Executive Summary
The manufacturing of milk tea may open up a new market for Kuwait Danish Dairy. Milk tea can serve as a new product for the company where the product line retains the dairy product consumers and captures the tea drinking market. The manufacturing process of the said product will be the topic of this paper. In phase 1, the decision in choosing the product to be manufactured by the company will be analyzed and discussed in according to the breakdown structure and component nomenclature of the product line. In the said phase the establishment of the production method will also be evaluated and discussed where the specific process flow of how milk teas are produced is carefully put into details. In phase 1 routine sheet of staff members who are part of the production team will be shown. Make or buy decisions in terms of raw materials and machines in making the product is tackled in the said phase. The processing of the product line is shown as it is specified and the different work stations are outlined in the said phase. Operation times of milk tea products are discussed as well as the number of stocks which serve as buffers is detailed. Also the assembly line balancing of the said set up is further detailed in phase 1. In phase 2, the design of the warehouse is discussed as well as the design of the material handling system. Specification of the warehouse is also indicated and discussed in phase 2 as well as the warehouse’s location. The outlook of the warehouse is detailed in the said phase and the safety system of the warehouse is also indicated in phase 2. On the last phase, the design of the personnel services is discussed. The area allocation and plant layout is analyzed in the said phase. An evaluation of the project is presented in phase 3 and the further considerations of producing milk tea are carefully detailed in the last phase.
Phase 1
Product to be manufactured
The team has chosen to produce ready to consume milk teas in cardboard containers. The decision to manufacture such product will put Kuwait Danish Dairy at an advantage in terms of its market positioning. Studies show that the number of patients suffering from cancer related diseases have risen in the past decades (World Health Organization, n.d.). People nowadays have become more and more health conscious thus consumers’ behaviors are geared towards products which have health benefits. Current trends in the food industry show that most products sold in the market and are in high demand have cancer preventing ingredients such as antioxidants (Winter, 2011). According to studies, tea drinks have high levels of antioxidants but when mixed with dairy products such as milk, the antioxidant levels of teas decrease (Nazario, 2008). In Asia, Hong Kong had popularized the mixture of black tea, evaporated milk, and condensed milk (Bubble tea, n.d.). The drink is known to provide nutrients such as calcium from milk and antioxidants from tea. Milk teas have beneficiary ingredients that provide consumers protein and cancer preventing nutrients. The Kuwait Danish Dairy is known for supplying families in the Middle Eastern region with high quality dairy products such as milks, labans, yogurts, labanehs, juices, ice creams, tomato pastes, olive oil, creams, whips, and butters (Kuwait Danish Dairy, n.d.). Adding milk teas to the product line of the company will open up a new market for KDD. Consumers such as the baby boomers, cancer patients or those who are simply health conscious will be the target market for this product line. The company will cater to a new set of consumers thus the new group of products will open up a new customer base from the company therefore opening up a new stream of income for KDD.
Breakdown Structure
The raw materials needed for the manufacturing of milk teas are black tea leaves and, instead of sugar, condensed milk and evaporated milk. The last two ingredients will be needed to add calcium and sweeten the drink. Black tea will be used because studies show that this type of tea leaf contains higher concentration of antioxidants than other varieties of tea leaves (Black tea or green tea – which is healthier?, n.d.). Tea leaves will be provided by a tea supplier, while the condensed and evaporated milks will be taken from the stocks of the dairy. These milks will be those extra stocks unsold by the company. By utilizing extra stocks the company reduces cost and wastage.
The leaves will be bagged in a sackcloth to prevent them from mixing with the liquid. They will be placed into a large boiler until boiled and simmered down for 3 to 6 minutes. While the tea is being made, the condensed and evaporated milks will be blended together in a mixer where the tea water will later be strained into after simmering. Tea water should be poured into the blended milks and not vice versa so as not to sterilize and impair the flavor of the milk. All tea leaves should be filtered out of the solution when pouring into the mixer in order to obtain a smooth creamy blend. The mixture of tea water and milks will then be shake inside the machine to obtain that delicate foam or bubble that milk teas are famous for. Lastly, the mixture will then be cooled before proceeding with the packaging process.
