Abstract
Lean operations as a strategy in project management are rapidly gaining popularity around the world. In this dissertation, the focus is to analyse the application of lean project management in different sectors of the economy. The researcher relied on data collected from both primary and secondary sources. Secondary data was obtained from books, journal articles, and reliable online sources. Primary data was obtained from sampled respondents. Once primary data was collected, the researcher conducted a quantitative analysis to understand how lean project management is applied in different areas based on the knowledge and experience of the respondents. Findings of the investigation show that lean project management is increasingly becoming popular. Government institutions, private companies, and non-governmental institutions have realised the benefits of using this strategy and are keen on applying it in their operations. The biggest challenge identified was that most organisations do not understand how it should be applied.
Introduction
Background
The concept of lean project management is rapidly gaining popularity around the world in different fields. According to Schaufelberger and Holm (2017), a lean operation involves the provision of excellent value to customers using the least amount of resources. Its fundamental principles are the creation of maximum value for clients and the elimination of waste. When using this concept, a firm should understand what the market needs and then develop unique strategies for providing it in the best way possible. Customer satisfaction is paramount at all times when applying the strategy. Waste elimination is of great essence when applying lean operations in a company (Yang et al., 2017). When a company eliminates waste, one of the outcomes is that the cost of production will be lowered significantly. The process requires a deep understanding of tasks and clear communication among all stakeholders involved so that they can understand what is expected of them when undertaking a project. Mistakes have to be eliminated because they are often responsible for the unnecessary generation of waste. The process also shortens the time that it takes to complete a project.
Lean operation is currently applied in the manufacturing industry, the service sector, governmental institutions, and non-profit organisations. Its relevance has been proven in different markets. Dahl (2020) explains that large projects both in the private and public sectors are currently implemented under this concept. It is beneficial to the project owner because of two principles meeting customers’ expectations and eliminating waste. The owner or sponsor of the project is assured that all tasks will be completed within a given period as per the expectations and using the predetermined resources. Cases of the inflated cost of projects and delays in their completion often make project owners avoid megaprojects because of the fear that they can stall. However, lean project management addresses such fears by ensuring that costs are maintained as low as possible. In this paper, the researcher seeks to discuss the application of lean project management in different areas.
Problem Statement
Government entities and private companies have embraced the concept of project management as the best way of undertaking developmental activities. This approach makes it easy to assign specific resources to the activity, set a timeline within which it should be completed, and assign specific individuals or companies with the best skills in that field the task of completing it (Modi, 2017). However, most of the major projects are often completed late and at an inflated cost. The problem is common in government projects that may take several years to complete. One of the most common excuses that contractors often give is the problem of inflation in the economy (Stark, 2019). The problem is that it is always impossible for the project cost to drop when there is a reduction in the cost of materials used in the construction.
Whenever a project is completed at a higher cost and at a date later than what was expected, its value would significantly drop. This problem has been affecting large projects both in the public and private sectors. The inability to determine the actual cost of a project and its timeline creates uncertainties. Parties involved in the project are not aware of what they should expect once a project is initiated. For a government or a company to approve a given project, some of the primary factors that have to be defined in clear terms are cost and timeline. Lean project management promises to eliminate these uncertainties by making the stakeholders understand what to expect and how to plan for it.
Cases of unnecessary generation of waste have been common when undertaking large projects. Salah and Rahim (2018) note that one of the reasons that cause massive waste generation is miscommunication among the relevant stakeholders in the project. When the designer fails to engage the contractor regularly to understand how the plan is being implemented, incidences may arise where a section of the construction has to be destroyed because of the failure to follow specifications. Assigning tasks to individuals who lack the capacity to deliver the desired outcome is another issue that always arises. Such individuals with limited knowledge and experience are likely to make costly mistakes because they do not understand how they can undertake a given activity appropriately. When these undesirable events happen, the additional cost is often transferred to the project sponsor, even if the mistake was made by the contractor and designer (Kim, 2017). Lean project management focuses on addressing these concerns. The contractor must understand tasks that have to be completed within a given period, assign experts who will avoid mistakes, and ensure that success is not compromised at all.
Justification for the study
Lean operation is rapidly gaining popularity because of its relevance in solving problems in project management. Currently, the global community is battling the COVID-19 pandemic that is threatening to cripple the economy of many countries. The rate of hospitalisation in many countries has shot up significantly, and many healthcare institutions are overwhelmed. As such, there is an urgent need for both public and private sector healthcare entities to expand their infrastructure. Hospitals are getting constructed all over the world to help create room for the additional patients who have to be admitted when their condition gets worse. Besides the pandemic, the need for private and public sector entities to expand their operations has always remained significantly high. Riis (2017) observes that one of the best ways of knowing whether a company is growing is to determine the amount of space it uses to support its operations. Governments also have the responsibility to regularly repair existing infrastructure (roads, rail, port facilities, housing, and communication infrastructure, among others) or build new ones. Cost is always the most important factor that has to be considered in such projects.
This dissertation will discuss how organisations in different areas can apply the concept of lean project management to improve efficiency in their production, human resource management, and other areas of operation. Oke and Aigbavboa (2017) argue that not all companies have been able to apply this concept adequately. It is one thing to popularise lean operations and another to actually implement them in actual activities within a project. Many companies claiming the use of this tool still produce unnecessary waste in their production because they do not understand how they can apply its principles and pillars. For instance, one of the critical pillars of lean operations is aligning workers’ skills with their assignments to ensure that only those who are highly qualified handle specific tasks (Rosenfield, 2017). It is only through such alignments that unnecessary generation of waste can be eliminated. The dissertation will discuss each of these principles and primary pillars that have to be embraced when a company or a government department is keen on embracing lean project management. Through this document, they can conduct a comprehensive assessment of their current methods to determine weaknesses that limit their ability to eliminate waste and enhance efficiency in their operations.
Research Aim, Objectives, and Questions
The aim of this dissertation is to analyse the application of lean project management in different areas of operation. The concept has gained massive popularity both in the public and private sectors over the recent past. It is necessary to look at how an organisation can use it to promote efficiency, reduce cost, and enhance overall performance. The following are the specific objectives that have to be realised through the collection and analysis of data from primary and secondary sources:
- To determine how well various stakeholders understand the concept of lean project management.
