Introduction
GASCO, also known as the Abu Dhabi Gas Industries Limited, is a large natural gas company which is has its headquarters in the industrial complex in Ruwais, Abu Dhabi. Started in the year 1978 through a partnership of Total, ADNOC, Partex, and Shell, GASCO was specifically developed to help the three companies extract onshore natural gas production. The firm identified four plants where gas was to be extracted.
The four plants are closely managed by the Abu Dhabi National Oil Company which has other plants within the country. These four plants were strategically located in the desert and had the capacity to produce enough gas for commercialization. After extraction, the natural gas, in liquid form, is transported to Ruwais Fractionation Plant in Abu Dhabi where they are treated and then fractionated into different products.
Propane, Paraffinic naphtha, Ethane, and Butane, are some of the main products out of the fractional distillation process. The Abu Dhabi Polymers Company is responsible for the exportation of ethane and propane to different global markets, while paraffinic naphtha and butane are directly exported to the global market.
According to Schneider (87), one of the biggest challenges that many of the companies in the oil industry face is the dangers associated with transporting their products to the market. The supply chain in this industry is always shaky, and it requires advanced mechanisms and use of modern technologies in order to achieve the desired success.
This is what has been affecting GASCO as it struggles to become one of the leading companies in the world. With the management emphasizing on creativity and innovation in this industry, it is set to offer serious competition to the top companies in this industry such as Gazprom of Russia.
It is clear that this firm needs an effective operational management in order to be able to meet the expectations of various stakeholders. Upon extraction of the raw products from the onshore sources, they are always transported to Ruwais NGL Fractionation Plant where the processing takes place.
With a processing capacity of 17 million metric tons in a year, the operational strategies at this plant must be at its top notch to ensure that every stage in the processes is a success. Currently, the firm has four fractionation trains, a loading jetty, and storage tanks to ensure that the supply chain at this plant is successfully managed. The figure below shows GASCO plants and products overview.
Plant overview
GASCO was founded on December 1978 by four companies that shared a common vision in the market. Shell, Total, ADNOC, and Partex agreed to come together to form this company as a way of boosting their capacity in the production of gas. ADNOC had the largest share in the partnership of 68%. Shell and Total had a share of 15% each, while Partex was the junior shareholder with about 2% of the market share.
The four companies committed financial resources and with the help of the government of Abu Dhabi, GESCO was founded. The new company was getting into a field that already had strong competitors such as Gazprom, and this meant that to be successful, it had to align its operational strategies with the market needs and the industry’s dynamism.
This was not a simple task for the young organization that was just coming into the market. The operational management had to be focused on cutting the cost, improving effectiveness of the entire system, and shortening the time taken in the production and delivery of the products to the customers. This would not only help in maintaining a regular flow of products to the market, but also cut the costs of operation.
The Ruwais refinery, fully owned by GASCO, has been responsible for the refinery, storage and supply of the products to various channels used to reach the market. The refinery receives raw products from the four fields through two pipelines which act as trunk lines. The first pipeline is 24 inch, while the second pipeline is 30 inch. These two pipelines have been very effective in the delivery of the products to the customers.
The products are distributed from the refinery using four trains. The four pipelines have been very instrumental in delivering products to various destinations. The table below shows LPG and NPL feedstock supply in the month of October 2012 when an insurance survey was done at the facility.
Train 4 29,400 25,068
As shown in the table above, the first two trains have the same capacity, but in the month of October, the output of the first train was higher than that of the second train. This means that train 2 was not optimized in this particular month. The operation management unit should be able to identify the reasons why the train failed to give the maximum output within this particular month.
It is important to mention that GASCO is currently using Continuous Process Strategy as a way of lowering the cost of production. Given the fact that its standardized products are needed in large volumes, the production process has been operating 24 hours in a day. The objective of the strategy is to maximize on fixed costs as a way of minimizing the unit cost of every product.
Process Units
The refinery plant at Ruwais has the primary responsibility to fractionate the LPG and NGL that is received from the four plants discussed above. This is done with the help of the four trains.
NGP at Train 1 and 2
Constructed in 1981, these two trains at Ruwais are fed by pipelines which run from the desert fields to the plant, a distance of about 67 kilometers. The LPG and NGL from the fields are fractionated at these two trains to give ethane, butane, propane, and pentane products. They have a capacity of processing 11750 tones of NGL feed in a day each.
The products are then shipped to the international market using marine tankers. It is approximated that these two trains have the capacity to export about 2500 tones of ethane in a day. The surplus gas is used within the firm as fuel. Below is a diagrammatic representation of the processes which takes place at the two plants.
