Opening
3-D printing is an efficient and essential tool for engineers, doctors, product designers, and entrepreneurs. 3-D printing is mostly used for prototyping, create broken parts, etc. The applicability of 3-D printing is incredibly vast; it can even produce medical implants. The technology of 3-D printing defines future progress since prototypes are generated faster and last as much as the actual object does.
This technology is based on Additive Manufacturing (AM), and its operations depend on the computer directing the 3-D printer to add every new layer continually as a precise cross-section of the final object. Additive manufacturing uses Fused Filament Fabrication (FFF), which uses the thermoplastics that turn into semi-liquid form at specific temperatures and solid on cooling down (Barnatt 2). The melted thermoplastic is precisely positioned layer upon layer while moving on a three-dimensional axis (Kim and Robb 19). The trends of 3-D printing are rising and will continue growing according to data obtained by the Google insight graph by 2015. 3-D printing is an innovation most people are interested in trying according to the statistics.
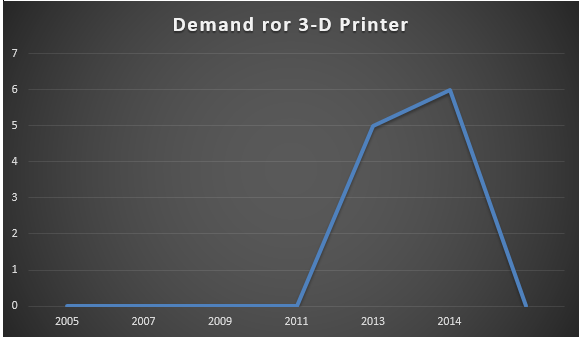
The popularity of the new invention has risen sharply since its benefits became obvious to the target audience. Because of the opportunities, which it offers in construction, the device can be considered a major breakthrough.
The Benefits of a 3-D printer in construction
- 3-D printing makes the construction process faster and more accurate. The advantages are mainly attributed to the fact that the human factor is eliminated in modeling (Husseini para. 3). Since machine production is involved, the element of approximations is resolved, and only exact values are given during the modeling of objects.
- Human labor is reduced mainly because the 3-D printing technology eliminates the need for manual architectural designs and manual prototype construction (Husseini para. 4). The actual architectural models of a building are built with the help of computer programs feeding the results to a 3-D printer. The printer carefully generates a sample of the building as directed, thus, making a prototype.
- Waste production is reduced with the use of 3-D printers (Husseini para. 3). The content that is produced by the printer is always accurate, and any miscalculations always lead to recycling the thermoplastic materials that were used in the process.
- 3-D printing helps reduce both health and safety risks involved (Husseini para. 2). 3-D printing replaces heavy-duty work and dangerous jobs on the site during construction. Tasks such as wall structures are replaced by three printers preventing the possibility of the walls collapsing on the masons (MoorefieId-Lang 70).
- 3-D printing defies the use of traditional forms of construction. The printing technology can help overcome challenges once it incorporates the architect’s and owner’s design. Traditionally flat walls had to be joined at ninety-degree angles because alternate models seemed impossible. 3-D printers can remove this obstacle enabling architects and owners to build buildings with more curves.
- The cost of development is reduced. 3-D printing will remove the need for extra labor force required in the construction industry and the need to buy manufactured materials since 3-D printers can produce them for their owners.
- Quality of development is increased with the use of 3-D printers. Most of the building errors are eliminated due to the high accuracy of a 3-D printer. The destruction of buildings due to human error is removed since the printer cannot make simple errors that humans make during the design of a building unless when it malfunctions. All those involved are immediately relieved of their guilt, and the existence of any lawsuit occurring is minimized, all thanks to the use of a 3-D printer in construction.
- The standards of development are increased because of the quality increase. If most of the companies embrace 3-D printing, what seemed impossible in construction is made possible due to the flexibility of the 3-D printer. The model graph clearly shows the rise in quality of building because of a 3-D printing application.
