Much progress has been made in the field of exoskeleton robotics. Two significant developments are prominent: the passive and the active exoskeletons. These two technologies have been used over the years. Most of the current exoskeletons in operation are designed to help the disabled, and the elderly to move. Even though most of the work in the field of exoskeletons is still experimental, there are significant challenges hindering the implementation of exoskeletons in the industry including safety and discomfort. For an exoskeleton to be compatible with the human body, its kinetics and kinematics must be correctly done—also psychological factors like feeling safe to determine whether workers can accept a device or not. This review critically analyses the five leading industrial exoskeletons: Paexo, Airframe, Mate, Skelex and Shoulder X and suggests ways of meeting the structural and legal challenges for their industrial implementation.
Summary of Existing Studies and Their Outcomes
Passive and active exoskeletons development helps support humans to run some activities that require potent abilities. Several scholars have researched various technologies to aid exoskeletons development. de Looze et al. reveal that the number of sensing technologies and lightweight materials used to develop the next exoskeletons is rising (18). The current exoskeletons are mainly designed to support disabled people in managing their activities. However, the development of the skeletons for industrial use slows down compared to those used for health care. de Looze et al. also indicate that the effectiveness of physical load reduction is crucial to ensure lifting and bending lifting. Industrial application has also seen an increase in interest, which makes it one of the rising technological aspects. Nevertheless, de Looze et al. indicate that few of the exoskeletons used in the industries are in actual application. This further reveals that the number of new technologies can rise in the future as several areas are yet to be explored.
The study’s outcome showed that the exoskeletons reviewed were mainly meant to support dynamic lifting and lowering of the labourer’s weight, stooped working postures, and general system support. The study also found that exoskeletons were meant to carry out some activities requiring specific permission. Moreover, the study indicated that tasks such as patient transfer, construction work, carpentry, and agricultural work were achieved using exoskeletons. The study also paid critical attention to the statistical testing of the devices using techniques such as PLAD (Personal Augmentive Lifting Device), the Muscle Suit, BNDR (Bending Non-Demand Return), the HappyBack, and the Bendezy (18). The physiological aspects of the study involved muscle activities utilizing the back, leg, and shoulder based on the different amplitudes and muscle fatigue. The biomechanical parameters involved loading the back with different types of forces. The research indicated positive effects for both cases, revealing active and passive exoskeletons.
Another study by Voilqu’e et al. pointed at the application of exoskeletons in the classification, structural analysis, and structural complexity indicators of industrial exoskeleton technology. The research indicated that manufacturers had shown an increased interest in using exoskeleton technology to ensure faster and more accurate plant operations (6). The analysis provided a new approach meant to improve work quality, the effectiveness of tasks, and productivity, by integrating human intelligence, skill, and robotic assistance. The study’s approach involved categorizing the industrial needs into three distinct categories: awkward movements and posture, manipulation of a heavy workload, and aid for assembly efforts. The research used an example of a car manufacturing plant to distinguish the classifications of the exoskeletons’ categories. The research reviewed literature, revealing 62 unique exoskeleton solutions and their industrial potentials, opening the future of possible industrial applications for the systems (6). The study listed the identified solutions based on their source of content, the status of development, source of energy they use, their targeted body parts, their mass, and the industrial needs they fill (6).
The research conducted a structural analysis of the existing exoskeletons, highlighting the significant issues associated with their structures and actuation systems. The study found that user feedback and industrial performance expectations converged on the same concerns around the devices’ mass, effort distribution, and actuation types. The research also explored the kinetics of the systems, which was a crucial aspect of the study as it involved a deeper analysis of the designs and how they work to ensure better industrial outcomes. The study found that it is crucial to understand the primary performance dynamics of exoskeletons to ensure they are effectively utilized in their specific application areas.
One of the primary applications of exoskeletons is supporting the upper and lower backs during industrial loading weights. A study by Zhang and Huang on the lower-back robotic exoskeletons revealed crucial information regarding how the systems play vital roles in the managing of industrial applications and maintenance of the health of the workers (31). The authors indicated that using such robotics help in reducing possible injuries to the spinal cord by protecting the worker who lifts heavy loads in the factory. The study was informed by past research on biomechanics that revealed crucial information regarding the compression of the lumber spine and its risk factors for musculoskeletal harm.
A wearable exoskeleton helps provide back support to limit lumbar spine compression. Even though industrial processes have led to more mechanization, artificial intelligence has not reached the level of human intelligence, which makes humans the primary factor in production. Some industrial works require human interventions, but due to the body’s limits, such people cannot do specific tasks, requiring assistive technologies (31). Thus, the research explored techniques necessary to help avoid muscle or tendons injuries and, at the same time, offer practical assistance to the workers.
Robotic exoskeletons mainly involve a series of elements, including sensors, actuators, programs, movable structures, and control systems that acquire information and use them to execute motor functions. The combination of these elements into a complete design makes it possible for the exoskeletons to interact with humans and the target devices seamlessly. The interaction achieved by the system can be categorized as physical human-robot interaction (pHRI) and cognitive human-robot interaction (cHRI) (22). cHRI mainly deals with how a human executes various functions that control what the exoskeleton does at any point according to the person’s desires. On the other hand, pHRI involves putting various forces that shift between the exoskeleton and humans. The user and exoskeleton interaction comprises sensing, deciding, and executing commands (30). Thus, developing a fully responsive system requires that each part of the robot can effectively respond to the slightest force applied by the user in the direction desired by the user.
The development of exoskeletons requires developers to have all the technologies that ensure that every module of the robot is made as needed. The sensing module is one of the crucial elements because it is the part of the robotics that is supposed to collect the information from the users’ environment. The sensing element must be made with all the precautions necessary to ensure that it can always only respond to the set forces so that it can ignore all the false inputs (3). Achieving this type of accuracy requires a deep system analysis and one that can simulate the natural environment, including mimicking the expected movements. Thus, such information inputted into the sensing element can come from the human user or sometimes from a device meant to create the movement.
The decision module is also a crucial part of the robotic system as it involves a series of processes that connect the input and the output. In most cases, the information comes from the users, while the production is directed to the devices or working area. For this to happen, the system needs should compare the input signal with the minimum or maximum reference values and take actions depending on each value received at any point (5). For instance, a sensor can be set such that it only responds to 50 Newton forces applied to it, which means that the user is actually in the process of achieving a given target per the industrial work. Therefore, the decision module of the exoskeleton interprets the information sensed and organized into the robot such that its output becomes helpful in the intended outcome.