Simplified Process Flow of Train 1 and 2
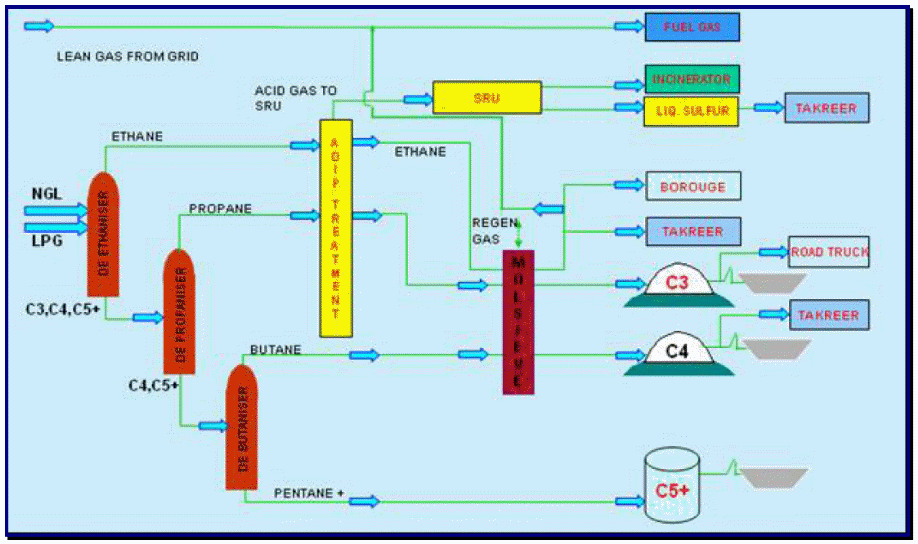
It is important to note that when the NGL is received, it is split into two streams and then fed into the two trains. NGL Feed Surge Drum is used to collect NGL that flows in the trains, while LPG Feed Surge Drum helps in collection of LPG feedstock in the system.
The fractionated distillation takes place in three columns which are De-propaniser, De-ethaniser, and De-butaniser. There is also a Sponge Recovery Unit which is responsible for the recovery of LPG products flared in the process of regeneration.
NPG Train 3 and 4
Constructed in 2009, train 3 also supports the fractionated distillation, just as the first two trains. The major difference between these two trains and the first two trains is that these two are more advanced technologically and have a higher capacity. Below is a simplified process flow schematic at train 3 which also located in Ruwais.
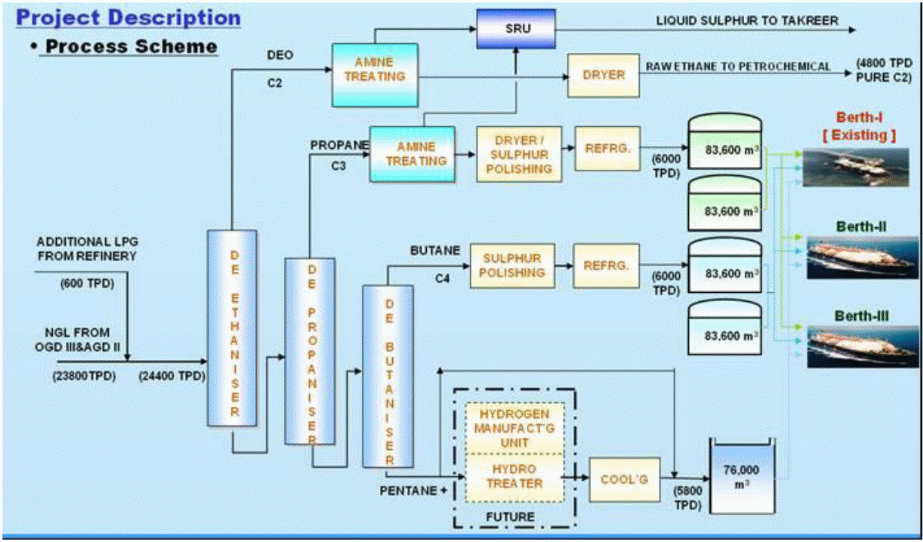
The principle used in this train is the same as that of the first two trains discussed in the section above.
Location
GASCO is located in the coastal strip of the Arabian Gulf, east of the Industrial Complex in Ruwais, South Western part of Abu Dhabi. It is about 240 kilometers from the city of Abu Dhabi in the United Arab Emirates. The location was very appropriate because of the onshore extraction of the products.
It is important to note that this is the location of the refinery plant where the products are distilled into final products before they are exported to the international products. However, the extraction of NPG and LPG takes place in the high seas. The map below shows the refinery plants at Ruwais complex and the high seas where extraction of oil takes place.
This strategic location shortened the distance between the point of extraction of the raw materials, and the refinery plants. It was also appropriate for exporting the materials using marine tankers.
The facilities of ADNOC within the city of Dubai have also acted as other sites for the products of GASCO, especially for the purpose of storage before they are transported to various markets in the region and internationally. This has helped improve the efficiency of the facility.
Management and Systems
According to Mahadevan (53), an organization can only be as successful as its management system. This scholar says that the leadership is responsible for developing policies that are followed when running the company. The policies must be based on the market conditions and should be customer-centric in order to achieve the desired results.
