Role of Systems and Operation Management in Airbus
“In to-day’s global manufacturing environment the challenges companies face are significantly different than what they did decades ago” (Aberdeen Group, 2008). Effective operation management is one of the tools to meet these challenges. The scope of operations management in any organization includes the transformation of materials and other resources into the final output. Such conversion process normally uses physical resources. The objective of managing the operations is to derive the desired utilities to the customer. At the same time, operation management has to meet the organizational objectives of effectiveness and efficiency.
Operation management differs from other activities of the organization. Operation management encompasses the processes where inputs are turned into outputs. Management of manufacturing involves executing different tasks by different people. To coordinate all the tasks and activities manufacturing must be viewed as a system. “A system is the action of two or more parts as they operate together,” (De Luca and Sanders, 2009). Generally, the manufacturing system model is described as consisting of four subsystems namely input, process, output, and control.” The following figure illustrates the “input-process-output” model of a manufacturing system.
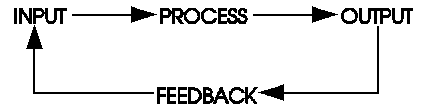
In the case of Airbus, the manufacturing system consists of the inputs from two broad systems of design and manufacture. Therefore, in the design and manufacturing of the A380 aircraft, there are two subsystems involved. Each of these subsystems represents an “input-process-output” model. The inputs of the design subsystem include the human resources being the technicians from Germany and France assisted by other lower-level workers. Software used in the completion of designing the aircraft represents an input. The process includes using the technical expertise of the technicians from both the countries and the use of software for finalizing the design. A complete and efficient design of the aircraft is the output of this model. Because of reasons of brevity, this report considers only the design subsystem, as the manufacturing subsystem consists of several inputs and processes.
The delay in launching the aircraft was due to a lack of coordination. There was a total lack of integration in the two processes involved in the manufacture. The design team and manufacturing team did not coordinate their activities, which led to the delay in launching the A380 as per schedule. The reason for the lack of integration was the use of incompatible software used by the German and French factories to design the wiring requirements of the aircraft. The company instead of streamlining the process of design by efficient processes used less temporary and less efficient processes, which hindered the progress of design development greatly. There was the need to share data at the initial stage to gain time savings (Tennant and Roberts, 2003; Ainscough et al, 2003; Baba and Nobeoka, 1998). Virtual collaborations greatly benefit information sharing (Chudoba et al, 2005; Majchrzak et al, 2005; Mertins and Jochem, 2005)
However, the lack of coordination between design and manufacturing processes in Airbus A380 was because of the weakness in the decision-making process in Airbus organization. Decision-making in a manufacturing environment may be strategic, operational, or tactical. Strategic decisions are of long-term nature and they set the direction for the entire organization (Scribd.com 2011). While strategic decisions are broad in scope the tactical decisions are narrower in scope. Tactical decisions are those, which focus on specific departments and tasks. Tactical decisions cover the specific day—to—day issues and they are concerned with quantities and timings of accumulation and provision of specific resources to aid production. These decisions in the context of a manufacturing organization are routine and are taken more frequently than strategic decisions. Tactical decisions are medium-term decisions aimed at arriving at ways of implementing strategic decisions. Operational decisions are short-term decisions covering the implementation of tactical decisions (Tutor2u). Organizational members at different levels are expected to take decisions to achieve the overall organizational objectives.
The following figure illustrates the levels of decision-making.
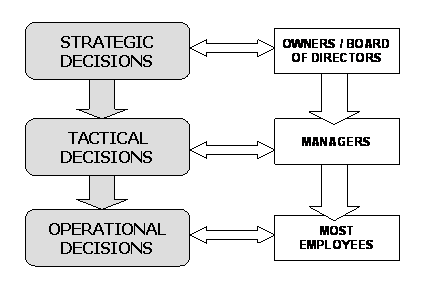
In the Airbus design system; there has been a severe deficiency in strategic decision making on how the system could be carried out. The weakness in the tactical decision-making process has resulted in corresponding weakness in the operational decision-making process and in the end, the entire design subsystem suffered. This resulted in a serious delay in launching the aircraft. For instance, the decision to use compatible software was a tactical one. On the other hand installation of different software in Germany and France, which were incompatible with each other was a wrong operational decision that delayed the design process. There was no control on information flow among the different constituents involved in the system. This clearly shows the need for systems thinking in the organization. Subsequently, Airbus decided to transfer German professionals to France. This was an operational decision. Even this decision was not an effective operational decision. This led to a weakness in the design subsystem. Therefore, the need for systems thinking in Airbus can be seen clearly.
