Introduction
Lubricating oil has found a wide range of applications in the world today. Unlike in the past when various fluids were used as lubricants, lube oil is the preferred lubricant given its high efficiency in the function of lubricating. As such, the production of lubricant oil in refineries is an important stage in crude oil processing.
Despite being various categories of the lube oil as mentioned earlier in the project, mineral lube oil from petroleum is the commonly preferred lubricating oil to the synthetic lube oil.
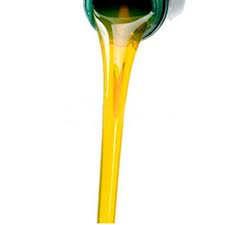
The history of lubricating oils can be traced back from the time civilization was born. In the historical times, various substances such as animal fat or plant oils were used as lubricants. Fluids such as water were also used as lubricants despite being inefficient.
The ancient people understood that parts of machines that were made of metal needed lubrication to prevent wear and tear as well as ensuing that they operated efficiently. For instance, the wheel axels of chariots were lubricated using tallow or rather animal fats to reduce friction.
However, as time went by there was steady development in the technology of lubrication especially after the realization of petroleum by Colonel William Drake in 1859.
However, the raw crude oil was a poor lubricant performing even poorer than animal fats and plant oils thus calling for the refinery of the crude oil to give several products. Among the many products recovered from crude oil refinery were lubricant oils, which play a significant role in reduction of friction in machine parts.
As mentioned earlier in this project, the extraction of lubricating oils from crude oil is a multistep process that involves distillation, solvent extraction, and dewaxing as shown in the diagram below.
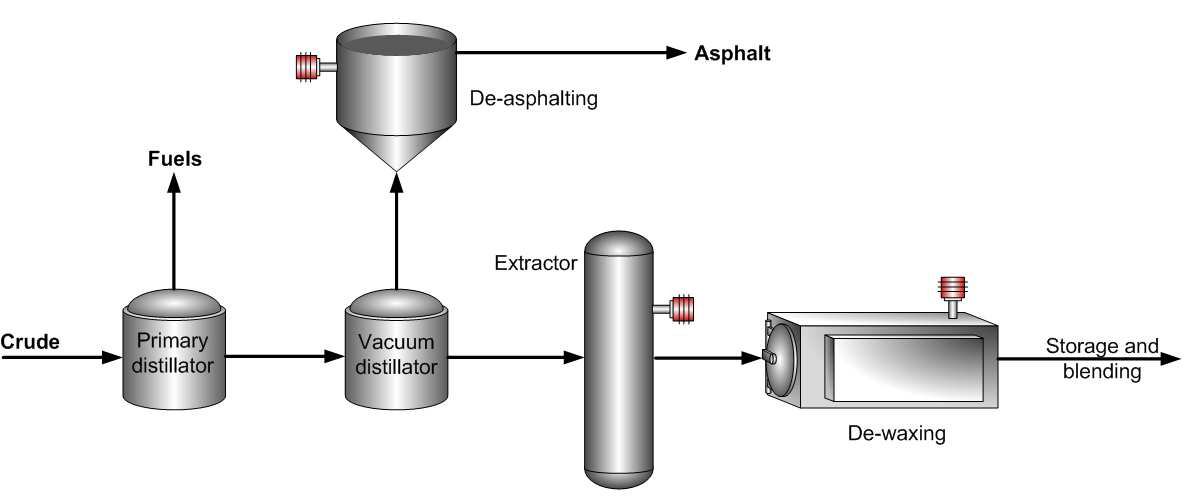
This section is an in-depth analysis of further processing of the dewaxed raffinates to produce different categories of lubricating oils.
Processes after dewaxing unit
Dewaxing of raffinates uses different methods, with crystallization method as the most commonly used method. Crystallization method is one of the most expensive of dewaxing raffinates in contemporary oils schemes.
Since this method of dewaxing is expensive, many studies have been carried out develop new methods. In this case, the process will make use hydrocracking also called catalytic hydrodewaxing (Wuest et al, 1999, p.71).
