Introduction
The layout design requires in-depth decision-making based on various factors which with affect production efficiency. Although creating plant layouts has been performed by manufacturing and industrial engineers for decades, no one set formula or method ensures the best outcome achievement. Many manufacturing companies are striving to adopt lean production techniques that eliminate waste through an enhanced flow of products within their production facilities (Heize & Render, 2008: 23). Tools utilized to implement lean production techniques include kanban, supermarkets, first-in-first-out (FIFO) lanes, pacemaker processes, management time frames, etc (Shafer & Charnes, 1988).
Numerous companies are also implementing the theory of constraints (TOC), which is a management philosophy to meet customer demand through synchronized production, to enhance the flow of products, and hence generate money for the corporation at an expedited rate. TOC utilizes tools like drum-buffer-rope (DBR), throughput accounting, and constraint management to achieve this. Although companies are striving to implement lean manufacturing and TOC through the implementation of the above-mentioned tools, they miss out on implementing an optimized macro-flow in their facilities (Shafer & Charnes, 1988).
Macro-flow is the optimization of the entire flow within the facilities of a company, which allows them to avoid sub-optimization within narrow departments or functional areas. Lean manufacturing and TOC stress the importance of maintaining a consistent macro-flow within the entire manufacturing facility for products, to achieve the highest impact in improving the productivity and profitability of a manufacturing plant.
For creating the most optimum macro-flow within a facility, various flow models have been used by plant layout engineers. However, the way these layouts are created and implemented has a lot of subjectivity built into them (Sethi and Sethi, 1990: 291).
Management decisions regarding physical arrangement are often characterized by several questions. These include (Heize & Render, 2008: 28):
- What centers should the layout include?
- What is the space and capacity requirement?
- What’s the effective center configuration?
- Which are the best locations for individual centers?
The location of a center has two dimensions:
- Relative location: The placement of a center relative to other centers.
- Absolute location: The particular space that the center occupies within the facility.
The prime aspects form the basis for the formulation of strategic decisions which define the layout approach employed by a firm. The layouts choices help communicate an organization’s product plans and competitive priorities (Heize & Render, 2008: 56). Changing layouts can have significant effects on how well it meets its competitive priorities in the following ways:
- Increasing customer satisfaction and sales at a retail store.
- Facilitating the flow of materials and information.
- Increasing the efficient utilization of labor and equipment.
- Reducing hazards to workers.
- Improving employee morale.
- Improving communication.
This paper explores the possible benefits that are likely to be accrued by shifting from functional layout to cellular layout. Additionally, it discusses some of the dis-benefits that they may be incurred from such a shift. This provides insightful information that could help the company in deciding on whether or not to shift its production from functional to cellular.
Background information
Lean manufacturing is an operations management philosophy focused on reducing waste in a manufacturing system. Lean identifies many different types of waste, among them the waste of overproduction – making products and building inventories for which there is no current demand. Installing pull production control policies is an important part of implementing Lean manufacturing in high-volume, repetitive manufacturing systems? Production control policies, which dictate when manufacturing resources should work, affect important measures of manufacturing system performance, including cycle time and work-in-process inventory (Heize & Render, 2008: 63). Pull production control policies have been shown to improve manufacturing system performance by linking production control to customer demand (Johnson & Wemmerlov, 1996: 328).
However, transforming a system governed by a push to one controlled with pull has not been studied extensively. The different ways to transform a system, the behavior of a system during transformation, and the real-world costs of Lean transition have never been measured. As a result, risk-averse manufacturers have been slow to adopt Lean practices. Using simulation models of manufacturing systems, one can study the effects of different types of production control rules on performance metrics. One can also study the behavior of a system undergoing a Lean transition (Johnson & Wemmerlov, 1996: 331). In doing so, this research aims to shed light on the transformation process, giving would-be practitioner tools and techniques for Lean transition and realistic expectations of system performance during the transformation.
