Introduction
Most devices, toys, and equipment used today play significant roles in people’s lives, and one undeniable fact is that such devices are all reliant on gears. Jelaska (2012) argues that gears complete a wide range of roles to enable numerous products and mechanical devices to be even more effective. The use and application of gears have made it possible for human beings to achieve much with mechanized equipment.
The common gear train or set is simple in nature since it contains only two components; one of the components is known as the input gear and the other is the output gear. Such a set will provide a single gear ratio (Kapelevich, 2013). However, a human invention, and a desire to achieve, even more, has led to the creation of different, more complex, gear sets. One of the most ingenious and recognizable of these sets is known as the planetary gear unit (also called an epicyclic gear system). This literature review focuses on providing a detailed analysis of this gearbox system, as well as outlining its historical applications, and modern uses to date.
Analysis of the Planetary Gear System
The planetary gear system borrows its name from the behavior of the sun and the planets in the solar system, as the gears in the system behave in a similar manner to the planets. As such, the planetary gear set is, without any doubt, a versatile system (Gawande, Shaikh, Yerrawar, & Mahajan, 2014). Unlike a conventional system, the planetary gear system has two inputs. With additional inputs, the gear sets are, therefore, more complicated to design or use.
The system consists of four unique components that work together to produce the required results. The first component is the central gear and is known as ‘the sun’ (Wang, Zhang, Liu, & Wu, 2015). This gear can either be supported by a shaft or bearings, depending on the functions of the system. More often than not, the sun gear consists of a metal shell.
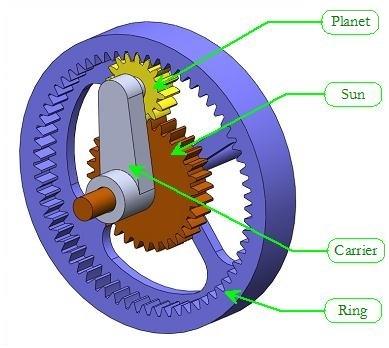
The second component in the system is usually composed of one or more ‘planet gears’ (Gawande et al., 2014), also called pinion gears. These planet gears must be held in place by a carrier in order to function optimally (Kapelevich, 2013). Within the gearbox assembly, the carrier should be attached to an output or input shaft, depending on its design. The planet gears can also be attached to another component within the assembly of the gearbox. By so doing, the gears are able to perform their intended functions.
The ring gear is the third element and is also referred to as the internal gear (Wang et al., 2015). This ring is usually helical in nature and the teeth of this gear are cut internally. The ring gear is usually connected to a given part of the gearbox in order to function. It is worth noting that planetary gear systems can be designed in different variations and combinations. The gears can also be arranged differently to meet a wide range of requirements (Kapelevich, 2013). The arrangements will be dictated by the speed-ratio expectations in order to fulfill the intended roles.
From this analysis, it is evident that the planetary gears within the system revolve or orbit around the sun gear. This orbiting principle is what makes the planetary gear set different from other contemporary systems. More often than not, the shafts of the planetary shafts are usually not fixed. This planetary motion is what gives the entire gearbox such a fascinating model of behavior (Jodder & Saha, 2016). The operational concept of the system is that two inputs are needed. The user or designer identifies the gears that should become the inputs. Normally, one of the two inputs is fixed in order to produce a proportionate gear ratio for the entire unit (Nandeppagoudar, Shaikh, & Gawande, 2017). This gear system is widely used when precision in motion control is critical. This is the reason why the planetary arrangement has been borrowed in a number of industries whereby higher torque can be transmitted in a controlled or limited space. Torque density in such an arrangement can be increased by adding more planet gears.