The execution module is the last part of the system, which receives all the commands based on the decision module’s output. For instance, the execution module can get information requiring it to lift a given force, which is critical to completing the actual task intended by the user. It is the part fully responsible for actuating or providing the system with mechanical power (36). The part also ensures that the whole can achieve its intended function since the system becomes unnecessary without delivering the needed mechanical power. For this reason, different types of exoskeletons are designed and implemented for various tasks that ensure specific functionalities requiring varied forces are achieved.
A study by Whitefield et al. focused on the personal augmentative lifting device (PLAD) that helps lift by utilizing power supplied by elastic straps worn on the upper side of the body. The researchers aimed to determine if the PLAD affected the user’s oxygen consumption when performing non-stop lifting tasks. They investigated if the impact could be due to variation in the activity of the muscles or the technique of lifting. The PLAD is worn like a backpack and assists the back muscles during tasks involving lowering, forwarding and bending. The researchers did not observe any differences in the consumption during no-PLAD and PLAD conditions. The thoracic erector spinae (TES) showed an 8.4% reduction in EMG as the participants lowered the load. In comparison, the biceps femoris showed a 14% reduction in EMF as the participants lifted the load (7).
The researchers concluded that the PLAD did not affect the consumption of oxygen; hence, neither employees nor employers ought to increase the demands of the tasks while wearing it (7). This finding is significant and relevant to the industry, and it should be taken into consideration. Industry players should note that even though the device reduces the back musculature’s musculoskeletal effort, it is not advisable to reduce either the loads or the rates of lifting. Wearing the device does not cause any change in the task’s overall physical demand.
Davenport et al. investigated the supernumerary robotic limbs (SRL) used in stating holding, utilizing active electric motor and viscoelastic elements placed in the upper body (8). The SRL is a wearable robot providing a third and a fourth arm to perform manipulative tasks using the wearer’s arm. At times, humans can perceive that the SRLs are their arms because of the close work relationship they have with them. An SRL consists of two robotic limbs acting independently, functioning either as an arm or a leg for the user to maintain balance, position objects or lift weights. They augment the precision, strength of the users and their skills as they interact with their environments. According to the researchers, the robotic design adheres to the principles of transparency, comfort and user safety.
In SRL’s suitable joint, torques emanate from the series of viscoelastic actuators, ensuring robust torque sensing and compliance. The elbow joint is actuated by a Bowden cable transmission, an action that minimizes the weight of the robotic arm. Also, in the SRL, wear-ability and comfort are enhanced by a tuned elastic human-robot coupling.
Kim et al. studied the quasi-active exoskeleton used for carrying, requiring an active power supply and used in the lower body. The system is made up of two active joints and four quasi-active joints, three passive joints and one active joint (33). The researchers’ verified the quasi-active exoskeleton’s efficiency by comparing the muscle activation results taken before and after a user wore the exoskeleton. The researchers concluded that the exoskeleton does not have a full active degree of freedom (DOF) but one that is partially active, also known as the quasi-active joint system.
All the exoskeletons in these reviews were anthropomorphic, meaning that they bore semblance with the human body, having many different actuated joints. The significant advantage of this exoskeleton is that it is small since it adheres to the body, and theoretically, its movements are unrestricted. Essentially, the exoskeleton copies the worker’s movements, meaning that the exoskeleton and the human limbs are aligned during motion. It is, therefore, necessary to detect human movement intention for the exoskeleton’s actuators to initiate suitable responses. It is not always easy to distinguish intended movements from unintended ones, increasing complexity in a multisensory system (3). Even though the necessity to improve control strategies has been suggested to smoothen motion at a considerably fast pace, the control strategy still faces hurdles like real-time safety and motion control, function and cooperation allocation and device-man information exchange.
It is still challenging for active anthropomorphic robots to align with human kinetics, kinematics and anatomy to enable natural and comfortable movements. One of the complex anatomies of the human being is the shoulder, which requires the incorporation of exoskeletons since it has a transversal centre of rotation and three orthogonal axes. The knee also brings a challenge since its centre of rotation habit shifts when it flexes. Also, for a rotational movement to occur in any joint there must be some movement between the skeletal structure and the skin. For that reason, the exoskeleton should be ideally designed to make it either short or extended, a design that was missing in the devices reviewed.
For one to use passive and active exoskeletons in an industrial environment, one must meet specific safety criteria. As the reviewed literature has revealed, many design issues compromise the safe use of the exoskeletons. There are many occupational risks for a worker who wears an exoskeleton in a workplace environment, including warehouses, construction sites, the floors of an industrial complex, or outdoors on the farm picking fruits or vegetables. Even though ISO 13482 governs the exoskeletons used as robots for personal care, no similar standard has been granted for the industrial use of exoskeletons, which is a massive barrier to the adoption of the devices.
Another safety concern that has been raised regarding lumbar orthoses is close-fitting lumbar supports. Extensive uses of the device have been associated with trunk muscles’ deconditioning. It is, therefore, recommended that the users either reduce the use time or use it but adopt strengthening exercises. This limitation is also apparent in the exoskeletons used on the industrial scale, making their adoption difficult.
In conclusion, this literature review has shown interest in active and passive exoskeletons for industrial use (2, 3, 14, 13, 26, 27, 37, 34, 35, 24, 33). However, the developments are still early, with most concepts texted only in the laboratory setup. Most of the cumbrances have to do with safety and certification, preventing the adoption of industrial exoskeletons for industrial use. Once the technical issues are looked into and tackled, it will be possible to undertake the large-scale implementation of the technology. Until such a time when all these issues shall have been tasked, people will have to wait upon the thought of implementing the use of exoskeletons in industrial setups.
Structural Analysis of 5 Leading Industrial Exoskeletons
Section I highlighted literature on the current exoskeletons technology and the challenges faced in the industrial application of robotics. One way of addressing the challenges is to carry out an in-depth analysis of the present technology and define the design and development indicators which are essential for its technological aspects like actuation, structure, and control and sensing. In this section, the author will analyze the exoskeleton structure of the five leading exoskeletons. The findings will be vital in future work on sensing, actuation and control of exoskeletons. The author will begin by presenting a structural analysis of Skelex, Paexo, Levitae, Mate, and ShoulderX, in the category of five-arm support industrial exoskeletons. Next, the author will propose and apply a structural complexity indicator. Lastly, the author will compare the complexity indicators with established experiments on how the mass and design of an exoskeleton affect its use.
