Introduction
The extraction of lubricating oils from crude oil is a multistep procedure as mentioned earlier in the paper (Speight, 1980, p.71). The reason behind this is the inability to achieve constant liquid phases as certain temperatures. For that matter, single stage extraction of lubricating oils is difficult.
In the ancient times, the extraction process was single stage thus giving a product with many undesirable compounds, which could be termed as impurities. This is what led to the invention of the solvent extraction method, which produces high yield of the lubricating oil. Nevertheless, the solvents have been used in the multi-stage extraction process to dissolve the crude oil and make it easy to get sufficient yields of lubricating oils among other products such as asphalt, gasoline, and gases just to mention a few.
In solvent extraction, phenol, NMP (N-methyl-2-pyrrolidone), and furfural are the preferred solvents given their high yields of the lubricating oils from crude oil. In fact, research conducted indicates that in solvent extraction, the yield is normally as high as 70-80 per cent of the total input.
In this extraction, there are also significant quantities of waste materials. When using solvents to extract lubricating oils, a single type of solvent or a combination of two solvents could be used. Research has shown that the yield from a combination of two solvents is greater than that from a one type of solvent.
Nevertheless, given the negative health and environmental effects of phenol, furfural is the most preferred solvent, which is mostly combined with NMP (N-methyl-2-pyrrolidone). This paper is therefore an in-depth analysis of the extraction of lubricating oils by looking at the methods of extraction, description of processes, purpose of extraction and new developments in lubricating oil extraction with emphasis on furfural extraction method.
Methods used to extract oil
The extraction of lubricating oils is highly dependent on the solvents used. Several methods can be used to extract lubricating oils after they have passed the other stages of separation. The commonly used method of lube oil extraction entails the use of solvents in the crude oil. These solvents include phenol, NMP (N-methyl-2-pyrrolidone), and furfural just to mention a few. Membrane extraction is also another method that could be used in the extraction of lubricating oil (Sankey, 2009, p.6).
Below is a typical chart showing the extraction of lube oil using furfural as a solvent.
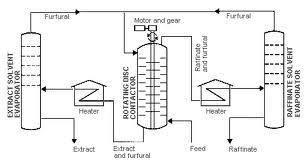
Phenol Extraction Method
This is one of the most recent methods of extracting lubricating oil from crude oil.
In this method, phenol is used as the refining solvent. Just like in furfural extraction, the phenol is put in the extraction unit to act as a solvent. However, unlike furfural, phenol is easily recovered after the extraction process (Stratford, Moor, and Pokorny, 1933, p.1). Phenol is selective in the derivation of a variety of distillates thus producing lubricating oils of high quality.
Phenol is the preferred solvent by many because of its non-reactive characteristic as well as because it does not decompose in oil during the extraction process unlike other solvents. Secondly, phenol mixes with oil at high temperatures of about 100-200F, which is similar to the distillation temperature (Stratford, Moor, and Pokorny, 1933, p.1).
This means that the extraction of lubricating oil with phenol is undertaken at a lower cost since less energy is required. In addition, it is less labour intensive and can be carried out by even three men. However, given the effects that phenol has on the health of human beings as well as the environment, it is rarely used as a solvent for extracting lubricating oil.
Furfural extraction method
In extracting lubricating oil, furfural is used to reduce the aromatic content of vacuum distillates. The removal of hydrocarbons from vacuum distillates is done in order to improve the lubricating properties of the oil. Once the crude oil residue is obtained after the distillation process, it is undergoes a further distillation process under a vacuum.
Here, the crude oil is becomes cuts of lubricating oil that are simultaneously obtained at different temperatures (Sankey, 2009, p.6). “The commonly obtained raw cuts are; the spindle distillate (SPD); the Light neutral distillate (LND); the medium neutral distillate (MND); the heavy neutral distillate (HND) and the bright stock distillate (BSD)” (Sankey, 2009, p.4).
For high quality extraction of aromatics from the mixture, it is important that a solvent with the right properties be used. This solvent should be able to create two phases of the liquid as well as have the ability to prevent oil from getting lost.
