Introduction
Carbon fiber consists of fiber of about 5 to 10 μm in diameter made of mostly carbon atoms. Carbon fiber is made from mainly Precursor and other materials. Polyacrylonite constitutes 90% of the carbon fiber produced while 10% is from rayon or petroleum pitch (Kroschwitz, Jacqueline & Howe-Grant, 1993). In some cases polyacrylonite is mad from ammonia. The carbon content of carbon fibers is between 93% and 95%.
About 50% of the world’s carbon fiber is produced in Japan and more than 60% used in the United States. Toray Industries in Japan is the biggest producer of carbon fiber. In the United States, Zoltek is the company that produces carbon fiber and its products in largest quantities.
Production process of carbon fibers, expose workers to health risk. Processing of carbon fibers sometimes result in wearing off forming dust particles. The carbon fiber dust pollutes the air and may cause the quality of surrounding air to be poor. It becomes dangerous when the concentration of para-aramid fibrils is high in the air. These particles irritate the skin when exposed and come in contact with it. When sizing is being done, the materials used for coating fibers may cause severe reaction on the skin of the workers because of the chemical content.
Machinery, Labor, and Infrastructure for Producing Carbon Fiber
Production of carbon fiber has been highly mechanized over the years. Currently production process is done using robots because of the temperatures and chemicals involved in the processes. Recently, only machine operators have worked in the factories which process carbon fiber and so the labor cost has been relatively reduced (Brady, George, Clauser, & Vaccari 2007).
Carbon fiber is manufactured through combination of chemical and mechanical processes. The following are major steps involved in processing of Carbon fiber. Spinning-Polyacrylonile plastic polymer is mixed with certain chemicals in large containers and heated in the presence of some catalyst to form a molten viscous liquid. The molten solution is then pumped into a chemical bath (to form a polymer jet). This occurs in specially made jets.
Carbon fibers are formed through solidification process. Spinning of the solution results in the formation of atomic structure of carbon. To achieve this at optimum levels highly instrumented machines are used to enable multi-component melt-spun precursor fibers.
- Stabilizing. The Carbon fibers are heated in presence of air to rearrange molecules bonding. This process transforms the linear polymer to a ladder structure which makes the polymer thermally stable. This is done by heating carbon fiber in air to about 200-300℃ for between 30 to 120 minutes.
- Carbonization. Since spun fibers will burn if brought to high temperature, oxygen free (Argon atmosphere) furnace is used to heat to a temperature of between 1000℃ and 3000℃ for some minutes. Heating the fibers makes the atoms to vibrate until nitrogen and other non carbon atoms are removed from the fibers. This process results in formation of long chains of carbon atoms (Figure 1). The atoms are intertwined in the chain.
- Treating the surface. Carbonization leaves the surface which does not bond well with matrix resins. Anodic oxidation in an aqueous bath provides a rapid process for rendering the carbon fiber bondable to matrix such as epoxies.
- Sizing. After surface treatment, the fibers are dried and passed through an aqueous bath to be coated with a sizing material. Coating of the fibers after surface treatment protects them from damage during its use. The sizing material should be soluble in water. The bundle is then dried and finally the tows are wounded on bobbins and packed ready for delivery (Bahl, et al 1979).
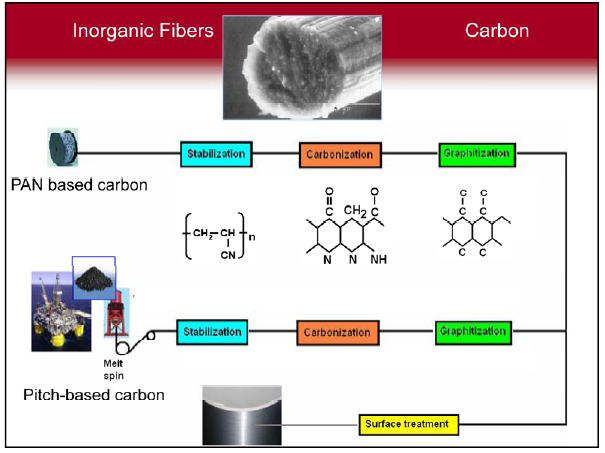
Cost Related to Alternative Materials
The cost of producing carbon fiber is high because of the mechanized processes shown above. The facility used in carbon fiber production should be highly instrumented to enable wide range of parametric controls for temperature and fiber drawing. The need for specialized fiber for wider range of use makes it more expensive. The cost of processing carbon fiber is high compared to other competing materials like fiber glass.
