Definition
Inventory control is defined as: “the process aimed to minimize the total cost of inventory and keep track of a stock” (Slack et al 2003, p. 5).
- Inventory control is a multidimensional process.
- Inventory control examines past activities and proposes future improvements for an organziation.
- Inventory control monitors present activities to assess an orgnaization’s ealth.
- The aim of inventory control is to foresee future barriers and prepare to overcome them.
Inventory Control and Planning
- Inventory control is linked to planning.
- Without a plan there is nothing to control, and without control, organizational plans cannot be fulfilled.
- Inseparable components of operations management, use sales forecasts and budgets to support inventory control.
The general purpose of inventory control
The purpose of inventory control is to help achieve internal and external balance of resources.
Inventory control is developed:
- to assure that organization’s goals will be achieved;
- the organization is moving in the proper direction;
- to assess the effectiveness of the use of material resources;
- to balance operations among different units.
Data for Inventory Control
Inventory control is based on data from
- accounting records,
- sales analyses,
- marketing research,
- forecasts,
- distribution,
- cost accounting, and
- simulation.
Car Wheels by OEM Company
- Problem identification:
- Unstable delivery and quantity of raw materials lead to stock shortage. In some days, the stock fall to zero.
- Inventory Management Process.
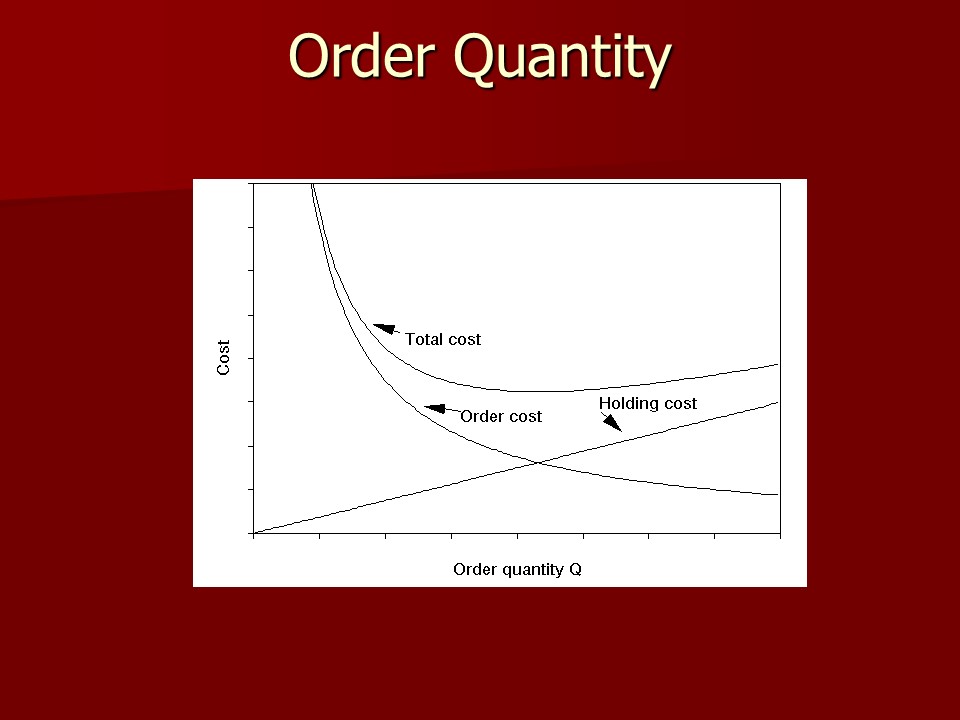
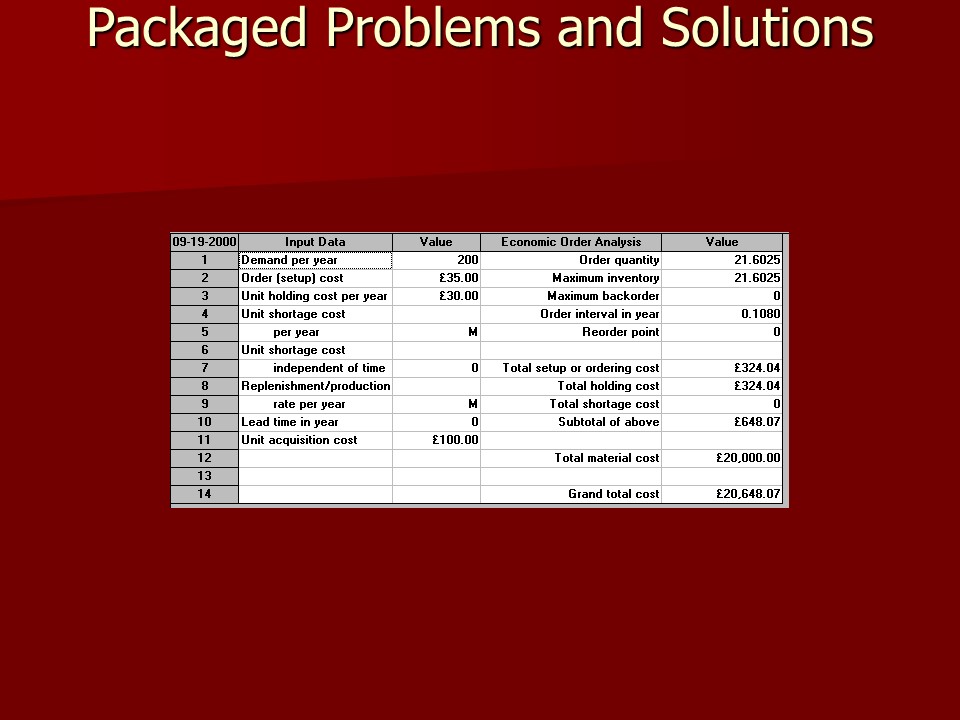
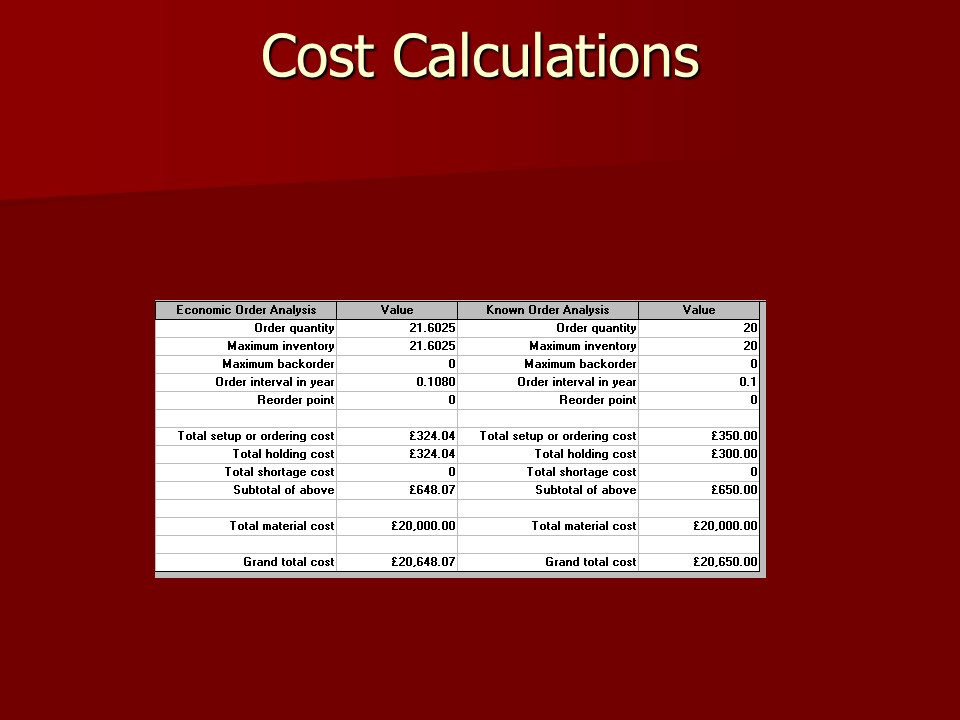
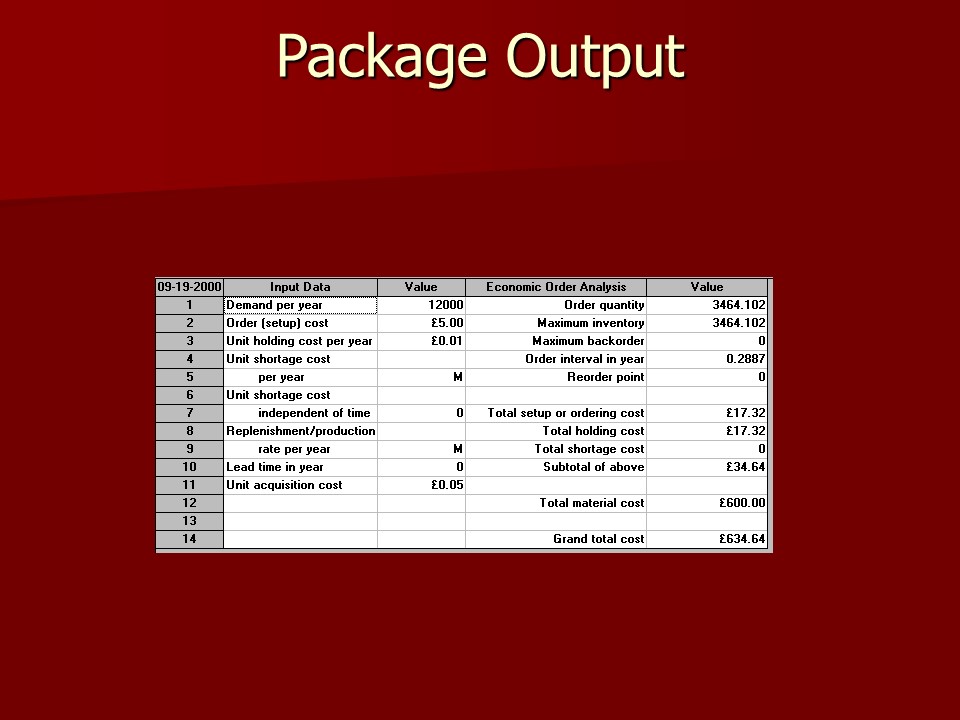
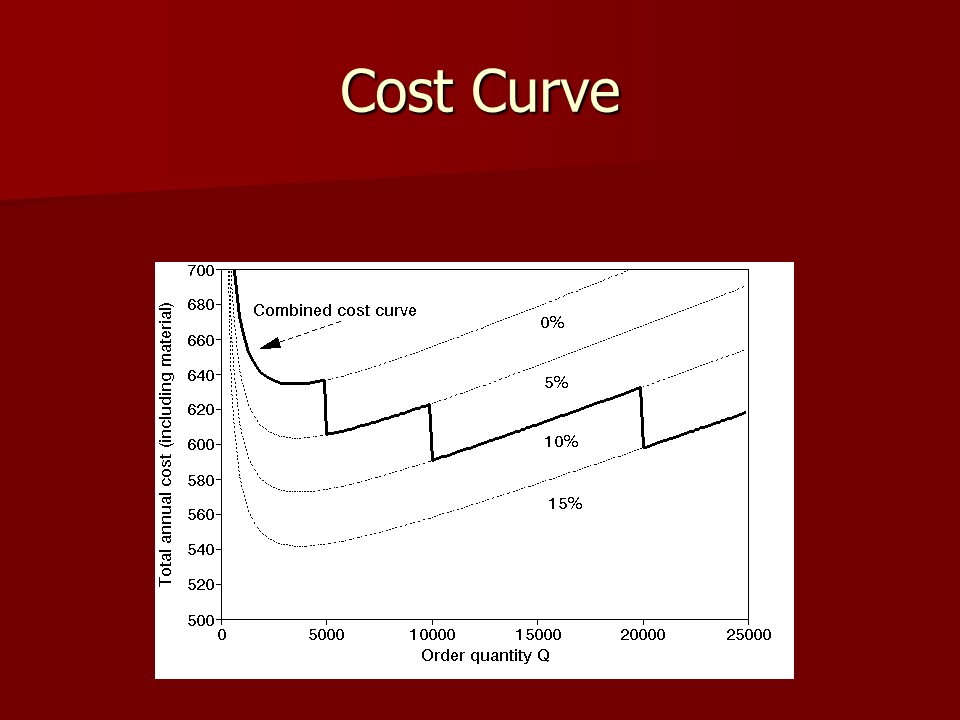
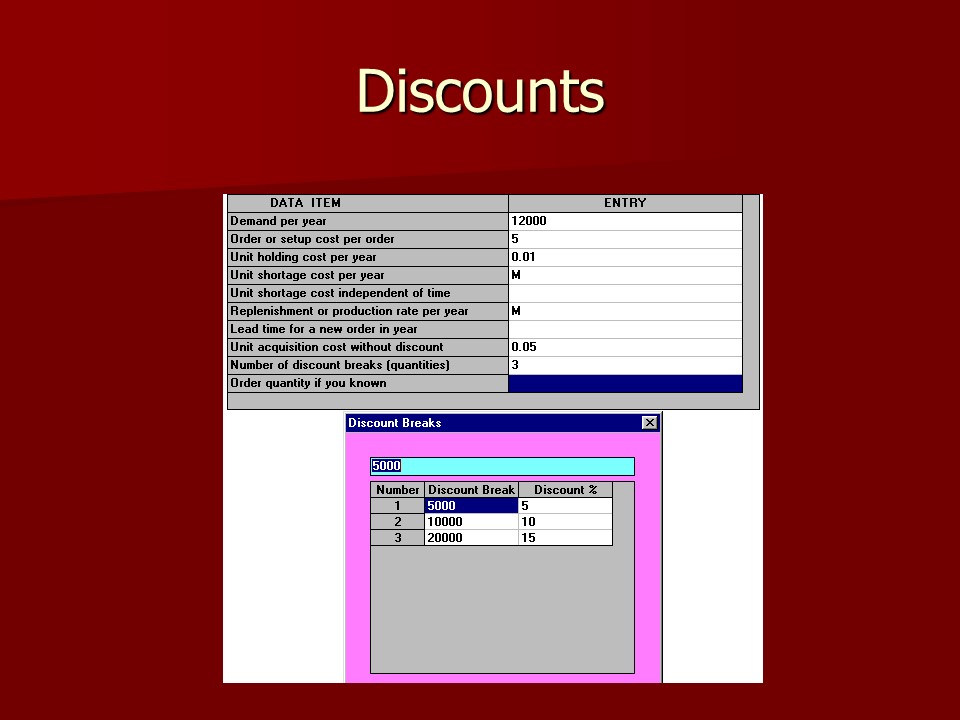
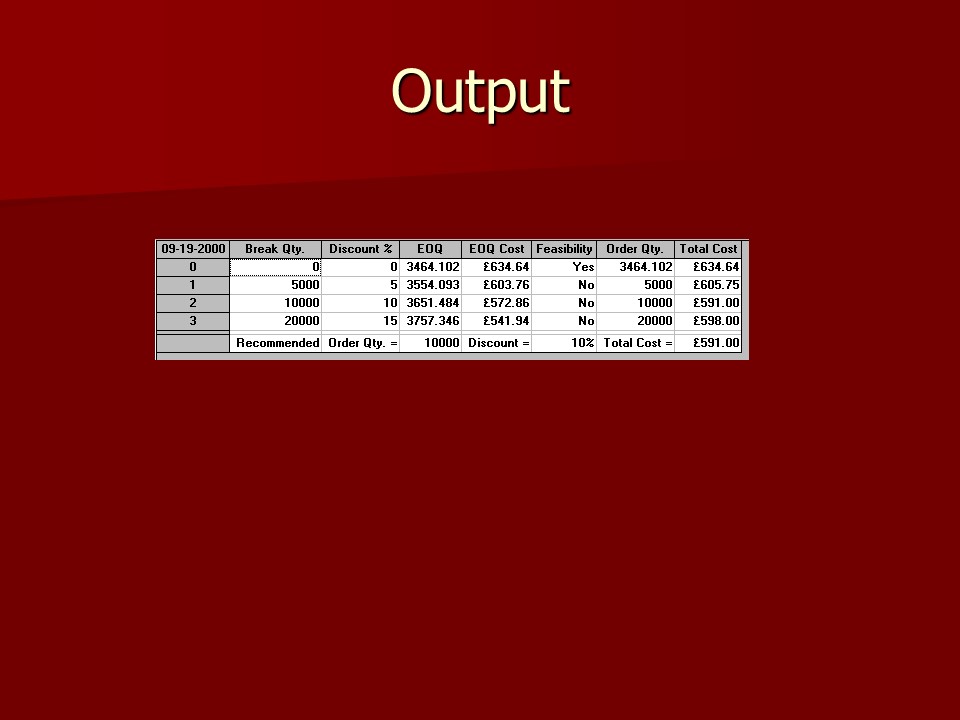
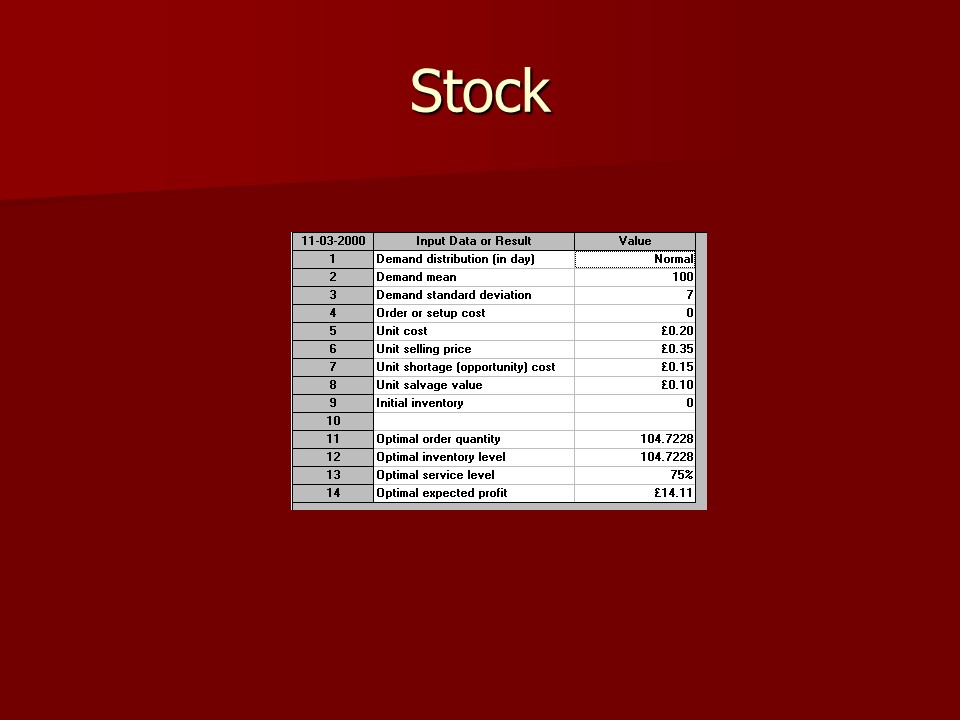
EOQ Model (applied for car wheel)
The aim of this model is to determine the most economical order quantity for an item for which the following is known:
- D = 325 parts /month.
