaluation is followed by control actions, which may even, imply a closure to the entire project or change of materials (Paustenbach 2000).
Secondly, once certain risks are anticipated, the workers should be sober enough to recognize any appearance of a potential risk. This will include abnormal effects in a worker or any other appearance of the risk.
Contaminants produced in the working environment include spills into water systems, gaseous compounds such as CO, CO2 and H2S. To monitor these substances, the workers should ensure that the spills are not directed to waterways, sewers, and drainage systems.
Avoid usage of hot bitumen since it can cause burns to the skin. All personnel working with the compound should be properly trained. The fire fighters to deal with any outbreak of fire should have proper protective gears.
First aid measures must be available at the working site to deal with any emergencies. Inhalation of some of the contaminants produced may result to sudden collapse. Thus, medical practitioners should be available at the working environment to deal with emergency issues.
Thus, to monitor the contaminants proper storage and handling should be emphasized. Accidental release measures, personal handling and fire fighting measures, should also be encouraged.
In the laboratory, fumes are generated to test the effects of the asphaltic fumes (Malchaire 1999). From documented evidence, there are conflicting data concerning the carcinogenic effects of asphaltic fumes.
Some researchers have said that the fumes have no notable carcinogenic effects while others have said otherwise. However, the fumes are known to cause eye irritation, gingivitis and other eyes and lungs related infections.
Other tests done in the laboratory include density test, H2S tests and tests for stability of the compounds. Example
The worker works a normal 5 shifts each week and 12 hours for every shift.
Substance: bitumen
Exposure Standard: 5 ppm, 8 -hour TWA (ACGIH, 2011).
Work shift: 12 hours
Solution:
Adjusted exposure standard for 12 hour shift =8 x (24 – 12) x Exposure standard (8 – hour TWA)/
(16 x 12)
= 8 x (24 – 12) x 5ppm
(16 x 12)
= 2.5 ppm (12-hour TWA)
Since the safe yield of 5ppm is not exceeded, then, the shift can be made on the basis of exposure of to bitumen.
In case the shift changed from 8 to 12 hours, this will imply longer periods of exposure to the fumes. There are standardized limits to which the workers can be exposed to a given contaminant.
Therefore, it would only be possible to extend the working shift if the workers are not adversely affected by the change in shift. To determine the viability of this brief and scala model is suggested (see details in the appendix).
Control banding
Control banding can be defined as a model that qualitatively or semi-qualitatively assesses and manages risk so as to ensure the health and safety of workers in the workplace (Nelson 2005).
The method encompasses the use of administrative controls, engineering controls and personal protective equipments to ensure safe handling. One of the initial control banding methods used is the UK Health and Safety Executive (HSE) referred to as the Control of Substances Hazardous to Health (COSHH) Essentials.
COSHH Essentials is available online and can be accessed free of charge (UK Health and Safety Executive 1999). COSHH Essential approach helps in assessing the level at which the need for risks can be identified and control measures put in place.
Control banding is used to compute the range of a risk against some predetermined value. The employee working in an organization would remain effective as long as certain parameters of safety are not exceeded (HSE 2006).
In industries, a performance based approach to employee protection is used. This approach encompass the three aspects of control banding: engineering controls, administrative controls and procedural controls.
Different chemicals are assigned different control bands in pharmaceutical industries in an effort to safeguard the health. The standardization of engineering controls is still going on in the industry to provide vital data for benchmarking.
In general control banding provides an all-round approach to promote safety handling by setting up the right rules. The International labor Organization (ILO) provides guidelines and a toolkit to govern the use of control banding (Nelson 2005).
The critical limitations of control banding can be attributed to lack of available data for benchmarking. The method requires use of engineering controls of which there are no standardized measures. Determination of enrolment criteria for Performance –Based Exposure Control Limit (PB-ECLs) also poses a limitation.
Most countries use the same (PB-ECLs), however, depending on the technology used by the manufacturing company the bands may differ slightly. The chemical control toolkit was originally made to suit small firms; nevertheless, the toolkits are now being made industry specific.
The acceptance of control banding can not be over amplified. Initially, the method was only applied in USA and EU. However, the ILO is promoting it to find global acceptance. Many countries have adopted it and are working hard to ensure safety in their work environments and occupational safety.
The COSHH Essentials developed by the UK ensures that even the small sized enterprises benefit since they may not afford the services of a resident occupational hygienist (Nelson 2005). International conferences to support the use of control banding have also been held recently.
Availability of online links that promote the use of control banding for instance, HSE website provides an avenue for people to hold discussions and debates on the acceptability of control banding.
The US National Institute of Safety and Health (NIOSH) and Center for Disease Control and Prevention (CDC) offer information and links via their website on control banding. All these efforts coupled together have made a whopping landmark in promoting acceptance of control banding.
An example of usage of control banding is in the pharmaceutical industry. The pharmaceutical industry began using this concept long ago, though it was under different definition.
