Introduction
Marks Dairy Industry is a company that deals in the collection and pasteurizing of milk and processing milk products that are later sold to the market in the form of pasteurized milk, butters, and cream. However, the management has realised that the processes are experiencing significant problems in delays and wastages that occur because of the problems with the logical organisation of teams and the management hierarchy.
Stevenson and Hojati (2007) maintain that the management intends to adapt the concept of lean management to identify the problems and improve the processes to achieve the benefits of lean management by reducing lead time, increase the efficiency of the teams, and reduce inventories and other benefit that might arise.
The lean management concept has its foundation on the lean manufacturing philosophy that was introduced in 1990 by the Japanese in the Toyota Processing Systems (TPS) to optimise manufacturing resources and reduce waste. The concept of lean management is one of the areas of production management that Marks Dairy Industry intends to adapt into its systems that many firms have widely adopted in running the production processes in the hope of reducing waste.
Womack and Jones (2010) argue that by continuously improving the quality of products to increase efficiency and effectiveness increases value, creates effective value stream processes, and optimises inventory and resource investments. Sacks and Goldin (2007) add to the concept of lean management as enabling effective time and space utilization, and increases perfection using less people in the transformation processes of production or service delivery to meet and even exceed customer needs and expectations (Martinez & Ioannou 1999).
To address the issues facing Marks Dairy Industry in its operations, the study will focus on the theoretical background on lean management and the applications of the lean management concepts, analyse the current state of Marks Dairy Industry operations, and make recommendations on the adoption of lean management concepts into the production processes of the company.
Theoretical background
Cox and Schleier (2010) argue that the theories proposed to explain the concept of lean management derive the fundamental existence on the principles of the lean thinking methodologies that firms adapt to maintain and sustain competiveness in accordance with the emerging and dynamic market requirements.
Salem, Solomon, Genaidy and Minkarah (2006) presents varying views and theories that provide different explanations on lean management from different perspectives based on the views that lean management is a tool to achieve organisational objectives based on the philosophy of reducing inputs and increasing outputs. Salem et al. (2006) contends that some academicians define lean management in the context of constraints in lean production environments.
Cox and Schleier (2010) argue that the consistence of the theory with lean management is to determine where the limiting factors or constraints of production lie that impedes the efficient execution of processes to be systematically removed to allow for the efficient and effective execution of tasks without incurring wastes based on science of logic.
Cox and Schleier (2010 agree with Salem et al. (2006) with the idea that the constraints theory points out a framework for organisations to adapt to enable the management provide leadership and direction for achieving lean production by identifying where the constraints lie in the production processes.
The constraints enable the management to achieve efficient synchronization of the processes to improve the performance of the system by repeating the process to be more efficient and effective. According to Salem et al. (2006), the underpinning successful use of the theory is to identify the need for change and what should be changed, and what strategy to put in place to make the change.
In summary, the theoretical foundation of lean management is focused on quality control to ensure that the cost of production is kept to a minimum. Lean management also depends on the foundation of the manufacturing quality processes and product quality, a fully integrated lean framework, a continually evolving quality improvement process, continuous improvements, and consistency in lean management approaches (Miller, Packham & Thomas 2002).
The components of lean management
Slack, Chambers and Johnston (2010) support the argument by Womack and Jones (2010) that lean management can only be an effective tool if implemented gradually within the operations of a firm if the management wishes to achieve value and reduce or completely do away with waste.
An outline of the lean management process by Stevenson and Hojati (2007) maintains that the following tools are appropriate for the management to use to implement the lean management system:
- Deployment of cross functional teams
- Continuous improvements
- Learning
- Value stream mapping
- Employee involvements
- Benchmarking
Cross functional teams
Cross functional teams play a significant role in the implementation of lean management strategies to achieve the organisational objectives of creating value and reducing or doing away with waste (Yang, Hong & Modi 2011).
Slack, Chambers and Johnston (2010) evaluated the lean management model by Sacks and Goldin (2007) and concluded that the strategic approach of using cross functional teams is for the management to provide leadership that enables the organisation to operate as a flat structure with all its teams under the direction of the vision statement that is created by the leadership.
However, Liker and Convis (2011) contend that those organisations that work on hierarchical structures suffer from the functional silo syndrome and the bureaucratic effects of power concentrations on one manager who is charged with the responsibility of coordinating all the functions of a firm.
The management approach in such a situation does not factor the interdependence and relationship among the functional units and the result show that the organisation can be made to act unintelligibly. However, integrating the concept of lean management enables the management to adopt strategic plans that lead organisation to reap the benefits of lean management through the use of cross functional team (Anderson & Anderson, 2010).