After cooling, the milk teas will be sent to the packaging department where they will be bagged, labeled and sealed into milk cartons. The products’ containers should be sealed tight to preserve the freshness of the tea. The cartons will then be transported and stored in a cool dry area so as to prevent spoilage. The product is then ready for distribution to the market.
Component Nomenclature
Milk teas can either be classified under dairy beverages or under tea drinks. Since the new product line caters to the dairy products consuming and tea drinking markets, milk teas can be categorized in between both dairy products and teas. Though the packaging and orientation of milk teas are that of a ready to drink pasteurized milk, consumers may also gain benefits of teas with milk teas. The group has decided to primarily focus on marketing the drink under the dairy products line.
Product Method (Process Flow Chart + Routine Sheets)
Kuwait Danish Dairy will operate daily, five times a week in manufacturing milk teas. A total of ten thousand milk tea cartons will be produced in a week’s time. At the start of the week, Monday, the production team will check and gather needed raw materials for the manufacturing process. Once all materials have been checked and are sufficient for the production the process of manufacturing milk teas will commence. The mixture of black tea with the condensed and evaporated milk will be followed by the packaging process once the milk teas have passed quality test procedures. Delivery of finished goods to distributors will be scheduled on every Thursday of the week. Every Friday the staff of the manufacturing department will have their weekly updates and reports with regards to material inventories and status of productions and deliveries.
Kuwait Danish Dairy’s manufacturing plant of milk teas will operate on Daily from 8:00 am to 5 pm. At exactly 8 am every day, attendance will be checked and tasks will be assigned to each staff. Goals and objectives will be defined so that the production team will have direction and focus on the needed quotas they need to achieve. Around 9:00 am, ingredient inventory will be checked to determine the sufficiency of the raw materials. Once ingredients are deemed sufficient in quantity and quality, the mixture process of milk teas will begin. This procedure may run through from 9:30 am to 12:00 pm. Lunch break will be observed among workers thus production will temporarily cease. Come 1:00 pm, the mixtures of milk teas will once again commence until 3:00 pm. During this time, the testing of quality of milk teas will be observed. The packaging of milk teas will follow around 3:00 to 4:30 pm. From 4:30 to 5:00 pm, the production team will check the quality and quantity of the finished goods. The products manufactured that day will be stored in a cool dry place ready for delivery on Thursday. This will be the routine of the production team form Monday to Wednesday. On Thursdays, the milk tea cartons that have been produced from Monday to Thursday will be delivered to respective distributors accordingly. On Fridays, the plant will have a comprehensive quality in checking and ingredient quantity inventory.
Make or Buy Decisions
In order to utilize available materials and save costs, decisions should be made whether to make products or just buy them. It is important for the company to evaluate the effectiveness and usability of products. There must be a great percentage of ROI in investing in products such as machineries. Decision makers of the firm must make sure that products bought must fully be consumed. A zero tolerance for wastage must be implemented. Products that would be made by the in-house team would be the evaporated and condensed milks. Since the company is already producing and supplying milk products, it would be more cost efficient to manufacture the needed evaporated and condensed milks. These products would be taken from the inventory of the company. Ideally these products would be those that are not sold by the company. To prevent wastage and save on cost, the milk tea team should utilize the remaining evaporated and condensed milks of the company. It should be noted though that these milk products are in good condition and are not expired. Second, since the company has a capable engineering department, a machine that mixes ingredients to produce milk tea must be made. Rather than buying a commercial mixer, it would be cheaper for the company to make one that suits the needs and demands of the company. Also since KDD already has a machine that helps in the packaging process of dairy goods, it would be best for the company to make a machine that handles the packaging process of the milk tea drinks. Materials to be purchased are only those that the company does not have. These would be raw materials such as black tea leaves for the mixture of the drink, cardboard and glue for the packaging and lastly steal, nails and screws for the making of machines. Black tea leaves, cardboards and glues will be in the constant “to buy” list of the company as they are considered consumable goods but the materials for the making of machines are only one time purchases.
Specifying the Processing
The processing of milk tea drinks would require both machinery and manual labor from the production team. The processing of milk teas must be given utmost attention in order to prevent the spoilage of the products. Quality testing must properly be implemented to avoid unnecessary and hazardous bacteria from forming in the products. Raw materials must be checked before they are put into the machine for mixing. The cleanliness of the machines must be checked before and after the production of milk teas.