- S = $20 per order placed.
- I = 20 per cent per month on average inventory value.
- C = $10 per part (Johnston 2003).
- The lead time is three working days.
- The following formulas will be used.
Direct Computation Model
To compute the p(u) where u is use during lead time, a general process is available.

Analysis
- The results allow to say that if R = 5 it is not sufficient but if R = 6 is is sufficient.
- the results are determined as R = 6, Q = 81.
- a stockout should cost $70.
- nif one set P(u) = 0.0261 by picking R = 5, then E(s) = 20[0.0190 + 2(0.0053) + 3(0.0015) + 4(0.0003)] = $0.71.
- Stockout cost per part is.
The data and results allow to say that $20 per part is sufficient to make the decision R = 6, value in the region $19 < π < $70 would led the organization to the same decision.
Q* is insensitive to π in that E(s) is minimal relative to S.
The model allows to estimate of the cost incurred when a part is demanded but not available,
In this case, the values of R and Q is determined directly.
Advantages of Inventory Control
- It maintain independence of operations.
- It meet variation in demand.
- It permits lexibility in production scheduling.
- It allows changes in raw material delivery time.
- It creates opportunities for economic purchase-order size.
Disadvantages of Inventory Control
- High holding, ordering, and setup costs.
- Inventory control does not allow to foreshadow production difficulties and problems in operations.
- Difficulties in control.
Difficulties of Inventory Control
- inventory control is complicated by;
- impact of external factors;
- the existence of multiple stratgies;
- multiple organizational bjectives;
- unambiguous goals;
- a hierarchy among controls.
Two Components of Inventory Control
- Inventory control system has two components:
- a monitoring process;
- an adjustment process.
Monitoring results from the generation of control intelligence and the use of criteria of performance. It attempts to check, evaluate, and ascertain whether performance quality is within proper limits.
Monitoring is developed to search for symptoms that indicate that production perations must be directed, realigned, or rebuilt.
The adjustment means:
- the demands of the production, or the balancing of corporate resources with market potential, is the essence of control activity.
Inventory control allows to end redirecting and reshaping effortd in order to maximize an organization’s impact and profitability. It is the area of corporate activity through which the resources and actions of a company make the most of changing marketing opportunities.
References
Bassett G. A. 1991. ManagementStrategiesforToday’sProjectShopEconomy. Westport, CT: Quorum.
Blake R. and Mouton J. 1984. TheManagerialGrid, 3rd ed. Houston: Gulf.
Chase R. B. and Aquilano N. J. 1989. ProductionandOperationsManagement, 5th ed. Homewood, IL: Irwin.
Dobyns L. and Crawford-Mason C. 1991. QualityorElse: TheRevolutioninWorldBusiness. Boston: Houghton Mifflin.
Dow, D. 1999. “Exploding the Myth: Do All Quality Management Practices Contribute to Superior Quality Performance?” Production and Operations Management, 8 (1), Spring pp. 1-25.
Johnston R. 2003. CasesinOperationsManagement, 3rd Edition Pearson Education Limited.
Naylor J. 2002. Introduction to Operations Management, 2nd Edition Pearson Education.
OEMHome Page. Web.
Slack N., Chambers S. Johnston R. 2003. Operations Management FT Prentice Hall.