Introduction
Naphtha reforming is the most common process of rearranging hydrocarbon molecules. The first attempt appeared as thermal reforming in the 1920s. Over the years, scientists have developed naphtha reforming as a method of generating high-octane gasoline for commercial use (Antos, Aitani and Parera, 2004).
The naphtha reforming is a key to the refinery processes because it offers high-value added reformate for the commercial “gasoline; hydrogen for feedstock improvement by the hydrogen-consuming hydro treatment processes; and frequently benzene, toluene, and xylene aromatics for petrochemical uses” (Antos, Aitani and Parera, 2004). Naphtha reforming technology has changed refinery processes. For instance, it has become useful in hydrogenation, dehydrogenation, and isomerization (Gary and Handwerk, 1984).
In addition, there are also feed treatment technologies, which have facilitated catalytic naphtha reforming processes. Recent innovations present a strong outlook for naphtha reforming technology. Naphtha reforming takes place under harsh conditions. Therefore, there is a continuous need for improvement. The research has advanced to produce high-levels of octane.
Since the introduction of naphtha reforming, scientists have conducted thorough studies in order to comprehend chemistry behind the process. The main elements of the catalytic naphtha reforming are platinum and other several metallic catalysts. The simple process relies on a combination of these elements in order to generate a high-performance reforming catalyst. The technical challenge has been how to understand the chemistry behind naphtha reforming. Therefore, many scholars have embarked on several studies in order to simplify the process. In fact, some studies have explored the unknown elements of the catalytic process in naphtha reforming. On the same note, other studies have attempted to predict the future of catalytic naphtha reforming technology. The focus on catalytic naphtha reforming technology is due to the rising demand for fuels and petrochemicals and the need for low emissions of dangerous gases from their usages.
The chemistry of naphtha reforming
Catalytic reforming changes naphtha into reformate. The procedure entails the regeneration of low-octane hydrocarbons from naphtha into rich-octane gasoline elements. This process does not affect or change the boiling point during the reaction. Paraffin, naphthenes, and aromatics are the complex elements that are available in naphtha and reformate. Thermal cracking also has olefins. However, naphthas that come from different sources have other elements like sulfur and nitrogen. These additional elements have effects on the performance of the metal catalyst. Therefore, it is necessary to eliminate such elements in the catalytic reforming before they can reach the reformer section. It is also necessary to note that elements in the hydrocarbons and concentrations of other elements are responsible for the quality of reforming feedstock.
Naphtha Elements
Crude oil or petroleum contains about 97 percent of hydrocarbons. Elements of hydrocarbons are mainly paraffinic, aromatic, or naphthenic. These elements also have light and heavy waxes. Other elements are mainly nitrogen, oxygen, sulfur, water, and salt. In some cases, there also metals like sodium, nickel, and vanadium. The crude oil contains naphtha that has a boiling point range of 30° C to 200°C. It usually has an average weight that constitutes about 15 percent to 30 percent of the total weight of the crude oil. The hydrocarbons mainly range from C5 to C12 with some elements of metal and sulfur.
There are:
- Light naphtha (30° C to 90° C), containing the C5 and C6 hydrocarbons.
