Abstract
As many states in the world strive to reach a state of industrialization, there is a growing need among them to exploit cheaper and effective raw materials for their industries to enhance speedy growth in their economies. Naphtha is a raw material that industrialists need to use to make various industrial products as this study will reveal. The raw material under our study is significantly easy to produce as opposed to various raw materials of its kind and has a multi-purpose value. This study was done to determine how the cracking of naphtha produces olefins. Cracking of naphtha was employed in Texas’ affiliated towns of Houston, Austin and San Antonio.
The purpose of the study was to establish the amount of olefin, gasoline and other crude oils that were to be produced in the exercise. The study focused on both specific and general objectives for which the case study was founded. The process of naphtha cracking was considered, the procedure determined, results analyzed and discussed (William, 19). Petroleum products were cracked; naphtha and olefin among other components were collected. Crude oil was heated in a furnace as the primary step in breaking the straight chains. Butane, light naphtha, heavy naphtha, and kerosene were formed.
The vacuum tower played a role in producing wet gas. Instrumentation was based on the major units which were the cocker and thermal units. Both properties of naphtha and olefin were considered and discussed in depth. Their advantages and disadvantages in the oil industry were also considered. The uses and application of naphtha and olefin were also analyzed and discussed. Health and environmental considerations were made, and hazards discussed.
All possible health outcomes were analyzed and effects like carcinogenesis and dermatitis were put into focus. The methodology involved effective sampling design and procedures, data analysis, presentation and discussion of the results. The sampling design was descriptive in form and the presentation was elaborate and informative especially to the people of Texas. Conclusions were drawn based on the procedure and recommendations.
Purpose of the study
The study was aimed at investigating the process through which the cracking of naphtha produces olefins. Naphtha, which is a flammable hydrocarbon liquid mixture, holds different properties with most of them being useful, considering the dissimilar industrial components. Naphtha proved to be a central industrial source of crude oil. The purpose of the study was to determine how the cracking of naphtha would produce olefin.
The cracking process and industrial application of this vital product were analyzed. The study was meant to create awareness among potential investors in the industrial sector who may find this study useful as it will create a conceptual basis for their energy creation options. Every potential industrialist who realizes the utilitarian value of cracking naphtha to produce olefins may find it necessary to use this study as a guide especially when creating necessary health and environmental guides for his/her workforce and the community at large.
Objective of the study
General objectives
To produce olefin by cracking naphtha.
Specific objectives
- To understand the history of olefin.
- To study the properties and applications of olefin and naphtha.
- To understand the process of oil production and refinery.
Background
Olefins are unsaturated alkene compounds containing one or more double bonds. They can be mono olefins with the formula CnH2n e.g., ethylene, butylene, or propylene. Others can be duo-olefins with the formula CnH2n-2 e.g., butadiene, and isoprene. In these cases, ‘C’ represents carbon atom and ‘H’ represents hydrogen. ‘N’ is the coefficient representing the number of atoms making up the compound. Olefins are considered to be slightly soluble in water.
They are environmentally friendly producing few byproducts and are easily recycled are thus renewable. They can be recommended for industrial use based on ethical considerations because they do not pose grievous health risks to human beings. The history of olefin fibers can be dated back to 1957 in Italy when a chemist known as Gallo Natta came up with olefins for textile technique applications. In the United States, the production of olefin began in 1960, later after Italy. Olefin fiber constitutes 16% of all processed fibers. In the production of olefins, a saturation of aromatization is responsible for the high number of octane and may lead to susceptibility of the catalyst.
On March 18, 2013; the federal regulation in existence made United States’ gasoline prices volatile and very unpredictable. This fact was reported by EPRINC, an energy policy research foundation. On March 14, 2013; a petroleum corporation in Hindustan in connection with the government of Indian states signed a memorandum of understanding that envisioned a photochemical and refinery complex barmier, close to oil fields and under improvement by Carsin Indian limited. Naphtha being a major constituent of gasoline needs processing to achieve suitable quality gasoline. Distillation is an important process in ensuring that high chains of naphtha are produced. Naphtha’s application in feedstock makes it suitable for producing high octane gas. This process is also applied in the bitumen industry as diluents.