- To discuss the level of application of lean project management in different sectors.
- To identify and discuss the benefits of lean project management in different organisations.
- To discuss challenges that different organisations face when trying to implement lean project management.
The researcher had to develop a list of questions that facilitated the collection of data. The following research questions were developed based on the above research objectives:
- How well do various stakeholders understand the concept of lean project management?
- What is the level of application of lean project management in different sectors within the local economy?
- What are the benefits of lean project management in different organisations?
- What are the challenges that different organisations face when trying to implement lean project management?
Literature Review
The chapter focuses on reviewing the literature to understand what other scholars have found out with respect to the application of lean project management in different areas. According to Oakland and Marosszeky (2017), lean operation in project management is a field that has attracted the attention of many scholars who are keen on understanding how efficiency can be improved. Reviewing what these scholars have found helps in identifying existing knowledge gaps.
Understanding the Concept of Lean Management
It is necessary to start the review by understanding the concept of lean management. According to Kumar and Basu (2017), lean management primarily focuses on the elimination of wastes in the production process. It strives at achieving project excellence through five main principles, which have to be observed in a systematic manner. Womack et al. (1990) defined lean production as “a business and production philosophy that shortens the time between order placement and product delivery by eliminating waste from a product’s value-stream” (p. 56). As shown in the definition, the concept emphasises the need to complete projects at the right time, in the best way possible, and using the assigned resources. The first step is to define customer value. This step involves understanding what customers need from the company. There is always the need to ensure that there is a continuous improvement of value for customers. Comparing what rival firms are offering and determining how well-satisfied customers are may help in determining the expected value. The second step is to measure the capability of the company to meet these needs. Kerzner (2018) explains that internal assessment helps in identifying possible weaknesses and developing effective ways of addressing them. This process entails coming up with a proper plan on how to meet the expectations of customers in the best way possible.
The third step involves creating flow and eliminating waste. At this stage, the team will be aware of customers’ expectations and the ability of a firm to achieve them using the available resources. At this stage, the team will put in place a system meant to achieve the desired goals using the available resources. Efficiency is given priority as the team is expected to eliminate all forms of waste in the process. The fourth stage requires improvement and innovation as the team moves toward meeting customers’ expectations (Kerpchar et al., 2015). It requires regular reviews to understand weaknesses in the current system and to develop new ways of fighting identified weaknesses. The last stage toward achieving project excellence is a controlled and sustained performance process. The assumption is that at this stage, the team should have achieved a proper rhythm of operation that avoids waste at all stages of production and emphasises the need for excellence. The team must then pursue perfection at every stage of the production process. Figure 2.1 below summarises the concept of lean management based on the above five principles.
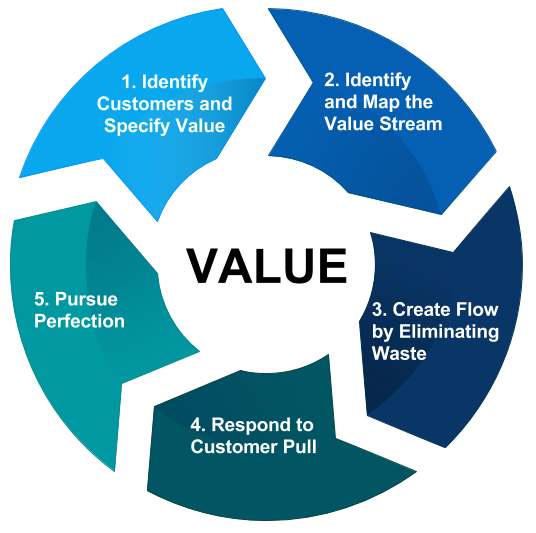
Origin of the Concept of Lean Management
The concept of lean production emerged because of increasing levels of competition in the global market. According to Hunt (2018), soon after the Second World War, American corporations dominated the global market in the automotive, aviation, security, and many other manufacturing industries. Their goal was to make their products available in large quantities across the world. The competition was relatively low, and as such, they could dictate forces in the market. However, that changed a few decades later as many companies started to emerge, targeting the same customers (Dahl, 2020). The introduction of new players in the industry meant that customers could choose from various brands based on quality and price. The new trend forced corporations to embrace new strategies that could ensure that they remain highly efficient. They had to cut the cost of operation while at the same time reducing the time within which their products are made available in the market. One of the companies that perfected the concept of lean production was Japan’s Toyota Corporation. Analysing the approach that this company took to cut the cost of its production and improve efficiency can help in understanding the origin and growth of lean project management.
Toyota’s Lean Production System
Toyota Motor Corporation is one of the companies that have perfected the concept of lean production. When it started manufacturing cars, Rosenfield (2017) argues that this Japanese company faced stiff competition from American and European car manufacturers. The competitors already had a strong brand in the industry and enjoyed the benefits of economies of scale. The company had to decide whether it would focus on the production of high-quality highly-priced cars or low-cost cars targeting the masses. The low-cost car market appeared more lucrative, especially within the Asian market that has a large population of the middle class. The management realised that they had to make a radical shift from traditional approaches to producing cars to ensure that they lowered the cost. It has to embrace unique ways of producing cars that would enable it to make its products highly affordable to the masses.
The initial concept that the company embraced focused on two primary pillars, which were respect for people and continuous improvement. The company realised that when its employees feel respected, they tend to perform well than when they feel oppressed (Salah & Rahim, 2018). As such, it introduced a new culture where its workers could easily contact their superiors so that issues that affect their work could be addressed. Ideas of junior employees would be taken into consideration when creating new concepts of operation. This strategy helped in promoting creativity and innovativeness among workers. Implementing new policies also became easier as all workers felt that their ideas formed part of these policies. The company also promoted teamwork among employees. The management made employees realise that the overall success of the company depends on the individual output of every employee. Assisting a colleague who is struggling to accomplish a given task is essential in enhancing the overall success of a department. Instead of promoting rivalry among workers, the management created a system for collaboration (Schaufelberger & Holm, 2017). It helped in enhancing the unity and productivity of workers. Cases of wastage and damages were reduced significantly because of these initiatives.