- Heavy naphtha (90° C to 200° C)
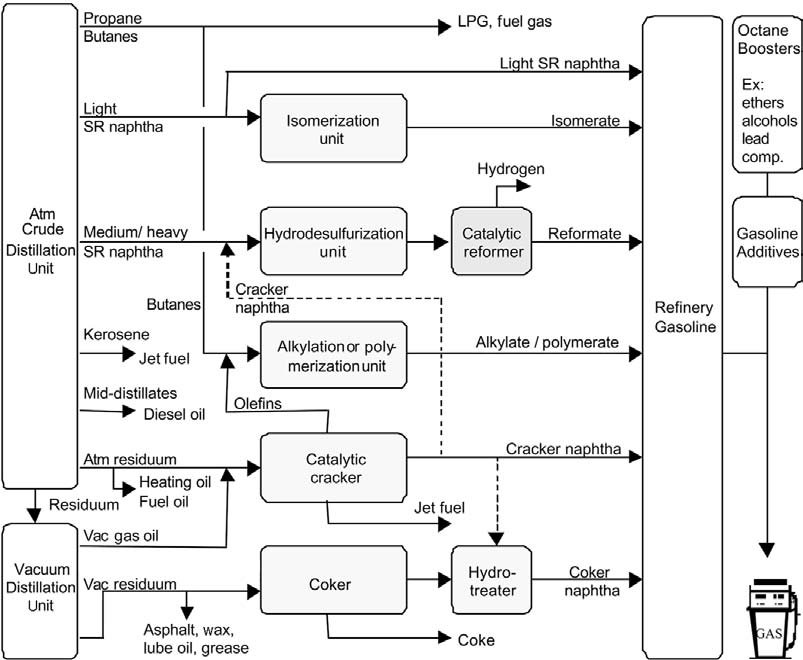
Naphtha Composition
Hydrocarbons
Aliphatic hydrocarbons consist of saturated alkanes. Alkanes have a general chemical formula of CnH2nþ2, which is either straight or branched. As alkanes become complex, their boiling points also increase.
Heteroatomic constituents, Water, and Metallic elements
Crude oil has sulfur as one of the constituents. The availability of sulfur depends on the type of crude oil. The weight of sulfur may range from zero to more than five percent in the crude oil based on the type of the crude oil. Sulfur is mainly common in the end of the crude oil. Sulfur concentration is useful in the feedstock processing. The process of eliminating sulfur from crude oil is hydrotreating (Little, 2007). This involves the change of sulfur to H2S by using a catalyst under hydrogen pressure.
There are also elements of nitrogen, oxygen, and water in crude oil. The presence of elements of water in crude oil is a challenge to naphtha reforming. Naphtha fractions may eliminate some elements of water during various processes. However, the distillation temperature of water is higher than petroleum. As a result, it creates challenges during the process of distillation. Water may also deactivate catalysts used in the naphtha reforming by neutralizing acidic contents.
There are also resins and asphaltenes metallic elements as a part of the naphtha compositions.
Impacts of naphtha composition on catalytic reforming
The composition of hydrocarbons, availability of impurities, and differences in boiling points of naphtha all influence the reformate product. Features of the feedstock also affect the naphtha reforming processes. These variations also have impacts on performance and the duration of the catalyst. The gasoline has to meet some quality requirements and octane rating.
Gasoline Quality Requirements in Gasoline and catalytic reforming process
The main aim of catalytic reforming is to enhance the presence of octane in the naphtha feedstock to a point that meets the requirements of the reformate product as a quality blended gasoline. The number of octane is critical because it shows the extent to which the gasoline can withstand knocking when burning the mixture of air and gasoline in the engine cylinder. The European gasoline standard must contain the research octane number (RON) with the range of 95 to 98. Such a high-level of octane number is suitable for effective compression ratios that are necessary for the best use of fuel. In addition, gasoline must also meet environmental safety standards and other properties that can make it to function efficiently. Olefins can clog the engine due to its tendency to create gum because of the oxidation process. The vapor pressure of the gasoline must be low in order to reduce cases of volatile light hydrocarbons.
There are also dangerous components in naphtha reforming that fall under the category of carcinogenic. In addition, a component like Tetraalkyllead has been an octane booster, but it is no longer desirable because of its gradual accumulation in the environment. Therefore, such elements are under strict regulation by governments, and a number of refineries no longer use them. Still, carbon usages lead to accumulations of CO2 in the atmosphere, which lead to the global warming and the poisonous carbon monoxide (CO).
The Octane Number
The aim is to determine the rating of research octane number (RON) and the motor octane number (MON). The RON and MON have different test processes. RON accounts for the performance of the engine at low-speed, whereas MON is for high-rate of the engine speed. The octane number is useful in gasoline blending in order to ensure the right knocking performance of the engine. Elements with the high number of octane like aromatics are suitable for blending.