Cellular and functional systems are two alternate ways of organizing production. In recent times, many firms have migrated from a functional type production system to the cellular type to gain a competitive advantage (Johnson & Wemmerlov, 1996: 333). Several companies which have implemented cellular manufacturing (CM) claim that the new system results in reduced move time, setup time, and throughput time, and work-in-process inventory (Sethi and Sethi, 1990: 297).
Investigation of the performance superiority of a cellular system (CS) over a functional system (FS) has generated interest among the research community. Johnson & Wemmerlov as well as Agarwal & Sarkis, provide excellent reviews on the relative performance of CS and FS. Even though several research papers have appeared in the literature comparing the performance of CS with FS, the current findings cannot readily assist the practitioners in making specific choices between FS and CS (Wheatley, 2000: 11). Generally, no consensus exists as to whether CR is superior to FS about performance efficiency (Sethi and Sethi, 1990: 298). Thus there is a great need for research to generate insights on how an FS is structurally different from a CS and the performance implications of these differences in understanding the relative performance of the two systems. Some early studies (Webster. and Tyberghein, 1989: 31). Compare the performance of CS and FS and find the performance of CS to be inferior in certain measures related to the queue time. Suresh (1994: 274) observes that conversion from FS to CS results in a reduction in machine pooling (MP) that degrades the queue time performance as explained below. The FS consists of multiple work centers, each comprising a pool of similar machines, while a CS system consists of multiple cells. In a CS, a cell is created by allocating a subset of machines from one or more work centers of FS (known as a machine group), which is then dedicated to the processing of a subset of parts (known as a part family).
Subsequent research papers have exploited how a CS may compensate for the loss of performance resulting from the splitting of machine pools. A CS provides better opportunities to implement improvements in some structural and operational factors, such as setup time, processing time, and transfer batching, than its counterpart FS. Possibly for these reasons, a majority of past studies have considered improved CS to compare with the original FS. For example, reduction in setup and processing time (Sethi and Sethi, 1990: 301), reduction in variability of arrival and processing time (Wheatley, 2000: 12), and use of operation overlapping or transfer batching have been modeled in their CSS. Favorable factor settings to CS in various combinations of setup time, processing time, a variance of processing time and setup time, move time and transfer batching have been considered by the researchers. Analysis of twenty-four model-based studies on the relative performance of CS and FS by Wheatley (2000: 12) shows that the cases in which CS have lower throughput time (better performance) correspond to the factory settings that are favorable to a CS system
Similar conclusions can be drawn from the findings of Agarwal and Sarkis (1988: 81). This paper proposes that CS can outperform the FS in terms of queue time when the factor settings are not necessarily favorable to CS. The following is the motivation for this thinking. The splitting of the part population while forming cells may promote some performance benefits. For example, a machine in CS has to process fewer parts than in FS which may lead to a reduction in process time (PT) variability of parts in that machine (Sethi and Sethi, 1990: 303), and in turn, this can help in reducing the queue time. Further, the similarity between part routings is likely to be more in CS than in FS and this may have desired effects of reducing the variability of inter-arrival time (IAT) of parts to a machine (not necessarily the one where the gating operation is performed) leading to lower queue time. Splitting of machines into more than one stage can further help smooth the part flow or reduce the variability of IAT (Venkatadri, Rardin, & Montreuil, 1996). Thus, factors such as variability of process time and inter-arrival time may naturally get reduced due to the reorganization to
CS as a result of the partitioning of the machine and part sets. There is a possibility that the amount of such benefit (reduction in variability of PT and IAT) can offset the degradation due to loss of machine pooling and, under those cases, relative queue time of CS to FS, RQT is better.