Workstation Layouts
Flow Pattern within the Product Department (Circular)
We have chosen to adopt a circular set up because we believe that everything must flow through a check and balance method among the production team. Each process must be verified by each team member in order to avoid mistakes being committed.
Operation Times
The operation of the plant will start from 09:00AM to 04:30PM. A 1 hour lunch break will be observed where machines will be shut off to cool down. In between operational hours a 20 minute break will be observed by workers. This will be divided in the morning and in the afternoon so that’s 10 minutes in the morning and another 10 minutes in the afternoon. Workers cannot go on their 10 minute breaks all at the same time. People are needed to look after the production process at all times.
Buffer Stocks at the Workstation
Every week there are 10,000 cartons of milk teas produced but only 9,000 of them are delivered and sold directly to distributors. The remaining 1,000 cartons of milk teas served as buffer stocks left at the workstation. These 1,000 cartons are used for product testing to determine the quality of the products at the same time they are also used as samples given out to prospective clients. Also the buffer stocks serve as stocks that are used to replace returned goods from distributors. They serve as emergency go to stocks of the company. The shelf life of the buffer stocks is about 3 weeks. In order to prevent wastage, buffer stocks are sold to preferred clients at a cheaper price once they are not consumed 1 week before the expiry date.
Assembly Line Balancing
In order to balance the line of assembling the goods the process flow mentioned above must be followed. Each team member should strictly implement the standard operating procedures of the company in order to achieve the needed results. There would be a check and balance procedure among the group to ensure the quality of products is of great standards.
Phase 2
Design of the Facilities Functions (Store and Warehouse)
Since the company would be needing a manufacturing plant and warehouse for this project. The above diagram shows how facilities will function and be utilized. The cycle will begin with raw materials being sorted out. The best quality of materials will be selected for the production of milk teas. Once materials have been classified the ones that have passed the quality testing procedures will undergo the broiler (tea leaves) and then proceed to mixture. Once the process has finished the milk teas will be transferred to another machine for packaging. Milk teas manufactured for the day will be put into storage and will be ready for delivery. At the end of each day the cleaning of machines and materials used in the production process will take place.
In building a warehouse to store the milk tea products the company must consider a few points for the storage of milk teas. The ideal warehouse for the said products must be near the factory so that it would be convenient for the company to store the products without spending for the extra delivery cost. The storage area must be properly sanitized and like most areas of the dairy factory it must properly abide to pest control systems and procedures. Trays or plastic containers must be available together with shelves to house milk tea cartoons. The warehouse must be spacious enough to house thousands of milk tea cartoons. It must have a fork and ramp where products will pass through once they are transferred to vans and trucks for delivery. When products are about to expire they must be chilled to prolong their shelf life thus a huge refrigerator must be available in the warehouse to anticipate such cases. The warehouse should be a high bay one with the following specification
In terms of safety system, the company can avail a CCTV camera to monitor the presence of people visiting the warehouse. There will be security guards who will look after the compound for 24 hours and will be assigned with shifting schedules. Aside from such necessary locks will be provided on the entrance and exit doors as well as additional padlocks will be placed on refrigerators.
Design of the Material Handling System
In terms of handling materials, a standard operating procedure will be followed where the cleanliness of materials used will be strictly implemented. When sorting out the best quality raw materials, the production team is required to wash the needed ingredients before putting them in the broiler and mixer. From the receiving store, materials will be sanitized before they are put into the broiler and mixer. On the other hand the machines must be properly cleaned as well. Once production processes are finished, the team is required to clean the materials used to avoid the development of bacterial. Upon packaging, materials should be of utmost quality where the cardboards and glues must pass quality tests. Once the whole process has finished, milk teas must be stored in a cool dry place to avoid spoilage.
It is important that in handling materials, careful analysis must be made in order to reduce wastage and costs. The acquisition and movement of products must be assigned and designated to authorize personnel. Carts, roller conveyors, hand trucks, manipulators, slides or chutes, ball transfer tables, mechanization and automation must have people assigned to control and operate such areas. A system must be drafted out so that it would be clear among team members their designated roles and the company’s expectations of them in handling materials. The goal of material handling is to maximize the building cube such as racks, mezzanines and overhead conveyors (Stephens and Meyers, 2010). Procedures in solving problems related to material handling must be discussed with staff. It is ideal that these methods be posted in a bulletin board where everyone can see it. The significance of such is to remind everyone on how to deal with issues related to material handling. Educating team members can be very effective especially since errors in material handling may cost the company a significant amount of money in repairing damages.