In most cases, the process involves increasing the octane number of reformate by changing naphthenes into aromatics with alkane elements. These changes are the main reactions for the naphtha catalytic reforming processes.
Catalytic Reforming Process
This process takes place at high temperatures that range from 450°C to 520°C with a regulated pressure of 4 to 30 bars. A suitable catalyst in a series of reactions in the presence of hydrogen changes naphthenes into aromatics dehydrogenation. At the same time, alkanes also go through dehydrocyclization in order to create aromatics.
The reactions also involve hydrogenolysis and hyrdocracking. These reactions (isomerization) result into paraffins with low weight of molecular together with the coke that deactivates the reforming catalyst (see figure 2).
The hydrogen from the reaction is significant for the process because it is applicable in the hydroprocessing units as an element for eliminating sulfur and nitrogen. It is also valuable for the hydrocracking process. The conversion of naphthenes to aromatics is a quick endothermic process. The process relies on high temperatures and low pressure to facilitate the reactions.
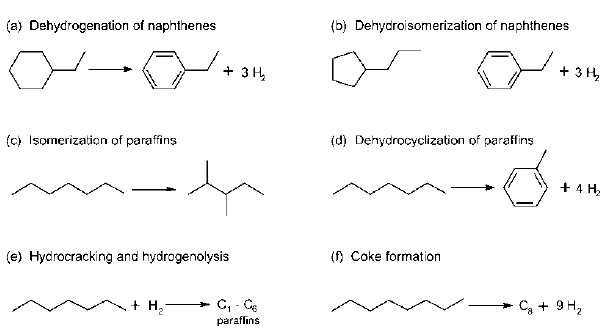
The reaction instantly hydrogenates olefins. A small percentage of olefins can occur with hydrogen under such pressure in the reforming process. Paraffins also experience quick isomerization under thermodynamic conditions. However, paraffins undergo a slow process of dehydrocyclization with controlled kinetic processes. As the pressure increase, the rate of hydrocraking also increases, but this reduces the yield of reformate. Coking is a slow process. However, it increases fast under low pressure of the hydrogen and high temperature. Coking is responsible for catalyst deactivation.
Controlling hydrocracking through high temperatures and low hydrogen pressure reduces the cause of low yield reformate. This is the method of optimizing the formation of hydrogen and aromatics in the hydrocracking. However, this process affects the stability of the catalyst.
The catalyst in this process has both metallic and acidic functions. The metallic function involves platinum, which acts as a catalyst during the dehydrogenation process. The acidic reaction occurs due to chloride alumina, which facilitates the isomerisation process. These properties give the catalyst a bifunctional role.
In the reforming process, platinum remains the active agent. As a result, it is effective for maintaining high rates of reaction on the acidic carrier (mainly aluminum oxide). The process also involves the use of catalyst enablers like fluorine, chlorine, and rhenium. Platinum is expensive. However, it has a long life and results into products of high quality and yield.
The main process involves breaking down hydrocarbon chains in order to obtain small-saturated chains. This reaction also results into the formation of isoparaffins. Isoparaffins have many structures of chain molecules. Cyclization or transformation of alkanes into naphthenes also takes place during this process (ring compounds). Dehydroganation of naphthenes results into aromatic compound. Aromatic compounds are not saturated, and they have few numbers of hydrogen atoms that link with the carbon. The process results into separation of “hydrogen, which forms an important by-product for catalytic reforming” (Antos, Aitani and Parera, 2004). The final products are “aromatics and isoparaffins, which have a high concentration of octane numbers” (Antos, Aitani and Parera, 2004).
In this initial stage, the naphtha charge must undergo the process of removing any elements of sulfur in the presence of hydrogen. The resultant feed then passes through hydrogen in order to form a mixture. This process involves heating at high temperatures of about 500°C to 540°C.