Problem statement
The purpose of the project is the cracking of naphtha to obtain olefin proved challenging and several issues had to be addressed. First and foremost, the market policy proved to be a complicated subject and the committee in coordination with a few corporate bodies had to come to an understanding of the marketing procedures. Standardization and certification were other issues that had to be addressed with immediate considerations. Both the local and international measures for the control of olefins had to be observed. Regulation of production in terms of demand and supply was also observed and discussed to bring balance to the various factors of production including land, capital, and labor. Finally, the environmental, health, and ethical considerations were addressed, and vital standards of operation were observed.
Limitation and delimitation
The complexity of the operations made the study limited to a certain scope. The scope of the study had to be affected along with factors of cost and urgency of production, operation and machine cost, environmental effects, ethical considerations and the subordinate circle. Delimitation was critical and could be achieved by commitment, team spirit, effective corporate network and government legislation.
Ethical consideration
Ethical standards like good neighborliness policy, standardization and certification were among the procedures observed in the project. Compliance with the law and policies of production necessitated ethical compliance of the study. Politically and socially, the immediate society was ready to extend its support and ensured that key stakeholders would embrace the energy revolution.
Significance of the study
The study provided not only an overview of the oil industry but also an in-depth analysis of olefin production among other fuel portions. The study brought out the many relations that exist between different energy molecules and sources. The information was vital in the understanding of the production, processing, and application of naphtha and olefins in general. The study defined the relationship between energy and the environment and how the two relate with each other and health considerations concerning the same.
The study enabled me to understand the process of cracking of naphtha and the compartments involved in thermal and active processes. Vladimir Shukor engineered thermal cracking. It was then modified by William Burton in 1908. William was credited for this invention though he had improved on what had been started by Vladimir. In 1934, in the Shukar factory, the process of cracking of naphtha was established in USSR at a place called Baku. In 1941, the Standard Jersey World made the first naphtha cracker. Throughout the world today, there is high demand for olefin. Propylene constitutes 94% of olefin in the world. In West Europe, 95%of olefin produced there is ethylene. 61% of the world’s production of ethylene is done in the Asian continent.
Literature review
Definitions
Naphtha cracking refers to the breakdown of high molecular weighed naphtha by heat application. The process produces many end products. Olefin is one of them. Naphtha is defined as a flammable liquid mixture produced through the process of distillation and it is a major source of crude oil. Olefins on the other hand are defined as unsaturated compounds commonly known as alkenes. They contain at minimum one carbon to carbon bond i.e., c=c.
The process
Olefins were produced during the cracking of oil and petroleum products to produce gasoline or olefins. The polymer, in this case, naphtha, was melted to a liquid state by going through a furnace process. It was then run through a spinner. The spun mixture was forced through small holes to produce long fibers. The fibers were useful in making fabrics. Naphtha contained long-chain synthetic fibers which were broken through the application of heat. Olefin fibers were produced through a conversion process that involved ethylene and propylene. The olefin fibers constitute approximately 85% of ethylene, alkene, and propylene. The addition of the dye to the spinner content was done before its melting. The melting of the polymer was done by subjecting it to a spinneret. It then went through water or cooled air.
The following diagram illustrates how olefin is collected at the collecting unit following the cracking process.
At the chamber, more heat meant a high reaction rate and so would be the output. Crude oil heated in a furnace was separated into butane, light naphtha, kerosene, heavy naphtha, and reduced crude and atmospheric gas oil. The reduced crude derived from the vacuum tower was cracked thermally in delayed cocker to produce wet gas and cocker gas. The light naphtha was streamed away from the crude tower. The cracking and cocker units were sent to the unit of isomerization.
In the isomerization unit, the paraffin straight chains were converted into isomers with high octane numbers. Heavy naphtha on the other hand went through a similar process. It streamed away from the crude tower. The cracking and cocker units were fed to the catalytic reforms to improve the number of octanes. From the catalytic reforms, products were blended into regular premium gasoline which was ready for sale.
Below is a diagram showing how crude oil is cracked to produce olefin among other quotients.
Isomerization unit
In steam cracking, the carbon-to-carbon bonds were broken when the heat was applied. The cracking rate was determined and depended on the temperature factor and catalytic activity. Alkanes were broken down into smaller alkanes and alkenes. The process of steam cracking involved 3 subsections and they were pylorisis unit, fractionation and compression units and finally the separation sector.