In handling equipment, fixed-path or point-to-point, fixed-area, variable-path variable-area and auxiliary tools equipment are the general categories that must be considered. The receiving and shipping departments are heavily involved in operating equipment especially in handling cranes, conveyers and other devices that are used in the transferring of materials from one point to another.
In terms of handling storage units which includes shelves, racks, double deep pallet racks, mezzanines, rolling shelves and drawer storage units, careful observations and handling must be practiced to preserve the materials at the same time ensure the quality of the raw materials and finished goods are in good condition upon receiving and delivering to clients. The receiving, shipping as well as the storage department teams must closely work with each other in order to ensure that materials are handled properly. Each team member should be well aware of their own functions and job responsibilities. When raw materials are received for storage, the receiving team should inform the storage team about the receipt of such materials. The latter must inform the former where the said materials delivered to the plant will be placed and the careful transfer of goods from the receiving department to the storage will be observed. Once the production team starts their process in the manufacturing of milk teas, raw materials will be obtained from the storage team. Once milk tea products are produced, goods will be sent to the shipping department for packaging procedures. There will be batches for delivery while some will remain for warehousing. Goods for delivery will be loaded in trucks for dispatching while goods for warehousing will be transferred to the storage area. The shipping team and the storage team must carefully coordinate with regards to the transfer and placement of finished goods in the stockroom. A pull out date will be imposed so as to avoid the spoilage of goods in the warehouse. All teams must closely work with each other to avoid inefficiencies. The procedure of everything starts with the receiving department and ends with the shipping and storage departments. The production team cannot function without these teams thus the careful handling of materials is essential especially in the mentioned teams. Staff must be well oriented with the functions and equipment used in the teams everyday standard operating procedures. Careful handling and implementation is greatly expected from team members of the concerned departments
Activity Relationship
In the manufacturing of milk tea products it is essentially important that departments are strategically located according to their respective functions. The supply department must be located beside the production department as ingredients for mixture will be coming from the former and the latter will be responsible in producing raw materials. After the product has been produced it must be transferred to the packaging department right away thus it must be noted that the production and packaging departments must be beside each other. After the packaging of products they will be brought to the warehouse for storage. The warehouse must be located near the packaging department. Also it is ideal that the logistics department is near so that the transporting of milk tea products won’t be a hassle. Sales, Marketing and Customer Service departments are essential in running a company as they are responsible for the flow of the products in the market. They are not necessarily required to be located near the factory but their presence is a must in every company.
In the manufacturing of milk tea products it is essentially important that departments are strategically located according to their respective functions. The supply department must be located beside the production department as ingredients for mixture will be coming from the former and the latter will be responsible in producing raw materials. After the product has been produced it must be transferred to the packaging department right away thus it must be noted that the production and packaging departments must be beside each other. After the packaging of products they will be brought to the warehouse for storage. The warehouse must be located near the packaging department. Also it is ideal that the logistics department is near so that the transporting of milk tea products won’t be a hassle. Sales, Marketing and Customer Service departments are essential in running a company as they are responsible for the flow of the products in the market. They are not necessarily required to be located near the factory but their presence is a must in every company.
The process can have 4 different process flows. First it can be the standard where the production team operates first at the supply department, and then production team, packaging, warehouse, logistics, marketing, sales and customer service departments follow the flow. The second alternative is to skip marketing and proceed to sales directly. Another option is, after packaging goods be delivered to logistics directly. It may also include skipping marketing and proceeding to sales directly. A fourth suggestion is from the packaging department goods will proceed directly to sales.
Auxiliary Services
The milk tea factory is in need of various facilities that may serve and function as support especially in terms of receiving and shipping, storage, warehousing, maintenance, utilities, heating and air conditioning (Stephens and Meyer, 2010) Kuwait Danish Dairy’s milk tea production factory will be located near the existing dairy products production plants. In order to maximize the services of the existing plants’ facilities and to lower down cost, the milk tea plant will also be covered by the support team’s services.