The gaseous mixture then goes through a catalyst with more than three reactor chambers. Over the years, the reaction process has increased from 25 bars (350 psi) of pressure to less than seven bars of pressure (100 psi). During the reaction, the mixture absorbs heat. Therefore, reheating is necessary between various chambers of reactors.
In the final phase of the reaction, condensation takes place in order to turn the product into liquid. The process involves separation of hydrogen elements through the fractionating column in which distillation process also eliminates elements of light hydrocarbons. The final reformate product can undergo “blending into the required gasoline without any additional chemical treatment” (Antos, Aitani and Parera, 2004). Hydrogen from the reactor is condensed and directed back to the reactor chambers.
In the reactor chambers, the operating conditions must ensure that the resultant product has the needed amount of octane. This optimal octane level is usually about 90 to 100. High-levels of octane result into small yield and constant catalyst application is necessary. Small amounts of carbon deposited on the catalyst causes “the process to produce low yield products” (Antos, Aitani and Parera, 2004). In some cases, the plant may have semigenerative facilities in which engineers must remove parts affected by the carbon deposits for rejuvenation of the catalyst. The demand for fuel rich in octane has led to the creation of continuous regeneration technologies. This prevents the plant shutdowns and increases the yield of octane in the fuel. The continuous regeneration moves the catalyst from the reactor chamber into the regenerator chamber in which elimination of carbon deposits take place and rejuvenation of the catalyst occurs. The rejuvenated catalyst then goes back to the reaction chamber.
In most cases, a catalyst may last between one and two years. The new systems allow the catalyst to have a cycle of six to eight days before regeneration can take place. The presence of sulfur affects catalyst, which is a reversible process. However, hydrotreatment can eliminate elements of sulfur in the naphtha feedstock.
It is also necessary to keep the level of water low in order to avoid leaching of the chloride, which affects the strength of the acid. Metallic elements like iron and silicon may affect catalyst reaction in the naphtha reforming. However, metallic elements are rare in catalytic naphtha reforming.
Reformer Feedstocks
Antos, Aitani, and Parera note that a typical reformer feedstock is “straight-run naphtha distilled directly from crude petroleum” (Antos, Aitani and Parera, 2004). In some cases, naphthas also come from fluid catalytic cracking and hydrocracker. Such naphthas also undergo processing in the reformer.
Removing sulfur elements from crude oil involves the process of hydrotreatment. The process is necessary for removing sulfur that can poison the following naphtha reforming. Sulfur contents in petroleum products must also meet environmental requirements. Molybdenum sulfide catalysts are the most common for commercial purposes in sulfur removal. These catalysts are applicable in the process of hydroprocessing of different forms of feedstocks.
Naphtha hydrotreatment catalysts must be of high activity and selectivity in order to facilitate the hydrogenolysis process. At the same time, the catalysts must have low selectivity in order to break the C-C bonds of carbons. Still, such catalysts must have low activity for hydrogenation of aromatic compounds. This is necessary for sustaining the octane number and lowering the usage of hydrogen. Hydrotreatment catalysts must also have long life and low reactivity to poisons.
Naphtha hydrotreatment usually sets up the feedstock for catalytic reforming. After a considerable period, sulfur compounds affect all reforming catalysts. Such metallic elements affect adsorption and coordination of the catalysts. High concentration of sulfur in the feedstock causes unwarranted coking and fast deactivation. Under commercial processing, the level of sulfur in the feedstock must be exceptionally low. The process eliminates nitrogen elements at the acid chambers. While such catalysts can slow the acid reaction, they also have the ability to change metallic properties of the platinum. Moreover, they can leach the chloride when there is water. Therefore, it is necessary to eliminate any nitrogen element at the reformer feedstock.