The operating factors defining the best layout are processing time, setup time, lot size, and inter-arrival time. It is important to note that these factors have not been considered together in the past comparative studies (Venkatadri, Rardin, & Montreuil, 1996). Although it may be more realistic in practice to give certain structural advantages
Cellular Layout
“Cellular manufacturing” involves the formation of two groups of machines, work stations that are not similar in functionality within the same floor of work. It is often dedicated to using in similar products/parts production. The approach offers a direct contrast to functional shop layouts which involve grouping of machines as per the type and parts which apply pallet load moving from one machine species to the next. In cellular layout, the produced arts determine the arrangement of machines within a work floor. The concept dates back to the 1970s and was initiated as a measure of improving the manufacturing assembly processes.
A Cellular Manufacturing System (CMS) design is usually partitioned into several phases, including the selection of parts and part families, machines and machine cells, tools and fixtures, material handling facilities, and layout (Wemmerlov and Hyer (1987)). These phases are not independent and should all be considered through cell design goals. The overall goal for the design process is to achieve performance improvement concerning lead time, inventory, quality, or other measures (Sethi and Sethi, 1990: 291), or in other words, to achieve advantages of a CMS. Venkatadri et al. (1997) presented a complete list of advantages of cellular manufacturing. The most important ones, also reported by Wemmerlov and Hyer (1989) and Hopp & Spearman (1996), include reduction in move times, throughput, and lead time, WIP and finished goods inventory levels, setup times, as well as improvement in quality, capacity, and equipment utilization. There are many available studies in the field of CMS design. Most of them, however, is focused on the cell formation problem.
Moreover, there are not so many papers that concurrently consider all three phases of the design, namely part/machines grouping, intra-cell, and inter-cell layout designs within an integrated approach. As Shafer & Charnes, (1993: 671) state, one of the major drawbacks of cell formation techniques is that they do not lay out machines in cells (intra-cell layout) and on the shop floor (inter-cell layouts). There are also a few approaches for the layout problem in CM (Suresh & Meredith, 1994: 470). Moreover, most of the available studies for the cell formation problem are concerned with creating machine cells with the minimal number of inter-cell movements and not with minimal flow cost (Flynn & Jacobs, 1987: 568; Morris & Tersine, 1990:1569; Suresh, 1991: 775). However, a cell formation with a minimal number of inter-cell movements is not always consistent with the one with minimal inter-cell material flow cost, due to lack of layout data in the cell formation process.
Additionally, although the cell formation and the inter-cell layout problems have been jointly considered in the literature, most of the available methods are either based on the sequential
approaches (in which machine cells are found in the first phase and then the inter-cell layout is constructed based on the given cell formation; thus the quality of final solution largely depends on the given cell formation) or are based on difficult mathematical models (in which solving the problem is not easy, and therefore cannot be easily coded and implemented). Moreover, as mentioned before, the literature lacks studies that concurrently consider all three phases of a CMS design within an integrated approach is not rich.
Cellular Manufacturing Today
Today, cellular manufacturing (sometimes referred to as the “focused factory” or the “factory within a factory”) is used in a variety of industries, including automotive manufacturing, electronics, and even some machine shops. Still, many manufacturers have not adopted the cellular concept and some are not familiar with it. Others have tried to implement cellular layouts, only to meet with failure (Heize & Render, 2008: 67). This may occur when management fails to take the necessary steps to identify the parts the company produces and the manufacturing process required to produce them. Without careful planning, a cellular system may be no better than the system it is designed to replace.
Essential Components for Success
Some issues must be addressed before rearranging equipment and materials on the shop floor, including:
- Top management support: It takes substantial time and money to properly set up a manufacturing cell. If top management is not behind the concept and does not understand the importance of the elements listed below, the effort is doomed to failure.
- Manufacturing engineering: Like a traditional functional layout, the manufacturing engineer lays out the step-by-step process that will take place within the cell.
- Team development: A successful cell is planned, designed, and administered by a cross-functional team that includes representatives from purchasing, engineering, design, scheduling, finance, and human resources.
- Preventive maintenance: This step is the responsibility of workers within the cell. Daily preventive maintenance is particularly critical within a cell, because if a machine breaks down there may not be another nearby to take over its function.