Continuous improvement was another factor that the management of Toyota focused on to help improve efficiency. The management realised that it could lower the overall cost and improve efficiency by maintaining a culture of continuous improvement. One of the main factors that helped in promoting improvement was the idea of observing best practices around the world to understand its own weaknesses. It made an effort to compare its mode of operations with other firms around the world, including those that were not operating in the car manufacturing industry (Salah & Rahim, 2018). Best practices were embraced and helped in defining new policies and operational practices within the firm.
The company also embraced the challenge as a way of promoting continuous improvement. The challenge was taken at different levels within the company. The first one was at the employees’ level. Employees were encouraged to challenge their own capabilities by striving to deliver better output every time they undertook a given task. The strategy helped in promoting creativity and innovativeness among these workers. The second was at the departmental level (Rosenfield, 2017). The management would set new manageable milestones every time the previous ones were realised. A clear path and relevant resources would be provided to help the department realise these new expectations. The entire organisation would also have its own new challenges meant to improve its capacity to deliver improved performance. The goal of the company has been to deliver better products to its customers at affordable prices. Figure 2.2 below identifies the pillars and foundation of lean management and operation at Toyota.
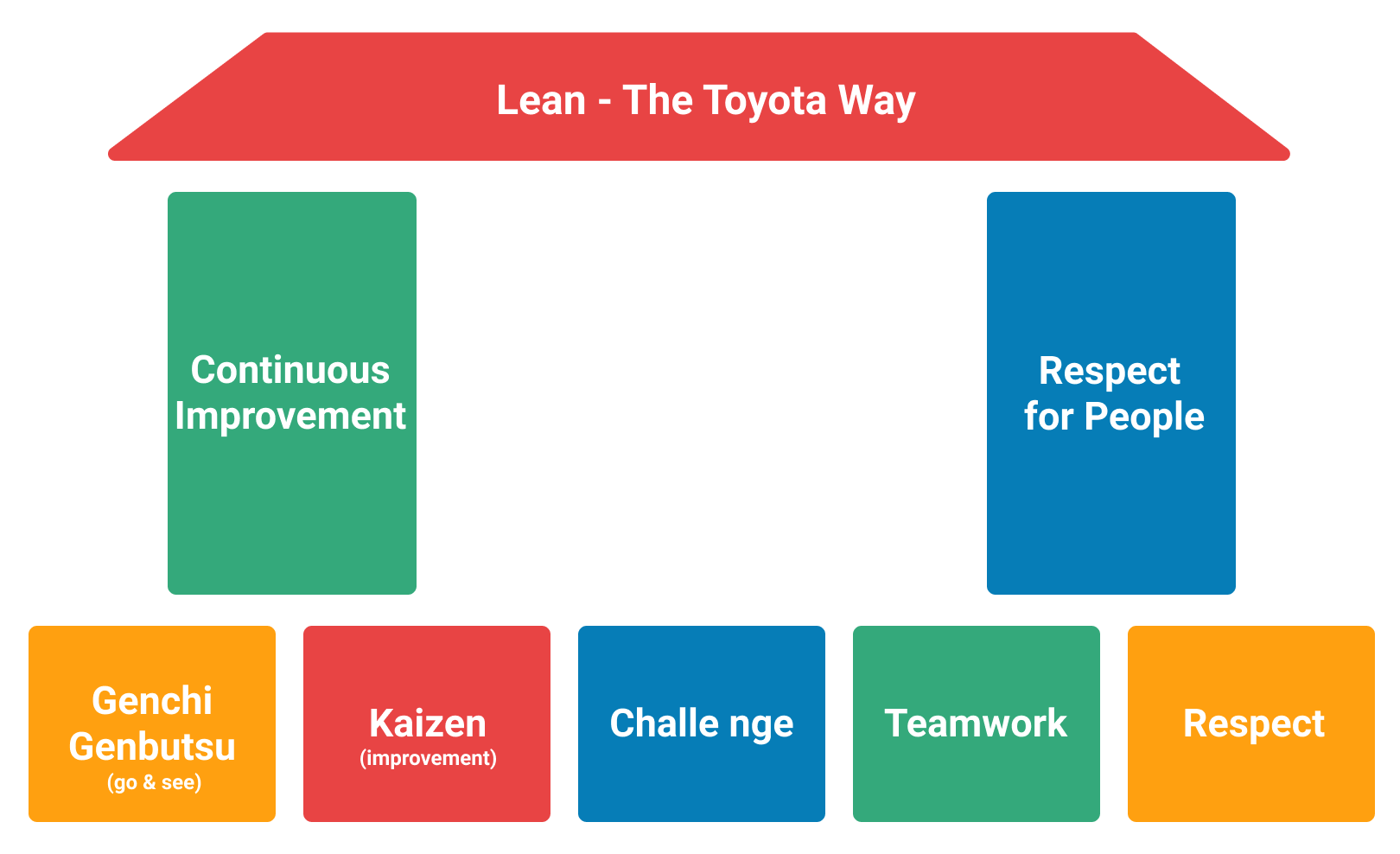
Basic Elements of Lean Production
Lean production has basic elements that have to be observed to achieve specific goals that an organisation desires. According to Baldwin (2019), the number of elements has increased since the concept emerged as new strategies continue to emerge to help in improving a firm’s performance. In this section, the researcher focuses on the basic elements of learning that must be taken into consideration in the application of lean project management, irrespective of the size of a company or the industry within which it operates.
Elimination of waste is one of the primary elements of lean project management. The project manager and team members should come up with effective strategies for identifying the primary sources of waste and develop means of eliminating them. Dahl (2020) explains that the process starts with the identification of the various types of waste. They include defects, damage during transportation, waste caused by delays, and poor inventory management. Other types of waste arise from overproduction, over-processing, and underutilisation of human resources. The significance of classifying wastes is to ensure that the management can address them from their source. For instance, if it is established that a significant amount of waste is generated during the process of transporting raw materials to the company or finished products to the market, the management will need to redefine its approach to transportation to eliminate factors that cause the damage (Heldman, 2018). When it is noted that human resource goes to waste because of the underutilisation of people, the management can find ways of redeploying the excess workforce to other departments or declaring them redundant. The goal is to have a system that is highly efficient and does not produce significant amounts of waste.