The receiving and shipping department, though the two departments are separate and function differently, will have similar people, equipment and space requirements. Material flow will start in the receiving department and it is in the shipping department that the material flow will end. Both departments are located next to each other. Since KDD already has existing receiving and shipping departments, it is best that we centralize such because by doing so the company saves on equipments and personnel salary, maximizes the utilization of space and reduce facility cost. Though this may result in some disadvantages thus KDD must be cautions of space congestion and a probability of a less efficient material flow. The possibility of having multiple receiving locations can be a double edge sword. This can be an advantage or a disadvantage to the company depending on how KDD functions with such.
Ideally the possible arrangement of the shipping and receiving area should be located near transportation facilities on one side of the building, transportation facilities on two adjacent sides of the building or transportation facilities on two opposite sides of the building (Tompkins, 2010). KDD’s receiving and shipping department is located at the two opposite sides of the manufacturing building.
The existing receiving department of KDD needs improvement. Doors must be converted to dock doors that may depend on the arrival rate at peak time and service rate. Since the existing one only has about 2 dock doors, there may be a need to add 2 more and replace the old ones. Dock plates, dock levers and dock boards are used to bridge the gap between the floors of the building and the floors of trailers so that materials can be moved on and off the trailer easily (Stephens and Meyers, 2010.) The existing dairy plant already has these facilities thus the new milk tea factory may share with the dairy plant but usages must be scheduled. Other facilities required for the receiving department include aisles which must be sized for the material handling equipment, the material being moved and the frequency of trips. The company can use the existing ones of the dairy products team.
On the other hand the shipping department is responsible for the packaging of finished goods for shipping, addressing cartons and containers, weighing each container, collecting orders for shipping, spotting trailers, loading trailers and creating bills of lading. The existing department of KDD functions and provides services to the dairy products production team. In terms of facilities the milk tea production team can share with the dairy products production team but it may be necessary to hire more manpower to serve the requirements of the milk tea team in terms of shipping procedures.
Facilities needed for the milk tea department’s safekeeping of raw materials, finished goods, office supplies, maintenance and janitorial supplies must closely be segregated from that of the other departments. Though office supplies, maintenance and janitorial supplies can be the ownership of a different department and can be shared with the dairy products production team, it is highly recommended that the milk tea division has its own as to avoid confusion among departments. In storing raw materials, a giant refrigerator or freezer will be needed as to preserve the quality of the materials. The storage capacity must be enough to accommodate the production of goods equivalent to a day’s requirements. In order to implement orderly handling and allocation of materials it is best that the company adopts a fixed/ assigned storage where each individual stock keeping unit is stored in a specific location. This way stocks will not be lost and staff will be well aware of the storage locations of materials. KDD must keep in mind that the store department’s objective is to maximize the use of the cubic space, racks, shelves and mezzanines, minimize aisle space and empty space, provide immediate access to selective materials and provide safekeeping of inventory including damage and count control (Stephens and Meyer, 2010). A separate storage are for the milk tea production department must be allocated so as not to mix raw materials, finished goods and other supplies of departments in doing so confusion between the departments will be avoided if not lessened. The storage of raw materials must be separate from that of finished goods. The locations of both storages will be fixed and must be closely monitored. Supplies must be in small amount of everything (1 day to 1 week supply) where excess inventory should be kept as bulk stock. To reduce the travel distance storage areas must be located near the production and packaging departments. Ideally the average part of total distance should be 28 feet compared to an ordinary warehouse where the average distance (one way) is 60 feet. This strategy will improve the efficiency and time management of the production team.
Maintenance of the service equipment is also important. This typically accounts for 2 to 4% of the plant personnel. Since the existing milk plant already has a maintenance team it is best that the said team adds manpower to accommodate the requirements of the milk tea department. A special team within the maintenance department will be formed to render their services to the milk tea production team. In terms of materials existing ones used by the dairy products production department will be used but if there are special equipments needed by the milk tea department’s machines the company must provide. The said team will also be responsible in preserving the working conditions of utilities, heaters and air conditioners of the milk tea department.