Here, bureaucracy is no longer the impeding element because the manager enables the teams to relate and regulate the minute details in each production process making them to function efficiently (Leffingwell 2010). Here, the role of the manager is to identify areas that need teams to communicate and cooperate on processing issues by making powerful decisions that override departmental decisions.
Here, the element of success is the main area of focus and is achieved through teams which work by developing waste and value management policies that are implemented to achieve the strategic goals and observes of the organisation.
Continuous improvement
A distinct difference exists between lean management and the six sigma steps of quality management (Salah, Rahim & Carretero 2010). Here, the six sigma steps of total quality management identify continuous improvement to be one of the critical success factors for an organisation to achieve quality using statistical tools that are not used for lean management (Akkerman, Farahani & Grunow 2010).
However, a critical analysis of the lean management function shows that continuous improvement is a component that can be used to inform the study from different areas of operations management including lean manufacturing.
Liker and Convis (2011) maintain that continuous improvements can be achieved when the manager is able to identify opportunities in the process workflow, develop a plan on how the processes can be improved, implement the new changes, and review the effectiveness of the changes. Continuous improvement enables the management to be able to identify areas of waste and to reduce and remove waste from the workflow processes to increase value and avoid sacrificing quality.
Leffingwell (2010) argues that teamwork is important because once opportunities have been identified and mapped out by the manager, the team becomes responsible for deciding on what to implement and what not to. However, Leffingwell (2010) contends that the manager and the team must work collaboratively together within the organisational culture to create an environment that factors efficiency and effectiveness in the production processes.
Learning
Applying lean management in the workflow production processes enables an organisation to identify the key strengths and weaknesses that exist within the company to acquire new abilities and competencies (Decuyper, Dochy & Van den Bossche 2010). The importance of learning is to enable the company to conduct internal and external benchmarking against the competing firms.
It has been established that Decuyper, Dochy and Van den Bossche (2010) argue that learning be done by embracing new mental models, ability of the management to discover the root causes of wastes and effects, and the use of knowledge to assure sustainable competitive advantage for a firm. Here, learning entails looking seeking for new ideas, being innovative, and seeking to know why and how things happen and should be done to remove waste and focus on value (Peters, Johnston, Pressey & Kendrick, 2010).
Values stream mapping
Lean management becomes complete when a firm is able to identify where waste lies in the production processes, in the context of this study. Value stream mapping consists of identifying areas where waste is incurred to stream line the processes and remove waste (Chen & Meng 2010).
The core elements that define value stream mapping include an analysis of the production processes, the waiting time for each task to be executed, identification of areas where waste occurs, determining the requirements that could be met to remove waste, removing from the system the elements that lead to waste, putting into action the lean state for process optimisation, and evaluating the lean state for effectiveness and efficiency (Chen & Meng 2010).
Employee involvement
To ensure sustainable competitive advantage, firms operate in a way that involves employees in decision making. Employee involvement spans administrative decisions, operational issues and conditions, and other issues that might arise and impede their performance for removal (Carmeli, Reiter-Palmon & Ziv 2010). Here, the company is able to capture new and innovative ideas and contributions for the success of the company.
Benchmarking
Benchmarking is defined as the “practice of being humble to admit that someone else is better at something and being wise enough to learn how to match and even surpass them all” (Rushton 2010, p.11). The concept has been applied in many organisations wanting to gain sustained competitive advantage by achieving improvements by determining how an organisation performs its production processes and comparing them with companies that have been successful in the performance of their operations.
Academic literature emphasizes that the positive benefits of benchmarking include effectiveness in business planning, policy formulation and deployment, ability to solve business problems and enhance continuous improvements. Business planning is achieved by creating a vision, formulating strategic goals, and implementing short term and long term plans to achieve lean production.
Short term strategic goals usually last for 3 to 5 years (Brown, Bessant & Lamming, 2013). On the other hand, policy formulation is done at the top levels of management in collaboration with other teams within the firm. Here, the element of quality is the main point of focus when solving business problems that are identified within the organisational processes.
Continuous improvements are achieved through benchmarking to determine the extent process needs to be improved. Brown, Bessant and Lamming (2013) proposed the idea that success of the process is based on customer satisfaction and the change in the culture of doing things.
Here, culture change entails the manager with their teams evaluating themselves on whether they are doing the right things, searching for better ways of working, identifying the things to change, establishing the reason why things work differently, and asking the “what if?” question and seeking for answers to the question (Björklund 2010).