Essentially, this section will study five major industrial arm-support exoskeletons using kinematic analysis, mainly focusing on the robots’ parallel mechanisms. Fig. 1 presents a photo, a connectivity diagram and a kinematic diagram for each exoskeleton. Future developers can benchmark this approach by designing the next generation of exoskeleton robots, using new indicators to appraise the different kinematics. The first and second columns in Fig. 1 represent each device’s actual devices and the kinematic structure, respectively. One can only observe some technical aspects after dismantling the exoskeleton. However, the author’s structural accuracy description could also be impacted by design approximation.
The devices have an orthonormal basis orientation which is based on the user’s body. The front left and vertical directions are Z₀, X₀, Y₀. Assuming that the device is a mechanism F which has several limbs Gi connected in a parallel orientation to a supporting part. In this case, each device’s limbs become a serial kinematic chain, assigned a letter. The kinematic chain Gi will have an operational velocity RGi as shown on the Tab. 1, below. We assign each link a unique number, with the limb letter as its index (for example, 2A). We assume that link 1 is ground 0, representing the human body on which the efforts are distributed. From Fig. 1, we can see the end-effectors that assist with the user’s limbs: 5a-b, 4a-b, 7a-b. In this scenario, the fasteners and straps are not represented. The exoskeleton has flexible parts that keep it close to the operator’s body and maintain its correct position. The red dashed lines represent the flexible parts, including the springs, which help generate effort.
The third column contains the connectivity graphs of the five devices, all designed to support the arms of a user engaging in an overhead task. The back structure distributes the effort to the waist, while a kinematic chain supports each arm. The torque generation coaxial to the user’s arm elevation produces the effort. In Skel’Ex, shown in Fig. 1a, the arms are supported through 5a-b, as shown in Fig. 1b. Parts: 1a-b generates a torque with respect to parts 3a-b, as the leaf springs S1a-b, flex upon the shoulders. The leaf springs are also part of 1a-b structurally.
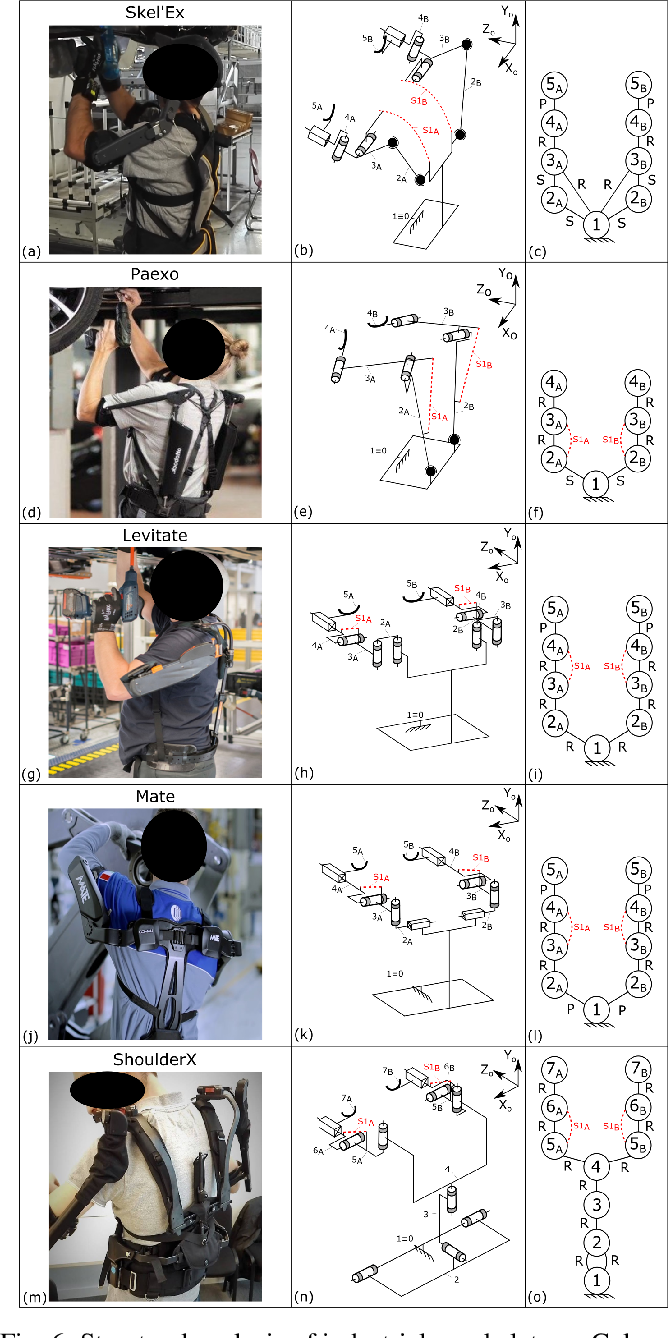
Paexo (Fig. 1d) assists the user’s arms through parts 4a-b, shown in Fig. 1e. The spring and lever mechanism S1a-b generates the effort between 2a-b and 3a-b. The Airframe, shown in Fig. 1g, assists the user’s arm through parts 5a-b, as shown in Fig. 1h. Parts 3a-b use a spring mechanism S1a-b to generate the torque for parts 4a-b. For Mate in Fig. 1i, assists the arms through parts 5a-b as shown in Fig. 2i. Parts 3a-b generate the torque through a spring mechanism S1a-b, for parts 4a-b. Shoulder X, shown in fig. 6n utilizes parts 7a-b to support the arms. There are several mobilities at the Shoulder X’s back part, between the shoulders and the waist. Parts 5a-b generate the torque through a spring mechanism S1a-b for parts 6a-b. While this category of exoskeletons is meant for use in similar cases, each is uniquely designed. Except for Paexo and Airframe, the other designs do not provide mobility for the shoulders’ centre of rotation.
The author, as a result of this, suggests a complexity indicator to help with the exoskeleton selection by utilizing the different parameters in Tab. I. One of the selection criteria is the exoskeleton’s versatility, which refers to the number of categories a particular device can use. The following indicator will be used to obtain the complexity indicator:
C= p.a.Nb equation 1.
