Introduction
The emergence of developing markets, the accelerating embracing of novel technology, ecological issues, and changing public tenure tastes are all elements triggering a substantial modification in modern s. The automotive industry will similarly endure a transition brought about by digitization, rising robotics, and developing commercial systems.
In order to increase human security and well-being, as well as comfort and luxury, advancements have occurred at a phenomenal rate in the car industry. Integrating technology in the basic design of 4×4 vehicles, including All-Wheel Drive (AWD) and Four Wheel Drive (4WD), has improved automobiles’ security, automation, and energy efficiency.
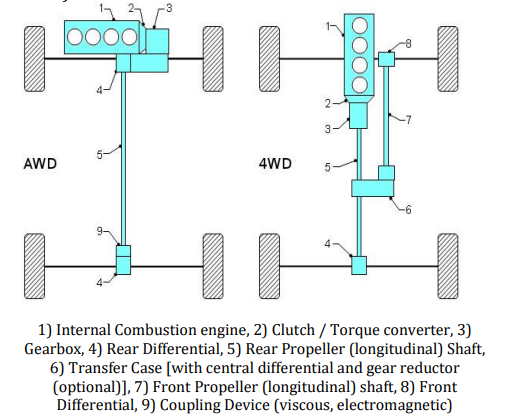
Four Wheel Drive (4WD) System
There are two variations of the four-wheel drive system: full-time and part-time. The Part-Time 4WD is simply a 2WD, except it has a transfer case. The automobile usually has two wheels, but there is an alternative to lock the axles of the rear wheels to connect the front pair as well. The wheels linked to the front axle of the transfer case have locking flanges and a secondary gear lever. The divergence at the fore axle transmits the energy to the rear wheels as shown in fig 1. Since there is no center differential, 4WD cannot be used on hard floors like bitumen since all axles spin at the exact velocity, which might cause axel wind-up (Gill et al. 361).
Once the 4WD is activated, the road parameters, every wheel’s adhesion with the terrain the vehicle is operated on, and the force proportion to each wheel all come into play. The motor also offers the choice of High-Range 4WD, which allows it to drive all four wheels while maintaining the same ratio of pace as 2WD, or Low-Range 4WD, which reduces the motor speed and results in a rise in the Internal Combustion (IC) vehicle’s RPMs, allowing it to produce more force at a lower speed.
A full-time 4WD system is one in which two axes constantly drive the car. In this kind of vehicles, there is no option for 2WD. A center split -inter-axial differential- is a feature of a full-time 4WD that enables all four wheels to revolve at different velocities without the axel winding up (Lee and Lee 91371). While the differentials set before either at the endpoint enable the sliding amongst each wheel, the inter-axial divergences permit slipping between the two axles. Once the driving gearbox outpaces the driven shaft, sliding happens. A locked center difference will cause the gearbox to function as a part-time four-wheel drive.
System Dynamics
In addition to its weight’s gravitational force exerted on it, a vehicle is subject to numerous other forces. Such forces could be spread horizontally or longitudinally, as in the case of friction force. The motor torque should be sufficient to conquer all the factors that prevent the automobile from moving, such as resistance between the wheels and the roadway (Park et al. 4). The forces applied to the wheels cause the car to move or reverse course. The three types of forces are the lateral force, the vertical or normal force, and the circular force.
The gearbox produces torque or brakes, which cause a frictional force to generate circumferential coercion, which causes the automobile to accelerate or decelerate. The forces acting throughout all times, whether the car is in operation or at repose, between the wheels and the terrain are known as vertical forces. In response to the vertical force, the portion of the tire that is in touch with the roadway deforms. A trapezoidal pressure-dissemination structure is created due to the vertical force not remaining neutral when the wheel turns. Once the car is being driven or there is a gust of wind that affects the mechanics of the automobile, the lateral force acts on the wheels.
The maximal friction force that may be applied at the tire patch is constrained by the tires’ coefficient of friction and contact force (acting across interface and object). Wheel slipping is an additional element upon which the horizontal, longitudinal, and driving elements of force rely. The amount of wheel slip is precisely proportional to the force imparted to the wheel (Xu et al. 3). To create traction, increasing the torque would also result in more wheel slipping. The wheel could enter a quick-escape slippage situation when the applied torque exceeds the maximum traction possible at the tire region.