- Product design: Changes in product design may have an impact on the layout of the cell. Conversely, the process of manufacturing a product within a cell may prompt design changes that spring from improved communication between designers and workers on the shop floor.
- Production control and schedule: Rather than producing a master schedule directing the flow of all products and materials through the plant, schedulers are concerned only with those parts produced within a particular cell.
- Housekeeping within a cell: Workers must be trained to take responsibility for keeping their cells neat and clean, and for properly storing tools within the confines of the cell.
- Quality control and inspection: Instead of periodic inspections of large batches of parts by the quality control department, quality control, and inspections are handled by the workers within the cell as they pass the parts to the next machine.
- Vendor development: Cellular manufacturing creates added demand for just-in-time delivery because the rate of production in a cell is more predictable than in an entire factory.
- Material handling: When a cell is implemented, the entire material handling system on the shop floor changes. Pallet loads no longer move from one end of the factory to the other. Instead, single parts or batches are handed from one machine to another just a few feet away.
- Setup reduction: One advantage of a cellular layout is that multiple parts can be run through the same cell. For this process to be efficient, setup times must be kept at a minimum to avoid wasting production time.
- Plant layout: This is the final step, once all of the above issues have been addressed. It is a mistake to implement a cell before analyzing the flow of the entire plant and the impact that the new cell will have on that flow. Functions that must be analyzed include factory flow, flow between cells within a department, the flow of materials between machines, and tooling requirements for individual machines.
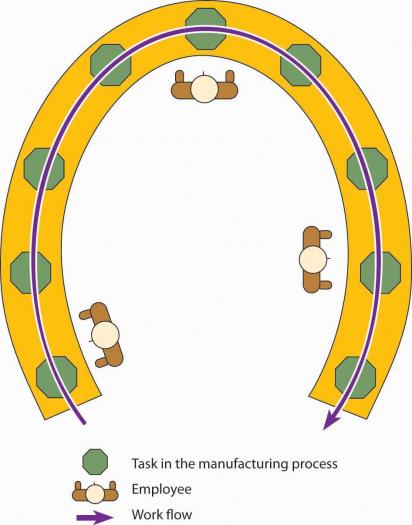
Functional layout
It is also referred to as process layout. It involves grouping of similar machines or processes into one place. The functions determine the arrangement of machines. For example milling processes are grouped at one point, lathes at one point and grinding operations at a different location. Job production and non-repetitive manufacturing environments form the ideal situations where this type of layout is applicable. The diagram below illustrates a sample layout of functional layout.
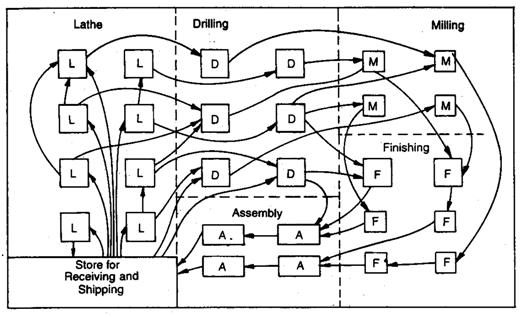
This type of layout has low initial investment, allow achievement of varied machine utilization degree because of the non-dedication of machines to one function, and great flexibility and expansion scope.
Discussion
Agarwal and Sarkis (1998) highlight important literature which looks into the relative performance and efficiency of both functional and cellular layouts in the manufacturing scenario. Their research include comparison of a series of research articles which consider the performance of FL and CM system and cast doubt on the actual benefits of CM. They also pointed out that the findings of research of Leonard and Rathmill, which involves several industrial case studies on medium to heavy engineering companies in the UK, ascertain this fact. Eight of nine simulation studies show the performance of CM to be inferior to that of FL. Generally, simulation studies reviewed shows some contradictory results of the superiority of CM and FL.