Benchmarking can either be internal or external and the processes are achieved by identifying improvement opportunities that can either be transferred, the rationale to invest in the processes, implementing training programs, and motivating team members to ensure success.
The next step is to develop objectives for improvement by being realistic, ambitious, and understandable and measurable. In addition, a gap analysis provides answers to the areas and opportunities to be exploited and implementing the required elements to achieve the targets (Adebanjo, Abbas & Mann 2010).
The gap analysis compares the competitor’s performance to one’s performance to identifying the gap to fill to become competitive. Researchers classify benchmarking into different categories which include strategic, process, internal, external, functional, performance or competitive and external benchmarking. However, in the context of this study, internal and external benchmarking will be the focus of the discussion (Adebanjo, Abbas & Mann 2010).
Internal Benchmarking
Internal benchmarking involves evaluating the effectiveness of different functional units within and organisations and establishing proficient and good practices within the organisation (Soni & Kodali 2010). The strategy enables easy access to data that could be used for lean management.
External Benchmarking
On the other hand, external benchmarking compares different functions of the organisations with good practices to ensure effectiveness and efficiency in production processes, a component that is lacking in the systems of Marks Dairy Industry (Soni & Kodali 2010). Here, differentiation and leadership are some of the components to benchmark within the organisation.
Lean management in the contemporary society
Different authors discuss the concept of lean management from different perspectives with some authors viewing lean management from the management approach when applied in the contemporary environment. Soni and Kodali (2010) argue that management is a tool that is used to reduce management hierarchies in an organisation leading to a flat organisation to create a leaner structure and optimal utilization of resources such as the people working within the organisation.
Salem et al. (2006) contend the views of other academicians by arguing that lean management as a process optimisation and customer oriented management approach for effective engagement and leadership of employees to work towards achieving organisational goals and objectives.
In each of the perspective of lean management, the authors agree that lean management includes value addition and waste removal from the systems that process lean inputs into outputs (Womack & Jones 2010). In the contemporary environment, lean management is applied as a tool to improve the production processes and increase the quality of the resulting products and often increase the price, increasing an organisation’s profits.
Toyota
Monden (2011) points out Toyota’s Production systems (TPS) to be the typical examples of the application of lean management in the context of lean manufacturing. Here, the company took the first step to implement the waste reduction systems by demonstrating that quality was not costly to implement in the production processes.
The success in the TPS demonstrated to the world that integrating the concept of lean management could lead to a reduction in the overall manufacturing costs, manufacturing cycle time, and maintain high quality standards. Here, it was established that anything that contributed to the increase in consumption of resources in the Toyota manufacturing process was identified as a waste (Monden 2011).
Different areas were noted to be the cause of waste in the TPS and include the manufacture of defective components, poor inspection, poor transportation logistics, undesirable inventory management practices, regular or continuous employee change overs, overproduction of component when not needed, and frequent movements within the manufacturing plants.
When Toyota identified the areas of waste and removed them by creating efficient transportation patterns, optimal production and inventory levels, improvements of the work pattern movements, and properly regulated change over plans, the organisation became a success (Karlsson 2010).
Lean management and lean production
Here the core elements that make lean production effective are mirrored in the implementation of the concept of lean management into the production processes. Here a company has to set up a lean production systems under a lean management process to guide the long term implementation strategy before the new system is fully implemented. Shah and Ward (2007) argue that the second phase is crucial because it requires a complete overhaul of the management structure and changes in physical procedures that often attract a lot of conflicts and upheavals for the management to address.
The core elements that are put into consideration include a focus on customer satisfaction by providing zero defect free quality products at the right time and in the right quantity, provide the leadership that creates the vision for the organisation and directs the organisation towards the vision, use of team based operations, establishment of long term relationships with external entities, and the management of the information using visual control systems (Corbett & Kleindorfer 2003).
In addition, lean management encourages a harmonious culture, enables skilled manpower to maintain production facilities, and organizes workers to perform their tasks using a team based approach. Lean management enables managers to implement the cross functional work approach that enables teams to work as cooperating entities that accommodate the vertical and horizontal collaborations.
Using the concept of lean management, many organisations have realigned their production processes by working in teams under a leadership driven by quality, team building, team work, and team play leadership approaches (Chalice 2007).
Analysis of Marks Dairy Industry operations
Marks Dairy Industry operations revealed the main problem to be the long lead times experienced at the firm. The current map of the operations at the firm indicates the processes and time required to perform each of the tasks in the milk production processes. The map shows that reception are as 9 people working to collect milk and each person takes 45 minutes cycle time to complete process.