C is the complexity indicator, p is the sum of the joints observed on the structure, and a represents the total sum of the actuation mechanism generating efforts[6]. At the same time, Nb is the sum of the user’s limbs involved in the mechanisms like legs, arms, trunk and hands. The numerical complexity value for the exoskeletons is computed as shown in Table 1. Paexo has the lowest complexity number, 36, while Shoulder X and Skel’Ex have the highest complexity indicator value, 60. Airframe and Mate had a complexity value of 48.
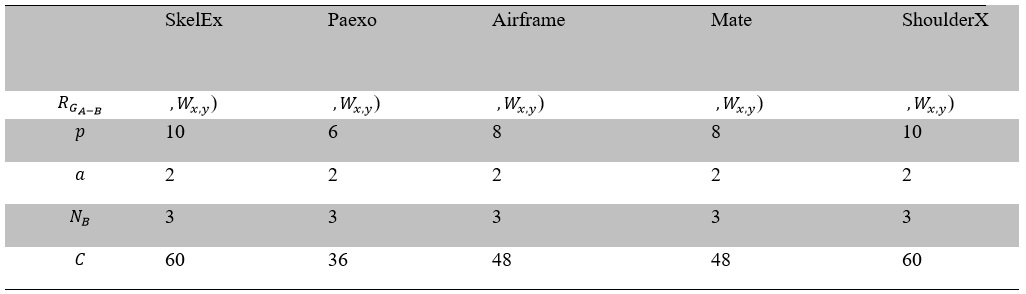
Here, RGa-b = RGa = RGb; V is the translation vector, and W is the rotation vector.
The complexity indicator has critical links in the evaluation of the structural technology of the exoskeletons. They hold the key to improving the confidence and acceptability of the existing exoskeleton technology. Looking at the table, it is clear that Paexo has the lowest complexity indicator value, followed by Mate and Airframe, and then shoulder Ex and Skel’Ex. There are two design consequences for these results. Firstly, complex systems can offer an improved motion and support range for the user to perform various sub-tasks. This design improvement is satisfactory for the exoskeletons whose weight transfers to the ground. However, for those exoskeletons that do not transfer their weight to the ground, the high complexity indicator can increase the system’s mass, making them a nightmare.
Another consequence of the complexity is that it raises the metabolic impact and reduces a device’s usability. The more complex a mechanism is, the more support it requires to connect with the user’s body, which increases the don-dof time and creates a heat sensation, pressure points and entanglements on the body. The devices with high complexity indicators are more expensive than those with low complexities. Designing, developing and assembling complex parts for building a highly sophisticated mechanism is more costly than dealing with a primary mechanism.
However, the complexity indicator cannot be adequate to make conclusions regarding the efficiency and usability of an exoskeleton. The other criteria include the usability, mass, versatility, and kinematic compatibility of the user’s limbs. Nevertheless, the complexity indicator is an essential factor that can be used to choose an industrial exoskeleton before the physical tests are carried out.
In one study, the researchers compared Poexo with Skelex, Shoulder X, Mate, and Airframe to determine how their masses and designs affect the users. Even though all these structures reduce the physical strain on the shoulder, their numeral values vary (see table 2) (12). Apart from Poexo, they cause problems like a low back strain, inhibit postural controls, and hinder freedom of movement and usability (12). These differences were attributed to the design styles.
The primary factor pointed out to be giving Poexo an edge was its lightweight, compared to the other four exoskeletons, which limit overloading. However, there are heavier exoskeletons with more tradeoff options; for example, Mate has a system that modifies its support with a button, while one requires tools to adjust the Paexo’s (12). Another advantage of Paexo is its structure’s flexibility; it has no rigid back elements enabling it to have a full range of back and upper limb motions. In one study, the participants reported that Paexo did not limit their movements, though the experiment did not measure the motion’s range. In the survey, more than half of the participants found Mate to be too cumbersome to use, emphasizing how the weight of the device can limit its usability. It also stresses that a structure which is light and flexible like Paexo’s is a crucial consideration in developing industrial exoskeletons
Another quality of Paexo is that it does not generate an upward torque when the user lowers the body, unlike the others like Airframe, which produces immense upward torque. For this reason, it is possible to work with Paexo in a comfortable posture whenever the user is not working overhead, without the user’s shoulder muscles. From this discussion, it is clear that Poexo has a great combination of complexity indicator, mass, and usability among these five exoskeletons. More industries are continuously using the exoskeletons in their operations in response to the rapid growth in technology and competition. The exoskeleton market is rising to meet these needs crucial in the industrial flexibility and protection of workers from harm.
It is vital to assess the cases in which such systems are used in actual cases to understand how these technologies are crucial to industrial performance. Some main areas where exoskeletons are used include car assembly firms, railway maintenance, repair, and operations (MRO), logistics, aviation MRO, and electronics assembly (10). All these cases have specific robotic structures that ensure the worker can handle the needed loads, reach the desired heights, or access some hidden areas within the work environment.
Paexo is a passive exoskeleton for the upper limb, designed to maximize a user’s comfort and freedom of movement while offering sufficient support. It is made up of a stabilization structure that is attached to the user. It also has a support structure that transfers some part of the arm’s weight to the hip belt from the bracelets of the upper arm, as shown in the figure below.
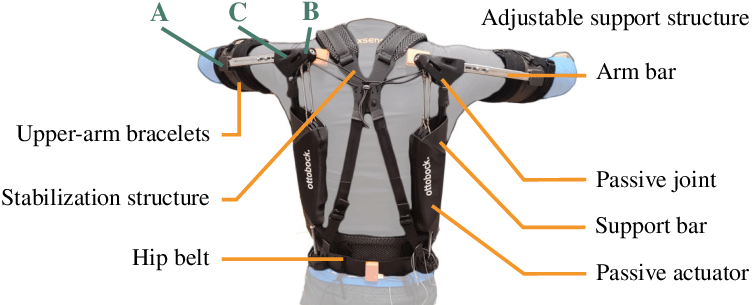
It supports the arms of the user by transferring some of the arm’s weight to the pelvis via a hip belt. Its assistive structure comprises an arm bar and a support bar connected through a hinge joint. The support torque in the hinge joint is generated by a passive actuator based on a spring. A bracelet connects the arm bar to the upper arm through a passive hinge joint from point A to the cable at point B’s end. It connects it to point C, which is the support between point A and point B. In this way, the spring can apply a downward force at point B, generating an upward support torque at point C, a passive joint. The lever arm BC determines the amount of torque generated by the spring; the length is adjustable. Furthermore, the assistive structure connects with the high through a hip belt passing through a ball joint. Since the entire system can be adjusted, including the hip belt width and the support bar length, it can fit diverse body sizes.
