Abstract
Apple Incorporation has a very successful supply chain management. The company purchases materials and components from a series of suppliers spread across the globe. These raw materials are shipped to a centralized assembly facility in China. The finished products are then transported directly to customers through FedEx and UPS. Apple Incorporation uses its direct and indirect distribution channels to retail other products and services via its primary supply chain partners. When the product life cycle ends, customers are encouraged to return the units to dedicated recycling plants or the nearest Apple store. Despite the successful supply chain management strategy, the company is faced with challenges such as sourcing bottlenecks and decentralized demand planning. Apple Incorporation could eliminate these setbacks through centralized planning for forecasted demand and engaging reliable or flexible suppliers.
Introduction
Apple Incorporation was founded in 1976 by three friends called Steve Wozniak, Ronald Wayne, and Steve Jobs. Over the years, the company has grown into a global brand that has more than 396 retail stores in the US market alone. At present, Apple Incorporation has operations across the globe. This paper explores the supply chain of Apple Incorporation in terms of suppliers, facilities, customers, and supply chain partners. The report also reviews the schematic of Apple Incorporation’s supply chain with the associated flow of goods, capital, and information. In addition, the paper examines supply chain costs, modes of transportation, warehousing, metrics for quantifying costs, service levels, and inventory turnover. The report concludes by recommending improvements in supply chain management for the company.
Supply Chain Management Components
The AMR research report has named Apple Incorporation as a company with the best supply chain practices across the globe for the last three concurrent years, that is, from 2015 to 2017. The high ranking could be attributed to the company’s ability to effectively merge digital and physical supply chain sides.
Supply Chain Planning at Apple Incorporation
The supply chain planning at Apple Incorporation is segmented into research and development, concept testing, pre-launch, launch, and quarterly review. The research and development segment is involved in developing new technologies and acquiring third-party businesses. The concept testing segment is mandated with the roles of conducting continuous market research and identifying actual or potential quality defects in the products manufacturing cycle (Lockamy, 2014). The pre-launch segment manages production ramp decisions and provides relevant software for new products (Long, 2014). The launch segment resolves any existing backlogs in addition to making market demand forecasts for up to five months. Lastly, the quarterly review segment tracks the inventory level from time to time besides adjusting the forecasted demand (Lockamy, 2014).
Suppliers
Apple Incorporation has more than ten main suppliers for its materials and technology. As captured in table 1, these suppliers are Samsung, Infineon, Primax Solutions, Foxconn International, Entry Industrial, Cambordge Silicon, and Unicorn Technology (Lashinsky, 2014). Samsung’s Singapore facility is the main source of video processing chips and CPUs for Apple products. The facility is the primary supplier of CPU fitted in iPhone, iPad, iMac, and other gadgets produced by Apple. Infineon Company’s Singapore production facility supplies the baseband communication hardware for Apple Incorporation. This hardware is manufactured in Singapore and shipped to the production sites in China on behalf of Apple Incorporation by Infineon Company. Based in Taiwan, Primax Electronics is the primary supplier of digital camera modules that are fitted in Apple products.
The Taiwan facility is contacted by Apple Incorporation to manufacture these digital camera modules, which are then shipped to Apple’s assembly sites. Also based in Taiwan, Foxconn International is another supplier of internal circuitry software that is used by Apple in the production of MacBook, iMac, iPad, and iPhone products (Long, 2014). Entery Industrial is contracted by Apple Incorporation to manufacture connectors in its Taiwan facility, which is then shipped to the assembly factories in China. Moreover, Cambridge Silicon manufactures Bluetooth chipsets on behalf of Apple in Taiwan. These chipsets are then supplied to Apple Incorporation in the US and other assembly sites. Unicorn Technology Company supplies printed circuit boards manufactured in its Taiwan facility to Apple Incorporation. Corning facility in Kentucky supplies strengthened glass used in MacBook, iMac, iPad, and iPhone. Some of the strengthened glass is manufactured in Taiwan, China, Korea, and Japan and shipped to Kentucky for assembly (Lashinsky, 2014).
Table 1. Apple Incorporation’s primary suppliers and location. (Source: Lashinsky, 2014).