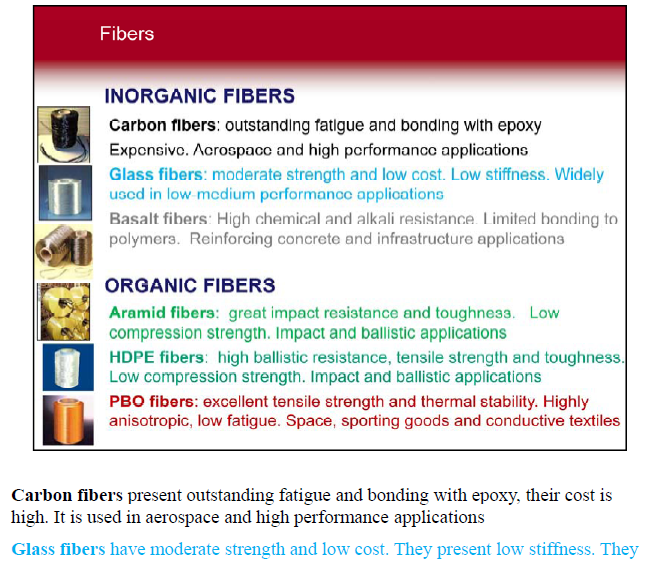
However, the cost is saved during operation of the final product due to its light weight. Carbon fibers are used in engineering situation which require high performance. Planes, cars, boats, wind mills, etc. (Figure 3) made from carbon fiber are lighter and save fuel during its use. The end product is lighter than most materials that are used for same purposes like fiber glass and metal. This has made distribution of carbon easier and cheaper than the other materials.
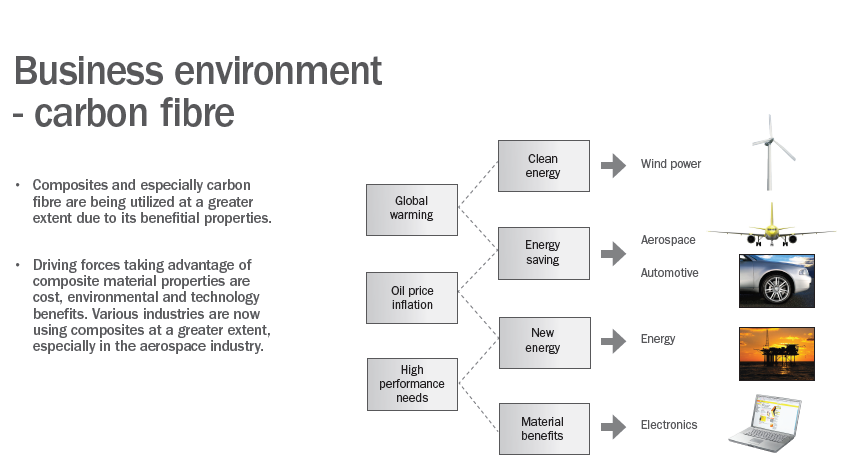
Environmental Concerns for Recycling Carbon Fiber
Recycling fiber carbon rather than dumping in land-fills reduces the amount of carbon sequenced in the landfill. Recycling carbon fiber reduces the quantities going to end life each year than it would have been without recycling (Miner & Garcia 2007). End of life incineration of carbon fiber results in carbon credits and energy recovery.
Recycling of carbon fiber is not easy as compared to other competing materials like steel which is easily recycled. Recycled carbon fiber is also weaker than original material. The recycled materials are used in applications that do not require full strength of carbon fiber like manufacture of consumer electronics like personal computers and laptops.
Environmental Concerns for Using Carbon Fiber
Even though carbon fiber is used to make materials with a high strength-to-weight ratio, it lack fatigue endurance limit. Failure can happen especially after a high number of stress cycles when used in civil works. This has forces engineers to use exaggerated safety factors when designing equipment to be made using carbon fiber. This provides component reliability over a long time.
Dust particles of carbon fiber have adverse health effects when inhaled. The effect is not immediately detected in the victims. These dust particles have long term effects more or less the same as those portrayed by persons who inhale asbestos particles. After long time, a person who inhale dust particles will eventually developed health complications related to respiratory system. The carbon fibers have carcinogenic effect when come in contact with soft body tissue.
Automobile, airplanes and other machinery made from carbon fibers, uses less energy (fuel), hence reduce environmental pollution from combustion.
Works Cited
Bahl, O.P. et al., “Recent Advances in Carbon Fiber technology”, J. of Scientific and Industrial Research, 38: Oct. 1977: 537-554. Print
Brady, George S., Clauser,H.R. and Vaccari J.A.. “Materials Handbook”. McGraw-Hill, 1997. Print
Kroschwitz, Jacqueline I. & Howe-Grant, M. Encyclopedia of Chemical Technology. Ed. John Wiley and Sons, Inc., 1993. Print
Miner, R. and Perez-Garcia, J.The greenhouse gas and carbon profile of the global forest products industry. Forest Products Journal 57: 2007: 80-90. Print
SACMA Releases “Carbon Fiber Industry Statistics”, Composites News, No. 1, 1998, Print