A stabilization structure of straps tied to the hip belt keeps the body and the support structure close, allowing it to move comparable to the user’s shoulder blade. Also, the straps enable the wearer to put on the exoskeleton the way people strap backpacks on their bodies. Paexo was designed to produce a supporting torque that is proportional to the elevation angle of the arm, which is similar to the torque that people typically experience when gravity acts on their arms. The maximum provided torque is therefore achieved at ninety degrees elevation when the upper arm lies horizontally and is zero when the user lowers the arm along the body. Also, it is possible for one to continuously tune the level of support by manipulating the lever arm length BC when they want to adapt to compensate for extra weight or to adjust to different weights.
Paexo is one of the leading exoskeletons used in various industries to help achieve specific tasks. It is used in automobile assembly to help reduce shoulder and upper back efforts and is mainly leveraged in two postures (12). For instance, it is useful when a worker is seeking to reach a static overhead area, such as when installing underbody elements and components of the vehicle in the manufacturing process, since the workers are required to stand to reach such points within the work area. However, when working in non-static areas on overhead points with their waist height postures, such as the rear tailgate assembly processes required when installing wiring, grommets, and fasteners.
The Airframe’s base is fixed on the human waist. It has five joints, two prismatic and three revolute joints. The first joint is for vertical adjustment, the second is for horizontal adjustment, the third is for rotational adjustment, the fourth one is a free external/internal rotation joint, and the fifth is the elevation joint. The three adjustment joints ensure the exoskeleton’s elevation joint centre is coincident with or adjacent to the centre of the shoulder joint. The Airframe’s cushion connects with the upper arm segment with five degrees freedom constraint comprising two torques and three forces (4). Put another way, Airframe’s last body joint is attached to the upper arm of the human by one degree of freedom revolute joint whose axis aligns with the direction of the shoulder supination.
Generally, the Airframe’s passive mechanism depends on human strength and kinetic energy to store energy in the spring. In other words, the Airframe’s spring mechanism utilizes gravitational torque or human power to store energy by increasing the spring’s length. The passive Airframe is designed for the specific motion path and external torque profile. However, it is possible to change its dynamics by manipulating the different motions or mass. However, when such adjustments are made, the Airframe becomes unstable. That means that the use of passive Airframe is restricted by flexibility and the tasks it may be required to perform. It, therefore, does not possess a versatile torque profile and cannot be optimized to perform different tasks.
The Mate exoskeleton is made up of three major modules: the trunk, the passive parallelogram arm, and the active parallelogram arm. Depending on the task at hand, any of these modules can be selected. The trunk module, for instance, when used, allows the user to conveniently lift low weights. The passive arms are designed for constant load and body compensation, which is a situation where the load stays in the user’s hand as long as possible. On the other hand, the active arm is the most appropriate when it comes to picking and placing tasks since it is possible to continuously adjust the lifting support. When the user is bending over, the trunk module helps in reducing the lower back forces of compression (6). When it comes to activities where the user does not need to bend over, they can use a simple backpack with mounting arms. Presently, the Mate designs focus on potential load reduction and increased functionality since, at the moment, one requires a trunk and active arms on an exoskeleton of around twenty-one kilograms to lift fifteen kilograms.
Shoulder X is a shoulder-supported exoskeleton that has undergone a lot of structural adjustments. However, one of its main structural challenges in the experimental set-ups is that it reduces the functioning of the shoulder. In one study involving EMG measurements to gauge the user’s participation, the researchers found that the exoskeleton reduced the activity of the user’s shoulder flexor muscle by upwards of 80%. At the same time, the usability was moderate (1). Therefore, to make Shoulder X effective, its efficacy should be considered alongside practical analysis.
In one experiment comparing the functionality of Shoulder X and Skelex, the researchers found that there was reduced TR muscle activity on the latter. Still, those results were not noticeable when it came to in-field work. The beneficial infield effects were more apparent when wearing Skelex, while Shoulder X offered better assistance during the isolated tasks. Even though there was a reduction in muscle activity and heart rate after wearing either of the exoskeletons, there was no change in RPE. Such could be due to limited usability, discomfort and frustration due to the usage of the exoskeletons (25). All these differences come about due to the differences in the structures of the two exoskeletons.
Practical Implementation of Exoskeletons
Exoskeletons can perform assistive tasks requiring repetitions and strenuous posture, hence reducing musculoskeletal disorders and increasing productivity in industrial settings. They are continuously implemented in the workplace where other techniques such as technology and workplace modifications cannot be used. The principle of their application is similar to that of weights operation in a beam balance where mass closer to the pivot point requires additional compensation on the other side. For example, when lifting load, the muscle proximity in humans to the rotational axis exerts a significantly higher load on the spine than the actual load itself. Despite the additional mass to the wearer, an exoskeleton used during lifting moves the centre of load on the upper body closer to the pivot, which reduces the compression forces on the lower back (9). A lack of standardization makes applying exoskeletons in industrial use difficult (12). However, evidence from previous studies can help decision-makers assess how to deploy the technology and optimize its use.
Exoskeletons can help perform tasks in specific workplaces characterized by manual handling, hazards, poor posture, and physical effort. The combination of human intelligence and resistant exoskeletons is gaining ground in the manufacturing sector, and implementation teams should ensure a correct implementation for positive integration and optimal benefits (10). The factors considered when selecting exoskeletons for industrial use include the nature of the project, workplace, ergonomics, and organizational environmental factors (8). These factors can also be examined from a physical and psychological point of view to optimize the use of exoskeletons (19). Increased exoskeleton adoption will occur when there is sufficient evidence of efficacy (24). The practical implementation of exoskeletons from the physical and psychological perspective will provide insights into ensuring the effectiveness of available devices.
