This paper outlines various aspects required for the effective implementation of engineering and construction projects by examining the approach used by the Custom Woody Company. This is a family business founded by Ron Carpenter in 1954. Initially, Ron Carpenter learned carpentry under apprenticeship. Ron Carpenter then used his entrepreneurial skills to establish the Custom Woody Company.
The company started by producing cabinet furniture. Nowadays, the company imports hardwood and utilizes the local indigenous softwood as raw materials. Currently, the family running the business has a formidable workforce. Owing to an increase in demand, Ron Carpenter has decided to move to subcontract work, which involves supplying and installing countertops, and other necessary cabinets required for new commercial construction.
Most construction and engineering companies often survive on contracts and subcontracts (Adams, 1995). In subcontracts, a general or main contractor hires subcontractor, who performs specific tasks as a part of the overall projects (Adams, 1995). The subcontractor is then paid by the main contractor for the services rendered. There are a number of advantages and disadvantages when both subcontracts and main contracts are considered.
Main contractors generate a higher income as compared to subcontractors because the construction tender is fully awarded to them by the client (Conrow, 2003). The main contractor controls the whole project. Winning a tender for the production of big products requires a massive investment. On the other hand, subcontractors venture into subcontracts due to the lack of capital and workforce required to complete the project at hand. As a result, they offer their services on contracts. This is advantageous because subcontractors provide specific tasks within a specific period.
By examining the case of the Custom Wood Company, a number of lessons can be learned. Ron Carpenter decided to move into subcontract work owing to an increase in the demand for cabinet furniture. Looking at the company’s reputation, it would have been better if Ron had prioritized winning tenders as the main contractor.
This would enable his company to generate more income. In this case, the company should aim at acquiring major construction projects and hire subcontractors to offer other services. In this case, the Custom Wood Company will produce the required furniture, while the subcontractor works on the other aspects of the project. This will give the Custom Wood Company a higher bargaining power because it will be in charge of the overall management of the project.
Looking at the Woody 2000 project, a number of issues concerning communication and the management of people are observed. The figure below represents a project organization chart. The Woody 2000 ought to have used this organization.
The relationship between participants working on the Wood 2000 project was poor. The project lacked proper coordination and communication. The project was managed by Spencer Moneysworth who was responsible for its successful implementation. However, when Spencer Moneysworth realized that more time was needed to concentrate on the paperwork, he decided to hand over the management of the project to Ian Leadbetter.
Leadbetter, an engineering graduate with no management skills, took the opportunity and promised to deliver quality work. This was a big mistake. Leadbetter lacked managerial skills thus he was not the right substitute for Moneysworth. The company had other qualified individuals who could have spearheaded the management of the project. Ivar and Win had management skills, and one of them would have been a perfect replacement for Spencer Moneysworth.
The project lacked proper coordination from the people in charge. This would have been solved by laying down a well-structured plan. The management should have informed the company’s personnel about the intended project during a well-organized meeting. The first meeting aimed at deciding whether to move the production to a new location or keep it at the initial site.
Thus, it would have been appropriate for the management to organize another meeting in order to inform the rest of the team about the intended expansion. Thereafter, the management should have crafted a plan for carrying out the possible extension. The management should have been involved in the allocation of duties.
This would have eliminated the risk of poor duty allocation. For example, Moneysworth’s mistake would have been prevented in such a case. At the time when it was obvious that the project would not be completed within the expected period, it would have been better to change the plan and schedule. This would involve increasing the workforce so as to cover the lost time.
In terms of record-keeping, the project manager should have done all the necessary records related to the project. All facts related to the project should have been forwarded to the project manager. The project manager would then have had a clear picture of all the proceedings. Records related to design, finance, goals, and achievements ought to have been kept. The figure below indicates how responsibilities would have been shared.
The other aspect which is important to view with regard to the Woody 2000 project is its cost. The top management estimated that the project would cost $17 million. However, EID‘s cost was set at $20 million. Such a high price occurred due to the lack of consultation between EID and Woody’s top management. This led to an overestimation of the price.
Besides, EID did not give a sincere explanation. According to EID, their quotation included estimation for uncertainties and a fee for planning services. It became apparent that the project had an overestimate of the price when Moneysworth presented EID’s project plan to the management. However, the recognition of the problem was a bit too late. This phenomenon had significant effects on the overall project.