In some instances, a minute level of sulfur may be necessary for lessening the extreme hydrogenolysis activities during the first stages of reforming catalysts. Prior sulfidation of the catalysts for inhibiting the active sites and avoiding rise in temperatures of the reactor because of the extreme hydrocracking process is necessary during the reforming process. High temperatures and hydrogen pressure have reversible effects on the catalyst in which removal of sulfur occurs, whereas other elements stay as irreversible. Some reports have indicated that the amounts of “reversible and irreversible adsorbed sulfur have equilibrium values dependent on the temperature and partial pressure of hydrogen sulfide” (Antos, Aitani and Parera, 2004).
The presence of sulfur in the feedstock reduces the lifespan of the catalysts. Therefore, it is necessary to keep the level of sulfur as low as possible in order to reduce poisoning effects and increase the lifespan of the catalysts. Therefore, engineers must observe the recommended levels of sulfur in order to prevent poisoning of hydrogen transfer abilities. Any increment in refraction of the metal results in an increase in poisoning sensitivity. Thus, adequate management of sulfur in the feedstock is necessary in order to protect the catalyst.
It is expensive to remove sulfur from the reformer feedstock. However, it saves to extend the life of the reforming catalyst in naphtha processes. Elimination of sulfur may be through a stream of hydrocarbon alongside a catalyst. The reaction uses up the hydrogen and produces hydrogen sulfide. Hydrotreatment is a method of removing hydrogen sulfide in the gas. This involves the use of amine solution to remove hydrogen sulfide. Hydrotreatment has been the effective method of eliminating elements like sulfur and nitrogen that contaminate gasoline in the reformer feedstock. The final stage in the hydrotreatment involves the passing of feedstock with hydrogen gas over a catalyst in order to produce the desired product quality and properties.
Process Flow Scheme of hydrotreatment
In most cases, commercial hydrotreatment plants have similar flow systems (see fig. 3). Hydrogen mixes up with the gas or oil and heats under high temperatures of 250° C to 450° C in hydrotreatment. Naphtha turns into vapor during this process. The desired product properties and compositions of the feedstock affect the feed that flows through various metal oxide catalysts. In this reaction, oil and hydrogen react to produce ammonia, hydrogen sulfide, and concentrated hydrocarbons.
In case where the unsaturated stock is, another reactor may be necessary for the main reactor. Additional reactor is useful for saturation of the diolefins under low conditions in order to eliminate high temperatures that occur under exothermic reaction.
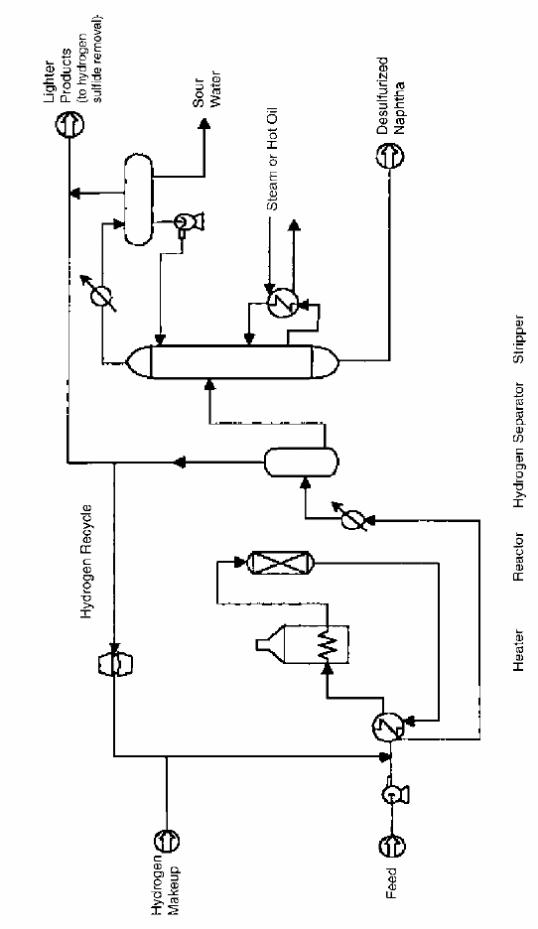
Operating Parameters of Hydrotreatment
There are two critical conditions, which influence the operating conditions of naphtha hydrotreatment. These include:
- The feedstock properties.