Furfural extraction Purpose
Furfural is preferred as a solvent in lube oil extraction because of its ability to select aromatic compounds thus increasing the rate of reaction. In addition to this, furfural can be used in vacuum distillates of different viscosities. Unlike other solvents, furfural is environmental friendly and causes less harm to the health of human beings.
In addition to this, furfural can be applied to a wide range of raw materials. This makes it a better solvent than the rest. Its ability to form emulsions is also low hence making it easy to be separated from oil. Furfural is also preferred for lube oil extraction since its raffinate extract is of higher yields compared to the rest.
Process description
The process of extracting lubricating oil suing furfural as a solvent normally takes place in a column that is fitted with rotating plates and sieves. It is normally a process with several stages, which can be listed as:
- Preparation of the raw material through drying and air removal.
- Solvent addition.
- Separation of lube oil and solvent.
In furfural extraction, the first step entails having the distillate obtained from the distillation process dried. After drying, it undergoes deaeration to remove air in the distillate. This is important because any traces of air and moisture in the distillate would affect the extraction process hence the quality of lubricating oil. Air is known to oxidize furfural; hence, it has to be removed to ensure high quality and yield of the lubricating oil.
Once the distillate is free of air and moisture, furfural is added in the column and the rotating plates facilitate mixing. The ability of the solvent to dissolve the crude oil is important in determining the ratio of oil to solvent. In most cases, the ability of a solvent to dissolve oil increases with rise in temperature and decreases with a fall in temperature.
Thus, for the extractor to perform well, it is endorsed with perforated disks that keep rotating. This creates a column known as the rotating disk column (RDC). The intensity of rotation depends on the flow of the distillate as well as that of the solvent. “In order to increase extraction degree, i.e. improve separation of the raffinate from the extract phase, cold reflux of the extract phase is added to the extractor” (Sankey, 2009, p.4).
The extract phase is then allowed to settle and later move to the flash column. The flash column plays the role of drying the furfural leaving the extract free from solvent. Upon cooling, furfural is removed and taken to a separator after which the extract is stored. The next stage involves taking back the furfural to the raffinate phase. Later, the raffinate phase undergoes dewaxing, a process that entails production of base oil and bitumen among other products.
Process configuration
The furfural extraction process is configured in such a way that is able to process up to four feed stocks, which include heavy neutral, light neutral, spindle oils and intermediate neutral. These can be tabulated as below:
Table. 1 (Sankey, 2009, p.6)
The extract is normally passed through various ultrafine filters to remove impurities. Aromatics are one such impurity and it contains six-carbon rings that affect the viscosity of the lube oil” (Fuels, Lubricants, and Coolants, 1992, p.92). Since the aromatics are highly soluble, it makes them easier to be removed through solvent extraction. In order to enable the lube oil to endure low temperatures and have other desirable qualities, it other additives are mixed with it (Fuels, Lubricants, and Coolants, 1992).
An assessment of the” flash, viscosity, specific gravity, fire points and colour is done”. Upon acquisition of the desirable standards, the oil is packaged and distributed (Fuels, Lubricants, and Coolants, 1992). Extraction of furfural from the raffinate is made by heating it thus leaving the extract.
Below is a diagram showing the configured process of furfural extraction of lubricating oil.
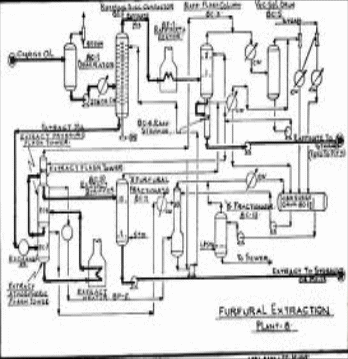
Equipment
Several equipments and machines are used in furfural extraction of lubricating oil. Some of which include;
- Extraction column: In this column, the solvent is fed into the crude oil and allowed to dissolve. This equipment contains an in-feed pipe from the vacuum distillatory and an out-feed pipe to the de-waxing equipment. Temperatures in this equipment are relatively high in order to increase the miscibility of the solvent with the lubricating oil.