Kaizen/continuous improvement is another major element that formed the basis of Toyota’s lean production system. According to Yang et al. (2017), companies must appreciate the fact that there is always room for continuous improvement in their production system. This element requires a regular assessment of the system to identify major areas of weakness. Each time a weakness is identified within the system, the management must investigate its cause, the individuals responsible, and ways in which it can be managed. When these factors have been defined, the team will then introduce corrective measures to eliminate the problem. Sometimes the need for improvement may arise from the emergence of new technology or system of production. As such, companies are encouraged to embrace best practices and new concepts that can help in achieving the desired goals (Oke & Aigbavboa, 2017). The Kaizen concept encourages the idea of always looking for new ways of making the production process more efficient by enhancing production strategies.
Continuous flow is another unique element of lean production. It propagates a change in strategy, from the mass delivery of production materials to a manageable approach where items are made available when they are needed. Davidson (2019) explains that the strategy requires effective communication among various departments to ensure that the production capacity is clearly understood by the finance and procurement departments. The goal of the continuous flow element is to ensure that production does not stop because of delays in delivering products. At the same time, it avoids cases where excess materials are delivered to the company when they are not yet needed. It helps to eliminate wastes that often arise from the increased handling of raw materials. It also reduces lead time and the need for more workers (Hunt, 2018). The outcome of the strategy is reduced cost of delivering products to customers at the right time.
Equipment reliability is another major element of lean production. Philippopoulos-Mihalopoulos (2017) explains that one of the major causes of delays and unnecessary production of waste is a regular breakdown of equipment. Every time equipment breaks down. The entire production process has to be halted so that the problem can be addressed. Sometimes the breakdown may affect an important stage that forces the management to discard semi-processed inventory, leading to massive waste. The concept of lean production requires a company to ensure that its productions tools and machines are running optimally (Oke & Aigbavboa, 2017). Regular checks, maintenance, and replacements may be necessary to ensure that everything is running as per the plan.
Process capability and control are also crucial in enhancing lean production in project management. Process capability focuses on assigning specific responsibilities to employees who have the capacity to deliver the expected output (Englund & Bucero, 2019). It discourages the unscientific practice of assigning tasks based on the preferences of the project manager. Instead, the manager must start by defining job requirements and expectations that have to be achieved. The responsibility of the holder of that office should then be outlined. It is then that the team must focus on finding individuals with the right skills to meet the set goals (Yang et al., 2017). Individuals who do not meet job specifications should be dropped from the project. Assigning people with the right skills to specific jobs helps to eliminate unnecessary mistakes in the project. It also improves the productivity of the department. System control promotes assessing the entire production unit to determine if it is running as per the expectations of the management. Weaknesses should be identified and eliminated at the right time.
Error proofing is highly encouraged in lean production. Dahl (2020) observes that a common practice in the modern business environment is to recall defective products that have reached the market and compensate customers accordingly. The problem is that sometimes customers may be harmed by the defective product, making the recall strategy impossible. It means that when errors in the production system and product are not detected at the right time, it may have devastating consequences not only on the finances of the company but also on its image in the market. The best way of dealing with the problem is to have a systematic way of error proofing. Mistakes in a product should be identified at the earliest stage of production to avoid cases where they are released to the market with defects. As Kerzner (2019) notes, such defects are often caused by an error in the production system. It may be the problem with the machines or individuals assigned the role of production and quality assurance. Addressing the problem at the source helps in ensuring that such errors are eliminated in the production system. Error proofing should be a continuous process, and it should be the responsibility of the quality assurance department.
The Kanban system is another concept that is often encouraged in lean production. In mass production, companies often use the push system, where the focus is to make products available in the market in large quantities. The company will then expect the sales and marketing department to find the market for the already available products. The Kanban system takes the opposite approach to production. In this demand-pull strategy, the production unit relies on the sales and marketing department to provide an accurate forecast of market demand within a given period. The company will then initiate the production of the needed items in the stated quantity. The aim is to avoid overproduction, which often leads to the unnecessary generation of waste. Instead, the company uses the prediction strategy to ensure that the exact amount that the market needs is made available.
Visual management is also emphasised as a major element in lean production. It helps in addressing various challenges that may arise in the production process. First, maintaining visual operations creates a perfect environment for new employees to learn new skills for undertaking their responsibilities (Oke & Aigbavboa, 2017). Secondly, visual management is one of the most effective ways of promoting the assessment of the production system. The quality assurance team is able to identify weaknesses in the current system at the earliest stage possible (Dahl, 2020). Such mistakes will then be eliminated to ensure that the entire production system is effective. Finally, visual management and operations promote transparency. Everyone will easily understand activities that are undertaken to achieve specific goals, resources used, time that was spent, and other factors that may be necessary for investigating the performance.
Application of Lean Project Management
Lean project management can be applied in different contexts, from manufacturing to the service industry. In the current competitive business environment, there is pressure for companies to deliver greater results using fewer resources. Kerzner (2018) explains that to achieve such great efficiency, it is important for a firm to embrace concepts and practices that help in eliminating waste while at the same time improving productivity. Lean management grew from the manufacturing industry, as shown in figure 2.2 below. The ability of a firm to charge competitive prices for its products depends on how efficiently the production process is. When the production cost is maintained as low as possible, then a company can afford to charge a lower price without compromising on its profitability. Companies had to embrace innovative ways that enabled them to maximise the use of limited resources to achieve the set targets.
Lean project management targets eight main processes and production stages where wastes are likely to be generated. The first one is the elimination of defects in the production process. Rosenfield (2017) explains that whether a firm is operating in the car industry, food industry, electronics, or cosmetics, defective products often have to be eliminated from the process line so that they do not find their way to the market. A phone that has a defect in its battery system may become explosive. Similarly, a car with a problem with its braking system can easily cause an accident if it reaches the market. When defects are identified and eliminated, the cost is transferred to the company. The concept of lean project management promotes the need to eliminate any form of waste at every stage of production (Salah & Rahim, 2018). The quality assurance team must identify specific factors responsible for waste generation and then find ways of eliminating them.