The process of dewaxing using catalytic hydrodewaxing uses high-silica zeolites that have catalysts that are a size of a pore and ranges between 38 and 52 nm to primarily split the n-alkanes. The dewaxed oils that are produced through this process cost less than traditionally manufactured oils by about 10 to 20%.
The refining of high wax oils requires that waxes be obtained to be used for different applications besides the dewaxed oils. In this case, it important to ensure that at first, the solid hydrocarbons are extracted from the raffinates where they go through partial dewaxing.
After partial dewaxing, slack waxes are obtained and deoiled so that the dewaxed raffinates can be taken through selective hydrocracking. In this section, three main processes that take place after dewaxing will be discussed. These processes are hydrofinishing (HDF), hydrocracking (HDC), and hydrotreatment (HDT).
Hydrofinishing (HDF)
The lube oil obtained after dewaxing normally encompasses foreign substances such as oxygen, sulphur, organic metallic compounds, and nitrogen just to mention a few.
The aforementioned substances lower the quality of the lube oil and should therefore be removed in order to improve the quality of lubricating oil produced. For instance, sulphur makes the lube oil corrosive because it presents itself as heteroatomic hydrocarbons and mercaptans, which are corrosive in nature.
Oxygen as foreign substance in lubricating oil may cause acidity if corrosion occurs in its presence. Oxygen could also affect the stability of oxidation especially in the presence of unsaturated compounds.
Nitrogen compounds affect the original colour of the lube oil by giving it an off-colour tinge. The metallic compounds on the other hand lead to degradation of metal parts in machines if the lube oil is used before their removal.
As such, hydrofinishing plays a significant role of enhancing the stability of the lubricating oil. This process majorly entails the use of catalysts to hydrogenate the lube oil after dewaxing. The hydrogenation takes place in the fixed bed reactor where nickel-molybdenum is added to the feedstock to serve as a catalyst.
Pressures in the reactor are relatively high to enable the catalyst perform well. “Temperature and pressure are maintained at around 3500C and 50-80 kg/cm2, depending on the feedstock to be treated (Chaudhuri, 2011, p.70).
Under these conditions, the foreign impurities mentioned in this section that include oxygen, sulphur, organ metallic compounds, and nitrogen are removed through hydrogenation hence leaving the lube oil free of foreign substances that lower its quality.
Hydrogenation is simply a method of decomposition of the foreign substances. The resulting lube oil after the hydrofinishing process is of higher quality than the lube oil at the feed pump after dewaxing. Below is a stepwise diagram of the hydrofinishing process.
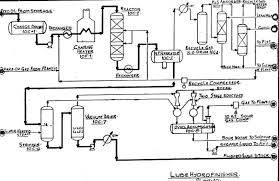
Hydrocracking (HDC)
Hydrocracking is yet another quality improvement process carried out after lube oil dewaxing. In hydrocracking, the aromatic content of the lube oil is reduced in bid to increase the viscosity index of the final product. Sulphur and nitrogen are also eliminated during this process.
Just as it is in the case of hydrofinishing, a catalyst is used in the presence of hydrogen to facilitate hydrocracking.
Essentially, hydrocracking will involve the cracking or breakdown of heavy stocks of petroleum at high temperatures and pressure (Luxton, n.d, p.1). The heavy stocks could include vacuum distillates and residues of the vacuum process.
Hydrotreatment (HDT)
This is the final step to producing high quality lubricating oil. As the name suggests, hydrotreatment is simply the treatment of the lube oil with hydrogen to help remove process-generated impurities.
As such, hydrogen gas from the hydrogen plant is pumped into the lube oil at optimum conditions and left to react hence decomposing the impurities to leave pure lube oil.
“As a final step the hydrotreated oil is fractionated under vacuum to separate out the gasoil fraction formed during the hydrofinishing and split the lube oil into the desired finished cuts” (Speight, 1980, p.102). Below is a diagram showing the hydrotreatment unit.