Phase 3
Design of the Personnel Services
According to K. Keller, customer satisfaction is when the products or services rendered by a business is above or equal to the customer’s expectation (Gupta, n.d.). In order for a business to continue surviving in the now very competitive market world, the level of customer satisfaction must be high or meets the customer’s expectations but because customers’ expectations are very high, it takes continuous effort on the part of the suppliers or service providers to please the consumer. Services and products should be of high standard and quality. The positive feedback of the customer is needed as this would ensure that their business would also continue to grow. Customer satisfaction’s goal is not only to get new customers into buying product but also to ensure that the old or regular customers would keep coming back (Cacioppo, n.d.). With the increasing competition in the market, businesses need to make sure that they are providing consumers the best that they can give so as other businesses would not be able to lure away their customers. Aside from quality service and product, availability of product would also boost up consumer satisfaction. If supply continues to not meet demands, consumers would soon enough move on to a different company or business where they can be assured that the inconvenience of unavailability would not hinder them from obtaining their wants and needs.
Through the manufacturing of milk teas, packaging and the overall concept of the milk tea drinks produced by KDD must be of superb quality and must conform with the depends of the consumers. At the back of the cartons a contact number will be placed for customers to call if they have any complaints, suggestions and/ or comments. The marketing and service team must work hard in order to provide quality services to the customers whether they may be in terms of providing promotional support or catering to their thoughts with regards to the improvement of the product. Customer service is the top priority in order for the milk tea drinks to capture a stable customer base.
Area Allocation
The location of the business is a very important factor in starting up a business (Spaeder, n.d.). This could be the defining point in which the business might succeed or fail.In choosing a good business location, the business must consider the location whether customers in the area are willing to buy the product or the population of the area is indeed big enough to sustain the needs of the business (Production and operations – business location for new business). The purchasing power of the people in the area should be high enough that the business would be able to profit during its stay (Purchasing power, n.d.). Low count of population would mean demand and sales of the products would also be low, therefore decreases in profit for the business.
The products should be distributed in supermarkets or convenience stores near offices and business areas and apartments or residential areas, (Allen, n.d.). This would give much convenience to people working in the offices when they need to stop for grocery on their way home or during lunch break. This is also a good area for business because this is where the financial department of the city or town is located therefore holding the most amount of money. While supermarkets and convenience stores near residential places would be handy for residents living in the area as this would save them time and gasoline to just walk to the supermarket. Moreover, consumers coming home from work could also stop by and pick up their groceries on their way home. Also, during holidays or events, residents can easily have access to the supermarkets for their preparations especially when they lack ingredients or supply had ran out in their house.
The factory where the milk teas be manufactured will be in the same plant where current products of KDD are manufactured but there would be a separate area for the production of milk teas. By sharing the factory with other product lines, the company saves on rent at the same time there would be a decrease of transportation cost because the condensed and evaporated milks will no longer be delivered using a van or truck to the production area of milk teas. On the other hand the distributors of current dairy products of the company can also avail the milk tea drinks. They can add this new product line to the existing one they currently carry. In terms of store location, it is highly suggested that milk teas be sold in grocery stores, convenient stores or any other businesses that sell dairy products.
Plant Layout
The milk tea plant must be located within or near the existing milk plant of KDD. Since the procedures of both product lines are similar, the company can model the new milk tea plant to the current milk factory. In terms of delivery, there are vans and trucks which are used to deliver other dairy products of the firm to its distributors. These can be used to deliver the milk tea drinks to clients provided delivery and usage of the vans must be coordinated among departments and teams.