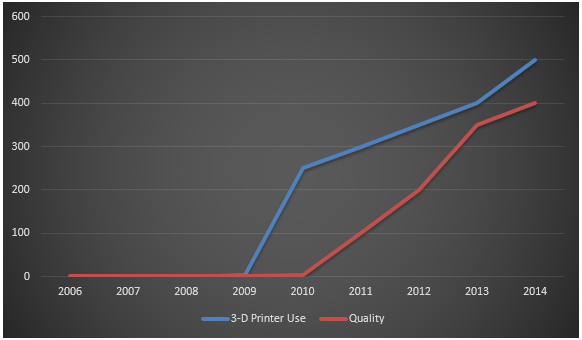
The Risks of a 3-D printer
- A reduction in the number of workers in the construction industry is expected. Removing studs, sidings, and drywalls from the process of building reduces the total number of people needed on the ground. The reduction of jobs leads to unemployment in the long run increasing the crime rates in the region.
- Allocating risks becomes difficult when 3-D printing is involved. When a problem occurs, it is hard to find who will take the blame. One risk to consider includes the contractual warranties. Example is the material and equipment that are to be furnished will be of perfect quality and new unless otherwise. The second case is that work will be free from mistakes and be of standard quality. The third example is that work will be completed according with the set requirements of the contract (Gibbs para. 2).
- With the emergence of 3-D printing copyrights, infringement is a significant issue since duplications of designs and structures will occur. There will be a major challenge for some companies copying other companies’ development models; all these have been made easier and faster because of the emergence of 3-D printers (Griffey 8).
- If most companies embrace 3-D printers, the construction industry will be flooded, and the price of houses in the market will drop significantly. With the construction being made easier by the printer, many companies will emerge and increase the competition in the construction industry (What Material Should I Use For 3D Printing? – Advanced Materials Review #1 – BendLay, Laywoo-D3 and LayBrick para. 3.).
Closing
Since 3-D printing is getting increasingly popular, the company investing in it will save a lot of money. 3-D printing benefits according to my opinion outweigh the risks, embracing it will prepare the company for any evolutions that are to occur in the future. A competitive edge over other building companies is expected since the jobs will be efficient and more reliable. At the rate, in which technology is going, we will soon come to print not only buildings but entire urban sections (Lipson and Kurman 53).
The price of a 3-D printer might be very high, but it is worth the cost considering the large amount of profit it would give to the company. If there is an investment worth, the risk is 3-D printing. The company making a first move will have the benefit of first mover effect in the construction industry. It will have already won the trust of its customers, and it will already be firmly rooted in the business before other companies start embracing it.
Before considering this emerging cutting edge technology as a development method, one should reflect on how it changes the exposures to danger and do some enquiry from a knowledgeable and trustworthy counsel and insurance level. The graph below shows that 3-D is in its early stages of adoption by many companies. In the next five years, the use of 3-D printers will increase significantly reaching its tipping point.
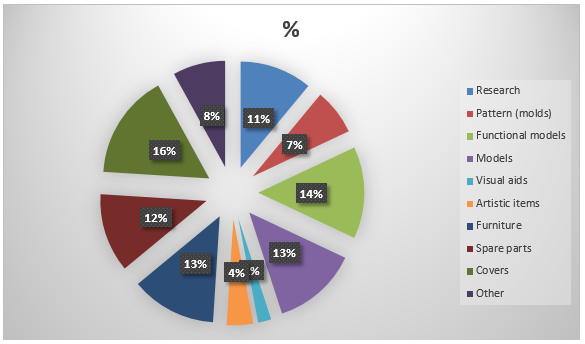
Works Cited
Barnatt, Christopher. 3D Printing: The Next Industrial Revolution. New York: ExplainingTheFuture.com, 2013. Print.
Gibbs, Samuel. “Metal 3D Printing and Six Key Shifts in the Second Industrial Revolution.” The Guardian. 2014. Web.
Griffey, Jason. ” The Types of 3-D Printing.” Library Technology Reports 50.5 (2014): 8-12. Print.
Husseini, Adam. “3D Printing and the Construction Industry.” Building Technologies 2014. Web.
Kim, Julie and David Robb. “3-D Printing: A Revolution in the Making.” University of Auckland Business Review 17.1 (2014), 16–25.
Lipson,Hod and Melba Kurman. Fabricated: The New World of 3D Printing. Indianapolis, IN: John Wiley and Sons, Inc., 2013. Print.
MoorefieId-Lang, Heather. ” 3-D Printing in Your Libraries and Classrooms.” Knowledge Quest 43.1 (2015), 70–72 Print.
What Material Should I Use For 3D Printing? – Advanced Materials Review #1 – BendLay, Laywoo-D3 and LayBrick. 2015. Web.