Historical Analysis and Uses of the Planetary Gear System
Although the use and application of planetary gears is something common today, relatively little is known about the specific history of the development of the system. The earliest known application of planetary gears is attributed to a Greek named Ptolemy (Jelaska, 2012). In one of his treatises, published in the second century, Ptolemy is known to have used rotating planetary gears to analyze the movement and behavior of the planets in the solar system (Kapelevich, 2013). In this work, the scientist and scholar predicted the movement of the moon, the sun, and the planets accurately. In this ground-breaking gear system, Ptolemy included the five planets that were known at that time: Saturn, Jupiter, Venus, Mercury, and Mars. The scientist indicated very clearly that each of the five planets always followed a unique trajectory. He represented this information accurately using a planetary gear system or train (Jelaska, 2012). He came up with a curve that has “for many centuries been described as an epitrochoid” (Jelaska, 2012, p. 48). From this analysis, it can be surmised that the first actual documented use of planetary gears was to analyze the solar system.
The famous Antikythera Mechanism has also been studied by many physicists and scientists because it represents one of the earliest applications of the planetary gear train (Wang et al., 2015). This mechanism was used in ancient times to display the behavior and movement of the moon within the solar system. The gear system was used successfully to produce the elliptical orbit followed by the moon. This mechanism has therefore been analyzed and studied widely by engineers in order to construct superior devices capable of completing a wide range of functions today.
Many historians strongly believe that the first complete planetary gearbox system was designed by an 11th-century astronomer and mathematician known as Ali-Muradi (Gawande et al., 2014). He is believed to have authored a number of manuscripts that describe the functioning of the planetary gear system. The manuscripts provided accurate details analyzing several complex clocks (Gawande et al., 2014), and seems to provide clear evidence that the first complete planetary gearbox was contained in an ancient clock invented by Ali-Muradi himself. He also managed to devise numerous devices that confirmed his ingenuity. However, it is the use of the planetary gearbox system that would eventually become the most popular and relevant in the future.
Borrowing much from the achievements and ideas of Al-Muradi, an Englishman named Richard managed to design a new planetary gearing system that would later be used in a revolutionary clock. This astronomical device would become common in different parts of Europe in the early 14th century (Jodder & Saha, 2016). The gearing system contained in the clock would later be studied by many scientists and, eventually, be applied in a wide range of innovative devices. Another notable application or historical use of the gear system is in the book wheel (Kapelevich, 2013). This wheel was designed as a revolving bookstand driven by a planetary gear system. The use of such gears made it easier for books to be oriented properly (Doane, 2015).
Modern Uses of the Planetary Gear System
For many centuries, mechanical engineers have tried to apply planetary gearboxes in different devices. Borrowing from ancient innovations, modern scientists and engineers have managed to come up with a wide range of applications for such a gear system and there are numerous systems that now use planetary gears (Doane, 2015). Much of this equipment dominates specific industries, such as packaging, construction, manufacturing, propulsion, and automation. Consequently, such systems have helped to keep the figurative gears of local and international economies moving.
Bohme and Frank (2017) acknowledge that conveyor belts in different industrial firms benefit significantly from the epicyclical performance of planetary gears. Conveyor belts and rollers contain drum motors that are designed using planetary gears (Jodder & Saha, 2016). The use of 2-stage epicyclical gears is a powerful concept that plays a significant role in reducing noise. The conveyors are usually propelled using the friction created between the belt and the drum motors. Such belts can be redesigned, depending on the products handled in a given factory. The invention of planetary gears is, therefore, something that has made it possible for many companies and manufacturers to realize their business objectives.
Planetary gearing has also been borrowed by manufacturers of toys and clocks. Due to the nature of the planetary principle, such gears can be used to produce toys that are capable of impressive movements. Indeed, the toy industry is one of the sectors that has benefited considerably from the application of planetary gear systems (Bohme & Frank, 2017). Manufacturers of clocks also use the machine because the planetary arrangement produces adequate torque transmission, unlike other gears. The issue of reduced inertia is also considered whenever applying the planetary arrangement in clocks (Nandeppagoudar et al., 2017). Since such gears require little or no servicing, many clocks can function optimally for many years.
Gas turbine engines have been observed to function efficiently using the planetary gear arrangement system (Jelaska, 2012). The engine is usually composed of several planetary gear assemblies. Such units work harmoniously since the shafts are coupled to different shafts outside the engine. The arrangement of the shafts and gears is designed in such a way that they can deliver the intended output. Gas turbine engines can, therefore, be applied in different devices and machines, to perform various tasks (Nandeppagoudar et al., 2017). This is further evidence that planetary gears have numerous applications.