Physical Aspects Affecting the Implementation of Exoskeletons
Many working populations have been diagnosed with work-related musculoskeletal disorders (WMSDs) and a third of the injuries affect the lower back. The main goal of an exoskeleton in industrial settings is to reduce the user’s muscular effort, endurance, and discomfort by generating physical power to perform a manual task. It is instrumental where automation and other work injury preventive measures are not feasible, such as constantly changing tasks (29).
Bosch et al. examined the physical aspects of exoskeleton use in a simulated assembly (29). The researchers measured the perceived discomfort and the electromyography for the back, abdominal, and leg muscles. The researchers also assessed endurance time when using an exoskeleton. Bosch et al.’s study showed that exoskeleton use reduced muscular activity by between 35% and 38% and lowered rates of discomfort in an assembly task (18). However, there was increased discomfort in the chest region. Using the exoskeleton in the static holding activity also tripled the average endurance time, increasing from 3.2 minutes to 9.7 minutes. It shows that the exoskeleton contributes positively to the physical aspects of a task. However, kinematic compliance is essential to ensure that the device’s mechanics do not impede natural human motion.
According to Cenciarini and Dollar, the physical requirements of the exoskeleton design should offer compatibility with the human body. The mechanics of joints and segments and gait changes variation in different people during task execution require a focus on the kinematics to allow for unconstrained and beneficial task support (17). Cenciarini and Dollar’s study focused on the physical considerations of the exoskeleton concerning the lower limbs (17). The five primary physical considerations are the degrees of freedom, range of motion, joint torque, motion velocity, and design compatible with human movement. The hip joint has three rotational degrees of freedom that allows for internal/external rotations, flexion and extension, and adduction and abduction. The exoskeleton should also account for knee joints’ internal/external rotations and flexion/extension. The ankle joint is more complex and allows only flexion and extension since it is a hinge joint. Its connection to the ground implies that the exoskeleton’s design should account for inversion, aversion, and external or internal rotation (19). These physical factors should be considered in an exoskeleton’s physical design to ensure that the device does not restrict movement or add unnecessary load, which is counterproductive.
The second physical consideration when implementing an exoskeleton is the range of motion. According to Cenciarini and Dollar, this varies with the purpose and individual’s safety margin (17). For example, an assistive exoskeleton for the average military male will have less than the minimum range of motion for the joints compared to one for regular walking. Therefore, a task’s desired range of motion and individual characteristics will inform the physical design for optimum use. Thirdly, the exoskeleton should provide the user with assistance during movement. Active or passive torque will be applied in the right direction, to the correct joint, at the appropriate time, and with the right intensity to attain the movement (16).
Gait cycles have varying joint torque. The ideal exoskeleton should account for the maximum value when sizing the actuator to allow for variability across different tasks and individuals. Gait is highly dynamic since the velocity and frequency of bandwidth movements vary. On the downside, exoskeleton actuators have dynamic behaviour that does not match the speed and frequency of humans (17). Practical assistive exoskeletons should generate the required torque intensity with speed and frequency. The four considerations are not exhaustive. According to Cenciarini and Dollar, one should also consider anthropomorphic abilities, the exoskeleton’s weight, inertia, and user interface. The design considerations are helpful for an exoskeleton’s mechanics to ensure its effectiveness in the industrial setting.
Psychological Aspects Affecting the Implementation of Exoskeletons
A holistic approach to exoskeleton implementation requires a focus on biomechanical aspects and psychological factors. The psychological factors contribute to the workers’ experience and the device’s effectiveness. Maurice et al. examined the acceptance levels when using an exoskeleton compared to those who did not. The mean user acceptance rate on a scale of 0-10, where 0=no acceptance and 10=full acceptance, was 7.76, with a standard deviation of 1.79 (20). The acceptability metrics were lower physical fatigue, unrestrained movement, ease of use within the first few movements, comfort, and willingness to reuse it in a similar task (20). This implies that designers should test their prototypes for acceptability and then modify the biomechanical aspects to maximize their effectiveness and adoption rates.
Baltrusch et al. also examined the psychological aspects of exoskeleton implementation and established that it is essential to address implementation barriers to improve acceptability rates. First, the final design should address the user’s requirements and needs (20). It implies that it should be fit for purpose and reduce muscular effort, task endurance, and discomfort. The aesthetic factors such as comfortable wear, versatility to different body sizes, comfort, personal taste, and social invisibility where one would not notice the device are essential for increasing acceptability. Focusing on the potential challenges like non-acceptance and aesthetic considerations, can improve the acceptability levels since the users’ psychological concerns will be factored in the design process.
Pros and Cons of Industrial Exoskeletons
Occupational Health
Occupational health concerns itself with minimizing fatigue and injury during work. Different stakeholders in the labour market are interested in worker safety. For example, workers desire fewer accidents and injuries, convenience in operations, higher performance, and lower fatigue. Similarly, the workers’ unions advocate for their interests and regulate employers’ practices. Policymakers also enforce workplace health and safety (24). According to Crea et al., the technology is at an early adoption stage, and occupational health concerns are not adequately identified. De Looze stated that exoskeletons reduce muscle activity by up to 80%, reducing musculoskeletal injury significantly. Over 30% of the work populations in the EU are exposed to repetitive movements and poor body postures (18). Over 40% of the workforce experience lower back, neck, and shoulder pain (18).
Kaupe et al. also reported that approximately 45 million people in European countries had been diagnosed with musculoskeletal disorders due to work (32). The financial costs exceed 10 billion Euros and a 4% GNP loss every year (23). While full automation might be impossible, external assistive devices can leverage one’s power and actuate the joints. Human flexibility and creativity will also lead to better task performance and creativity. It also reduces load handling and the prevalence of musculoskeletal injuries.
According to Kaupe et al., previous literature supports the use of exoskeletons in production processes to address operational issues like efficiency, work ergonomics, occupational safety, productivity, and inclusive workspaces that integrate the elderly and people living with disabilities (32). In the logistics sector, where physical labour is inevitable, workers experience back pain due to repetitive lifting and poor posture. Exoskeletons can reduce support workers performing the processes, enhance their strength, improve their endurance and work capacity and reduce pain. The devices can reduce occupational injuries from repetitive strain and the financial consequences (32). Exoskeletons are essential for addressing occupational health concerns and can significantly enhance safety and minimize harm and damage. However, Kaupe et al. acknowledged that the data on the negative impacts are scarce, and new measurement methodologies should be adopted to objectively assess exoskeletons’ influence.