A simulation study (Assad et. al, 2003), which compare functional and cellular layout, shows that CM system can reduce flow time relative to job shop configuration. They analyze flow time reduction white at the same time regulating reduction set-up expenses, total loading, and the size of production batches. They identified that bottleneck may occur in CM system as the pooled resources of the job shop are segregated in to cells. The bottleneck has more pronounced effect on flow time and as a result CM system flow time will be inferior to job shop. This paper suggests that conversion to cellular manufacturing systems may not be advantageous if the utilization level is high or if there is not sufficient potential to reduce setups.
Morris and Tersine (1990) apply simulation in analyzing functional layout and cellular layout in relation to throughput time and the mean work-in-progress duration. They achieve this by considering various factors which affect production efficiency. According to them, none of the aforementioned factors reflect absolute advantage of cellular over functional layout (Morris and Tersine, 1990). Ultimately, though, the results postulate idea situations fro the cellular layouts. More stable demand pattern creates an environment where cellular layout out perform process layout. The result from the simulation experiment reveals that WIP level and average flow times are elevated in both systems due to the higher level of machine utilization caused by their higher set-up time. The cellular manufacturing layout problem by Salum (2000) narrates that most of the techniques for the cell design problem in cellular manufacturing consider only the machine-part incidence matrix as the input. Lack of adequate information has over time made it difficult to validate the perceived benefits of CR. A heuristic algorithm for machine assignment in cellular layout by Shafer & Charnes (1988: 340) presents a heuristic algorithm for the intra-cell machine allocation and evaluation. The heuristic algorithms contribute to the CM by providing good machine layouts for a cell and it is considered to be very good in terms of a heuristic approach.
The result from a simulation by Shafer & Charnes simulation showed that the average WIP and average MLT are elevated in cellular system (1988:339). Also, it was established that utilization of some machines is high in certain cell. This may be the reason for high WIP and MLT for cellular layout. This is mainly due to machines in some cell may become bottleneck as the pooled resources of process layout are segregated into some cells and congested as a result of cellularisation. This showed a point that the flow time in cellular manufacturing system is more sensitive to machine utilization in cells. This result indicates that machine utilization in cells should be kept at a medium level for improved performance in WIP and MLT and this fact should be kept in mind while designing cellular manufacturing system (Suresh, 1992: 271).
Average queue length in front of machines is found high in cellular system that might have caused elevated WIP and flow time. The mean usage time of plant is more in functional as compared to CR. This is matching with the general concept that cellular layout has lower average machine utilization due to duplication of machines. One can make some general observations about the relative queue time RQT and operating conditions. All four operating factors considered in this study have statistically significant effects on RQT when considered either individually or in some combination of settings of other factors (Suresh, 1992: 274). The finding of this exploratory research that, under certain experimental conditions, the loss of machine pooling can be counter balanced by benefits arising from splitting of part and machine populations is quite significant. However, further research is required to establish the conditions that are favorable to CS.
Researchers have been active in identifying the causes of superior performance of the cellular system over the functional system. Some early research studies show that the splitting of machine population leads to an inferior queue time performance in a cellular system. Several subsequent research papers have explored the ways in which a CS can be improved in order to compensate for the loss of performance resulting from splitting of machine pools (Webster & Tyberghein, 1989: 29). Review of literature indicates that CS can outperform the FS in terms of queue time without the settings being favorable to CS. This finding is quite significant and will open up an avenue for research.
Conclusion
The study, comparison of process layout and cellular system, has shown that the setup time reduction in cellular system cannot overcome the pooling loss. The batch sizes were same in both the systems. Use of reduced batch sizes may provide an improved performance for cells. Our simulation runs have shown the need for linking pooling loss and manufacturing load (demand) of cells with the reduced performance in MLT and WIP. Bottleneck may occur as the pooled resources of the job shop are segregated in to cells. Dedication of machines in cellular layout led to the formation of longer queue, more work in process inventory and longer waiting time. The result from the simulation experiment reveals that WIP level and average MLT are increased in cellular system due to high level of machine utilization (Suresh, 1992: 279). Generally, the advantages provided by the cellular configuration for managing the production system are intangible and hence it could not be appropriately included in the simulation model. One of the advantages due to cellular configuration is set-up time reduction and this aspect is only incorporated in the simulation. Other advantages are easiness to planning and scheduling, reduced congestion of plant for material movements, better production control, easy supervision, and better role of workers in managing production system, better tool control, etc.