- Solvent recovery system: It is made up of two fractionating units together with a surge drum. The fractionators labelled as A and B serves the purpose of separating water from the furfural moisture, in this case the raffinate. The surge drum on the other hand, plays the role of drying hence facilitating complete removal of furfural from the extract.
Process variables
The process variables in the extraction of lubricating oil are the temperature used, solvent to oil ratio, and the stages of extraction that the oil undergoes.
Temperature
As mentioned earlier in the paper, the temperatures used in the solvent extraction unit are significantly high to increase the surface areas of reaction between the solvent and the oil. Thus, low temperatures are bound to inhibit reaction hence poor extraction of the lubricating oil.
Ratio of solvent to oil
The ratio of solvent to oil is also crucial as it significantly determines the reaction rate of the oil with solvent hence affecting extraction.
Number of stages
Finally yet importantly, the number of stages of extraction is also important in determining the quality of the final product of lubricating oil. The more the stages, the better the quality of the lubricating oil produced.
New development in lubricating oil
New developments in extraction of lubricating oils centre on the source of the lubricating oil and the methods of extracting it. Currently only furfural and phenol extraction methods have been in use. Canadian engineers discovered the EXOL N extraction method. The new Exol N solvent is said to have better lube extraction selectivity than both phenol and furfural; better chemical and thermal stability than furfural; and it is safer then phenols (Ferris, Birkhimer, and Henderson, 1931, p. 754).
Tests have proved that use of the solvent increases the yield of lubricating oil and save the cost of energy. The Residuum oil Supercritical Extraction process is a new solvent extraction method said to be efficient for recovering lubricating oil of higher value from the crude oil residue. It is based on the use of a paraffinic solvent, which can be recycled and recovered. The advantages of the residuum oil super critical method is that it saves on the energy and reduces the cost of investment on equipment.
The new development, which has stirred controversy in scientific and environmental circles, is extraction of oils from algae. Experiments have proved that lubricating oils and biodiesel oils can be extracted from algae. In that case, algae is selectively harvested and used in oil extraction. “The chemical methods are categorized into; supercritical fluid extraction method; soxhlet extraction method; and Hexane solvent extraction method” (Ferris, Birkhimer, and Henderson, 1931, p. 755).
Mechanical methods include Ultrasonic-assisted extraction and Expeller/ Expression press method (Ferris, Birkhimer, and Henderson, 1931, p. 756). The extraction methods generate more controversy as mechanical methods would require the energy intensive process of drying the algae while the use of chemical solvents poses both health and safety dangers.
Nevertheless, given the exploitation of natural oil resources such as crude oil, it is evident that soon or later the synthetic-based lubricating oils will be in high demand given the non-renewable feature of natural sources.
Conclusion
From the above discussion on extraction of lubricating oil, it can be deduced that it is quite cumbersome to come up with a product that will protect the wear and tear of machines. It has also been noted that of the three commonly used solvents, furfural is the most preferred given its good qualities and ability to give high yields of the lubricating oil.
This quality is also significantly influenced by three variables mentioned in the paper, which include process temperature, the ratio of solvent to oil and the extraction stages.
By putting all the aforementioned factors in mind, the lubricating oil is of high quality thus perfectly playing its functional role. Given the high demand of high quality lubricating oil, the manufacturers have resorted to ways that could ensure that they produce high quality lubricating oil at reasonable costs. One of these ways is by using furfural solvent under the discussed optimum conditions.
Reference List
Ferris, S., Birkhimer, E., and Henderson, L. (1931). Solvent Extraction of Lubricating Oils. Industrial Engineering Chemistry 23(7), 753-761.
Fuels, Lubricants, and Coolants. (1992). Canada: Deere & Company Service Publications.
Mortier, R, et al. (2010). Chemistry and Technology of Lubricants. New York: Springer.
Sankey, B. (2009). A new lubricants extraction process. The Canadian Journal of Chemical Engineering 63(1), 3-7.
Speight, J. (1980). The Chemistry and Terminology of Petroleum. New York: Marcel Dekker.
Stratford, R., Moor, H., and Pokorny, O. (1933). Phenol as a selective solvent in refining of lubricating oils. Web.