The inability to manage overproduction is another factor that is always associated with an increase in the overall cost of production. Riis (2017) observes that when embracing the lean production concept, the marketing department must maintain constant communication will all the other departments, especially the production unit, finance department, and logistics unit, to ensure that what is needed in the market within a given period is what is released. Overproduction forces the management to expand its storage capacity, which inflates the overall cost of production. Another major challenge that often arises is damage arising from the constant handling of finished goods in the warehouse. Pilferage is also a concern when a company regularly overproduces products, which then have to be stored for long. When a company is producing perishable products, it may be forced to sell the excess products at lower prices or face the risk of throwing them away. Such incidences not only lead to an increase in the cost of production but also results in unnecessary waste and theft. Producing just enough goods needed in the market helps in cutting the cost of operation.
Targeting non-utilised talent is another major concept when one is keen on embracing lean production within a company. According to Salah and Rahim (2018), cases, where one’s skills are mismatched with their talents, are some of the most common practices in underperforming companies. Such cases arise when one is forced to fill a vacancy that is not aligned with their training. Lean management encourages project managers and departmental heads to identify the special skills and competencies of their subordinates. Tasks should then be assigned to them based on these identified skills. As Kerzner (2018) observes, people tend to perform optimally when they are assigned tasks aligned to their skills. They get greater motivation when they put to practice something that they have learned over a given period. It also eliminates unnecessary mistakes often associated with guesswork.
Transportation is another area of concern that has to be considered in lean production. Many companies spend more than is necessary because of their inability to have an effective transport system. The management of a company has to determine whether it is necessary to have an internal transport system or source for these services from specific providers (Schaufelberger & Holm, 2017). It depends on how often the company uses transport services, the level of sophistication needed during transportation, the availability of employees to undertake such tasks, and associated costs. Careful planning and assessment of the various available options can help the management to make the right decision.
Inventory management is also essential when embracing the concept of lean production. Once goods leave the production plant of a company, they have to be handled with care during the entire transit process till they reach the final customer (Salah & Rahim, 2018). A product such as milk is not only highly perishable but also delicate and requires proper handling. As the company speeds the process of making it available to customers in the market within the shortest time possible, it must remember that spillage is a possible threat that has to be observed. Any form of contamination of the product can shorten the lifespan even further. Managing the inventory is, therefore, an essential part of an operation that has to be handled with care. Eliminating breakages, pilferage, and spillage of products once they have been manufactured and during the entire process of availing it to customers is critical in lowering the overall cost of production. Extra-processing and motion are the other factors that a company, government entity, and non-governmental organisation should not be ignored when they are keen on cutting their cost of operation.
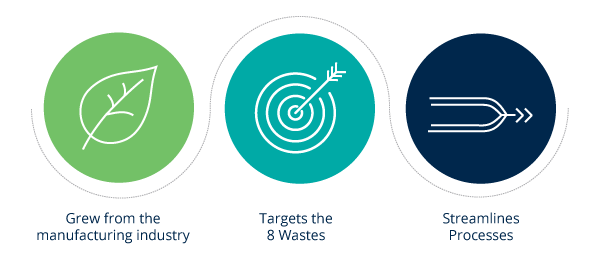
The principles and practices discussed above can be applied in different areas of operation. In the manufacturing sector, companies have realised that the only way of maintaining a low cost of production is to embrace lean production concepts. It helps to identify and eliminate waste while at the same time promoting efficiency. In the service delivery sector, this concept has also proven to be very effective. For instance, service sector companies have learned the significance of matching the skills of their employees with tasks assigned to them. Doing so helps to avoid unnecessary mistakes because one is fully aware of what is expected of them and how to achieve the desired goals. Yang et al. (2017) note that lean production has also gained popularity in the public sector. Government departments are using it to lower the cost of their operations, eliminate waste, and enhance efficiency. Incidences, where governments outsource services from specialised companies, are becoming common because of the understanding brought about by this concept (Salah and Rahim, 2018). Non-profit making organisations are also using lean management practices to ensure that they are more responsible for the donations they receive. They understand the fact that it can help them achieve more using their limited resources.
Project Management History and Theory
Project management has been in existence for as long as the civilisation of humankind. However, Westland (2018) explains the use of the phrase ‘project management,’ and some of its unique techniques are relatively new. The modern approach to project management can be traced back to 1911, when Frederic Taylor published ‘The Principle of Scientific Management’ (Westland, 2018). The revolutionary publication created awareness about undertaking tasks in a coordinated approach, using specific resources, and within a given period. In 1917, Henry Gantt developed the Gantt chart to help in allocating time to activities in a given project. It was a major milestone as it made it easy for stakeholders to have an accurate prediction of when a project should be completed (Wysocki, 2019). Tasks had to be defined and allocated time in a systematic way that makes it easy to hand over responsibility to the next team once one unit has completed its assignment. Dupont developed the critical path technique in 1957 (Westland, 2018). It was one of the earliest tools that were used in project management.
These concepts gained popularity even in governmental agencies. The United States Department of Defence, under its Navy Special Projects Office, created a program evaluation review (PERT) to facilitate the evaluation of its projects (Dahl, 2020). It gained acceptance in both public and private sector companies because of its relevance. The United States Department of Defence started using a work breakdown structure (WBS) IN 1962 to help in assigning tasks in major projects based on competencies. Eliyahu Goldratt developed the management philosophy theory of constraints (TOC) in 1984 (Westland, 2018). It focused on identifying elements that may affect the ability to complete projects at the right time and with the budgeted resources. In 2001, agile as a tool and a theory in project management emerged and was put to use among many companies in the United States, Europe, Asia, and other parts of the world. A major advancement was made in 2008 when projectmanager.com was launched (Westland, 2018). It brought project management to the world of cloud computing.
On-Time On-Budget Mantra
The fundamental mantra for lean project management is on-time, on-budget delivery. This mantra emphasises two main factors that often define the ability of a project to deliver the desired value. First, there is a need to deliver projects within the set timeline. Delay in major projects has always been blamed on cost inflation. Issues such as theft, wastage, and the need to redo some activities often arise when a project is not delivered within the planned time. When the delivery is delayed, another problem that would arise is that the expected value or benefits would not be available at the expected time. If it is the construction of a road, those who were to benefit from it may have to wait for a longer period than was expected to start enjoying it. Rosenfield (2017) believes that delaying a project often diminishes its expected value of a project. A company may be forced to get into unexpected expenditures when delays arise. For instance, when the construction of a warehouse takes longer than was expected, the affected company may be forced to rent a facility to sustain its operations during the period before the project can be completed.
