Introduction
During production, raw materials are converted into finished products, and this process involves procurement, allocation of resources as well as utilization of the resources. This operational process requires that goods are produced efficiently and in the most economical way. For an organization to realize its profits and satisfy the consumers, production is a key area of focus. Production management requires decisions be made about the products design, planning, and control.
For the processes to run smoothly, the movement of information and materials should be consistent so as to unite the parts involved into one. This way, the goal, which is the final product, is achieved by many units working as a team. Given that the modern customer requires the products at the most convenient time, location, and at a low cost, an organization should perform its production process based on the nature of the targeted market.
Inventory helps to ensure that the organization responds to consumer needs in the shortest time possible. The nature of the raw materials and transportation is also another area of focus in production because a lot of costs are incurred in this area. This article will discuss on operations management using the Stickley Furniture Company as the model to explain the procedures and processes involved in the production.
It will further discuss how the management can efficiently improve product and service quality at a low cost while meeting the market demands (Ross, 2010). Efficient management in operations is an essential component in supply chain; it not only simplifies operations and cost but also acts as an area in which an organization can focus on so as to gain a competitive advantage.
Stickley Furniture’s Production Processing
Production in supply chain management comprises of drivers that support the conversion of raw materials into finished products that appeal to customers. These include the procurement process, designing the supply chain, inventories, transportation of supplies and the finished products, warehousing, and the collaboration of these units to work as a team.
For the Stickley Company, timber is sourced from outside as well as other products such as glue and other equipment that are used in production. Its supply chain is centralized in one unit where procurement, production, and distribution are operated. It has various dealers outside who are the main point of contact between the organization and the suppliers.
Inventory involves the semi-finished products which are assembled and delivered once orders are received. The scheduling office is used in locating products; this is a one way form of communication in which may not involve the rest of the units (Stevenson, 2009).
The main form of the production process in this company is a job shop in which involves companies which produce a low volume of goods that have a wide variety. Given that when timber is received, the procedure is standard, they are cut into smaller sizes using a computer-controlled optimizer saw. In this case, the optimizer is a standard tool that can be adjusted to fit the required sizes. It is always the first operation performed when timber is received.
Once they are cut into smaller sizes, differentiation starts and parts are produced according to the king of item required, thus the wide variety in production. The pieces are assembled so that the workers to come up with the final product. This means that the equipment used are not extremely flexible because the parts are defined and procedures require standards. For instance, saws and sanders are a must-use for any product.
The final product has different processing requirements, for instance, some items may require carving while others do not. The function of the furniture also defines the processes to be carried out, design is not high because the variety available offers many design changes are not frequent.
To a lesser extent, the continuous product processing is also applied in this organization because the products are standardized and some workers apply low skills while others need to be highly skilled. For example, carving requires skilled craftsmen while other procedures like drilling and mortising can be performed by low to moderately-skilled workers (Stevenson, 2009).
In Stickley Furniture the management stamps the date of production on every item, to ease tracking. Items are also stamped for identification during the assembling process. Stamping the items names and dates of production makes the assembling task simpler and the location of an item can be tracked easily. This is because the procedures are continuous and items made on a day have a standard period in which they are expected to be ready.
If required urgently, then they can easily be retrieved from the production stage as defined by the date. Updated records are kept to ensure that those items can be matched easily with their original pieces based on aspects like wood type and the finishing. Bar code stickers are used to simplify the process because once they are scanned in the computer; they are located from the scheduling office (Stevenson, 2009).
For supply chain management to be effective, this is essential because it promotes collaborative planning in which the participating partners can share information as compared to the simple exchange. In this case, the parties purchasing timber, the production workers, and the inventory team should share information such that orders can be placed by just checking and updating the status from a common system. This will eliminate the long process that is followed while establishing product availability when an order is placed (Ross, 2010).
If the company received an order for 40 mission oak dining room sets, it would require careful planning, scheduling, and processing to ensure that the customer needs are met at the shortest time and the right customer expectations. This is necessary because it adds value to a product.
In this case, first, the management would need to establish the complete parts available in the inventory. This will help them establish the exact number of pieces or items that will need to be prepared from scratch. This way, a plan is made to come up with the amount of timber that will be required to produce the deficit as well as replace the ones obtained from the inventory. Once this is accomplished, it will schedule the timber for timber to be delivered in the workshop.
Next, it will match the skills required, with the product for it to assign the workers on the task while considering the volume to be worked. This also factors in the time before delivery can be done. Once the available workers are identified the task is commenced, while some workers are working on the unavailable parts, others should be working on assembling the ready parts from the warehouse.
This ensures that the products are availed at the shortest time and in the best quality because inventory saves the organization the procedures required for such an amount of furniture. Finally, distribution is organized to ensure that the products are delivered according to the customers instructions. So in this case factors to consider include; the funds required, amount of labor required and the time available (Stevenson, 2009).