Facilities
The main production facility for Apple products is based in China as part of the cost-saving strategy in supply chain management. Apple Incorporation has established a giant production complex in China, where the MacBook, iMac, iPad, and iPhone brands are assembled. Specifically, this facility is the central site where any hardware is assembled. Moreover, the site in China is used to hold inventory and handle picking, packing, and shipping steps of Apple Incorporation’s fulfillment process. Specifically, the entire product inventory for Apple Incorporation is done in China to ensure that is a flow between sourcing for raw materials, production processes, and finalization of the new products at any given time. Moreover, isolation of the products such as MacBook, iMac, iPad, and iPhone is also done at this center. This means that packing processes and planning for shipping are accomplished from the same site. Shipping of the final products from this facility in China is coordinated by Apple Incorporation to meet the market demand in different targeted regions (Lashinsky, 2014). The company has managed to invent and produce an intoxicating mix of software interfaces, brilliant industrial design, and consumable products that set the pace in the digital world while maintaining a low cost of production in the China facility.
Customers
Apple Incorporation’s customers are segmented into business and individual clients. The notable business customers are companies in service, software and programming, electric utilities, discount retail, technological retail, and Internet/mail order/online shop industries. These customers are spread across the globe and are dependent on Apple Incorporation products to facilitate their own businesses. The company retails most of its products and sometimes resells other third-party products in the global markets either directly to clients or through its expansive online and retail stores. Apple Incorporation also has an active and robust direct sales force, especially for its local market in the US. In order to reach the business segment customers, the company relies heavily on wholesalers, value-added resellers, retailers, and cellular network carriers, which form part of its indirect distribution channels (Long, 2014). Apple Incorporation’s net sales via its indirect and direct distribution channels account for 70% and 30% of all net sales (Lashinsky, 2014). The individual customers consist of people who value the aesthetics, style, and function of gadgets. These customers view computers as lifestyle tools.
Supply Chain Partners
Apple Incorporation’s leading supply chain partner is Best Buy, which has more than 1,600 retail outlets in Canada, Mexico, and the US. For instance, following the increase in demand for Apple watches in 2013, the rollout of this device expanded from about 100 to more than 1,050 stores (Lashinsky, 2014). Best Buy has also integrated other Apple services such as Apple Care+ and AppleCare packages in addition to other hardware options. The second supply chain partner is Verizon Communications, which is currently the largest cellular network provider in the US. This company offers Apple products through affordable installment plans. At present, Verizon Communications is ranked as a strong retailer of Apple products (Lashinsky, 2014). The third partner by rank is AT&T, which retails Apple Incorporation’s satellite television. Through a strategic alliance, the company has been able to dominate the retail of Apple TV through its offline and online stores. Sprint Corporation is in the fourth position in terms of sales volume for Apple Incorporation products. For instance, Sprint’s iPhone Forever program offers customers an opportunity to lease an iPhone 6s product for as low as $1 per month (Lashinsky, 2014). This strategy enables customers to easily upgrade their phones at the time when Apple launches a better version.
Schematic of Apple Incorporation’s Supply Chain Associated Flows
The schematic of Apple Incorporation’s supply chain integrates the aspects of the product (goods/services), finances (money/cash/capital), and information to complete the associated flows. As captured in Figures 1 and 2, Apple Incorporation uses a vertical integration strategy in sourcing for suppliers, distributors, and retailers. These functions are spread across the supply chain locations and based on a dynamic system.