Pharmaceuticals compounds were subjected to different alternatives in setting numerical exposure limits (OELS) such as occupational exposure bands (OEBs), mostly for compounds with limited information. The PE-ECL categories and associated recommendations are based on experiences with similar substances.
Assuming the environment has not changed, the previous performance of hazardous substances remains unaltered. Matrices have been developed to determine the control strategies for use with each PB-ECL category (ISO 7726).
Effects of heat stress and regulatory techniques
Exposure of workers to extreme thermal conditions is a health hazard. The working environment should always be maintained at levels where the prevailing temperature conditions are conducive for the workers. The performance of workers is negatively affected by either too cold or too working environments.
This is amplified in mines where at times the air is not sufficient enough for the miners (Sawka 2000). To assess and combat the heat stress, it is imperative to analyze the heat in the surrounding using the heat balance equation. This would help strike a balance between the heat lost and the heat gained by an individual.
Once the heat situation on the employees is assessed, then the right measures can be adopted. According to the national institute of occupational safety and health (NIOSH), the following measures are recommended for hot environments (Brake and Bates 2012).
- Acclimatize the workers recovering from illnesses or from vacations.
- Implement a work/rest regiment matched to the severity of the worker’s heart exposure.
- Scheduling hot operations for the coolest parts of the day.
- Making salt and drinking water available so as to replace the effluents of sweat.
- Making protective clothing available to workers.
- Reducing environmental heat by engineering controls.
- Monitor the environmental heat at the site.
- Performing periodic medical examinations to discover those at risk.
- Educating workers and supervisors about preventive measures and early detection methods of heat related disorders.
Noise and audiometric testing
Noise can be described as any unwanted sound that may cause damage to the human hearing. Noise is measured in decibels. The decibels measure the pressure levels of the noise/sound being produced by the source. The range of the sounds produced is enormously large as a result a logarithmic scale is used.
Sound pressure can be described as the varying component of pressure in a sound field. Hazardous noise refers to noise that exceeds the exposure standard for noise in the work place (Tilman 2007). This kind of noise affects the proper functioning of the inner ear; this may result to temporary hearing loss.
An exposure to an extremely loud impact or explosive sound may result to permanent hearing loss (Chan Wong & McPherson 2004). The level of hearing loss is determined by the length of exposure time, intensity of the noise and the susceptibility of the individual (Brake and Bates 2012).
Documented evidence also reveals that there extended exposure to arm vibrations may also lead to hearing loss. Ototoxic activities such as weapon firing, degreasing, fire fighting, fuelling vehicles and air crafts may lead to hearing loss. The figure below shows the various parts of the human ear.
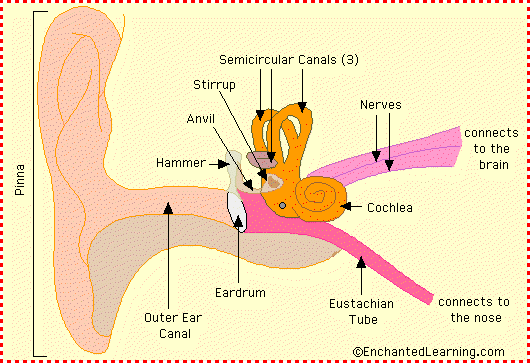
The ear consists of three main parts, the outer ear, middle ear and inner ear. The outer ear consists mainly of the pinna whose core function is to trap sound waves and directs them to the middle year.
The middle ear holds the eardrum which forms the part that receives the sound waves before sending them to the brain through the auditory nerves for interpretation. If the eardrum is impaired then a person will suffer from hearing loss. It is the eardrum that detects the intensity of sound received.
Use of certain medications and exposure to certain chemicals in industries may lead to hearing loss. The chemicals enter the brain through the cochlea and damage the cells in the inner ear leading to hearing loss. The combination of noise and these substances raises the chances of hearing loss.
The average standard exposure is 85 db over 8 hours; however, the susceptibility of the individual would vary depending on the loudness of the noise (Standards Australia, AS 1259.1). There are stipulated times within which, for a given level of noise, hearing loss will not occur.
Audiometric testing means the use of monaural pure tone air conduction threshold tests to determine the hearing threshold levels of a person. Initially, it was developed to model the ear in response to low sound ranges. Today sound is measured using A-weights.
In Australia, a standardized frequency response applied in sound measuring instruments is used (ISO 7726). The model was initially, developed for modeling the human ear response at high sounds. In order to reveal the cause of changes in hearing abilities of employees, audiometric tests are carried out.
The test is not a preventive mechanism and is only carried out after a consensus involving the employer and workforce of the company or organization. Audiometric testing program should be available to any employee who is likely to be exposed to prolonged noise irrespective of whether they use hearing protectors.