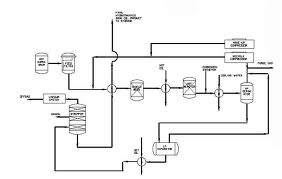
Types of lubricants produced
Lubricating oils can be grouped into three main classes depending on the kind of processes they are subjected to after dewaxing. This can be depicted in the flow chart below.
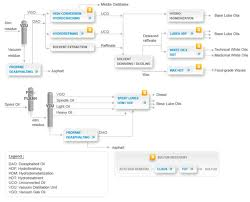
Base Lube oils
These are produced when the dewaxed raffinate undergoes the hydrofinishing process. They normally make 80-90 percent of the lubricating oil generated after refining.
Other modified lube oils that are tailor made to meet the specifications of the user take the balance of 10-20 percent. However, the base lube oils are further classified into three groups in accordance with the American Petroleum Institute (API). This is depicted in the diagram below.
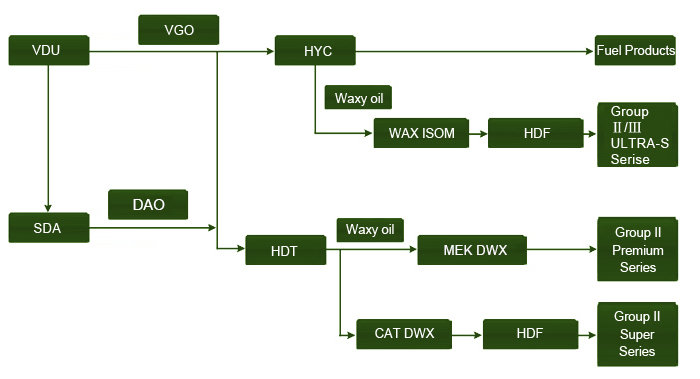
Group I Base oil
Group I base oils are produced by a simple solvent refining process to get a product with saturates percentage of less than 90 and a sulphur content of more than 0.03 percent. In addition, they have a viscosity ranging from 80.
They work best at temperatures ranging from 32 to 150 degrees F. They are the cheapest type of lube oil found in the market today given their less costly method of manufacture.
Group II Base oil
These have a saturate percentage greater than 90 and a sulphur content of less than 0.03 percent. They have the same viscosity as group I base oils but differ in terms of processing since they are produced by hydrocracking (Nigmatullin et al., 2000, p. 26).
“This process saturates all the hydrocarbon molecules present in the oil thus making it bear better antioxidation properties” (Nigmatullin et al., 2000, p. 26).
As a result, group II base oils will have a clearer colour than that of group I base oils. Given their better qualities as lube oil, group II base oils are preferred to group I base oils.
Group III Base oil
Group III base oils are highly viscous with a viscosity of more than 120. They have saturates making up to more than 90 percent with a sulphur content of less than 0.03 percent (Luxton, n.d, p.1). In terms of refinery, group III base oils are hydrocracked and hydrotreated to produce a highly pure product.
The table below shows the classification of base oils according to API.
Table (Pickle, 2012, p.1).
Technical White oils
These come about after the hydrotreatment of dewaxed white oils. It is a pure grade of oil, which is produced after technical refining of the lube oil. As such, it could be used in equipments in the food processing plant since it complies with the FDA regulations.
Medicinal White oils
These are more refined than the technical white oils thus of a higher grade. Medicinal white oils are produced after hydrotreatment of the final lubricating oils. They normally lack components and substances that could be of harm to the human health.
They have therefore found great application in the food industry as well as in pharmacology. For instance, medicinal white oil is used to lubricate parts of meat packaging and soda bottling plants among other food industry machinery.
Specification and properties of lubricating oil
Generally, lubricating oils are expected to have the following characteristics in order to function as expected.
- They should have low friction.
- They should be non-corrosive.
- They should have a high thermal stability.
- They should be resistant to wear and tear.
- They should be consistent.
- They should be less volatile.
- They should be oily.
However, different lubricating oils will bear different characteristics given their mode of processing and refining. Good lubricating oils will have a stable viscosity index such that the viscosity does not change with changes in temperature.