- The preferred properties of the product.
These two conditions are the prerequisite for setting naphtha hydrotreatment. However, there are also other properties to consider, which include the type of catalyst, pressure, heat, and the purity of the hydrogen.
Increments in the level of sulfur, oxygen, nitrogen, and olefin elements also result in increments of advance hydrotreatment in order to reduce these high concentrations to appropriate levels.
Table 1: Naphtha Hydrotreating operating parameters (figures from Antos, Aitani and Parera, 2004).
Usually, straight-run stocks require mild conditions while straight-run feeds and blends require severe conditions.
Changes in hydrotreatment
Hydrotreatment is one of the most significant processes in refinery operation. However, demands for safe and efficient fuel have led to changes in hydrotreatment. For instance, the demands for clean fuels and strict environmental laws have led to significant changes in hydrotreatment. As a result, refineries have increased capacities in order to meet such demands for increased quality and quantity (Enos, 2002).
In the recent past, the need for heavy fuel has reduced and the trend would continue into the future. Therefore, refineries must opt for processes that can yield gasoline with desired properties. The aim is to increase the production of cracked stock. Cracked stock is important for isomerisation and reforming. For instance, in the next decade the focus of oil refineries shall be on reducing environmental challenges, producing low sulfur fuel and reducing the amount of gasoline in fuel. One such approach shall involve the posttreatment in order to eliminate sulfur from the fluid catalytic cracking (FCC) naphtha and other blendstocks and meet stringent requirements (Magee and Dolbear, 1998).
The refineries shall be able to manufacture high quality petroleum products by integrating conventional processes and applying specific measures of eliminating hydrocarbon elements from the fuel. In this regard, the focus shall shift on hydrogen management for reducing the amount of sulfur gasoline. Refiners expect to rely on catalytic reforming in order to generate hydrogen for the process.
Changes in Catalyst Reforming
Catalyst for naphtha reforming has been a major area of focus for refiners in the preparation of platinum catalysts. Platinum is the most important metal in all commercial processes of naphtha reforming. However, the process has evolved since 1940s with the particular focus on chemical components of reforming catalysts. From 1960s, there were bimetallic catalysts such as Ir, Sn, Re, and Ge to act as process enablers. These catalysts reacted with platinum in order to provide the best gasoline selectivity and enhance performance stability. Such additional catalysts have provided opportunities for reducing operating pressure in the refineries. The aims of both bimetallic and multimetallic reforming catalysts are to enhance the role of platinum on halogen like chlorine for providing the necessary acidity for naphtha reforming.
Some researchers (Chevron and UOP) have commercialized their findings on multimetallic catalysts such as L-zeolites, which rely on the platinum of the alumina. These multimettalic catalysts have high selectivity for dehydrocyclization. However, they have low number of units relative to the total units. Such low numbers in units may result from sulfur poisoning.
Platinum-containing Catalysts
It is important to consider main characteristics of catalysts in order get the best performance and cost benefits.
- The catalyst should have low platinum content, evenly distributed for utmost atomic diffusion. This is necessary for eliminating cases of sintering in high temperatures.
- Proximity to the acid sites.
- Retention of the mechanical properties of the platinum and other support catalysts.
Placing alumina support on platinum requires the use various impregnation methods, which include impregnation with interaction and impregnation without interaction. Impregnation with interaction involves the formation of an electrostatic with the platinum elements. In impregnation without interaction, the catalyst support has no affinity for the surface of the platinum, and it remains as localized elements during evaporation of the solution. Some studies have shown that catalyst impregnation through contact is superior because of effectiveness in metal diffusion and catalyst activities.
