Toughness of a material is defined as the strength of the material to be able to undergo stress and strain without breaking or fracturing. Thus, it is measure by the energy the material is able to absorb when strain and stress are applied without breaking. Therefore, the more the energy required to break a material the tougher the material and the lesser the energy required to break the material the less tough the material. Most tough materials when exposed to stress tend to undergo plastic deformation without breaking. The unit for measuring toughness is Joules per cubic metres.
Toughness is measured using Compact tension test, Izod test and Charpy test.
The Charpy Test
A small notch is cut into the square shaped material to be tested. The toughness of the material is then measured by the distance that the pendulum will swing after successfully breaking the material. Thus, the further it swings then it means less energy was absorbed while the lesser it swings then the more the energy absorbed during the breaking. The pendulum is fixed to a pointer that shows the readings for distance the pendulum swings. In conclusion, the material with the highest toughness absorbs more energy and provides a shorter swing of the pendulum while the material with a lesser toughness absorbs less energy and the pendulum swings the furthest. The test if illustrated in the diagram below.
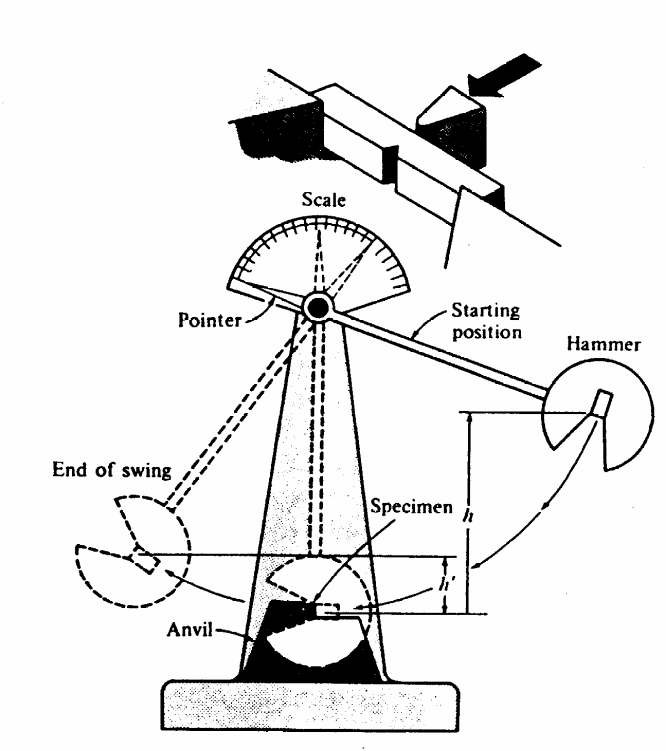
Corrosion refers to the slow but consistent destruction of metallic materials due to the effects of a chemical reaction. It is mostly associated with rusting of iron materials due to the formation of iron oxides from the process of oxidation. Thus, the process of corrosion is irreversible and is catalysed by the chemicals present in the environment of the material.
Corrosion occurs as a result of the material substance reacting with chemicals in its environment. The process usually requires the presence of up to four elements to take place. These elements are found in the environment in which the material is found and they include the metallic material or alloy, anode and cathode as well as an electrolyte.
There are different types of corrosion which include:
- Uniform corrosion.
- Galvanic corrosion.
- Pitting corrosion.
- Stress corrosion.
- Crevice corrosion.
- Intergranular corrosion.
- Filiform corrosion.
- Erosion corrosion.
- Fretting corrosion.
- Corrosion in cement.
Galvanic Corrosion
This type of corrosion takes place where there is a presence of two or more metallic materials that are immersed in a substance that acts as an electrolyte. The metals must have different electrode potential such that one metal will act as the anode while the other will act as the cathode. The more active metal is the one that becomes an anode while the one with active becomes the cathode. The substance in which they are immersing in should act as an electrolyte with the ability to permit the movement of ions from the anode to the cathode. Thus, the process of moving ions corrodes the anode while the cathode corrodes at a slower rate. This is the process that is used to coat galvanized iron sheets so as to prevent them from corrosion.
Galvanic corrosion is likely to occur in the oceans especially in seawater. Thus, it hugely affects the operation of ships. It also occurs in batteries that have an anode, cathode and an electrolyte. The prevention of galvanic corrosion involves the use of sacrificial anodes which are mostly used to protect the materials that are not supposed to corrode. These sacrificial anodes are mostly made of zinc and magnesium since they have very low potentials and thus take a longer time to corrode gradually. Furthermore, to ensure the materials are not affected by corrosion, when they deteriorate another layer is added.
References
Cottrell, A. (2012), The Mechanical Properties of Matter. London, UK: McGraw Hill.
Dowling, E. (2011). Mechanical Behavior of Materials. New York, NY: Prentice Hall.
Green, D. (2009). An Introduction to the Mechanical Properties of Ceramics. New York, NY: Cambridge Univerisity Press.
Hertzberg, R. (2010). Deformation and Fracture Mechanics of Engineering Materials. London, UK: Wiley.