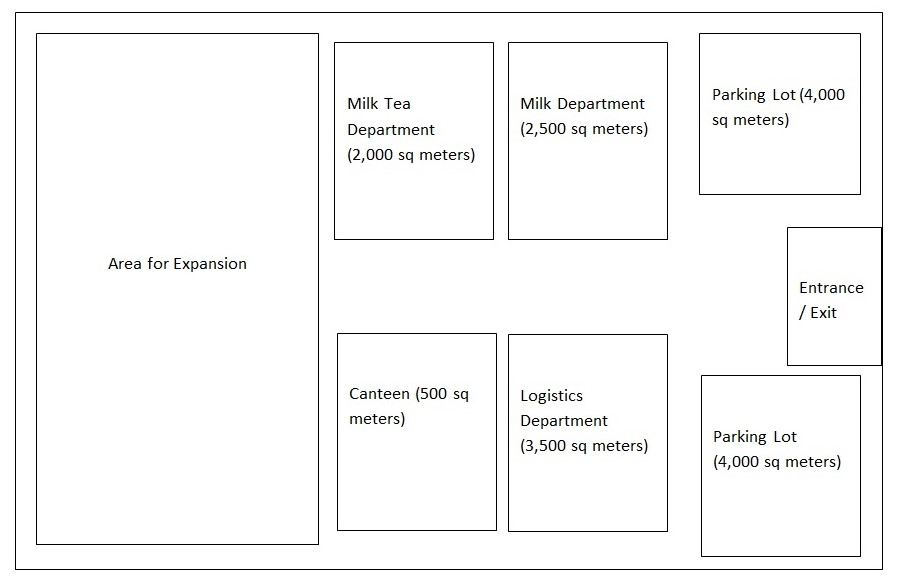
Evaluation and Considerations
Through careful analysis, the production of milk tea drinks would help boost annual revenues of KDD but it is essential that the departments of the company closely coordinate among each other to fully maximize the idea of selling milk tea drinks. Milk tea drinks may be a new concept in the Middle Eastern region thus the marketing and customer service teams must be active in promoting the product and must cater to the needs of the customers. The constant innovation in this product line must be observed as this will be the first of its kind in the market.
In terms of production and manufacturing, the production team must closely follow given standard operating procedures to ensure the cleanliness of the products. Sanitation is important in the production of milk tea drinks. Quality tests must constantly be conducted to ensure that the milk tea products conform to the standards of the company. In order to evaluate the marketability as well as the profitability of the new product line, the marketing team must conduct market surveys to check if the milk tea drinks conform to the demands of the market. Improvements must be implemented without sacrificing the taste and the nutrients of the drink.
Personnel Requirements
The total headcount for the milk tea production project is about 40. For every team around 5 people are expected to work together to attain good and efficiently delivered results. The company must prepare personnel requirements because “the location and quality of these services affect the efficiency and productivity of employees, the quality of work life and employees’ relationship with the company’s management” (Stephens and Meyer, 2010). Services the company will provide are parking areas, employee entrance, locker rooms, restrooms, cafeteria, drinking fountains and medical services.
Parking areas will be provided to team leaders and managers. Staff will not be provided parking spaces. The parking slots will be located near the entrances of the main door approximately 100 – 500 feet away. Parking lots will be broken down to manufacturing employee parking, office employee parking and visitor parking (Stephens and Meyer, 2010). Since the company has already have existing parking spaces for the other product teams, the milk tea production team can lobby to get some extra parking spaces of the other teams. The team will only need 8 parking spaces for the team leaders. Visitors of the milk tea team can park on the visitor parking spaces of the company. The size of the parking space will be 2 per 100 stalls.
Employee entrance is located near the parking area. “Employee entrance affects the placement of parking, the locker room, time card racks, restrooms and cafeterias” (Stephens and Meyer, 2010). The door size of the entrance will be about 5 feet with an aisle leading into the plant. Employee entrance will have a security office about 200square feet. Locker rooms with shower will also be provided for all 40 employees of the milk tea production team where all will be required to leave their belongings, change their clothes and bathe in the said area. A space of 4 square feet will be given per employee thus if we have 40 employees we would be requiring atleast 160 square feet for the areas. There will be 2 locker rooms, one for the male employees and another for the female.
The company has an existing cafeteria which is within 1,000 feet of all permanent employee workstations thus the milk tea production team can use the said facility and take advantage of the services. The cafeteria allows delivery of food and trash pickup and allows employees to have an outside view while eating. The existing food services of KDD can be improved by adding the supply of dishes that are served every day. Kitchen facilities are based on the total number of meals served. The cafeteria can add 40 heads to feed in their count so as to accommodate all the personnel they are serving every day. 8 tables seating 5 people each will be added in the cafeteria room to accommodate the milk tea production team. The area’s ventilation and exhaust must be check to ensure that odors do not interfere with other activities of the said facility. Lunch break for the team will be on a shifting time basis.
Other food service alternatives which will be included are dinning away from the facility and vending machines. The milk tea team will be treated out by the company every end of the month if they have reached their targets. A vending coffee machine will be provided at the employee office. Food is not allowed in the work area. Each area will have 2 toilets for employees to use. A total of 16 toilets will be provided for the said groups which are located 150 feet away. Drinking fountains will be located outside the toilet areas.