The device can also cause health risks. Exoskeletons can add to the worker’s weight burden since they will have an additional load that should be adapted to human motion. The adaptations can create design challenges requiring alterations, creating further complexity and weight burden (24). There is a need to engage stakeholders to identify its risks and benefits for informed choices. Previous research indicates that the exoskeletons can contribute to weaker back muscles. Extended use of orthotics can weaken one’s musculature since muscles remain active to a lesser degree. It can be addressed by performing muscle-strengthening exercises.
Moreover, the exoskeletons should be used for a limited period and in specific tasks. The manufacturers should also adapt the devices to ensure comfort since discomfort can limit acceptability (29). While exoskeletons can reduce occupational health hazards, it also poses health risks. Therefore the manufacturers should consider the dangers and adapt the exoskeletons to optimize the benefits.
Effect of Industrial Exoskeletons on Muscle Activity
Exoskeletons in the working environment have their benefits and drawbacks. The invention decreased mechanical loading to minimize effort and injury while enhancing productivity (23). Previous research shows that the benefits of using exoskeletons in the work environment outweigh the drawbacks. Bosch et al.’s study showed that it reduces muscle activity and discomfort. Previous research demonstrates that the positive effect on muscle activity ranged from 21-31%. Bosch et al.’s analysis compares with this finding but established higher level of reductions. Specifically, the back muscle activity was reduced by 35-38%, the erector spinae activity declined by 37%, and the thoracic and lumbar activities decreased by 14% (29).
There was no effect of using the exoskeleton on abdominal muscle activation. On the downside, the exoskeleton reduced the leg extensor activity. However, a lack of confirmation by Bosch et al. attributed the scenario to the positioning of the exoskeleton. The front side attachment implied a backward translation of force that kept the knees in an overstretched position, and the Biceps Femoris was activated to prevent this. This can be advantageous when performing forward bending, but the health risks are unknown (18). Therefore, it is essential to identify all threats to ensure that users experience no harm.
Discomfort
According to Bosch et al., people using exoskeletons reported lower discomfort levels than those working without them. However, the manufacturer’s design contributes to comfort levels significantly (29). It implies that manufacturers should consider the biomechanical factors and aesthetics of the device. The factors include such as ease of wear, versatility to different body sizes, personal taste, and social invisibility (29). Bosch et al. reported that chest discomfort escalated during assembly work (29). It can be attributed to the contact point between the chest area and exoskeleton chest pads. The straps also had additional pressure and friction on the armpits. The exoskeleton also led to more significant endurance static holding tasks. The participants were able to work for longer without discomfort or unpleasant feelings that can cause distractions and accidents. It shows that exoskeletons reduce discomfort, and manufacturers should pay attention to the comfort attributes of the device.
Regulatory Concerns
Regulation is essential for a soundly functioning business environment, law and order. Robotic devices such as exoskeletons are becoming part of people’s private and professional lives. It creates legal and ethical dilemmas, especially regarding autonomy, privacy, and liability. The risks and rapid pace of advances in automation require changes in legal frameworks that take time. It is often claimed that the regulator intervenes too early or too late (21). It can stifle innovation or cause regulatory gaps. Creating a distinction between humans and things also creates data protection and autonomy challenges. One should be free to exercise their free will devoid of unnecessary limitations. The health risks of the novelties such as exoskeletons have not been exhaustively examined. It creates a challenge when protecting individual rights without infringing on their autonomy (21). The challenge can be overcome by balancing laws and social norms since legislation alone cannot address the challenges of robotics.
References and Notes
A. Golabchi, A. Chao and M. Tavakoli, “A Systematic Review of Industrial Exoskeletons for Injury Prevention: Efficacy Evaluation Metrics, Target Tasks, and Supported Body Postures”, Sensors, vol. 22, no. 7, p. 2714, 2022.
A. Ebrahimi, Stuttgart Exo-Jacket: an Exoskeleton for Industrial Upper Body Applications. Stuttgart: Fraunhofer Institute for Manufacturing Engineering and Automation IPA, 2017, pp. 1-6.
A. Kian, G. Widanapathirana, A. Joseph, D. Lai, and R. Begg, “Application of wearable sensors in actuation and control of powered ankle exoskeletons: A Comprehensive Review”, Sensors, vol. 22, no. 6, p. 2244, 2022.
A. Nasr, S. Ferguson and J. McPhee, “Model-Based Design and Optimization of Passive Shoulder Exoskeletons”, 2022.
A. Trifonov, A. Kuzmin, S. Finalist, S. Degtyarev and E. Petrunina, “Biotechnical System for Control to the Exoskeleton Limb Based on Surface Myosignals for Rehabilitation Complexes”, 2020 IEEE 14th International Conference on Application of Information and Communication Technologies (AICT), 2020.
A. Voilque, J. Masood, J. Fauroux, L. Sabourin and O. Guest, “Industrial Exoskeleton Technology: Classification, Structural Analysis, and Structural Complexity Indicator”, 2019 Wearable Robotics Association Conference (WearRAcon), 2019.
B. Whitfield, P. Costigan, J. Stevenson, and C. Smallman, “Effect of an On-body Ergonomic Aid on Oxygen Consumption during a Repetitive Lifting Task.”International Journal of Industrial Ergonomics vol. 44, no. 1, p.39–44, 2014.
C. Dahmen and C. Constantinescu, “Methodology of Employing Exoskeleton Technology in Manufacturing by Considering Time-Related and Ergonomics Influences”, Applied Sciences, vol. 10, no. 5, p.1591, 2020.
C. Davenport, Parietti, F. and H. Asada, “Design and Biomechanical Analysis of Supernumerary Robotic Limbs.” In ASME 2012 5th Annual Dynamic Systems and Control Conference Joint with the JSME 2012 11th Motion and Vibration Conference, 787–793. Fort Lauderdale, FL: American Society of Mechanical Engineers, 2012.
D. Ippolito, C. Constantinescu and C. Rusu, “Enhancement of human-centered workplace design and optimization with Exoskeleton technology”, Procedia CIRP, vol. 91, p. 243-248, 2020.
H. Ryu, J. Choi, B. Yi, J. Lee, D. Kim, and J. Ko, “Humanrobot Integrated Model of Upper-extremity.” In Ubiquitous Robots and Ambient Intelligence (URAI), 2012 9th International Conference 7–9. Daeyeon: IEEE, 2012.