The mantra encourages the completion of projects within the original budget. One of the biggest challenges that companies, governmental institutions, and non-profit companies face in megaprojects is the upward adjustment of the planned cost of a project. According to Dahl (2020), many of these projects often experience over a 30% increment in the initial cost. One of the primary factors that often lead to cost inflation is unnecessary wastage during the process of implementation. The contractor may fail to ensure that materials used in the construction process are kept carefully for future use. Another challenge that may emerge is pilferage. Cases, where employees steal some of the materials from construction sites, are often common. Wrong designs or ineffective implementation of the right design may bring about the need to demolish a section of the construction, leading to a loss of time and resources. All these wastages and thefts lead to an increase in the overall cost of production that the owner has to meet. Lean management eliminates possibilities of wastage and damage that may result in inflation of the operation cost.
Benefits of Lean Project management
Lean project management has numerous benefits to corporate entities, governmental institutions, and non-profit organisations if it is applied in the right way. According to Stark (2019), the growing popularity of this concept in construction, manufacturing, air travel, automotive, and numerous other industries is a clear testament to its effectiveness in lowering operations costs and enhancing overall productivity. It is a major improvement of tools such as total quality management (TQM) and six-sigma, among others. It is necessary to discuss these benefits to help in defining why it is essential for one to embrace them.
As evident in the discussion above, one of the greatest benefits of lean project management is the reduction of waste. One of the biggest concerns when undertaking both large and small projects is the unnecessary production of waste. Carelessness is known to be one of the major factors that often lead to the mass production of waste. Actions such as taking wrong measurements, delay in undertaking a given task, and other related mistakes may lead to mass production of waste. Lean project management helps in eliminating this problem by investigating all the potential causes of waste production (Dahl, 2020). When these sources are identified, the management has to find a way of eliminating them as a way of enhancing efficiency in the production process.
Reduced lead time is another benefit of using lean project management. According to Modi (2017), when a company manages a project under the lean concept, it must follow specific guidelines at all stages of operation. One of the requirements is that workers must be assigned tasks based on their skills and experience (Stark, 2019). It strongly discourages cases where tasks are assigned based on one’s availability or desires of the project manager. This skill-based approach to assigning tasks eliminates cases of delay that may arise from the mistakes of employees. Lean project management also promotes the use of a just-in-time (JIT) approach to making production materials available for the company. It means that cases, where activities are stopped because of delayed delivery of raw materials are eliminated.
Less rework is another major benefit that is associated with lean project management. One of the undesirable practices when managing a project is the need to redo an activity that had been done by someone else. Such incidences often arise when tasks are assigned to individuals who lack the right skills or experience. Redoing a work may also be necessitated by poor communication among stakeholders. When the team fails to implement the original design as expected by the owner, the team may be forced to undo and redo sections of the project. Employing lean project management eliminates such events. First, it ensures that there is effective communication among stakeholders. It also ensures that an efficient communication system is maintained throughout the lifespan of the project. The implementing team should be aware of what is expected of them at every stage of the project. On the other hand, the designer and project owner should be aware of every activity that is undertaken in the project.
Financial saving is another benefit that is associated with lean project management. Many companies are currently under tight financial pressure because of the need to expand, conduct research, and ensure that they deliver superior products at competitive prices. As such, they cannot afford to deal with unnecessary inflation in the cost of major projects (Voehl & Harrington, 2016). The fundamental principle of lean production is to ensure that activities are conducted based on the predetermined budget. Identifying potential sources of waste and eliminating them is one of the best ways of keeping projects’ costs as low as possible. Using experts to undertake specific responsibilities also enhances efficiency, lowering the operation cost.
The lean concept also enhances the understanding of processes in project management. The success of a given project depends on how well the stakeholders involved understand the primary goal that should be achieved and their role in achieving the set objectives. Yang et al. (2017) argue that it is not just about completing tasks assigned to an individual or a team. It is also critical for one to understand how their individual action would help realise the goal of the project. This understanding creates commitment as everyone will have the anticipation to facilitate the realisation of the primary goal. Lean project management requires the project manager to explain these goals to project members, including all the beneficiaries. Tasks should then be defined to ensure that every stakeholder understands what is expected of them and the interrelationship of tasks. This strategy makes it easy to have a smooth production process based on a mutual corporation among all stakeholders.
Methodology
The previous chapter focused on a detailed review of the literature. The purpose of this chapter is to discuss the method that was used to collect and analyse data in this dissertation. Sources of data, research design, method of data analysis and presentation, research constraints, and ethical considerations are discussed in this chapter.
Research Methodology
Research methodology helps in defining the approach that one should take to analyse primary data collected from respondents. Trueman (2016) explains that the chosen methodology should help to achieve research goals and objectives. In this dissertation, the researcher seeks to analyse the application of lean project management in different sectors of the economy. The most appropriate research design for the study is a qualitative method (Nunkoo, 2018). This approach was considered appropriate in understanding the level of popularity of lean project management among local companies and government entities. It was also possible to understand the views of respondents about the level of relevance of this tool in enhancing operations within a given organisation.
Data Collection
It is important to note that the dissertation relied primarily on secondary data sources. However, it was equally important to collect data from a few individuals who have been involved in project management using the concept of lean operations. The researcher had to collect primary data to achieve the objectives of the study. It also helped in confirming or challenging information obtained from secondary sources. Under normal circumstances, the researcher would have had a manageable sample of the population to participate in the data collection process. However, the current problem of the COVID-19 pandemic made it impossible to choose this approach. Health experts have strongly advised against having physical interactions because of the ease with which the virus can spread from one person to another. The researcher had to adhere to these guidelines. Hence sampling was avoided. Despite this major impediment to the collection of primary data, the researcher was lucky enough to reach out to three individuals who have vast knowledge about project management and the use of lean operations. All of them are family friends who could easily be contacted over the phone without having to meet physically.
The first participant was a project management consultant who has over 20 years of experience working in this field within the country. She has also worked in Europe and the Middle East on major projects. Hence she was considered knowledgeable in this field. The second participant was a senior manager at a multinational manufacturing corporation with a branch in the country. The company is known for its unique strategies that enable it to eliminate waste production and ensure that products reach customers within the right time. His position as one of the senior managers in the production department at the company meant that he could help explain how lean project management can be applied in companies. The third participant is a government employee working with the Department of Housing. The massive infrastructural development in the country using emerging strategies makes this participant suitable for providing the needed information. Bertrand and Hughes (2017) explain that it is always advisable to have a sample size large enough to represent the entire population. Unfortunately, that could not be the case in this dissertation because of the problem explained above. This weakness was addressed by identifying three individuals with vast knowledge and experience in this field.