First, it resulted in the delay of the project. Second, it increased the project’s overall cost. When crafting an expenditure plan for any given project, it is important to involve all the stakeholders. The cost would have been minimized if the company had crafted a project plan. This would minimize extra costs which EID charged with regard to planning services. When a project encounters some setbacks due to poor planning, a number of steps can be taken to resolve the matter.
Risk identification and management are required for the successful completion of any project. Risk management planning is the process of determining how to approach and resolve risks anticipated in the project (Molenaar, Anderson & Schexnayder, 2010).
Risk identification and management can be done through a number of ways. One of such methods is the Appriss approach. The Appriss approach to risk management starts with a plan that defines the scope and process for the identification, assessment, and management of risks which could impact the implementation of the project (Heldman, 2005). The objective of the risk management plan is to define the strategy required to manage project-related risks; thus there is acceptable minimal impact on cost and schedule as well as operational performance.
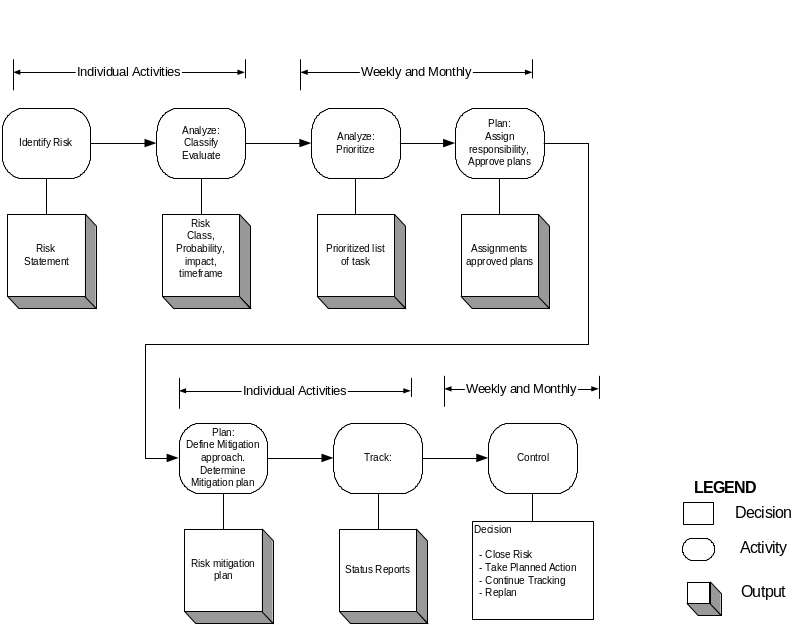
The approach accepted by EID to solve the cost-related risks was effective. EID agreed to complete its task through a fully reimbursable contract. Further negotiations allowed EID to offer their services on a cost-plus basis. Under this scheme, EID was paid per hour. The payment covered wages, head office overhead, and payroll burden. However, another option would have been to lower EID’s initial quotation. In return, EID would be given time to complete the project instead of terminating their contract.
The Custom Woody Company encountered a number of obstacles due to poor planning. The Woody 2000 project had poor record-keeping. For example, Kim locked the monthly cash flow charts in his locker and this significantly affected cost evaluation. Moneysworth chose his successor without involving the top management. His successor was inexperienced, and this also influenced the implementation of the project. In addition, Moneysworth decision to choose EID to quote the expected cost for expansion was wrong.
The decision ought to have been taken collectively. Other challenges resulting from poor planning occurred when Faster was given the responsibility for managing procurement. Leadbetter and Faster then abandoned their duties and went on vacation. This significantly affected the delivery schedule and caused a delay in the completion of the project. Another issue occurred when it was discovered that the paint surplus did not meet the set standards. The worst effect the delay had on the company was the loss of production, customers, and sales opportunities.
References
Adams, S. (1995). Risk. London: Routledge.
Conrow, E. (2003). Effective Risk Management: some keys to success. New York: AIAA.
Heldman, K. (2005). Project Manager’s Spotlight on Risk Management. Connecticut: John Wiley & Sons.
Molenaar, K.R., Anderson, S.D. & Schexnayder, C.J. (2010). Guidebook on Risk Analysis Tools and Management Practices to Control Transportation Project Costs. New York: Transportation Research Board.