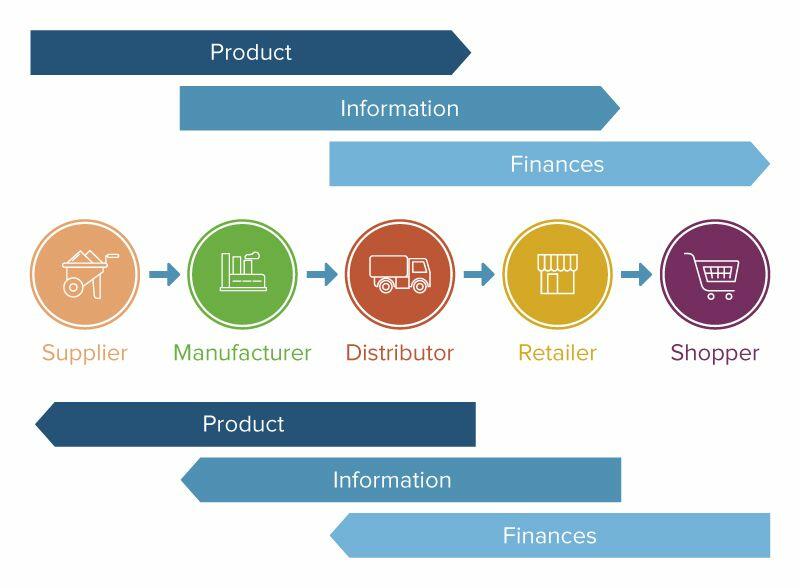
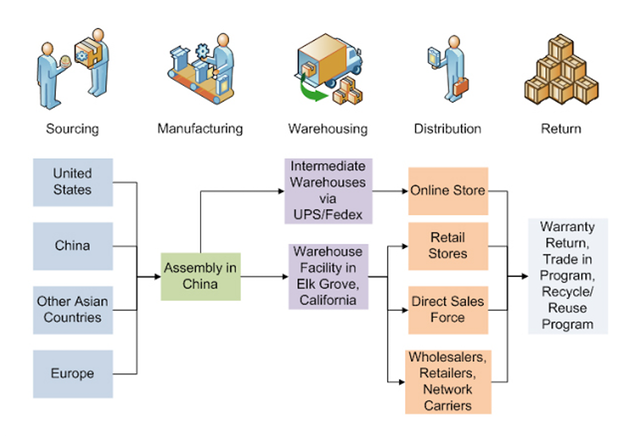
Supply Chain Cost as a Percentage of Sales
In the last five years, Apple Incorporation has managed to consistently reduce the cost of the supply chain as a percentage of sales through its extensive and optimized resource utilization approach. The company has steadily sealed the wastages and inefficiencies in the supply chain through recruiting competitive suppliers and rolling out strategic partnership deals with the supply chain partners. In the year 2011, supply chain cost was 29% of the sales. The value reduced to 26% in 2013 and further climbed downwards to 23% in 2014. The company has forecasted that costs will reduce by at least 3% of the previous value (Lashinsky, 2014).
Modes of Transportation throughout the Supply Chain Network
Apple relies on road and air to transport raw material to the manufacturing plant in China. Depending on the location of suppliers of different components of the final products, the company has developed an extensive road and air transportation network in a bid to reduce costs, improve efficiency, and optimally track the entire process. From time to time, “Apple first coordinates flights and trucks to move components from suppliers to assembly plants in China” (Lashinsky, 2014, p. 26). For instance, transportation of production components from Taiwan, Korea, and Singapore plants to China is done using either air or road, depending on the urgency and existing transport policy. However, Apple Incorporation is very discrete in the transportation of raw materials to its primary production plant in China. The moving process of new products begins in China, where pallets of finished Apple goods are moved from the production factories via road in unmarked containers that are trailed by security detail.
These containers are loaded onto special trucks and moved to the shipping warehouses within China by road. The containers are then packaged and shipped using pre-bought space in airfreight to the US market. Specifically, “these shipments are steadily monitored by security guards at all times, from truck depots, airports, customs, and storage warehouses until the product is finally unveiled” (Lashinsky, 2014, p. 45). Among the notable airfreight spaces utilized by Apple Incorporation is used Russian military transport planes. Apple Incorporation also uses FedEx airline’s Boeing 777s, which are chartered at the cost of $242,000 per trip from China to Memphis and can carry up to 450,000 iPhones (Lashinsky, 2014). The transportation ends in Apple’s traditional retail stores, where adjustments are made on the basis of customer demand.
Types of Warehousing
Apple Incorporation uses different types of warehousing in supply chain management. The primary warehouses include distribution centers, private warehouses, public warehouse, and automated warehouses. These warehouses are climate-controlled and use state-of-the-art technology in line with the company’s sensitive products. The distribution centers are spread across the globe, with the main hub in Memphis. In these warehouses, Apple’s shipped products are stored temporarily while awaiting transportation to retail stores (Long, 2014). The company uses these distribution centers to receive finished products, which are then shipped to customers. Apple Incorporation owns several private warehouses to store its inventories. Since finished products are shipped in bulk at the launch of a new version, these private warehouses are used to prepare for an influx of orders (Lockamy, 2014).
When the demand is very high, especially in the first three months of a new product launch, Apple Incorporation often rents many private warehouses to keep up with market demand. The company also leases public warehouses to meet the short-term distribution needs. For instance, when the forecasted demand is higher than the available storage space for new products, the company seeks out additional storage in public warehouses. This strategy is aimed at keeping a surplus inventory to meet any additional market demand. Moreover, Apple Incorporation uses automated warehouses as part of a cost-cutting strategy in supply chain management (Ali & Shukran, 2016). These warehouses are completely automated and require minimal manpower for supervision since most of the work is done by carriers, cranes, and the latest software technology.