The researcher contacted each of these three individuals through their phones. The researcher explained the goal of the study, the desire to collect primary data, and the challenges that made it impossible to sample a large group of people to facilitate primary data collection (Sirakaya-Turk et al., 2017). The three individuals agreed to take part in the data collection process. The researcher then developed a simple questionnaire to facilitate primary data collection. These participants were informed to choose an appropriate day and time when a phone interview could be conducted. As Klugman and Lamb (2019) note, a face-to-face interview is always one of the best ways of collecting data from respondents. Besides the ability of the researcher to read facial expressions and other non-verbal cues during the interview, it is also possible to ask participants to provide further clarification on some of the responses. The global health problem explained above made it impossible to have such physical interactions. The phone interview was a suitable substitute because it allowed the researcher to engage participants directly. Fortunately for the researcher, all three participants had time to participate in the interview. They provided dates that were appropriate for this project that had to be completed within a short period. The questionnaire helped in ensuring that data was collected in a standard manner.
Research Constraints
It is important to point out various constraints that the researcher faced in this study at this section of the research. One of the major challenges that the researcher faced was accessing the school and local libraries to have access to the needed books. The new physical interaction restrictions made it difficult to access some of the local libraries with needed materials. As such, all the sources had to be obtained from online databases. Some of these databases require a subscription, while others are freely accessibly. It took time to sample the resources needed for the study. Another major challenge was the inability to have a sample of participants and to conduct physical interviews. The researcher had previously planned to have a large sample of at least 100 people participating in the primary data collection in the study. However, these new developments meant that the strategy could not work as was intended. Only three people could become a participant in the study. The bulk of information used in the study had to come from secondary sources because of this challenge. Time can also be identified as a constraint in this study. World Health Organization and various other local and international agencies are working on ways of managing this pandemic. It means that if this project could be delayed by several months, it is possible that the above challenges would not exist. However, this was a timed project that had to be completed within a specific time, irrespective of these new developments.
Ethical Considerations
The researcher had to observe ethics when conducting this study. As explained above, all the three respondents are family friends known to the participant. This could pose a challenge if personal issues were involved in the data collection process. The researcher explained to each of them that this was important academic research, and engagement during the entire time of the investigation had to be maintained at an official level. The identity of the respondents had to be kept a secret, as is always required in standard research, although they were not at risk of being victimised or intimidated because of their views. Fact that the researcher could not reach out to the managers of the respective organisations where these participants work, it was not possible to get informed consent from these institutions. Respondents were therefore informed that they would like a participant in the study as independent individuals with knowledge and experience in this field instead of being representatives of their organisations. The dissertation had to observe all the academic rules and regulations writing a dissertation. Any form of plagiarism was avoided in the study, and sources used were referenced appropriately using Harvard referencing style. The completed paper was submitted within the time that the school provided.
Analysis
This chapter focuses on the analysis and discussion of data collected from primary sources. As explained in the previous chapter, the researcher chose qualitative design as the most appropriate method of analysing data collected from sampled participants. The approach was considered effective in explaining the application of lean project methods in different industries. The following are the main questions in the study and how the participants responded to them.
How well do various stakeholders understand the concept of lean project management?
This question focused on determining the level of knowledge about lean project management that stakeholders have in different industries. Each of the respondents was asked to answer the question based on their experience of interacting with different stakeholders in their respective industries.
Participant 1 said, “Many people have heard about the concept of lean project management. They also know that it focuses on eliminating waste and improving productivity. However, many lack proper knowledge about how it should be applied to achieve desired goals.”
Participant 3 said, “The majority of people I have interacted with know the goal that lean project management seeks to achieve. Nonetheless, I have noticed that its application is still a major challenge within the institution where I work,”
The two respondents explained that the concept is becoming common and popular in the country and most certainly in other parts of the world. However, they raised an issue about the level of knowledge that stakeholders have about its application. Knowing about lean project management and its goal is a major step towards its effective application. However, one must understand that success in its use goes beyond knowing of its existence and benefits. One must understand how it should be applied effectively to achieve desired goals.
Participant 2 said, “Although the concept is widely known among stakeholders in this industry, a worrying trend has emerged where many people believe it is the responsibility of senior managers and departmental heads to understand how it should be applied.”
The work of senior managers can be very complicated if they have to explain everything about lean operations to their subordinates. It would be easier if these subordinates understood the steps involved and how they fit in the system under lean operations. It is evident from responses obtained from participants that more awareness campaigns are necessary so that stakeholders can understand what is expected of them.
What is the level of application of lean project management in different sectors within the local economy?
The researcher wanted to determine how widespread the application of lean project management is in different organisations around the country.
Respondent 2 said, “I have noticed that there is a growing number of companies using this concept based on the level of consultations I have been receiving. It is becoming a common practice in the country.”
Respondent 3 said, “The government is increasingly using this concept to ensure that its projects are completed in time and using the right amount of resources.”
The two participants strongly feel that lean project management is becoming common in the country, both in the public and private sectors. It is apparent that project managers have come to appreciate the impact of lean project management in enhancing success in their operations.
What are the benefits of lean project management in different organisations?
The researcher wanted to determine the benefits of using lean project management based on the knowledge and experience of the three participants. They were requested to outline some of the notable advantages of using the concept.
Participant 1 stated, “Lean project management helps in cutting the cost of projects irrespective of their sizes. When wastes are eliminated when undertaking various activities, the team will end up using few resources.”
Participant 2 noted, “Using lean project management helps in ensuring that projects are completed as per the schedule. Unnecessary delays often caused by poor coordination and communication are eliminated.”
Participant 3 noted, “Lean project management promotes excellence in operation because of its emphasis on assigning roles based on employees’ knowledge and experience. Unnecessary mistakes are eliminated by having tasks done by those with the right qualification.”