Updating of Information System and Operation Management
Information system and operation management in Airbus can be improved by systems thinking. “Systems thinking” is a skill for planning and controlling. There are different models, which can be employed to help managers and supervisors organize and control a system (Mackie, 2008). “Systems thinking” helps in improving organizational performance by:
- providing an orderly way of thinking,
- showing the interrelationship of parts
- identifying sources of problems and how problems affect the performance of the entire system” (De Luca and Sanders, 2009).
It is important that the information systems and operation management of Airbus need to be improved for enhancing organizational performance. One of the tools that the management of Airbus can employ is the “Soft System Methodology” (SSM). SSM is a modeling tool, which compares the real world, as it is with some models developed based on the perceptions of what the world should be (Williams 2005). This tool provides the opportunities to develop various ideas for improvement. Soft System Methodology (SSM) deals with soft problems as distinct from other methodologies that deal with ‘hard’ problems (Checkland, 1981). Soft problems are difficult to define and in soft problems, the analysts do not think of problems but problem situations. Under soft system methodology, problem situation is analyzed to infer why things are not working the way one wants to and is there anything that can be done to improve upon the situation. In essence, it is a classic situation of not looking at a ‘problem’ but exploring an ‘opportunity’. (Couprie et al, 2007)
Stages in Soft System Methodology
There are different stages in the process of soft system methodology:
Identifying the basics of the Problem Situation
Under this step, the basic research into the problem area is undertaken. In this step, the important players and the method of executing the process are decided.
Expression of the problem situation through Rich Pictures
When the problem on hand is presented in the form of a picture, it reveals more information and knowledge on the problem and the picture gives rise to alternative solutions, which are suitable to solve the problem.
Naming the Relevant System
Once the problem is identified in its fullest detail it is possible to arrive at the root definition of the model. “The purpose of the root definition is to express the core purpose of some purposeful activity system,” (Peter Checkland and Jim Scholes 1990). The root definition should involve the perspectives of the players of the world connected with the problem situation. The definition of the worldview has a considerable influence on the decision regarding the proposal that is eligible for selection. Nevertheless, at the same time, it is not necessary to consider all the worldviews with the same intent. Different persons and agencies like the company executives, project members, workers, and even competing organizations may present the views on the problem situation. All these views will have a bearing on the root definition of the proposed solution.
CATWOE in Soft System Methodology
The CATWOE is a key element in the soft system methodology. The first letters of the various actors, involved in the problem situation make this expression.
- Customer – this denotes any person who will stand to gain from the benefits of the intended system.
- Actor – actors represent the agencies, which do the activities explained by the system.
- Transformation Process – this is the conversion of input into the output.
- Weltanschaung – is the German word for the Worldview (Wilson, 1990). This is the one, which makes the transformation process meaningful in the problem situation.
- Owner – means the proprietor of the system who enjoys the power to open and shut the system.
- Environmental Constraints – these represent the factors, which are situated outside the system that is being studied.
CATWOE can be applied to deal with the situations, which are covered by the root definition. It is also possible that various factors covered under CATWOE can become the building blocks for defining the root definition. It is better to take into consideration the worldviews of the parties connected with the designing of the aircraft, especially about the issues connected with the wiring involved.
Development of Conceptual Model
It is easier to draw a conceptual model once the root definitions are evolved. A conceptual model represents a human activity model, which conforms to the root definitions. Systems thinking is the foundation on which the conceptual model is developed. Systems thinking is an iterative process that takes into account the perceived world, ideas, and methodology.
Application of Soft System Methodology in Designing Airbus A380
Soft system methodology when used will result in improved efficiency of the designing of A380. This method has the analytical ability to deal with problem situations, where the social and political interactions of the actors are necessary.