Stickley Company’s level production policy is convenient for this order. This is because the company keeps an inventory ready for the demand period. It is likely that the order received could be furnished if the items required are ready for assembling. The fact that items can be located from the scheduling office makes, it is easy to determine what is available and what needs to be acquired. This way decision-making is fast and efficient.
The company has employed many workers who are utilized through preparation of inventory items. The extra human resource provides labor when demand rises. Another advantage of this system is that workers have specialized according to their skills. This causes the determination of the workers group to which the job can be assigned and scheduled. As outlined below, the production process is the central point where the supply chain drivers interact (Stevenson, 2009).
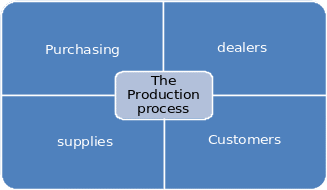
There are challenges that may arise while responding to the oak dining set order, for instance; the inventory may not be having adequate pieces that match the customer’s requirements. This means that the whole production process would have to be carried out, and this may take a lot of time.
Another challenge can be the risk of unsatisfactory products given that the workers are responsible in making decisions about the quality of the products. A poor judgment may be done which can result in losses in case the products do not satisfy the customer. Obtaining workers readily to perform the task immediately can be a challenge if it happens to be a peak season when labor is a lot.
If there happens to be a multiple of orders, then there is a likelihood of delay because job sequence is determined by the supplies on hand. If the oak wood is not available, then it is likely that it will be scheduled later when supplies are obtained. The scheduling is planned 8-10 weeks ahead, and this may disrupt operations if the order given is urgent (Stevenson, 2009).
Recommendation for Stickley Furniture
The company keeps track of items by keeping records as defined by the dates stamped on these items. This could be improved by specialization of the production process such that similar items are produced in the same location. This way tracking will not require a lot of record-keeping because similar items are stored together.
This way it will only require barcode stickers to identify the location of an item. The company has a range of low-skilled workers and highly skilled ones. It would be necessary if the low-skilled workers could work along the highly skilled craftsmen so that the learning process can be enhanced. Through this, innovation and creativity can be improved, and the company can acquire more workers who are skilled (Ross, 2010).
The issue of quality is a sensitive one because a mistake on this can lead to substantial losses in terms of resources and business. This should have a standard measure through which products can be defined. When this responsibility is left for the individual workers, it is likely that the products offered will be inconsistent in terms of quality. The organization defines the quality standards that each worker must attain to build customer loyalty.
This will eliminate the probability of a customer getting unsatisfactory products. Another area is on the issue of repair and sharpening of equipment used. This process involves the use of resources while there is no output. Therefore, such activities can be allocated downtime such that the time used for maintenance can be included in planning. This will minimize waste of resources and improve efficiency, as well (Ross, 2010).
The management defines the level of output expected to maximize the production capacity for the workers and the equipment used. This simplifies the planning process since the profits can be estimated by comparing the estimated output against the costs incurred. Another area of concern is the costs incurred on inventory.
This could be reduced by working with the dealers by encouraging them to have inventories for the products that have demand. This way, the product is taken nearer to the consumer’s location. Once an order is placed, the final product can be assembled and delivered faster as opposed to assembling from the company’s workshop (Ross, 2010).
Warehousing is an essential aspect in supply chain; the locations determine the costs that are likely to be incurred during transportation. If the warehouses are located near the targeted markets, then the inventory costs go down. Given that Stickley Furniture maximizes its production while anticipating for the demand that comes in the peak season, it is advisable that the company introduces warehouses. These can be located near the leading dealers such that when orders are placed, the turnaround time is effective.
This also favors the customers who would love to purchase directly from the organization. It also familiarizes the organization to the customers because customers get to know the company’s existence and demand also increases especially for the foreign markets.
For Stickley, a centralized warehousing location may not be convenient because the dealers are decentralized. Therefore, the company can opt for decentralized locations for the dealer’s convenience. It will improve the level of responsiveness and efficiency of customer service (Ross, 2010).
Conclusion
Efficiency in production management gives an organization a competitive advantage. This is achieved by maximizing the available resources to obtain maximum output. Today, organizations are developing strategies to improve their efficiency in operations to reduce costs without compromising the level of customer service. If an organization introduces machineries that consume a lot of power, the productivity should be much higher to cover the costs incurred. In the case of Stickley furniture, the saws and sanders used should be included during the planning process to ensure that such costs are accounted. This minimizes waste in the production process. A market-driven demand is also essential because it encourages innovation and increases sales volumes. When the production process takes minimum resources, an organization can provide quality products similar to those of competitors at a lower price and thus increase its demand. When organizations respond to consumer needs fast, they add value to their products and this gives these organizations a competitive advantage.
References
Stevenson, W. J. (2009). Operations management. Boston, Mass: McGraw-Hill.
Ross, D. F. (2010). Introduction to Supply Chain Management Technologies. CRC Press.