Introduction
Nuclear life cycles are associated with many radioactive emissions. Alpha rays, beta rays and gamma rays radiations form the distinguished bands of emissions from power plants. Gamma rays have very short wavelength usually dependent on electric field and magnetic field of its particles in a free atmosphere. The ionizing radiation nature of gamma rays makes it easy for the atoms associated with its propagation to undergo radioactivity in expose to light. In this assessment, we will explore the potential hazards and threats that people may encounter while working in a nuclear plant. Based on the study of Pressurized Water Reactor, We will also assess the various risks involved in conducting inspection and maintenance exercise in the plant (Pentreath 1980, p. 23). By identifying and assessing the risks involved in servicing the plants, observations made on operating in dusty conditions is unusually entered and such areas form the basis of risk assessments. Inferring to the risk informs the mitigations strategies considered against international standards in the final part of this assessment (Trudeau 1991, p. 1-5).
Case overview
Pressurized Water Reactor exploits nuclear sources to generate energy used in a variety of industries. Despite its significant contribution to development of different economies, the reactor needs careful handling during operations just as it demands many precautions to carry out occasional inspections and maintenance services. Since the first Pressurized Water Reactor (PWR), developed by Westinghouse Bettis Atomic power in 1982, several companies have embarked on similar projects of building PWR to complement the ever-growing energy demands in a rapidly industrializing world with a continuously narrowing technology gap. A typical Pressurized Water Reactor consists of three distinct cooling systems. In the Main Steam System are the Condensation Feeder water System and Reactor coolant although only the Reactor coolant inhabits radioactivity. The main challenges faced by these plant operators include nucleate boiling and thermodynamic pressure which must be mitigated for higher efficiency. The loops in the containment of a PWR normally transmit water at high temperatures and pressures; this justifies the constant monitoring and maintenance of these components done to minimize the degree of potential risks that may occur in the plant. In the PWR, water plays a critical role as a coolant and steam pressure that turns the turbines, which in turn drives an external generator, it therefore important to avail adequate water to control potential risks and hazards (Radioisotope Power System Committee 2009, p. 16).
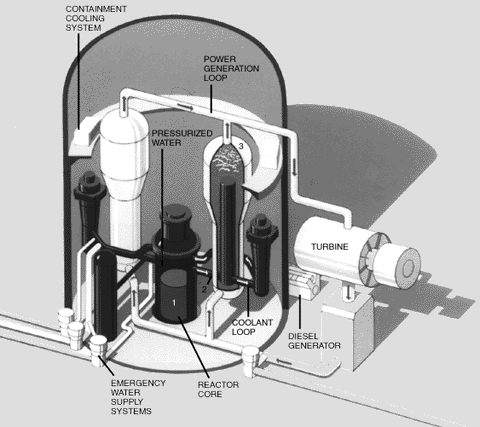
The multinational companies that build PWR include Siemens, Framatome and Mitsubishi. Upon installation they offer after sale services such as monitoring the productivity of the plants for their clients as they understand their technology better; this helps in their durability, maintenance, efficiency and modification aimed at conforming them to the new technologies. However, the experts are usually required to highly regard precaution measures to curb against the wide range of possible risks. Some of these risks, which predispose people to adverse health conditions, follow in the discussion bellow:
The operations of a PWR greatly depend on nuclear heating as the main input in its power production. In the entire nuclear life cycle, nuclear reactor forms just a small proportion of the full and half-atomic lifespan. In the reactor, uranium, coal and lithium undergo fusion through thermal decomposition. Over time, reprocessing of radioactive Uranium 238 and Uranium 239 isotopes may decompose in the reactor chamber resulting into gamma ray emissions by reflection on dust constituents. The air contaminated with this objects even in tiny sizes pose serious threats to the human gaseous system (Organization for Economic Co-operation and Development, 1997, p. 33). Therefore, specialists who enter the containment area of the reactant risks charred bodies if they lack highly protective covering. Safety equipment is therefore compulsory in any event of entering the processing room. Evidently, such environments inhibit proper air circulation because Uranium isotopes and Carbon compounds in the local atmosphere creates dense impure oxygen. This calls for the use of protective devices which are expected to mitigation inhalation of gases in the environment (OECD Nuclear Energy Agency 2001, p. 1-7).