Given the fact that most of the lubricating oils are applied on moving parts of machines where temperatures fluctuate, it is important that lubricating oils maintain their viscosity in all instances to enhance efficiency.
Good lubricants are those with low volatility rates because volatile lube oils will vaporize with time leaving the machine part without any lubricant.
At the same time, lubricating oils ought to be oily and able to slide within the films that they have been applied onto. The lubricating oils are expected not to be able to catch fire since they are used in automobiles and other machinery that are prone to fire (Banta, 1998, p.72).
Finally yet importantly, lubricants ought to be non-corrosive so that they do not corrode the metal parts of machines.
Uses and application of lubricants
The main use of lubricating oils is to lubricate machine parts in a bid to reduce friction hence preventing wear and tear of machines. In addition, lubricating oils serve the following roles:
- Transferring heat.
- Preventing corrosion.
- Preventing dust.
- Transmitting power.
- Keeping moving parts away from each other.
- Stopping the risk of fire and smoke.
Nevertheless, it is important to note that different types and categories of lubricating oils will be applied in different scenarios as follows:
Solid lubricants
These are highly viscous and used as coating layers, bearings and sliding surfaces. They will be most suited in machine parts with temperatures of up to 3500C.
They are also applicable in high vacuum machine parts since they can stand high pressure. As such, they have found their application in air compressors, railway tract joints, heavy machines and chains just to mention a few. Solid lubricants are commonly used hot climatic regions.
Semi-solid lubricants
These are semi-viscous and resist being moved or squeezed out. This makes them suitable in heavy machines as well as in machine parts that are not easily accessible.
They are also best suited in parts with sudden jerks and those that move with slow speed (Willmer, 1971, p. 95). Just like solid lubricants, semi-solid lubricants prevent dust accumulation by providing a coat layer on the parts they have been applied. They can be used in regions with varying climatic conditions.
Liquid lubricants
These have a lower viscosity thus able to flow easily in machine parts. In addition to this, they act as a cooling agent to moving machines while at the same time preventing dirt and corrosion. The application of liquid lubricants is quite high in the automobile industry where delicate machines are involved (Rhodes, 1993, p.45).
This is because of the fact that liquid lubricants perform best in fast moving machines that operate under low pressure. Below is a picture showing lube oil being poured into the engine part of an automobile. Liquid lubricants work best in cold regions where the temperatures are low.
Conclusion
From the above discussion of the production of lubricating oils, it can be deduced that it is a multistep process that yields different grades of products depending on the involved processes. Both hydrofinishing and hydrotreatment process are aimed at improving the quality of the lube oil by removal of impurities.
Nevertheless, all the types of lube oils produced have their applications most of which is industrial application. As mentioned in the paper, lube oils play a significant role of reducing friction between machine parts thus preventing wear and tear of machinery.
Reference List
Banta, F., et al. (1998). Improved processes produce high-quality lubes. Oil & Gas Journal 96(1), 70-74. Web.
Chaudhuri, R. (2011). Fundamentals of Petroleum and Petrochemical Engineering. London: CRC Press.
Luxton, A. (n.d). Hydrocracked Base Oils What Are They? Web.
Mortier, R., et al. (2010). Chemistry and Technology of Lubricants. New York: Springer.
Nigmatullin, R., et al. (2000). Selective Hydrocracking of Partially Dewaxed Raffinates. Chemistry and Technology of Fuels and Oils 36(1), 25-28.
Pickle, J. (2012). Understanding the Differences in Base Oil Groups. Web.
Rhodes, A. (1993). Refinery operating variables key to enhanced lube oil quality. Oil & Gas Journal, 91(1), 45-45. Web.
Speight, J. (1980). The Chemistry and Terminology of Petroleum. New York: Marcel Dekker.
Willmer, S. (1971). Classification of lubricants and hydraulic fluids. Industrial Lubrication and Tribology 23(3), 92-95.
Wuest, R., et al. (1999). Singapore all-catalytic lube plant performs well. Oil & Gas Journal, 97(1), 70-73. Web.