The first and second stage in the application of the SSM model deals with the identification of the basics of the problem situation. In the first stage, the problem is not defined but the general area that interests the development of a solution is identified. In the second stage, the issue involved is expressed in some way. According to the guidelines, “structures, processes, climates, people, issues expressed by the people, conflicts” are addressed. While considering the use of SSM in Airbus, the design department becomes the structure. Designing for proper wiring is the process involved in the SSM. The key players in the issues relating to the development of the design are the German engineers and technicians associated with the design department. The issue expressed by the people is the bad design of the wiring and lack of integration between the French and German plants. Conflicts arise because of the incompatible software used by both plants.
The third stage is the root definition of the relevant system (Wilson, 1984). Every other thing grows from this stage. The root definition is a process of transformation that takes an input and produces a new form of output. Therefore, the starting point is a “Transformation”, implying how the input is transformed into an output (Checkland & Poulter, 2006). The following table illustrates the process of transformation, which is typical of the design issues faced in the manufacture of the A380 by Airbus. The transformations will largely depend upon the worldview that is applied to the issue.
The CATWOE model for the design department consists of the following activities and agencies. The manufacturing department of Airbus involved in developing the A380 will be the customer for the design department. Engineers and technicians from Germany and France form the actors involved in the SSM as presented in the CATWOE model. The software and materials used in the design department represent the inputs for the transformation process. These inputs are converted into the final design. The viewpoints of the different persons and agencies connected with the introduction of the new system would go a long way in designing the aircraft and these represent the worldviews in the CATWOE model. In the design department of Airbus, the departmental managers and people above them are the people who have the power to take decisions to introduce changes in the system, and therefore these people are the owners under the model. The environmental include the organizational policies and the legal and ethical issues connected with the issues. In the case of Airbus, the cultural differences between the German and French engineers and technicians are one of the environmental constraints.
The next stage in the application of SSM is the development of a conceptual model. Formal systems thinking lays the foundation for the conceptual model and it also functions as a measuring device to check the efficiency and utility of the conceptual model developed under the system.
The formal system should have a mission pointing towards the development of an efficient wiring design for the Airbus A380. It must also include a measure of performance as represented by the time saved and the efficiency of the aircraft. The owners of the design department must follow the decision-making process and the model must be a part of a wider system with which it interacts. This interaction will take place when there is the integration of the expertise and skills of German and French engineers. The system will have sufficient resources at its disposal surely when it has the equipment, R&D capabilities, and technical expertise of both German and French engineers and technicians. The system will also function to ensure long term stability and the ability to recover in the event of a breakdown where the owners can revert to a fall back system developed for the design creation. The components of the system have all the properties of a subsystem in which wiring is truly a subsystem of the design development system and the components of the subsystem have all the properties of the subsystem.
Analysis of the people, technology, and organizational issues involved in improving the operations at Airbus
The delay in the launching of the Airbus A380 can be attributed to three factors, which are people issues, technological issues, and organizational issues. Conflicts based on the emotions of the German and French staff in the production area represent the people’s views. This clearly shows an attitudinal problem, which was caused originally by the use of incompatible software by both German and French technicians. In addition, there had been high pressure on the people to meet tight production schedules and several other conditions that need to be fulfilled for the early launch of the Airbus A380. This caused stress on the employees who were on the front line and resulted in conflicts among them. German engineers and technicians thought that their knowledge is better than their French counterparts are. This also created conflicts among the engineers. The viewpoints of both German and French staff must be considered in the decision-making process to avoid such conflicts.
The use of incompatible software in the two production areas led to a serious delay in completing the design. This is the key technological problem and this resulted in the delay in the launch of the A380. The complex wiring problem and the adjustments the engineers had to make to the computer blueprints because of the use of old software by the French plant.
Organizational issues cover improper decisions made while solving the problems relating to the use of software in developing the wiring design, which was a complex one. To solve the problem, the decision was taken to transfer two thousand German staff to its Toulouse factory. The enmity between Germany and France affected the cooperation between the staff of the countries, which in turn resulted in a lack of teamwork. There have been instances where the company has taken decisions to implement temporary and inefficient solutions in the place of permanent and efficient solutions. This organizational issue needs consideration for the prevention of any such future occurrences. This type of decision-making without having an overview of the issues involved and the likely consequences on organizational performance will only lead to undesirable consequences causing not only great financial loss to the organization but also reputational loss which cannot be repaired. The lack of organizational efficiency because of bad decision-making will reflect on the customer confidence and the sales growth of the company. Airbus has to meet the effects, as the improvements in the wiring design were worked out expensive than anticipated. The company also lost substantial revenue in the process.