In recent studies conducted to determine the levels of contaminants on the surrounding of Coolant system reactants, high levels of arsenic and lead showed in the gradual degradation of the containment area posed the risks associated with exposure to gamma radon rays radiation. In the event that workers in the PWR expose themselves to these radiations in highly concentrated areas, it has the potential of denaturing their body cells. In particular, exposure to gamma rays often results into cancerous blood cells. The condition of the victim may worsen as the patient develops sickle cell anemia. Due to the complexity of managing these kinds of illness, the workers require precautionary measures to enable them ward off the fatal risks such as this in the plant. Since, uranium and carbon concentration in the concrete wall may gradually diffuse into the external areas of the containment, the possibility of inhaling air contaminated by the radioactive substances in particulate forms instantaneously suspended in the most accessible areas of the reactor, pose the potential risks of choking the workers. In the areas of high lead, cobalt, uranium and carbon particles concentration, choking may result into blood dehydration and unusual clotting then fatal death because the patient lacks oxygen threshold for effective survival. In minor cases, the specialists working in the PWR risk respiratory infections due to oratory exposure to gaseous contaminants in the plant most sensitive areas (Soares 1997, p. 11).
Potential Risks
Due to their frequency and wavelength, gamma rays can penetrate the reactor chamber and cause harmful effects upon close range radiation on the workers. In particular, exposure to these rays in a Pressurized Water reactor may result into serious health hazards such as development of cancerous cells. Any leak from the reactor chamber would allow gamma ray emission to the accessible areas where the plant specialists are operating. In the event of such an occurrence, the plant poses a potential risk hazard on the body parts of the workers exposed to the particular environment. So that thick materials such as concrete, water and stock bocks make the most suitable protection against the rays.
Gamma rays comprise of ionizing radiation that may pose threats even in the absence of major industrial activities. Therefore, in the absence of protective material that may protect the workers against any eventualities, negligible impurities may infiltrate any faulty components of the reactor and ionize the surrounding atmosphere leading to adverse effects to workers. In particular, it may produce foam in the reactor and impair vision as well as blind the workers. Exposure or contact with the ionized air formed by disassociation of the radioactive lead, zinc and carbon from coal readily combines with the air to form oxide compounds of the substances. The compounds then pose great danger to the specialists as they cause irritation and blisters on the body whenever contact occurs.
Prior to the entry of the workers in the site, the PWR owners need to take precautions to ensure that no fuels leaks or pores are left to remains carelessly in the operation area. This is particularly important in minimizing the risks of fire outbreaks. The chances of all the workers dying in case of an outbreak while they are in the plant are very high. In addition, an ambulance with adequate first aid equipment and health facilities must be availed at the site to facilitate the process of taking care of any emergencies and persons who may be injured in the process (National Academy of Sciences 1980, p. 12).
Gamma rays have subatomic particles which have the potential of presenting grave risk hazards to humans when they get in contact with the body at the reproductive areas. Hence, according to research on exposure to the substances, the chemicals may cause genitival disorders in the lineage of the victim. The workers therefore risk life long illness with far reaching effects on their families, in the event that they make themselves obliviously exposed to the dusty chemicals in the coolant reactor room. Research shows that inhaling air contaminated with constituents of nuclear material such as uranium and zinc would inevitably lead to blood conditions such as leukemia. The company should also take care to desist from calling the same workers to come and conduct check up for plant each time it closes for inspection instead they should alternate to reduce the exposure time for the specialists.
Mineral elements of uranium, lead and carbon used in the plant sometimes contain traces of arsenic impurities. Over time, the impurities may infiltrate the reactor chamber and synthesize themselves on the irregular pores in the housing unit. Therefore, exposure to the dust material in the uncommonly accessed areas bears the potential risk of contaminating the blood of the workers. This may further lead to poor blood circulation system as the respiratory system inhibits oxygen flow because of inhaling impure air that has carbon impurities (OECD Nuclear Energy Agency 2000, p. 103).
In addition, burns and scalds form a large proportion of the risks in nuclear reactors leading to death. Any slight exposure to coal in highly sensitive but accessible areas usually require adequate protection and extreme care in order to avoid contact with highly poisonous chemical reactors in the coolant reactor that also has the potential to tarnish the skin. Moreover, any possible leak from the reactor in the containment because of cumulated heat or pressure due to sudden changes in temperature may also constitute a serious threat. For example, in past incidences of nuclear reactor accidents, just some slight leak led to the exposure of workers to gamma ray radiation particularly from uranium 238 and carbon materials. In the case of specialists inspecting a PWR in order to a certain whether it would suit further human and economic activities, their conditions of possible dangers while working in the site may greatly increase due to combination of radioactive gamma ray radiation and heavy metals impurities in the air. Therefore inhaling the air may result into fatal death due to congestion of the respiratory tract by mineral elements present in the dust particles and the surrounding air (Wilson & Crouch 1982, p. 44).
Mitigation Measures
Since production of electricity has to continue and the plants specialist must carry out regular inspection in maintenances and services on the PWR, observing mitigation measures is essential as it would minimize the extent of damage in case some risks occur. Due to the risks associated with the plant operation, inspection and maintenances, the workers take a number of precautionary measures. Usually, they consider the various ways through which they can remain safe after the exercise and at the same time conduct it without any industrial accident occurring to the team.