The milk pasteurization process takes 60 minutes to complete with 2 people employed to do the work. The butter machine has 2 people working on it and takes 60 minutes to complete each task while the butter packing machine takes 100 minutes employing 5 people and the trolley filler takes 20 minutes to complete and employs 9 people.
The last task in the process is storage and delivery which takes 120 minutes and employs 4 people to work in the section.
Table 1 Summary of the map of the cycle time
When a values stream mapping was conducted to determine the total time taken on the tasks, the total cycle time for each of the activities were summarised in table 1 above.
Waste areas
Table 2 waste checklist
The areas identified to be the cause of waste lack of include teamwork, benchmarking, continuous improvements, learning, administration, plant layout, staff, and frequent wastes and damages. On the other hand, the company shows that the management is keen on identifying new technologies and physical faults.
Suggested areas of improvement:
- Teamwork
- Internal and external benchmarking
- Continuous improvements
- Administration
- Plant layout
- Staff
- Wastages and damages
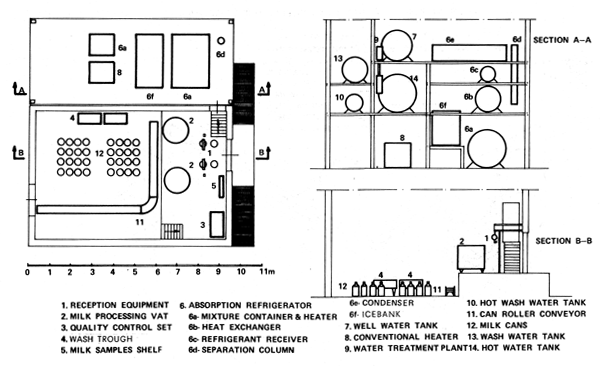
Figure 1: Current milk processing layout plant
Wastes occur in the layout at the reception, milk processing, and at the wash troughs. Lack of value stream mapping is evident because of the poor flow of milk through the plant involving the customers and the workers. In addition, the plant consists of two separate processing facilities that consume more time because of the movements from one section to the other (Chalice 2007).
Improvement on Marks Dairy Industry operations
An administration structure should be implemented to coordinate the lean management functions and the people to work as a team. In addition, a benchmarking framework should be implemented to compare the firm with other successful firms to enable them improve the milk production processes to reduce waste through continuous improvements.
Continuous improvements should be in the areas of plant layout to improve the milk processing steps through continuous learning from external sources.
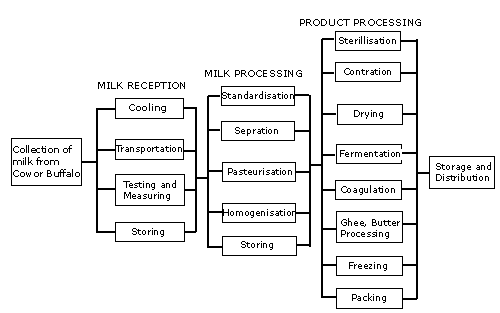
Figure 2: suggested improvements
Figure 2 above shows the suggested layout that optimises the collection, reception, processing, and product processing by differentiating the processes into their respective functions (Koskela, Huovila & Leinonen 2002).
Value is created by following the steps shown into specific compartments based and waste is eliminated in each because specific resource optimising functions are done at each step before the next step starts (Hajmohammad, Vachon, Klassen & Gavronski 2013). According to Hajmohammad et al. (2013), all the pre-requisite processes to the next step are done systematically to avoid waste and increase value as shown in figure 2 above.
Conclusion
In conclusion, the concept of lean management is important when implemented in production systems to remove and increase value of the processes and products within a system. The Marks Dairy Industry’s processes for the pasteurization of milk and production of other products from milk suffer administrative, team, and plant layout problems that increase product lifecycles time leading to long delays.
However, with the introduction and implementation of the lean management concepts into the production to enable the company identify areas of constraints where waste occurs, the results could lead to removal of waste and value addition into the production processes.
References
Anderson, D & Anderson, L A 2010, Beyond change management: How to achieve breakthrough results through conscious change leadership, John Wiley & Sons, New York.
Adebanjo, D, Abbas, A. & Mann, R 2010, ‘An investigation of the adoption and implementation of benchmarking’, International Journal of Operations & Production Management, vol. 11, no. 30, pp. 1140-1169.
Akkerman, R, Farahani, P & Grunow, M 2010, ‘Quality, safety and sustainability in food distribution: a review of quantitative operations management approaches and challenges’, Or Spectrum, vol. 4, no. 32, pp. 863-904.