4WD Control Strategy
Directional stability is crucial for the automobile to drive in the desired way. A type of mobile security management system called a traction control system (TCS) can improve a motorist’s ability to operate a car amid challenging circumstances. In order to increase the traction strength between the tires of the car and the surface, for example, a wet or cold road, and regulate the slide ratios of the operating wheels function in the best traction performance situations. As seen in the display, TCS frequently uses the reasoning edge approach in light of tests. The functioning of the mechanism depends solely on the rotation of the wheels. The Anti-Braking System (ABS), comprised of an Electronic Control Unit, is activated when it detects a substantial acceleration of one tire over the other. As a result, brakes are applied to the wheel, rotating with little traction, causing friction that transfers energy to the differential.
All Wheel Drive (AWD)
Although they have a different proposal, AWD systems are frequently mistaken for other 4WD technologies. Although an AWD system has an inter-axial split, it cannot shut the inter-axial differential, limiting its performance to that of a Part-Time 4WD vehicle. Based on the manufacturer’s preferences, an AWD system may be configured to function in several different ways. Once an AWD system has an On-Demand Mode, the automobile may run in 2WD form and mechanically activate the AWD in the event of tire slipping (Jung et al. 7). As soon as the tire slippage is resolved, the car switches back to 2WD configuration. A multi-plate mechanical clutch, a fluid coupling, and any other mechanism that may contact the opposing gearbox may be used to accomplish this.
System Dynamics
The quantity of torque given to the rear or back driveshaft determines the condition of an AWD automobile. With the use of a multi-plate wet clutch, the AWD system can regulate the amount of power that is transiently delivered to the rear motor shaft (Jung and Choi 2). Therefore, modelling representations of dynamic front shaft power distribution based on clutch involvement power must be supplied, particularly across clutch sliding conditions and incarcerate mode.
Based on the type of material and the degree to which oil is involved, the clutch is often separated into a parched clutch and a wet clutch. If the slip time is protracted, a parched clutch could be consumed. Wet clutches offset the drawback of dry clutches by absorbing heat produced in the friction plate. Humid clutches fall short of the maximum permitted torque that friction plates may withstand. It is possible to increase the maximum permitted torque via merging several slabs. To ensure the accuracy of the simulation, it is crucial to establish a system-wide viability of resistance model that takes the contact tension between two moving slabs into account (Kulikov et al. 2). The transfer situation system was selected to be modelled using the Generalized Maxwell Slip (GMS) model that is widely recognized for modelling friction.
In simulations of everyday driving, the GMS model closely corresponds. Difficult or dangerous driving conditions, such as quick acceleration on flat terrain, could bring on the stuttering reaction of the clutch transmission torque. Both the gearbox output shaft and the clutch-driven shaft experience identical angular amplitudes in the lock-up stage as shown in Fig 2. To enhance the precision of the AWD simulation model, it is crucial to determine if the clutch is sliding or seized at the moment. The GMS model distinguishes the present condition by the maximum static torque permitted. But in the event of simulations with complete automobile models.
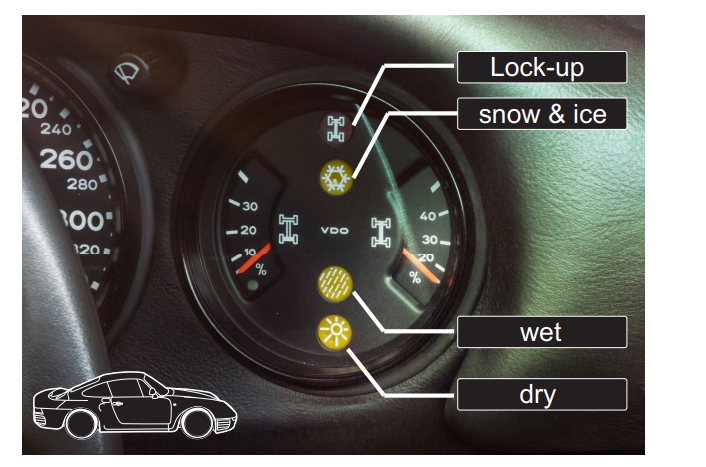
Control Strategy
Real-time vehicle conditions for the AWD control system are assessed depending on wheel type. In practice, the 2WD automobile lateral velocity is the least tire angular speed estimate among the four rotation speed detectors. Nevertheless, since all wheels get propelled when the gear is activated, it is impossible to estimate the longitudinal speed of an AWD automobile using only tire detectors (Mavi and Parmar 1030).