The pylorisis section contained the pylorisis furnace which produced steam and cracked gas. The energy requirement in this unit was high with approximately 61% of the total energy input with variables experienced with temperature change. In some cases, pyrolisis would operate under extremely elevated temperatures of between 750°C to 900°C or even more. In this case, more ethylene was produced. This kind of pylorisis was referred to as destructive distillation. In some cases, pylorisis would operate under a reduced temperature of about 500°C commonly known as delayed cracking. This aspect would produce needle coke due to delayed heat and low temperature.
In the fractionation and compression sector, the energy requirement would amount to almost 65% of the total energy input, slightly higher than in the pyloric unit. In this unit, the pressure build-up was experienced due to compression and fractionation resulting in partitioning and segmentation. In the separation unit, a lower energy input was experienced about 25% of the total.
Little energy and temperature were needed in the separation of the various quotients, but fractionation played a major role in segmentation. Products from this section included ethylene (24%), propylene (20%), butadiene (3%) and petrified ether (25%). Steam cracking (pylorisis) was the most energy-consuming process and used approximately 8% of the oil sector’s total energy use. This process consisted of the pyloric, fractionation, compression, and separation fragments.
In advanced cases like advanced distillation, the column membranes happened to be energy conservative. In these scenarios, energy saved amounted to about 10%. This aspect was commendable since it saved on the cost of production. Financially, it was a relief from the burden of stretching to other quarters like marketing and advertisement. Alternative technology was applied in hyropylorisis in which water which meant that steam was involved in cracking of naphtha zeolite.
Hydropylorisis was effective in the breakdown of naphtha to produce olefin. It was discovered that introduction of the catalyst had an enormous energy saving potential. The catalytic activity incorporated alumina which was produced by the crushing of pumice. The alumina catalyst necessitated an increase in activation energy and reduced the rate of energy consumption. The activation energy was defined as the amount of energy required to overcome an energy barrier. The overall effect of the catalytic system was a net increase in output of production and consumption of energy. However, the catalytic system was selective.
The system was particular on the aluminum catalyst to be used to generate the equilibrium between the input and the output networks. In some instances, the operation required the removal of coke. This fact saved on cost of energy and time. Plenty of room was created for energy saving. It was recorded that 90% of chemicals benefited from the catalyst and the saved energy was about 20%.
Comparative case study
Cracking as a process is challenging as it involves several complicated processes. Cracking can be hydro cracking or fluid catalytic cracking (FCC). FCC produces high volumes of gasoline and liquid petroleum gases also known as LPG while cracking of naphtha through hydro systems produces jet fuels and diesel products. The FCC system is composed of cat crackers which are used in oil refineries within the US due to high gasoline demand. FCC was first employed and used in 1942. It uses a powder catalyst mainly alumina obtained from crushed pumice. The gasoline which is produced in the FCC portion has high octane number.
However, gasoline is unstable chemically due to olefin properties. The olefin contained in products of gasoline is used to make polymers used in the production of storage tanks, fuel pipes and automotive injectors. The deposits especially in storage tanks have profound negative effects on the final product. The amount of deposit may increase with a coefficient in production rate and the operation of the FCC unit. The FCC liquefied petroleum gas is believed to be a rich source of c3 to c4 isobutene and olefin. Hydro cracking on the other hand employs operation of hydrogen gas created under partial and optimum pressure.
In the study, the hydrogen molecule plays the role of purifying the hydrocarbon gas. This process was done to ensure purity of Sulphur and nitrogen atoms. Products in this system were saturated and this happened after the double bonds were broken and included ethane, LPG and isoparaffins. The hydro cracking system was facilitated by a bi functional system of catalyst. The system was to break and at the same time rearrange the hydrocarbon chains.
The system was also responsible in the addition of hydrogen to olefin band aromatics. This step was done to produce saturated alkanes and naphtha. The hydro cracking process constitutes the production of octane and jet fuel. Hydro cracking was also common in the US due to high demand for gasoline. Steam crackers were used for the production of butane and propane through use of steam pressure in a pyloritic chamber. The aim was to produce lighter hydrocarbon output. This process was done in absence of oxygen. High temperatures of about 850°C were channeled briefly.