The KDD has an excising clinic to cater to sick employees or those who meet accidents during working hours. This room is about 6 foot by 6 foot. A registered nurse is present to facilitate the heath needs of the employees.
Office Layout
In designing the milk tea production team’s office would be that of a portable office which is located in the middle of the production department. The office will be immediately accessible and will have a line-of-sight with regards to the whole operation of the milk tea production team. This type of office falls under the category of supervisors’ office. Though the office is classified as that of a portable office, the interior design should be a combination of an open office concept and conventional office thus a modern office design where managers can occupy private rooms while staffs will be occupying tables and chairs in an open area and only partitions will provide them their needed privacies. There are 8 mangers for 8 departments. Each department has 4 staffs thus in the said office there will be 9 private rooms, 8 for the managers and 1 for the milk tea production general manager. There would be 12 tables located in the center of the office. These tables will be occupied by the staffs of all departments except for 5 departments namely supply, production, packaging, warehousing and logistics since the said departments’ employees need to be in their respective posts (i.e supply room, production room, etc.). A meeting room will be built near the office entrance and a long working table will be placed in one corner of the room. This table will be used by the personnel who do not have their own tables but may need from time to time to do their reports. Given that each employee is given a minimum of 200 square feet space allocation, the office must be at least 8,200 square feet in measurement. The given available area is 10,000 square feet for the office. The office space determination of each employee must be:
The office area will be very spacious with additional areas for facilities such as fax machines, photocopying machines, comfort rooms and an area for the vending machine. Managers’ offices will be located in all corners of the office while the staffs’ area will be located on the center.
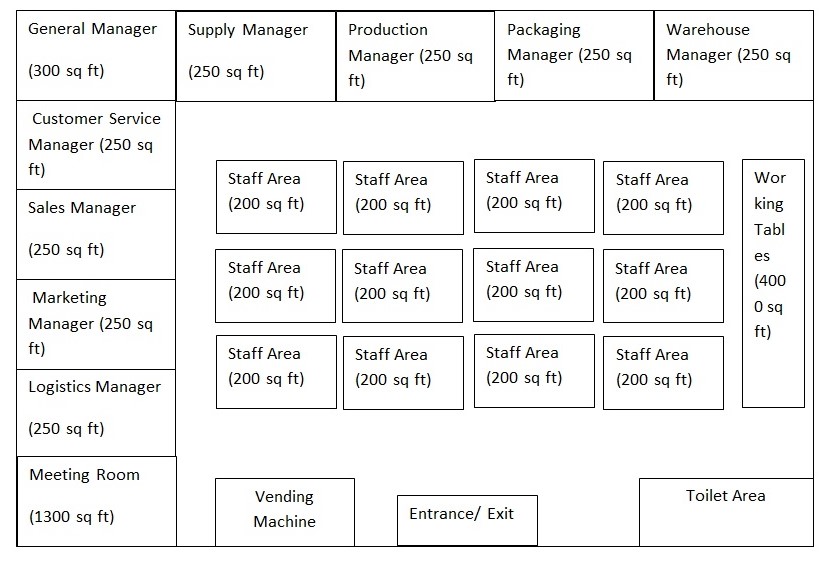
Cost Evaluation
Reference List
Allen, S. (n.d.). Choosing a Location for your business. Web.
Black tea or green tea – which is healthier. (n.d.). Web.
Bubble tea. (n.d.). Web.
Cacioppo, K. (n.d.). Measuring and managing customer satisfaction. Web.
Gupta, N. (n.d.). A summer training report on analysis of New Honda City customer profile and satisfactory level. Web.
Kuwait Danish Dairy. (n.d.). Web.
Nazario, B. (2008). Antioxidants in green and black tea. Web.
Production and operations – business location for new business. (n.d.). Web.
Purchasing power. (n.d.). Web.
Spaeder, K. (n.d.). How to find the best location. Web.
Stephens, M and Meyers, F. (2010). Manufacturing Facilities Design and Material Handling. United States, New Jersey: Pearson Prentice Hall.
Tompkins, J. (2010). Facilities Planning. United States, New York: Pearson Prentice Hall.
Winter, J. (2011). Global antioxidant sales hit $3.4 billion. Web.
World Health Organization. (n.d.). Web.