The three respondents identified various major benefits of using lean project management. The idea of eliminating waste helps to ensure that a project is completed using the least resources possible. Elimination of waste is facilitated by having the right people assigned the right responsibilities. In such cases, unnecessary mistakes in the project that may result in demolishing an already constructed structure are eliminated. The respondents also noted that using this strategy also eliminates delays in the project. Improved communication and coordination help in ensuring that every individual task is completed at the right time. It explains why the concept has gained popularity both in the public and private sectors.
What are the challenges that different organisations face when trying to implement lean project management?
It is necessary to acknowledge the fact that although lean project management is essential and should be embraced by organisations irrespective of their sizes, it also has some challenges that should be addressed. The researcher asked respondents to state some of the challenges they feel should be addressed.
Respondent 1 said, “The biggest challenge in the application of lean project management is that many people still lack a proper understanding of how it should be applied.”
Respondent 2 explained, “Some managers think that lean operations only focus on cost reduction. They fail to provide the right resources but expect their team to deliver the best outcome.”
Respondent 3 noted, “Some people still feel that lean operation is something that only project managers should focus on. As such, they do not take it seriously.”
It is clear from their responses that there exist some challenges that may make it difficult for stakeholders in different sectors of the economy to implement this strategy effectively. Lack of proper knowledge about project management, unrealistic expectations of those in authority, and the belief that only project managers should have detailed knowledge about lean operations are some of the major challenges that need to be addressed.
Conclusion
The application of lean project management has become popular in different sectors of the economy around the world. Findings made in this dissertation show that lean operation has been embraced as the best way of eliminating waste and enhancing product and service quality in the current competitive business environment. This tool has proven to be effective because it emphasises the need to align task requirements with the skills and experience of employees. It promotes the practice of continuous improvement both in private and public entities. As shown in the discussion, an organisation can achieve such levels of improvement by conducting regular analysis of the current methods with the aim of identifying potential weaknesses and then formulating ways of addressing them. Every time a milestone is made, a new one should be set based on the realities that a company faces. When applied appropriately, lean project management helps in lowering the overall cost of operation, enhancing efficiency in a project, and ensuring that activities are completed within the schedule.
The study shows that despite the obvious benefits of lean project management, its implementation is sometimes affected by some challenges. The main challenge that was identified as the limited knowledge that some stakeholders have in terms of its implementation. Lean operations require managers to allocate tasks to employees based on their capabilities to avoid mistakes in the implementation process. It also encourages continuous improvement in operation. However, some managers end up making unrealistic demands from their employees, believing it is the best way of achieving efficiency. They fail to understand the underpinning principles and primary pillars of this concept. The study strongly recommends improved awareness creation about this concept as a way of ensuring that its implementation does not face challenges. Those in management positions need to understand what it takes to operate in a lean system. Empowering employees through regular training is another important way of enhancing the application of this concept. It helps in ensuring that workers have the capacity to undertake roles assigned to them. The more changes emerge in the market, the more the training should be maintained. It is also critical to create and maintain an effective communication system within a firm that can support its implementation.
References
Baldwin, M. (2019). The BIM-manager: A practical guide for BIM project management. Beuth Verlag.
Bertrand, I., & Hughes, P. (2017). Media research methods: Audiences, institutions, texts. Palgrave.
Dahl, J. (2020). Leading lean: Ensuring success and developing a framework for leadership. O’Reilly Media.
Davidson, J. (2019). Everyday project management. Berrett-Koehler Publishers.
Englund, R., & Bucero, A. (2019). The complete project manager: Integrating people, organizational, and technical skills. Berrett-Koehler Publishers.
Heldman, K. (2018). PMP: Project management professional exam deluxe study guide. Wiley & Sons.
Hunt, J. A. (2018). PMI-ACP project management institute agile certified practitioner exam study guide. Wiley.
Kerpchar, J., Protzman, C., & Mayzell, G. (2015). Leveraging lean in the emergency department: Creating a cost effective standardized, high-quality, patient-focused operation. CRC Press.
Kerzner, H. (2018). Project management best practices: Achieving global excellence. Wiley.
Kerzner, H. (2019). Innovation project management. John Wiley & Sons.
Kim, Y. (2017). Activity based costing for construction companies. Wiley Blackwell.
Klugman, C., & Lamb, G. (2019). Research methods in health humanities. Oxford University Press.
Kumar, P., & Basu, C. (2017). A handbook for construction project planning and scheduling. Copal Publishing Group.
Modi, J. (2017). Essentials of operations management. PHI Learning Private Limited.
Nunkoo, R. (Ed.). (2018). Handbook of research methods for tourism and hospitality management. Edward Elgar Publishing.
Oakland, J., & Marosszeky, M. (2017). Total construction management: Lean quality in construction project delivery. Routledge.
Oke, A., & Aigbavboa, C. (2017). Sustainable value management for construction projects. Springer.
Philippopoulos-Mihalopoulos, A. (Eds.). (2017). Research methods in environmental law: A handbook. Edward Elgar Publishing Limited.
Riis, J. (2017). Project management: A multi-perspective leadership framework. Emerald Publishing Limited.
Rosenfield, J. (2017). Lean game development: Apply lean frameworks to the process of game development. Apress.
Salah, S., & Rahim, A. (2018). An integrated company-wide management system: Combining lean six sigma with process improvement. Springer.
Schaufelberger, J., & Holm, L. (2017). Management of construction projects: A constructor’s perspective. Routledge.
Sirakaya-Turk, E., Uysal, M., Hammitt, W., & Vaske, J. (Eds.). (2017). Research methods for leisure, recreation and tourism. CABI.
Stark, J. (Ed.). (2019). Product lifecycle management: the case studies. Springer.
Trueman, L. (2016). Research methods for the biosciences. Oxford University Press.
Voehl, F., & Harrington, J. (2016). Change management: Manage the change or it will manage you. CRC Press.
Westland, J. (2018). Project management: history of project management. Project Manager. Web.
Womack, J., Jones, D., & Roos, D. (1990). The machine that changed the world. Macmillan.
Wysocki, R. (2019). Effective project management: Traditional, agile, extreme. John Wiley & Sons.
Yang, L., Hsu, K., Baughman, B., Godfrey, D., Medina, F., Menon, M., & Wiener, S. (2017). Additive manufacturing of metals: The technology, materials, design and production. Springer International Publishing.