The company can take the following strategic measures for motivating the team members. The first thing the company has to do is to improve interpersonal relationships. This can be achieved by resolving conflicts and encouraging cooperative behavior among team members. It would help in improving team morale. It is important to analyze how personality differences affect interpersonal relationships (Moore et al. 2004). As a second measure, the company has to ensure effective coordination of the teamwork by identifying the role of different players and their actions, which are critical to team performance (Morgeson et al 2005).
Efficient communication is the primary vehicle, which enables the group members to accomplish their goals. The team members must strive to exchange information in a clear and timely manner. One of the essential prerequisites for improving organizational performance is effective decision-making. Problem identification and assessment are at the root of effective team management. Generation and evaluation of different solutions and their implementation is another strategic measure that the organization can adopt for effective decision-making. Unless the problem situation in any organizational context is approached with comprehensive details and information on factors causing such problems, it may not be possible to find the appropriate solution for the problem. Soft System Methodologies discussed within this paper will be of great assistance to Airbus in improving the performance of the design department as well as the overall organizational performance.
References
Aberdeen Group, (2008), Manufacturing Operations Management, Web.
Ainscough, M, Neailey K, and Tennant, C, (2003), A self-assessment tool for implementing concurrent engineering through change management. International journal of project management, Vol. 21, 2003, p. 425-431.
Baba, Yasunori, and Nobeoka, Kentaro, (1998), Towards knowledge-based product development: the 3-D CAD model of knowledge creation, Research policy, Vol. 26, p.643-659.
Checkland Peter, (1981). ‘Systems Thinking, Systems Practice’ London, John Wiley & Sons.
Checkland, P.B. & Poulter, J. (2006), Learning for Action: A short definitive account of Soft Systems Methodology and its use for Practitioners, teachers and Students, Wiley, Chichester. ISBN 10 0-470-02554-9.
Checkland Peter and Scholes Jim, (1990), Soft Systems Methodology in Action, Toronto: John Wiley and Sons.
Chudoba, Katherine M, Wynn, Eleanor, Lu, Mei, and Watson-Manheim, Mary B, (2005), How virtual are we? Measuring virtuality and understanding its impact in a global organisation, Information systems journal, Vol. 15, 2005 p.279-306.
Couprie Dale, Alan Goodbrand, Bin Li, David Zhu, (2007), Soft System Methodology, Department of Computer Science University of Calgary.
DeLuca Bill and Sanders Craig, (2009), The Universal System Model Relating to Manufacturing, Web.
Mackie, B. (2008), Organisational Performance Management in a Government Context: A Literature Review, Web.
Majchzak, Ann, Malhotra, Avid, John, Richard, (2005), Perceived individual collaboration know-how development through information technology-enabled contextualization: Evidence from distributed teams, Information systems research, Vol. 16, p.9-27.
Mertins, K and Jochem, R, (2005), Architectures methods and tools for enterprise engineering, International journal of production economics, Vol.98, p.179-188.
Morgeson P Frederick, Reider H Matthew and Campion A Michael (2005), “Selecting Individuals in Team Settings: The Importance of Social Skills, Personality Characteristics and Teamwork Knowledge”, Personnel Psychology Vol. 58 pp 583-611.
Moore S Linda, Dietz J Tracy and Dettaff J Alan, (2004), “Field Notes: Using the Myers-Briggs Type Indicator in Field Education Supervisor” Journal of Social Work Education, Vol. 40 pp 337.
Scribd.com, (2011), Introduction to Operation Management, Web.
Tennant, C and Roberts, P, (2003), The creation and application of a self-assessment process for new product introduction, International journal of project management, Vol. 21, 2003, p.77-87.
Tutor2u, Organization: Decision-making in Business, Web.
Williams Bob, (2005) Soft System Methodology, Web.
Wilson, B. (1984) Systems: Concepts, Methodologies and Applications, John Wiley & Sons Ltd., ISBN 0-471-92716-3.
Wilson B, (1990), Soft System Methodology, John Wiley & Sons Ltd. 2001. ISBN 0-471-89489-3.