Audiometric testing should be carried out by qualified experts selected by the leadership of the organization in collaboration with the employees (Standards Australia, AS 1259.1). The procedures and equipments used should be inline with the specifications quoted in part 4 of Australian / New Zealand standard.
The testing scheme should include a reference test followed by periodic monitoring tests. Within the first 12 months of reference test, the monitoring test should be carried out to compare the results. In case, the change or swift in threshold frequency is not significant then the monitoring tests should be done annually.
While managing hearing loss using audiometric metric testing, employees hearing changes are tracked. In case of notable variations in hearing frequencies, the employer is liable to put measures that will protect the employee from further hearing risk.
The results of the changes in hearing frequency should be discussed between the employer and the employee. Critical measures will then be endorsed to curtail further employee hearing risk. These will include administrative controls and process equipment controls (ASTM D6494-99 2010).
According to Australian standards on health and risk, it is a requirement not to exceed an exposure period to a hazard (every requirement must be complied with). Every person in the workplace has a duty to assess risk and implement a specific control measure (Standards Australia, AS 1259.1).
A duty holder has a responsibility of assessing the risk that may result into a risk to health and safety. The duty holder must reduce the risk as long as is practically possible. If the duty holder finds it impractical to eliminate the risk the hierarchy of control measures to safety and health is applied.
The hierarchy of controls used according to Australian standards entails:
- 1. Eliminating the hazard completely. For instance, – get rid of the dangerous machine.
- Substituting the hazardous substance with a safer option. For instance, – substitute the old machine with a safer one.
- Isolatingthe hazard from people who could be harmed. For instance, – the machine can be operated in a remote environment.
- Engaging engineering controls to minimize the risk. For example, – attach protective guards to the machine to protect operators.
- Using administrative controls to lessen the risk. For example, – educate workers on proper usage of the machine.
- Using personal protective equipment (PPE). For instance, – wear helmets, gloves and goggles when operating the machine.
Other regulations in this health and safety are review of control measures (constant review to the work environment is encouraged), maintenance of control measures (implemented control measures ought to be reviewed constantly to ensure that they remain effective).
It is a duty to maintain the working environment free from risk (Australian Standards / New Zealand Standards 2011).
Conclusion
In respect to the above arguments, one can conclude that there is a need to adopt a global approach to deal with problems related to hazards at the work environment. It is the duty of every participating party to ensure that they work toward the protection of others.
By so doing, the disorders such as hearing loss, eye-based disorders and lung diseases will be significantly reduced. The adoption of control banding would play a central role in standardization of the procedures and standards to combat hazards.
References
ACGIH 2011, TLVs and BEIs: Threshold Limit Values for Chemical Substances and Physical Agents and Biological Exposure Indices, American Conference of Governmental Industrial Hygienists, New York.
ASTM D6494-99 2010, ‘Standard Test Method for Determination of Asphalt Fume Particulate Matter in Workplace Atmospheres as Benzene Soluble Fraction’, Scope Audiology, vol. 43, pp.323-329.
Australian Standards / New Zealand Standards 2011, Occupational noise management, Part 4: Auditory assessment. Web.
Bohm, A & Chaudri, D 2000, Securing Australia’s future: an analysis of the international education markets in India, IDP Education Australia, Sydney.
Brake, D and Bates, G 2012, ‘Fluid losses and hydration status of industrial workers under thermal stress working extended shifts’, Occup Environ Med. vol. 60 no.2, pp.90-6.
Chan Wong, E & McPherson, B 2004, Occupational hearing loss, Australian Institute of Occupational Hygienists, Tullamarine, Australia.
HSE 2006, COSHH Essentials, UK Health and Safety Executive. Web.
ISO 7726, Thermal environments – Instruments and methods for measuring physical quantities. Web.
Malchaire, J 1999, Evaluation and control of warm working conditions, BIOMED.“Heat Stress.” Conference, Barcelona.
Naumann, B 2005, Control Banding in the Pharmaceutical Industry, Australian institute of Occupational Hygienists,Tullamarine.
Nelson, D 2005, Control banding: Just the FAQs. The Synergist. Health and Safety Executive: COSHH Essentials, London.
Paustenbach, D 2000, Occupational Exposure Limits, Pharmacokinetics and Unusual Work Shifts, John Wiley & Sons, New York.
Sawka, M 2000, “Hydration effects of thermoregulation and performance in the heat”, In: Lau, W, (eds), Proceedings of the International Conference on Physiological and Cognitive Performance in Extreme Environments, Defense Scientific and Technology Organization, Rawalpindi, pp. 42.
Standards Australia, AS 1259.1, Acoustics – Sound Level Meters, Part 1: Non-integrating, Standards Australia. Web.
Structure of the ear. Web.
Tilman, C 2007, Principles of Occupational Health & Hygiene, An introduction, Allen & Unwin, Auckland.
UK Health and Safety Executive 1999, Under thermal stress working extended shifts. Web.