Planetary gearboxes are currently being used in lifting equipment and cranes. The planetary gear arrangement is used in various pieces of machinery, such as winches, slewing drives, and wheels (Doane, 2015). Such planetary gear systems have replaced conventional designs here because they are capable of turning cogged loads that should be moved slowly. A study by Wang et al. (2015) indicated clearly that the market demand for planetary gearboxes was on the rise in different parts of the world, now more than ever before. Engineers have also been examining how such planetary systems can be applied in hoists in order to improve performance (Gawande et al., 2014). Experts argue that planetary gears are reversible and capable of responding to a wide range of commands.
Modern cars are fitted with various innovations relying on the planetary principle. A good example is a car mirror (Bohme & Frank, 2017). This technology uses a planetary system whereby several gears work in unison to produce the intended result. The planetary gear is usually engaged by a central sun gear. The external mirror is then mounted on a carrier. The position of the system’s carrier is determined by “the angular velocity of the sun gear” (Doane, 2015, p. 85). This invention has been made possible through the use of a planetary gearbox system.
The idea of 3 dimensional (3D) printing is the latest development that has benefited from the use of planetary gears. The main reason why such gear systems are used for 3D printing is that they offer a huge gear ratio. The inclusion of stepper motors makes it easier for people to produce accurate, high-quality 3D prints (Nandeppagoudar et al., 2017). Such motors turn much faster in order to produce the desired output. Many manufacturers of 3D printers argue that the inclusion of planetary gears makes it easier for users to produce better-quality images.
It can be argued that the number of devices and equipment able to be fitted with planetary gearbox systems is inexhaustible. Indeed, many engineers and scientists have been undertaking numerous research projects in an attempt to come up with more complex systems that can make work even easier. This research explains why devices such as gearhead motors, turbines, and lunar calendars are now fitted with planetary gear arrangements (Bohme & Frank, 2017). The efficiency of planetary gearboxes can also be used to explain why such systems will find numerous applications in the future.
Conclusion
The planetary gearbox has proved to be effective and capable of providing the required stability in a mechanical system. The gear system also tends to have reduced weight in comparison with other boxes. On the other hand, planetary gearboxes are quite hard to service compared to more conventional systems (Doane, 2015), and repairs should be done by professionals in order to minimize cases of injury or malfunction. However, studies have clearly shown that most planetary gearboxes can last for the projected machine’s lifespan. Another common issue associated with these gear systems is noise. However, planetary systems continue to meet numerous challenges that would not be solved using conventional gearboxes. In summary, a planetary gear system has low inertia, higher torque density, and is compact (Gawande et al., 2014). These attributes explain why the planetary principle has gained much attention recently and have led mechanical engineers to feel confident that the planetary gear unit will continue to be applied in a wide range of machinery, toys, engines, and automated systems, in the future.
References
Bohme, T., & Frank, B. (2017). Hybrid systems, optimal control, and hybrid vehicles: theory, methods, and applications. Natick, MA: Springer International Publishing.
Doane, J. (2015). Machine analysis with computer applications for mechanical engineers. New York, NY: Wiley.
Gawande, S., Shaikh, S., Yerrawar, R., & Mahajan, K. (2014). Noise level reduction in planetary gear set. Journal of Mechanical Design and Vibration, 2(3), 60-62. Web.
Jelaska, D. (2012). Gears and gear drives. New York, NY: Wiley.
Jodder, C., & Saha, J. (2016). Structural analysis of three-stage coupled planetary gear train and determination of efficiency. International Journal of Engineering Research, 5(9), 746-748. Web.
Kapelevich, A. (2013). Direct gear design. New York, NY: CRC Press.
Nandeppagoudar, S., Shaikh, S., & Gawande, S. (2017).Optimization of planetary gearbox for high reduction ratio. Journal of Mechanical and Civil Engineering, 1(1), 39-50. Web.
Wang, H., Zhang, T., Liu, G., & Wu, L. (2015). System-structure coupling dynamic analysis of planetary gears. Mathematical Problems in Engineering, 1(1), 1-10. Web.