Catalyst performance requirements
Naphtha reforming processes are diverse so that catalysts have their own processes. The process of naphtha reforming is also bifunctional, i.e., some reactions occur at the surface, whereas others occur at the acid sites of the platinum, alumina, or other metal catalyst (Hyne, 2002). However, optimal performances require the two approaches to interact and mix. However, the challenges are due to diverse properties of naphtha reforming catalysts. In most cases, researchers may overlook assumption when developing appropriate models for reforming catalysts. It is necessary to consider the quantity, strength, and distribution of the acid site and gauge the amount and activity of the catalysts.
Chemical engineers should prepare catalysts with similar properties and develop the process to have catalysts with the necessary selectivity and activity, control catalyst performance, and regulate conditions of the working catalyst in order to maintain performance and achieve required specifications for a long time. Therefore, it is necessary to relate characteristics of the catalyst with its performance requirements. However, it is not necessary to have the absolute values with regard to features of the catalysts. Therefore, if 30 ppm of chlorine in the reforming offers the best activity and selectivity for naphtha reforming for a certain catalyst, then refiners’ approach needs only the quantity of the chlorine for the reforming. In other words, it is not necessary to provide the exact amount or properties of the catalyst. In this sense, characterizations for engineering purposes are “essential for the successful application of catalysts in commercial naphtha operations” (Antos, Aitani, and Parera, 2004).
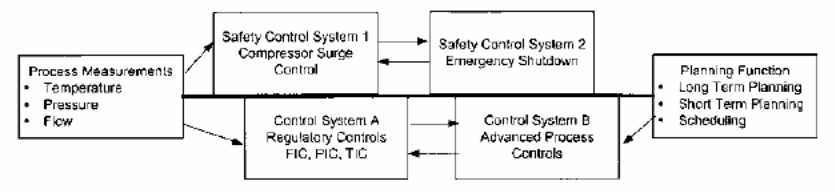
Conclusion
It is a fact that catalytic naphtha reforming has been the main process in the refinery for manufacturing gasoline that is rich in octane. The demand for gasoline has increased significantly, and the need for naphtha reforming has increased too. As a result, chemical engineers have formulated new methods of naphtha reforming to meet such new demands.
There is a need to produce environmental friendly gasoline. Thus, regulations have pushed refineries to redefine their processes. Specifically, there is a need to reduce the amount of sulfur in gasoline. This demand has affected the catalytic reforming processes in productions.
As a result, new technologies and discoveries have developed effective processes of “hydrogenation, dehydrogenation, and isomerization have all benefited from the catalyst, reactor, and feed treatment” (Antos, Aitani and Parera, 2004).
The long-term position for the naphtha reforming remains positive as new technologies emerge. The conditions of naphtha reforming have continued to present challenges to engineers. Therefore, there is a need for reformates.
Recommendation
- There is a need to deploy new technologies in catalysts or improve processes of naphtha reforming.
- Refiners must maximize the utilization of the available facilities.
- As the demand for clean energy puts pressure on engineers, they must react by producing clean energy to meet strict regulations and environmental requirements.
- Chemical engineers must recognize that the current practices shall not counter the demands on fuel energy.
References
Antos, G., Aitani, A., and Parera, J. (eds). (2004). Catalytic Naphtha Reforming (2nd ed.). New York: Marcel Dekker, Inc.
Enos, J. (2002). Technical progress and profits: process improvements in petroleum refining. Oxford: Oxford University Press.
Gary, J.H. and Handwerk, G.E. (1984). Petroleum Refining Technology and Economics (2nd ed.). New York: Marcel Dekker, Inc.
Hyne, N. (2002). Nontechnical Guide to Petroleum Geology, Exploration, Drilling, and Production. Tulsa, OK: PennWell Books.
Little, D. (2007). Catalytic reforming. Tulsa, OK: PennWell Books.
Magee, J., and Dolbear, G. (1998). Petroleum catalysis in nontechnical language. Tulsa, OK: PennWell Books.