The first precaution involves proper dressing to protect the body from the risks of any exposure to the contaminated air and dusty conditions in the plant. While the air may look clear and deceptive, it greatly differs from the free air in the atmosphere. Specialists take good care since they understand risks involved and that the dust presents a potential hazard that may cause serious dangers to the workers. Clearly, wearing heavy jackets with cotton lining to absorb the gamma chips in the plant may be components of the dust. Hence, the dressing has to take into consideration, protection from misty conditions as the carbonic gases mixed with zinc and uranium particles can end up accumulating in the plant accessible areas. The activity gear worn by the engineers on this particular exercise ranges from helmets, overalls, boots and multi-layered jackets. The attire setup must include portable oxygen gas, as the workers may need to supplement a failed individual (Roberts Green & Graham, 1991, p. 132).
Workers must take precaution from any leaks in the containment area. Use of many walls to protect the containment area from possible risks of gamma rays to the external environment has significantly reduced the possibility of risks directly related with gamma rays. However, it amounts to ignorance if one would still go into the plant unprotected. Other protective measures include gloves and goggles which still form suitable defensive roles, important in safeguarding oneself from harmful effects of chemical impurities of radioactive material such as zinc and uranium commonly used in PWRs.
Moreover, the workers can never a certain whether all the heat dissipated completely when the plant closed for inspection until the time of the actual exercise. Therefore, testing for high temperatures require that the workers keep some safe distance from the coolant reactor system and in particular the reactor. In the process, they can use metal linkages to coordinate the test for heat and pressure consistent with the processes of the plant normal operation. The safe distance is important for two important reasons; to keep the workers from burns and scalds that my result from underestimating the temperature of the coolant system and the pressure of the reactor. Again, this keeps the workers against confusion and errors resulting from anxiety in the event of risks in the loops faults. In addition, the workers need to ensure that all the fire extinguishers disposable for the exercise can best suit the activity in the event of fire.
Another precaution usually emphasizes the need to limit the time of carrying out the tasks of inspection and maintenance services in the plant. In case of any slight exposure, this measure would serve in limiting the risk of contacting diseases such as cancer and respiratory infections. Naturally, as specialists, sometimes one may find himself or herself exposed to the dusty conditions in the plant while inspecting the area. However, with limited time for exposure to the prevailing condition, the workers can only inhale a small proportion of the contaminated air (International Atomic Energy Agency 1988, p. 2).
Features of International Standards in the effectiveness of Mitigation Measures
International standards for mitigation against risks in PWR consider the classical assumption that assumes risk attacks and exposure follow in similar magnitude and direction. The mitigation measure suggested follow the same principle as we can see that steam and heat protection-according, influence the protection design with the view of reactor intensity. This assumption of international standards caters even for the minimal risks such as exposure to dust particles settled on the different chambers of the plant reactor. The linear no threshold principles guides the protection practices of workers on the site on this particular day just as it would to other workers in the plant on a normal day. It covers the levels of exposure to gamma ray radiation by limiting the extent of exposure to the radiation. This guide has significantly informed the threshold distance precaution in dealing with heat and pressure intensities in a nuclear reactor. In this regard, both the measure and the international benchmark have greatly considered the need to observe care while approaching sensitive components of a plant even while under protective gear. However, the principle may fails to forecast the consequence of direct exposure to minimal radiation. For instance, it claims that when the risk of exposure occurs to a lesser degree, the effect would also be less (Okrent 1981, p. 67).
The measure recommending for availability of sufficient firefighting equipment and additional gear for protection against constituents heavy metal suspension in the environment all improve the effectiveness of the measures suggested. According the International Commission on Radiological protection (ICRP), various recommendations influence the activity of the workers including the measures and mitigations. Its justification prohibits any practice or procedure that does not bring positive benefits. In this case, the workers put in their efforts with the intention of refurbishing the plan if necessary but most importantly, to carry out an inspection that would direct their action to areas with fault and errors. All in all, there are expert engineers in the mission of improving the output of the PWR and the same are set to eliminate any dangers that may risk the lives of normal workers in the company. Hence, their move attains adequate justification (Primack 1975, p. 15).