Metrics to Measure Supply Chain Performance
Cost
The cost metrics for measuring supply chain performance at Apple Incorporation are reduced wastes and total manufacturing costs as functions of the same elements in the previous financial year. The company would declare an improvement in supply chain performance when wastes are lower than those of the previous year (Lockamy, 2014). The same trend is used to track the total manufacturing cost. Whenever there is a reduction in the total cost of production, Apple Incorporation records an improvement in supply chain management.
Service Levels
The metrics used to measure improvement in the supply chain at Apple Incorporation are near real-time information flow and the establishment of a collaborative framework against the performance of the same elements in the previous production year. When the collaborative networks between the company and suppliers/supply chain partners improve, the service levels equally expand and vice versa (Mandal & Korasiga, 2016). Moreover, an improvement in the real-time information flow is a sign of efficiency and commitment to sustainable and effective value proportion.
Inventory Turnover
The primary metric for measuring improvement is a reduction in inventory turnover in the entire supply chain network. Higher inventories than the previous production plan suggest increased inefficiencies in the production cycle (Long, 2014). On the other hand, a reduced inventory translates to improve efficiency and dependability of the entire supply chain sequence.
Apple Incorporation’s Metrics
The internal measures of effective and sustainable supply chain management are the ability to function within the projected long-term commitment, supplier dependability, high sales volume, and eradication of delays (Chopra & Meindl, 2014). Fulfillment of any of these metrics is an indication of an improved supply chain performance.
Supply Chain Improvements
On the eve of the important iPhone launch in the previous year, Apple Incorporation’s supply chain experienced delivery delays and shortages against high market demand. Although the company projected a worldwide pre-order of 40 million units, the company was only able to avail 20 million iPhone units (Lashinsky, 2014). Moreover, the company was not able to resolve the shortages as market demand surpassed production capacity. In order to avoid the recurrence of a similar situation in the future, Apple Incorporation should remove sourcing bottlenecks and centralize demand planning.
Remove Sourcing Bottlenecks
In last year’s smartphone release date, Apple Incorporation only managed to avail 3 million units due to sourcing challenges. Many industry analysts have associated the shortages to a “low stock of three parts of the phone, including issues with sourcing the sophisticated facial recognition components, circuit boards, and camera modules” (Lashinsky, 2014, p. 67). The biggest contributor to delays was the new technology of facial recognition, which needed a 3-D sensor to use face recognition in unlocking the new handsets. With a short supply of 3-D sensors, the company’s production function faced hurdles. In order to avoid a similar incident in the future, the company should remove such bottlenecks in the supply chain through engaging reliable and consistent suppliers that are flexible to meet expanding customer demand (Chopra & Meindl, 2014).
Centralizing Demand Planning
In a complex supply chain like that of Apple Incorporation, strategic collaboration with stable and reliable global fulfillment partners may be critical in ensuring delivery and manufacturing timelines are met. Thus, integration of a well-centralized demand planning approach alongside reliable fulfillment supply chain partners will guarantee the company of effective handling of inventory, planning, and supplier management (Ali & Shukran, 2016). Since supply chain excellence is constantly experiencing a paradigm shift into difficult and more complex networks, Apple Incorporation should recruit effective end-to-end physical and digital supply chain management partners to optimize the outcome.
Conclusion
Apple Incorporation has a stable supply chain network. There are suppliers and supply chain partners supporting the company’s stratified approach in managing its value chain. The production facility is based in China. Apple Corporation uses road and air to transport raw materials and finished products. However, the company is grappling with challenges such as decentralized demand planning and sourcing bottlenecks. Apple Incorporation may engage flexible and reliable suppliers to overcome these setbacks.
References
Ali, I., & Shukran, K. (2016). Managing supply chain risks and vulnerabilities through collaboration: Present and future scope. The Journal of Developing Areas, 50(5), 335-342.
Chopra, S., & Meindl, P. (2014). Supply chain management: Strategy, planning, and operation (5th ed.) [Ebooksbvd version]. Web.
Lashinsky, A. (2014). Inside Apple: How America’s most admired-and secretive- company really works. New York, NY: Business Plus.
Lockamy, A. (2014). Assessing disaster risks in supply chains. Industrial Management and Data Systems, 114(5), 755-777.
Long, Q. (2014). Distributed supply chain network modeling and simulation: Integration of agent-based distributed simulation and improved SCOR model. International Journal of Production Research, 52(23), 6899-6917.
Mandal, S., & Korasiga, V. (2016). An integrated-empirical logistics perspective on supply chain innovation and firm performance. Business: Theory & Practice, 17(1), 32-45.