Introduction
Polymers are chains of tiny molecules linked together repeatedly to develop a single layer molecule (Polymer chemistry n.d.). The small, repeating units are called monomers and the entire process of joining the molecules is called polymerization. When similar units are joined repeatedly to make the polymer a homopolymer is formed. Conversely, when different repeating units are linked to form a polymer the resulting product is a copolymer (Kurtz 2012).
Polymers can also be linear or branched. The conditions present during the synthesis of a polymer determine whether the polymer formed is branched or linear. Polymers form the basis of ingredients for substances with exceptional chemical and physical traits. Polymerization manipulates huge, complex molecules and takes advantage of the linkages between their molecular configurations that make them helpful (Polymer chemistry n.d.). The exceptional properties of polymers are determined by the extent and the organization of the molecular chain. In addition, the temperature sensitivity of most polymers is a function of their chemical composition and arrangement.
Polyether ether ketone (PEEK) is a high-temperature thermoplastic polymer that exists in a crystalline form (Nicholson 2006). It is an aromatic compound implying that it contains a benzene ring in its structure. PEEK is also a linear homopolymer meaning that the repeating units making the polymer are similar (Kurtz 2012). One molecule of PEEK contains about 100 monomers with a molecular weight that ranges between 80,000 and 100,000 g/mol (Kurtz 2012). PEEK belongs to the PAEK (Poly arylene ether ketones) polymer family frequently used for orthopaedic and spinal implants (Kurtz 2012).
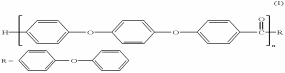
Physical Properties of PEEK
According to Boakye et al., PEEK has an elasticity that is similar to that of bones (2005). Unfilled PEEK biomaterials have an elastic modulus ranging from 3 to 4 GPa, which can be customized totally with the elasticity of the cortical bone (Kurtz 2012).
The melting point of PEEK is 334 oC. At temperatures of 700 oC and below PEEK undergoes a single-stage thermal decomposition (Krzysztof & Njuguna 2005). The thermal degradation is instigated by arbitrary homolytic scission of the carbonyl or ether bonds found in the polymer chains. The outcomes of the scission can volatilise if they display adequate mobility. Cyclisation to benzofuran derivatives can also take place. According to Krzysztof and Njuguna, oxidative environments greatly diminish the thermal stability of PEEK (2005).
The heating of most polymers leads to three key transitions, which are “the glass transition, melt temperature, and the flow temperature” (Kurtz 2012). However, PEEK undergoes an additional transition known as the recrystallisation transition. Polymer chains exhibit the behaviour of brittle glass at temperatures below the glass transition. At such temperatures, the polymer chains do not have adequate energy to slither beyond each other. The only way for the material to act in response to mechanical stress is by stretching the covalent bonds in the molecular chain (Kurtz 2012). The glass transition temperature for PEEK is about 143 oC. A fascinating fact about PEEK is that it remains ductile and flexible below its glass temperature.
Increasing the temperature beyond the glass temperature escalates the mobility in the amorphous zones within the polymer. At this point, secondary intermolecular forces such as the van der Waals forces affect the flow and movement of the polymer chain (Kurtz 2012). A polymer can form crystals at temperatures above the glass transition if it undergoes a rapid melt in its preceding history. This trait is useful to scientists in providing an idea of the processes that substances undergo. Raising the temperature of a substance beyond its recrystallisation temperature melts the tiny crystals in the polymer. Differential scanning calorimetry (DSC) is used to quantify “the melting behaviour of semi-crystalline polymers” (Kurtz 2012, p. 4). It establishes the magnitude of heat necessary to raise the temperature of a sample of polymer.
A DSC trace for PEEK reveals that the recrystallisation peak for an annealed rod is about 150 oC. This is the heat required to form crystals when the material is heated beyond the glass condition. In addition, a DSC curve shows that the peak melting temperature for PEEK is 343 oC. According to Kurtz, the melting temperature is an indicator of the thickness and flawlessness of crystals (2012). Thick and well-shaped crystals melt at higher temperatures compared to smaller crystals without perfect shapes. Heating PEEK beyond the melting temperature causes it to undergo a flow change (or flow transition), which is usually around 390 oC (Kurtz 2012).
PEEK is insoluble in most solvents and is resistant to damage by chemicals and radiation. PEEK absorbs more than 1000 megarads of radiation without displaying significant damage (Massey 2005). According to Massey, PEEK can resist dose levels above 10,000 megarads of alpha or beta radiations without affecting its physical properties (2005).
PEEK is compatible and blends well with most of the substances used as reinforcing agents to form a composite. Such substances include glass and carbon fibres. A composite is a substance comprising two or more separate phases, “each retaining unique physical, bioactive, and mechanical properties, bonded together by an interface” (Kurtz 2012, p. 5). The incorporation of carbon and glass in PEEK increases its power and rigidity. Carbon fibres form a powerful boundary with PEEK, which transmits stress between the polymer matrix and the fibres efficiently (PEEK (polyetheretherketone): Aetna plastics, n.d.).
Adding 30% glass fibre to PEEK immensely diminishes the rate of expansion and raises the “flexural modulus” making such a blend excellent for structural uses requiring high strength, rigidity, and stability (PEEK (polyetheretherketone): Aetna plastics, n.d.). The high strength per mass of PEEK makes PEEK an appealing material in industrial applications.
Chemical Properties of PEEK
PEEK shows outstanding resilience to numerous organic and inorganic compounds. Most of the solvents used in high-performance liquid chromatography (HPLC) are compatible with PEEK. Concentrated nitric and sulphuric acids are the only solvents that can attack PEEK (Properties of PEEK, polyetheretherketone, n.d.). However, it is possible for PEEK tubing passivating a system to endure 20 to 30% nitric acid.