The optimization aspect of the exercise as recommended by universal standards falls just in the core of the engineers actions. Ideally, some of them could have had appointment from the PWR manufacturers such as Siemens, Mitsubishi or even Westinghouse. These companies operate the plants with profit motives and understand economics of cost reduction. In addition, the universal law that covers the rights of workers always heeds the calls to keep their lives safe from dangers while they provide essential service to the company’s investments. This agrees with the intention of the measures put in place to guarantee the workers success in their mission and ensure that even in the case of slight exposure to certain risks, they still end up with a chance to get restoration. Therefore, this recommendation forces the company to take the lives of the workers very seriously and grant them all the required material that would ensure they function safely. The limiting aspect of the mitigation recommendations also finds resemblance in the international standards codes that demands minimal exposure to the risks of duct conditions in the plant. In our discussion, we suggested that workers could do this through limiting time in the plant and period of contact in high sensitive areas of the plant. It is no coincidence that ICRP recognizes the need to reduce the severity of the risk occurring while they conduct maintenance work in the plant. However, other recommendations of the international standards do not apply in this scenario (Cho, & Jones 1995, p. 23).
Conclusion
Companies involved in the manufacture of PWRs have made commendable efforts in inspecting and maintaining the plants. These efforts create safe working conditions in the plants favorable for working as they minimize possible panics of the employees due to risks occurring. Regular inspection to seal all the possible leaks that would cause adverse health effects on the workers by the plant specialists however should not expose the specialists’ lives to the dangers of polluted air in from the coolant reactor system. The specialists must ensure that they observe the standard requirements on their attire the exercise (Jaeper 2001, p. 89). Lathered jackets should be included to mitigate exposure to the harmful effects of radioactive gamma rays. In as much as the lives of the specialists are concerned, the management has to confirm that all the loops are leak proof to minimize risks of death due exposure of the workers to gases contaminated with radioactive substances such as lithium, uranium and titanium used in the plants. While this assessment concentrates on the risks and risks involved in the use of PWR it should be noted that radioactive materials only pollutes water in the primary loop and not the one in secondary loop; this is because the primary loop is completely separate from the turbine loop (National Research Council (U.S.) & Committee on separation Technologies, 1996, p. 1-9). The risk hazards associated with PWR are grave, they can cause cancer, sickle cell, and genetic disorders that can last through generations, it is there fore imperative that exposure of the gases is minimized and exposure time of the specialists reduced by alternating them. Otherwise, they are of great importance in the contemporary world which requires regular propulsion for their aircraft carriers and should be maintained regularly to contain hazards (Mannan 2005, p. 4).
Reference List
- Cho, F. L. & Jones, E. D., 1995. Risk and safety assessments: where is the balance? : presented at the 1995 Joint ASME/JSME Pressure Vessels and Piping Conference, Honolulu, Hawaii. (296). Michigan: University of Michigan.
- International Atomic Energy Agency & OECD Nuclear Energy Urgency. 1988. Severe accidents in nuclear power plants: proceedings of an International Symposium on Severe Accidents in Nuclear Power Plants, New York: International Atomic Energy Agency.
- Jaeper, C., 2001. Risk, Uncertainity, and Rational Action. London: Earthscan.
- Mannan, S. L., 2005. Loss prevention in the process industries: hazard identification, assessment, and control, (1). London: Elsevier.
- National Academy of Sciences. 1980. Nuclear reactors: how safe are they. Washington, DC: National Research Council.
- National Research Council (U.S.) & Committee on separation Technologies. 1996. Nuclear wastes: technologies for separations and transmutation. Washington, D. C.: National Academies Press.
- OECD Nuclear Energy Agency. 2000. Reduction of capital costs of nuclear power plants. Paris: OECD Publishing.
- OECD Nuclear Energy Agency., 2001, Nuclear fuel safety criteria: technical review, Issue 964. Paris: OECD Publishing.
- Okrent, D., 1981, Nuclear reactor safety: on the history of the regulatory process. New York: University of Wisconsin Press.
- Organization for Economic Co-operation and Development., 1997, Nuclear safety research in OECD countries: capabilities and facilities, Paris: OECD Publishing,
- Pentreath, R. J.,1980, Nuclear Power, Man and the Environment. London: Taylor and Francis LTD.
- Primack, J., 1975. Nuclear Reactor Safety: An introduction to the issues. Bulletin of Atomic Scientists.
- Radioisotope Power System Committee.,2009, Radioisotope power systems: an imperative for maintaining U.S. leadership in space exploration. Washington, DC.: National Academies Press.
- Roberts, M., Green L., & Graham J., 1991, In search of safety: chemicals and cancer risk. New York: Havard University Press. Print.
- Soares, G., 1997. Advances in safety and reliability: proceed of ESREL’97. International conference on safety and reliability. Lisbon, Portugal, Volume 1. Elsevier.
- Trudeau, P., 1991, Energy for a Habitable World. New York: Crane Russak.
- Wilson, R. & Crouch, E., 1982, Risk/Benefit analysis. California: Ballinger.