The management must also understand its workforce to ensure that they have the capacity to deliver results which are desirable in the market.
When making policies, it may be necessary for the policy makers to involve the junior employees who are involved with operational activities in order to identify some of the areas that may need adjustments in the company’s strategic objectives. It is only through this that it can be able to remain effective in the production process and competitive in the market.
When analyzing the management system, it is important to start by understanding the hierarchies that are involved and the offices which are responsible for various tasks. At the helm of this firm is a board of directors that is headed by the chairman. The board is responsible for making strategic decisions about the firm.
The board has delegated daily management responsibilities to its secretary, who is the chief executive officer of the firm. There are senior vice presidents who head various departments. They include the marketing head, the finance head, the technical head, the productions head, the supplies and logistic heads.
These officers report directly to the chief executive of the firm. In 2012, the firm created the office of senior Vice President Projects Functions who report directly to the firm’s chief executive. Below are the vice presidents are the senior management officials in charge of various departments. The figure below shows the hierarchies of the management unit at this firm.
Each of the departments has the sub departments which are responsible for various operational activities within the firm. The firm has been focused on achieving ISO 50001 and ISO 14001 accreditations as a sign of the improved service delivery to its customers. It has also been determined to inculcate the culture of creativity and innovativeness among its employees in the market.
This is meant to propel the management into higher heights of success in the market and efficiency in service delivery. Some departments have also been created within the firm to ensure that the quality of products that is released into the market is of the right standards. The management introduced Operation Excellence Division that was meant to ensure that the products from this firm are of high quality.
This unit is expected to operate under the Operations Support Group within the firm. Other departments which are specifically focused on improving the quality of the products and operations include Integrity Assurance division, Product Excellence, Maintenance Excellence, Asset Life Extension, and Reliability Divisions. Enterprise Risk Management Group is also active in this firm.
Inventory management
Inventory management is one of the most important tasks within an organization in the current competitive market environment. Murthy (34) defines inventory management as “The process of efficiently overseeing the constant flow of units into and out of an existing inventory.” At GASCO, there has been a concerted effort by the management to ensure that it has an effective inventory management system.
It would be important to give a brief analysis of the performance of the four trains mentioned in the section above. Although the first train’s output was slightly higher than that of the second train, it is clear that it was unable to give 100% of its capacity. The third train has a higher capacity than the first two trains, while the fourth train has the highest capacity.
However, it is evident that train 3 and 4 also failed to realize 100% output within the month of October in 2012. This means that this plant’s operational plan is failing in one way or the other, and this could be the reason why there is a gap between the trains’ capacities and what they delivered within that particular month.
According to Kamauff (76), the current competitive environment demands for a near 100% efficiency if a firm expects to achieve success in the market. This means that any failure in the operation system may not be tolerated because it shall open an avenue for other firms to penetrate the market.
In this particular survey, it was determined that propane, butane, and pentane are primarily exported to the plant market via jetty, while ethane is transported using marine tankers to the plant in Ruwais. At this stage, the focus will be put on the specific operational activities which take place when handling the products within the warehouse of the firm.
Processes at GASCO Warehouse
There are a number of activities which take place within GASCO warehouse. The process of managing the inventory within the warehouse involved a number of activities. This can be classified into three main
Receiving Process
The first process involves receiving the products into the warehouse from the refinery plant. This involves a number of activities. It is important to mention that there are some challenges that the company has to overcome in this process.
They include the massive paper work that takes place at this stage when the products are received. Another problem has been the time taken to determine the quantity of the products received from the refinery into the warehouse. However, these problems are being addressed by automating the process.
Issuing and Returning Process
The second process involves managing the inventory within the warehouse. It is at this stage that various orders placed will be analyzed with the view of determining their availability within the firm. According to Mahadevan (45), this would involve a physical check into the stores to determine the amount of products, and their quality.
The quality assurance team must be careful to ensure that only the standard quality products pass through this stage. This is to help eliminate any complaints from the customers about the quality of the products. At GASCO, this problem has been riddled with a number of challenges because it is always done manually. The problem can be addressed by automating the system.
Stock Count Process
The last stage involves the stock counting process. It involves the physical count of the products then issuing a print sheet about the stock within the warehouse. At this stage, the quality and quantity of the products will be clearly defined. This is the last stage before the products can be dispatched to the market. This process, just like the first two processes, can be improved using the technology.
Works Cited
Kamauff, John W. Manager’s Guide to Operations Management. New York: McGraw-Hill, 2010. Print.
Mahadevan, B. Operations Management: Theory and Practice. Upper Saddle River: Pearson, 2010. Print.
Murthy, P R. Production and Operations Management. New Delhi: New Age International (P) Ltd. Publishers, 2005. Print.
Schneider, Mitch. Operations Management. Clifton Park, NY: Thomson/Delmar Learning, 2003. Print.