In order to evaluate the car’s longitudinal speed and to get the roller side slip inclination, it is also necessary to measure the vehicle’s lateral velocity. These automobile modes could be determined by employing a planar bicycle model and the machines longitudinal, transverse, vertical, and tire kinematics as shown in fig 3. Undoubtedly, the maximum capacity of the wheel longitudinal and turning rigidity may be used to determine the AWD operating situation. The AWD system tends to control the car’s horizontal and vertical motions. There are numerous methods for creating tire stiffness-based vehicle control algorithms. Moreover, no rationale for detecting saturation points has taken concurrent vehicle weight movement and slide into account.
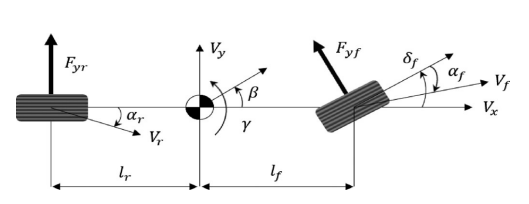
Conclusion
Incorporating technology in the core components of 4×4 systems has improved the vehicles’ security, automation, and energy efficiency. The addition of traction control mechanisms has improved the ability of automobiles to operate on both off-road and on-road settings while prioritizing the motorist’s well-being. The technology used in modern 4×4 gearboxes like AWD and Full Time 4WD has a long journey because it is still a freshly created technology with a complicated design.
The malfunction of a single element might result in several system problems currently since these complex structures are more reliant on electronics than essential machine elements, which are more robust and long-lasting. Extreme climatic conditions have the potential to negatively impact these electrical elements in a system that uses modern technology. Prospective systems are expected to be safer and more effective, with the technology used to support them becoming lighter, more precise, more secure, and more effective.
Works Cited
Gill, Bir Armaan, et al. “Four-Wheel Drive System: Architecture, Basic Vehicle Dynamics and Traction*.” International Journal of Current Engineering and Technology, vol. 8, no. 02, 2018, pp. 361–366., Web.
Jung, Hojin, and Seibum B. Choi. “Real-Time Individual Tire Force Estimation for an All-Wheel Drive Vehicle.” IEEE Transactions on Vehicular Technology, vol. 67, no. 4, 2018, pp. 2934–2944., Web.
Jung, Hojin, and Seibum Choi. “Control of AWD System for Vehicle Performance and Safety.” MATEC Web of Conferences, vol. 56, 2016, pp. 1–5. Web.
Jung, Hojin, et al. “Model Predictive Control of an All-Wheel Drive Vehicle Considering Input and State Constraints.” International Journal of Automotive Technology, vol. 21, no. 2, 2020, pp. 493–502., Web.
Kulikov, Ilya, et al. “Component-in-the-Loop Testing of Automotive Powertrains Featuring All-Wheel-Drive.” Energies, vol. 14, no. 7, 2021, pp. 1–18., Web.
Lee, Kibeom, and Minyoung Lee. “Fault-Tolerant Stability Control for Independent Four-Wheel Drive Electric Vehicle under Actuator Fault Conditions.” IEEE Access, vol. 8, 2020, pp. 91368–91378., Web.
Mavi, Shreyash, and Chirag Parmar. “Experimental Analysis on All-Wheel Steering System by Using Linear Actuator to Improve Efficiency & of the Vehicle Increase Stability of the Vehicle.” International Research Journal of Modernization in Engineering Technology and Science, vol. 02, no. 08, 2020, pp. 1027–1032.
Park, Giseo, et al. “Torque Vectoring Algorithm of Electronic-Four-Wheel Drive Vehicles for Enhancement of Cornering Performance.” IEEE Transactions on Vehicular Technology, vol. 69, no. 4, 2020, pp. 3668–3679., Web.
Warth, Georg, et al. “A Concept for Using Road Wetness Information in an All-Wheel-Drive Control.” Energies, vol. 15, no. 4, 2022, pp. 1–24., Web.
Xu, Shiwei, et al. “Research on Multi-Mode Drive Optimization Control Strategy of Four-Wheel-Drive Electric Vehicles with Multiple Motors.” Sustainability, vol. 14, no. 12, 2022, p. 7378. Web.