Other chemicals such as dimethyl sulfoxide (DMSO), methylene chloride, and tetrahydrofuran (THF) can cause puffiness in PEEK. At temperatures of 200 oC, PEEK has high-quality resistance to chemicals such as sodium hydroxide solution, liquid ammonia, sulphur dioxide gas, carbon monoxide gas, methane, 50 % ethylene glycol, and phosphoric acid (Properties of PEEK, polyetheretherketone, n.d.). At low temperatures of 20 oC, PEEK displays superior resistance to chemicals such as acetic acid, acetaldehyde, anhydrous ammonia, aromatic hydrocarbons, boric acid, calcium hydroxide, and cyclohexanone among many others (Properties of PEEK, polyetheretherketone, n.d.). However, it is not recommended to use PEEK at 20 oC in chemical solutions containing bromine, aqua regia, liquid chlorine, 100% nitric acid, phenols, and sulphuric acid (Properties of PEEK, polyetheretherketone, n.d.).
Synthesis of PEEK
PEEK can be prepared through a condensation (step polymerization) reaction involving 4-4-difluorobenzophenone and an anion of hydroquinone (Nicholson 2006). A polar solvent with a high boiling point such as N-cyclohexyl-1-2-pyrrolidone is required to perform the reaction. Step polymerization occurs when functionally substituted monomers are condensed. Bifunctional reactants are used in synthesizing products with a high molar mass, whereas monofunctional substances regulate the reaction.
Trifunctional compounds contribute to the production of cross-linked or branched polymers. The mechanism involved in the synthesis of all PAEK is aromatic nucleophilic substitution in a reaction involving “activated aryl dihalides with aromatic di-phenolates in a dipolar aprotic solvent” (Synthesis of aromatic polyketones via soluble precursors derived from bis (α-aminonitrile) s, n.d.). The Friedel-Crafts method or electrophilic acylation of aryl ethers can also be used.
The initial endeavour to synthesize PEEK utilizes DMSO and NaOH in a polycondensation reaction involving bisphenolate and activated halides. However, this method only produces PEEK with low molecular weight because high molecular weight PEEK is insoluble in DMSO. The use of diphenyl sulfonate as a solvent solves this hitch and enables the synthesis of PEEK with high molecular weight. The key setback of the synthetic route of synthesis is the high cost of fluoro monomers. The substitution of fluoro monomers with less expensive chloromonomers does not yield polymers with high molecular weight using dihalides triggered with carbonyl groups.
The successful synthesis of high molecular weight PEEK is possible by substituting the costly fluoro monomers with activated chloromonomers (Synthesis of aromatic polyketones via soluble precursors derived from bis (α-aminonitrile) s, n.d.).
The nucleophilic and electrophilic methods of synthesizing PEEK involve extremely inhospitable reaction situations to produce high molecular weight PEEK. The use of soluble precursors in the process helps produce high molecular weight PEEK after which the soluble components are eliminated using chemical means.
Uses of PEEK
PEEK has exceptional thermal traits and is commonly used in industrial applications. Some of the uses of PEEK include “high-performance automotive and aerospace components and in printed circuit boards” (Nicholson 2006).
The elasticity of PEEK makes it an excellent structural implant. PEEK implants have the advantage of excellent strength and confer resistance with radiolucency (Boakye et al. 2005). Implants made of PEEK do not bring out inflammatory rejoinders in vivo and in vitro. This means that patients who receive such implants adapt to them easily because of the negligible cytotoxic responses. In addition, PEEK cages are suitable substitutes for anterior cervical diskectomy and fusion (ACDF). PEEK’s insolubility and long-term compatibility with living systems further make it an excellent choice in structural implants.
These traits imply that it is long lasting and does not disintegrate under the influence of the numerous chemical compounds present in the body of living organisms. The medical profession reaps immense benefits from PEEK because its use as an allograft greatly reduces the numerous threats posed by using allografts from cadavers (Boakye et al.2005).
The high-temperature stability of PEEK makes it extremely useful in making components of automotive engines, compressor valve parts, and bearings (Properties of PEEK, polyetheretherketone, n.d.).
The ability of PEEK to withstand high dosages of radiation and high temperatures also make it useful in making reusable medical constituents such as dental syringes and keyhole surgery tools (Massey 2005). It is possible to sterilize such equipment using steam in autoclaves at temperatures of 143 oC.
References
Boakye, M., Mummaneni, P., Rodts, G. E., & Haid, R. W 2005, “The poly-ether-ether-ketone (PEEK) spacer,” in Kim D. H., Vacarro, A. R., & Fessler, R. G. (eds), Spinal instrumentation: surgical techniques, Thieme, New York, pp. 246-249.
Krzysztof, P & Njuguna, J 2005, Thermal degradation of polymeric materials, Rapra Technology Limited, Shropshire, UK.
Kurtz, S. M 2012, “An overview of PEEK biomaterials” in Kurtz, S. M. (ed), PEEK biomaterials handbook, Elsevier, Waltham, MA, pp. 1-7.
Massey, L. K 2005, The effect of sterilization methods on plastics and elastomers, (2nd edn), William Andrew Inc., Norwich, NY.
Melt processible polyether ether ketone polymer n.d. Web.
Nicholson, J. W 2006, The chemistry of polymers, 3rd edn, Royal Society of Chemistry, Cambridge, UK.
PEEK (polyetheretherketone): Aetna plastics n.d. Web.
Polymer chemistry n.d.. Web.
Properties of PEEK, polyetheretherketone, n.d. Web.
Synthesis of aromatic polyketones via soluble precursors derived from bis (α-aminonitrile) s, n.d. Web.