Generally, a robust design methodology was available in literature for designing cellular manufacturing system that involves dynamic and deterministic production requirements. Robust cellular layouts reflect no change on configuration of cells based on the fact that product mix and product demand are seasonally and vary from one to another. The robust cellular layout available in the literature performs well with respect to the objective function value, which includes the total inter-cell material handling cost and machine acquisition cost.
References
Agarwal, A., & Sarkis, J., 1998. A review and analysis of comparative performance studies on functional and cellular manufacturing layouts.Comput Ind Eng, 34, pp. 77–89.
Flynn, B., & Jacobs, F. R., 1987. An experimental comparison of cellular (group technology) layout with process layout. Decision Sci, 18, pp. 562–581.
Heize, J., & Render, B., 2008. Operations Management, 9th ed., Upper Saddle River: Pearson-Prentice Hall.
Hopp, W. J., & Spearman, M. L., 1996. Factory physics: foundations of manufacturing management. Irwin: McGraw Hill.
Johnson, D. & Wemmerlov, U., 1996. On the relative performance of functional and cellular layouts: an analysis of the model based comparative studies literature. Prod Oper Manag, 5(4), pp. 309–334.
Morris, J. S., & Tersine, R. J., 1990. A simulation analysis of factors influencing the attractiveness of group technology cellular layouts. Manage Sci, 36(12), pp. 1567–1578.
Sethi, A. K., & Sethi, S. P., 1990. “Flexibility in Manufacturing: A survey,” The International Journal of Flexible Manufacturing Systems, 2, pp. 289-328.
Shafer, S. M., & Charnes, J. M., 1993. Cellular versus functional layouts under a variety of shop operating conditions. Decision Sci, 24(3), pp. 665–681.
Shafer, S. M., & Charnes, J., 1988.Cellular versus Functional Layout under a Variety of Shop Operating Conditions. Decision Sciences, 36, pp. 333-342.
Suresh, N. C., & Meredith, J. R., 1994. Coping with the loss of pooling synergy in cellular manufacturing systems. Manage Sci, 40(4), pp. 466–483.
Suresh, N. C., 1991. Partitioning work centers for group technology: insights from an analytical model. Decision Sci, 22(4), pp. 772–791.
Suresh, N. C., 1992. Partitioning work centers for group technology: analytical extension and shop-level simulation investigation. Decision Sci, 23(2), pp. 267–290.
Venkatadri, U. et al., 1997. A Design Methodology for the Fractal Layout Organization,” IIE Transactions, 29, pp. 911-924.
Venkatadri, U., Rardin, L. R., & Montreuil, B., 1996. Facility Organization and Layout Design: An Experimental Comparison for Job Shops. Technical Report No. 96-27, Québec: Laval University.
Webster, D. B. & Tyberghein, B. M., 1989. Measuring Flexibility of Job Shop layouts. International Journal of Production Research, 18, pp. 21-29.
Wemmerlov, U., & Johnson D., 2000. Empirical findings on manufacturing cell design. Int J Prod Res, 38(3), pp. 481–507.
Wemmerlöv, U., & Hyer, L. N., 1989. Cellular Manufacturing in the U.S. Industry: A Survey of Users,” International Journal of Production Research, 27, pp. 1511-1530.
Wemmerlov, U. & Hyer, N. L., 2002. Re-organizing the factory competing through cellular manufacturing. California: Productivity Press.
Wheatley, J. 2000. Super Factory – or Super headache. Business Weekly, 4, pp. 10-12.