Instruments and other requirements
The operation employed use of the cracking unit, the cocker unit and the isomerization unit (Prestoris, 40). The cracking unit was composed of the cracking chamber or the furnace, the spinner and catalysts. The isomerization unit incorporated the blender, the isomerism catalyst and the collecting systems. Other requirements were the distiller, dye system and the cooling system.
Research instruments
The research happened to be an involving undertaking in terms of time and materials. Some of the instruments that were used were: map indices, stationeries, Google tools, reference materials like books, search engines among others. The instrument helped me to come up with relevant data and incisive analysis on the subject.
Properties of naphtha
Naphtha was seen to be a colorless band and to some extent reddish brown similar to gasoline in appearance. It had a molecular weight of between 100 and 215g/mol with a density of between 750 and 785kg/m3. The boiling point was considered high ranging from 160 to 220°. It has an odor like that of kerosene. Naphtha is liquid at room temperature and pressure, insoluble in water and incompatible with many strong oxidizers.
Uses of naphtha and industrial application
Naphtha was used in production of motor gasoline in industrial networks. It was used as a cleaning fluid for most industrial solvents (Fourie, 23). Certain scientific practitioners used it as an oil painting media. Naphtha is an important ingredient in shoe polish. Others used naphtha as fuel for fire spinning or fire juggling or in gas turbine units. Some watch mechanics use it in cleaning watch parts (Kent, 1983).
Properties of olefins
Olefin fibers are bulky with low specific gravity. They have low moisture absorbing power. They however dry easily and quickly due to low melting point. Olefins are believed to be resistant to fire and chemical attack. Despite their inability to absorb dyes effectively, they color fast and are thus efficient in performance.
Uses and applications of olefins
Olefin fibers are used to make sports and active wears, underwear and socks. They are useful in making lining fabrics, outdoor and indoor carpets, wall coverings, floors and slip covers among others. In the automotive industry, olefins can be used in making of interior fabrics for automotive.
Health considerations and hazards
Naphtha forms are considered to be carcinogenic. Direct or indirect exposure to them is highly discouraged and protective clothing should be worn when handling naphtha. Naphtha is known to depress the central nervous system. Depression of this vital system has adverse effects on an individual bringing about mild consciousness, panic, stress, and mental disturbance. In certain cases, naphtha can be used and administered in general anesthesia. In advance cases, naphtha can lead to narcosis, mild chronic encephalopathy, dermatitis which is characterized by a persistent rash.
Location of the study
The study was conducted in Dallas, Texas in the United States of America. The aim was to target resources and people from San Antonio, Houston, and Austin.
Methodology and sampling procedures
The sampling procedure employed in data collection was random sampling. This fact is because random sampling is not biased, and little time is consumed during the procedure.
Research design
The study used descriptive design to evaluate and analyze the data that was collected. Descriptive design was privately utilized and worked within a short period.
Data analysis and presentation
Both Microsoft access and excel were unemployed in analyzing the data collected. The presentation was done using tables, graphs, and diagrams as below
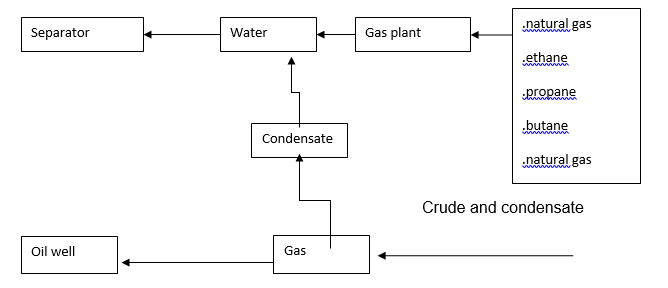
In separation, the oil patch (polymer/naphtha) went through a water compartment. Part of it was passed as condensate and part through the gas plant. In the gas plant, the component was separated into other smaller fractions of natural gas, ethane, propane, butane, and natural gas. Butane and propane in this case were referred to as low power gas (LPG). The study performed also involved a comparative case on products made by the United States petroleum industry and the following was noted
Results
Discussion of results
Grease had the highest number in terms of production because it is easily produced. The breakdown of macromolecules like naphtha produces more grease than gasoline or olefin because olefin is volatile. Though fairly produced, negativities like volatility, low melting point, low specific gravity, and bulkiness tend to derail the production of gasoline. Fuel gas is the least produced due to the complexity of its production and operation. When a pipe was still cut in the range of c5 to 4200F, the following quotients were clear.