J. Bornmann, B. Schirrmeister, T. Parth, and J. Gonzalez-Vargas, “Comprehensive development, implementation and evaluation of industrial exoskeletons”, Current Directions in Biomedical Engineering, vol. 6, no. 2, 2020.
J. Masood, J. Ortiz, J. Farnandez, L. Mateos and D. Caldwel, “Mechanical Design and Analysis of Light Weight Hip Joint Parallel Elastic Actuator for Industrial Exoskeleton”, in 6th IEEE RAS/EMBS International Conference on Biomedical Robotics and Biomechatronics (BioRob), U-Town, Singapore, 2016.
J. Naito, G. Obinata, A. Nakayama and K. Hase, “Development of a Wearable Robot for Assisting Carpentry Workers”, International Journal of Advanced Robotic Systems, vol. 4, no. 4, p. 48, 2007.
K. Stadler and D. Scherly, “Exoskeletons in industry: Designs and their potential.” In 8th International Symposium on Automatic Control (AUTSYM 2017), Wismar, Germany, 21-22 September 2017. ZHAW Z¸ rcher Hochschule f¸ r Angewandte Wissenschaften, 2017.
K. Low, X. Liu and H. Yu, “Development of NTU Wearable Exoskeleton System for Assistive Technologies”, in Proceedings of the IEEE International Conference on Mechatronics & Automation, Niagara Falls, Canada, 2005, pp. 1099-1106.
M. Cenciarini and A. Dollar, “Biomechanical considerations in the design of lower limb exoskeletons”, 2011 IEEE International Conference on Rehabilitation Robotics, 2011.
M. de Looze, T. Bosch, F. Krause, K. Stadler and L. O’Sullivan, “Exoskeletons for industrial application and their potential effects on physical work load“, Ergonomics, vol. 59, no. 5, p. 671-681, 2015.
N. Hoffmann, G. Prokop, G. R. Weidner, “Methodologies for evaluating exoskeletons with industrial applications”, Applied Ergonomics, vol. 65, no. 2, p. 276-295, 2021.
P. Maurice et al., “Objective and subjective effects of a passive exoskeleton on overhead work”, IEEE Transactions on Neural Systems and Rehabilitation Engineering, vol. 28, no. 1, p. 152-164, 2019.
R. Leenes, E. Palmerini, B. Koops, A. Bertolini, P. Salvini and F. Lucivero, “Regulatory challenges of robotics: some guidelines for addressing legal and ethical issues”, Law, Innovation and Technology, vol. 9, no. 1, p. 1-44, 2017.
S. Aldini et al., “Effect of Mechanical Resistance on Cognitive Conflict in Physical Human-Robot Collaboration”, 2019 International Conference on Robotics and Automation (ICRA), 2019.
S. Baltrusch, H. Houdijk, J. van Dieën, and Kruif, “Passive Trunk Exoskeleton Acceptability and Effects on Self-efficacy in Employees with Low-Back Pain: A Mixed Method Approach”, Journal of occupational rehabilitation, vol. 31, no. 1, p.129–141, 2021.
S. Crea et al., “Occupational exoskeletons: A roadmap toward large-scale adoption. Methodology and challenges of bringing exoskeletons to workplaces”, Cambridge University Press, vol. 2, 2021.
S. De Bock et al., “Passive Shoulder Exoskeletons: More Effective in the Lab than in the Field?”IEEE Transactions on Neural Systems and Rehabilitation Engineering, Vol. 29, p. 173-183, 2022.
S. Kawale and M. Sreekumar, “Design of a Wearable Lower Body Exoskeleton Mechanism for Shipbuilding Industry”, Procedia Computer Science, vol. 133, p. 1021-1028, 2018. Web.
S. Toyama, and G. Yamamoto, “Wearable Agrirobot”, Journal of Vibro-Engineering, vol. 12 no. 3, p. 287–291. 2007.
S. Toyama and J. Yonetake, “Development of the Ultrasonic Motor-Powered Assisted Suit System”, 2007 IEEE/ICME International Conference on Complex Medical Engineering, 2007.
T. Bosch, J. van Eck, K. Knitel, and de Looze, “The effects of a passive exoskeleton on muscle activity, discomfort and endurance time in forward bending work”, Applied Ergonomics, vol. 54, p. 212-217, 2016.
T. Xue, W. Wang, J. Ma, W. Liu, Z. Pan, and M. Han, “Progress and prospects of multimodal fusion methods in physical human–robot interaction: A review”, IEEE Sensors Journal, vol. 20, no. 18, p. 10355-10370, 2020.
T. Zhang and H. Huang, “A Lower-Back Robotic Exoskeleton: Industrial Handling Augmentation Used to Provide Spinal Support”, IEEE Robotics & Automation Magazine, vol. 25, no. 2, p. 95-106, 2018.
V. Kaupe, C. Feldmann, H. Wagner, Exoskeletons: Productivity and ergonomics in logistics: a systematic review. In Hamburg International Conference of Logistics (HICL) 2021, 527-561, 2021.
W. Kim, S. Lee, H. Lee, S. Yu, J. Han, and C. Han, “Development of the Heavy Load Transferring Task Oriented Exoskeleton Adapted by Lower Extremity Using Qausi-active Joints.” In ICCAS-SICE, 2009, 1353–1358. Fukuoka: IEEE, 2009.
X. Ji, D. Wang, P. Li, L. Zheng, J. Sun and X. Wu, “SIAT-WEXv2: A Wearable Exoskeleton for Reducing Lumbar Load during Lifting Tasks”, Complexity, vol. 2020, pp. 1-12, 2020. Web.
Y. Hasegawa and M. Muramatsu, “Wearable lower-limb assistive device for physical load reduction of caregiver on transferring support”,2013 IEEE/ASME International Conference on Advanced Intelligent Mechatronics, 2013.
Y. Long, J. Du, W. Wang, L. He, X. Mao, and W. Dong, “Physical human-robot interaction estimation based control scheme for a hydraulically actuated exoskeleton designed for power amplification”, Frontiers of Information Technology & Electronic Engineering, vol.19, no. 9, 1076-1085, 2018.
Z. Luo and Y. Yu, “Wearable stooping-assist device in reducing risk of low back disorders during stooped work“, 2013 IEEE International Conference on Mechatronics and Automation, 2013.