Björklund, M 2010, ‘Benchmarking tool for improved corporate social responsibility in purchasing’, Benchmarking: An International Journal, vol. 3, pp. 17, pp. 340-362.
Brown, S, Bessant, J R & Lamming, R 2013, Strategic operations management. Routledge, London.
Carmeli, A, Reiter-Palmon, R & Ziv, E 2010, ‘Inclusive leadership and employee involvement in creative tasks in the workplace: The mediating role of psychological safety’, Creativity Research Journal, vol. 3, no. 22, pp. 250-260.
Chalice, R 2007, Improving healthcare using Toyota lean production methods: 46 steps for improvement, ASQ Quality Press, New York.
Chen, L & Meng, B 2010, ‘The application of value stream mapping based lean production system’, International Journal of Business and Management, vol. 6, no. 5, pp. 203.
Corbett, C J & Kleindorfer, P R 2003,’ Environmental management and operations management: introduction to the third special issue’, Production and Operations Management, vol. 3, no. 2, pp. 287-289.
Cox, J F & Schleier, J G 2010, Theory of constraints handbook, McGraw-Hill, New York.
Decuyper, S, Dochy, F & Van den Bossche, P 2010, ‘Grasping the dynamic complexity of team learning: An integrative model for effective team learning in organisations’, Educational Research Review, vol. 2, no. 5, pp111-133.
Hajmohammad, S, Vachon, S, Klassen, R D & Gavronski, I 2013, ‘Lean management and supply management: their role in green practices and performance’, Journal of Cleaner Production, vol. 1, no. 39, pp. 312-320.
Karlsson, C 2010, Researching operations management, Routledge, London.
Koskela, L, Huovila, P & Leinonen, J 2002, ‘Design management in building construction: from theory to practice’, Journal of Construction Research, vol. 3, no. 3, pp. 1-16.
Leffingwell, D 2010, Agile software requirements: lean requirements practices for teams, programs, and the enterprise, Addison-Wesley Professional, New York.
Liker, J & Convis, G L 2011, The Toyota Way To Lean Leadership: Achieving And Sustaining Excellence Through Leadership Development , CRC Press, London
Martinez, J C & Ioannou, P G 1999, ‘General-purpose systems for effective construction simulation’, Journal of construction engineering and management, vol. 4, no. 125, pp. 265-276.
Miller, C. J, Packham, G A & Thomas, B C 2002, ‘Harmonization between main contractors and subcontractors: a prerequisite for lean construction?’, Journal of Construction Research, vol. 1, no. 3, pp. 67-82
Monden, Y 2011, Toyota production system: an integrated approach to just-in-time. CRC Press, London
Peters, L D, Johnston, W J, Pressey, A D & Kendrick, T 2010, ‘Collaboration and collective learning: networks as learning organisations’, Journal of Business & Industrial Marketing, vol. 6, no. 25, pp. 478-484.
Rushton, A 2010, The handbook of logistics and distribution management. Kogan Page Publishers, New York
Sacks, R & Goldin, M 2007, ‘Lean management model for construction of high-rise apartment buildings’, Journal of construction engineering and Management, vol. 5, no. 133, pp. 374-384.
Salah, S, Rahim, A & Carretero, J A 2010, ‘The integration of Six Sigma and lean management’, International Journal of Lean Six Sigma, vol. 3, no. 1, pp. 249
Salem, O, Solomon, J, Genaidy, A & Minkarah, I 2006, ‘Lean construction: from theory to implementation’, Journal of management in engineering, vol. 4, no. 22, pp. 168-175.
Shah, R & Ward, P T 2007, ‘Defining and developing measures of lean production’, Journal of operations management, vol. 4, no. 25, pp. 785-805.
Slack, N, Chambers, S & Johnston, R 2010, Operations management, Pearson Education, New York.
Stevenson, WJ & Hojati, M 2007, Operations management, McGraw-Hill/Irwin, Boston.
Soni, G & Kodali, R 2010, ‘Internal benchmarking for assessment of supply chain performance’, Benchmarking: An International Journal, vol. 1, no. 17, pp.44-76.
Womack, J P & Jones, D T 2010, Lean thinking: banish waste and create wealth in your corporation. Simon and Schuster, London.
Yang, M GM, Hong, P & Modi, S B 2011, ‘Impact of lean manufacturing and environmental management on business performance: An empirical study of manufacturing firms’, International Journal of Production Economics, vol. 2, no. 129, pp. 251-261.