- Light virgin naphtha consisting of c5 to 160°F
- Intermediate virgin naphtha consisting of 160 to 280°F
- Heavy virgin naphtha consisting of 200 to 380°F
- Very heavy virgin naphtha consisting of 250 to 410°F
The following pie chart represents the information
- Light virgin naphtha…….160°/1230°* 360°= 47
- Intermediate virgin naphtha……280°/1230°*3 60°= 82°
- Heavy naphtha……380/1230 * 360°= 111°
- Very heavy naphtha……410/1230 * 360 °= 119°
Conclusion
The production of olefins from naphtha cracking is a complex but important process in the oil world. Energy is important in running machines and facilitating industrial applications. Olefin energy output has proved to be potentially fair in terms of production and performance. Its positive effect on the environment makes olefin human friendly and therefore appealing to the eye. It is also important to note that information is useful as it guides the correct production and use of olefins and involves the integration of all factors. Only informed individuals can be able to run these processes because there are some risks involved (Beychok, 34). These effects include carcinogenesis, narcosis, dermatitis, and other mild health complications. Proper choice of study location and the target group is a necessity in managing an enterprise dealing with an olefin (Fleig, 12).
A comparative study of the case should be done with progressive research on different and related subjects. Health measures should be taken to safeguard the lives of the people within the study area. Ethical standards are crucial to maintaining a peaceful, calm, and authoritative system of production especially in an industry of this type. The environment system should be economically, socially, and politically viable (Gary, 24). The environment should exploit study sources and provide potentially productive pathways in terms of knowledge and information for comparative studies in this area.
All stakeholders and philanthropic organizations must harness and protect this provision of nature by stimulating information empowerment and awareness schemes notwithstanding the challenges and limitations of the study. A stimulating environment breeds a healthy platform for growth. The cracking of naphtha means that an industry that deals with olefin is an educative and informative venture for scholars, industrialists, and scientists. Greater research on the cracking of naphtha will also attract investment and donor funding given that olefins do not pose serious environmental and health implications if properly processed and used.
Recommendation
I would like to recommend the people of Texas and the government to employ better, safer, and faster methods of harnessing energy and power. I would encourage the government to create awareness through campaigns and use the media in building what is considered the interest of the majority. The government through the necessary education authorities should also establish a relevant curriculum to be studied by scholars to enable research to be carried out in the area of production of olefins by cracking naphtha. The cracking of naphtha to produce olefins should be an area of study that all scholarly bodies especially the ones dealing with engineering should finance to create new knowledge that will improve on the existing practices.
Investors on the other hand should be encouraged to bring their efforts in making the nation powerful in production, job creation, and extension services. I would also like to recommend the civilians and the general public who have got the passion and zeal of promoting scientific innovation through value addition in the cracking of naphtha to produce olefins to be financed to boost their projects to their final realization. My recommendation also goes to all the nongovernmental organizations both local and on the global scale to encourage alternative production of energy by funding communal and individual projects aligned towards alternative energy production.
I would recommend the government of Texas to employ knowledgeable and energetic individuals who have the skills and experience to conduct the processes of naphtha cracking as an independent and selective industry in the oil world. This will lead to the high productivity of olefins which will create a wider market and supply networks and hence improve the living standards of the people of Texas.
Works Cited
Beychok, Milton. Aqueous Wastes from Petroleum and Petrochemical Plants, New York City, USA: John Wiley & Sons, 1967. Print.
Fleig. Frank.Oil Empire: Visions of Prosperity in Austrian Galicia (Harvard Historical Studies, Harvard, United Kingdom: Harvard University Press, 2005. Print.
Fourie, Pieter.Media Studies: Media History, Media and Society, Landsdown, South Africa: Juta and Company, 2008. Print.
Gary, James et al. Petroleum Refining: Technology and Economic, New York, USA: CRC Press, 2007. Print.
Prestoris, Anders. Compositional Analysis of Naphtha and Reformats, New York, USA: CRC Press, 2004. Print.
William, Leffler. Petroleum Refining for the Nontechnical Person, Oklahoma, USA: PennWell Books, 1985. Print.