Introduction
Fireproofing is a process through which burnable materials are made to resist fire attacks. In the construction industry, any material that is combustible is often covered with outside layers that make them less susceptible to fire attacks. To a large extent, fireproofing is meant to reduce chances of construction materials catching fire and causing irreversible damage to costly constructions. It is important for constructors to pay close attention to the kind of material that is used when putting up structures bearing in mind that it is the contents of a building that are usually destroyed during a fire attack. Unlike in the past, construction firms are today required by law to comply by set building standards.
According to N.Y. LAB. LAW § 264 : NY Code – Section 264: Fireproof Building (para. 1), a fireproof building is one constructed using incombustible materials. In other words, wood is not meant to be used structurally. However, if it is used, it has to be protected using non-inflammatory materials. Ordinarily, the discarding wood applies particularly to the interior of structures since the exterior walls are easily made incombustible.
While defining the term fireproof, most writers are very careful not to underestimate the importance of fireproof construction. Writers often strive to ensure that constructors understand what fireproofing can do and what it can not do. Typically, constructors focus on building structures that stop rather than propel the spread of fire. There is a general awareness that all buildings should be designed such that the floors and roofs act as firebreaks. By creating compartments that are resistance to fire, a fireproof building can allow occupants of a building enough time to escape. This also makes it possible for fire fighters to carry out their rescue operations more effectively. Rather than concentrating on building structures with inflammable materials, fireproofing must include mechanisms of suppressing a fire. The understanding of what constitutes best practice has, however, changed over the years prompted by increased understanding of the performance of materials and the relative value of certain design features and fire protection appliances increased.
Construction of buildings is a very costly undertaking and so much planning and energy is expended before any construction project can be completed successfully. It thus makes economic sense for constructors to do everything possible to ensure guarantee the stability of structures. It pays in the end to ensure that buildings are made to be resistance to fire. For this to happen, most people reinforce their structures using all forms of material including steel and tough concrete.
Materials and Substances used for Fireproofing
One approach that has been used over the years to build fireproof structures is the strategic choice of building material. Among others, the use of heavy timbers tends to provide structures that are firm and less affected by fire disasters. Apparently, this is due to the fact that unlike other types of materials, heavy woods burn very slowly. The woods start burning from the outside implying that it takes longer to destroy the inner parts of a building. As such, the inside part remains intact long enough to support a building under fire attack. In some cases, protective substances are used to coat building materials in order to reinforce their durability.
In fireproofing steel, several approaches may be used. Apparently, steel qualifies for a fire resistance rating if the type of protection used passes a standard fire test (Quarles para. 3). While there is no such thing as a truly fireproof building, the term has been used over the years to refer to the system used to insulate steel. Arguably, construction is done in order to fireproof the steel and the material used is referred to as fireproofing. Within the construction industry, steel that has been fireproofed is usually known as protected steel. However, steel material that has a weather protective layer is similarly considered protected. According to Brannigan (289), fireproofing of steel can be classified as individual fireproofing or membrane fireproofing. Individual fireproofing offers protection for each piece of steel in a building while membrane fireproofing does not. In one method under individual fireproofing, steel is enclosed in a structure. Concrete, terra cotta, wire lath, plaster and brick are materials that are commonly used to secure building materials from fire attacks. Alternatively, fireproofing may be applied to steel by directly spraying the fireproofing substance on to it. When membrane fireproofing is used, wire lath and cement plaster are the materials commonly used.
To ensure conformity, fireproofing is applied to meet the standards required by the local building code. If, for example, the code requires a given fire resistance on columns in a building, the designer has to select a system that has been approved by a building department. In addition to outlining the recommended standards, the building department also provides guidelines on the approach to be taken in ensuring the security of structures from fire attacks.
Ostensibly, the efficiency of fireproofing first depends on the competence of the subcontractor and then the willingness of the builder to demand quality work. It also depends on the building department personnel who inspect the original installation, and on the fire department inspectors to ensure that fireproofing and fire protection standards are not compromised. This is especially important in the case of spray-on fireproofing.
Originally, terra cotta tile was used to enclose building material (Tile Map para. 22). The cast iron columns of the Parker Building in New York City, for example, were protected with three inch terra cotta tiles. Electrical conduit was laid against the columns inside the tile and when the heat made the conduit longer, the fireproofing got torn from the column.
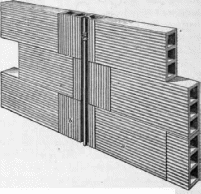
The problem occurred due to a disastrous failure of a major column in the building. Another error in the enclosure was caused by the fact that the bottom web of the beams was unprotected. After a number of failures, the error was finally corrected by the development of tiles which were shaped to fit around the steel. These tiles, called skewbacks, could easily be removed in order to access the beams during important alterations, making the fireproofing seriously defective. Fireproofing that is easily removed is usually at the mercy of the person making alterations and who often has knowledge of why the material is present. In altering an operating department store for the construction of a subway entrance, a contractor was required to first remove the protection from a major column. Approximately a hundred cylinders of propane gas were stored adjacent to the column. It is presumed that a fire attack could easily collapse the building.
With time, concrete became quite popular as a protective covering for steel, particularly where concrete floors were to be used. Seemingly, the woodwork required to make concrete provides a high fuel load and has been used in a number of serious construction fires. Concrete has the advantage of being the most permanent fireproofing because it is so difficult to remove.
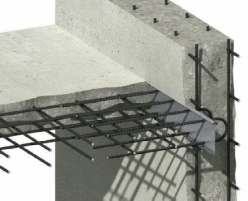
Figure 2
However, it can easily be knocked off beams and columns. Another disadvantage of concrete is its weight. In the effort to reduce the dead weight of a building, and thus its cost, fireproofing is often a tempting target. Enclosure systems of gypsum board or wire lath and plaster are an example of materials developed to save weight. Wire lath covered with cement plaster has also been used for fireproofing for many years. Some circular steel columns can be made to resist fire by filling them with enough concrete.
The search for lighter fireproofing led to the discovery of various sprayed-on coatings. Apparently, sprayed concrete performed so badly when exposed to fire. Figure 1 shows sprayed-on fireproofing coming off before a building is complete. Many combinations of asbestos and other materials were also developed. While some of these materials can successfully pass laboratory tests, some serious questions are often raised about their reliability in the field. Seemingly, when sprayed-on assemblies are tested, the steel is cleansed with carbon tetrachloride or some other solvent (Bingelis para. 3). Making sure that the material is applied at the specified thickness and density is another problem associated with sprayed-on coatings. On another front, asbestos fireproofing is under attack as there is a serious health hazard associated with its use. In the United States, it is difficult to sell a building with asbestos fireproofing. Health regulations have eliminated the use of asbestos fireproofing, and asbestos is even being removed from existing buildings. Very little has, however, been said regarding the replacement of asbestos as a coating material.
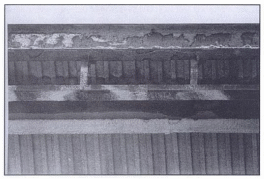
Figure 3
Membrane fireproofing is accomplished by the use of a suspended ceiling that provides a covering under the area to be protected. The cover may be of cement plaster on wire lath, but in recent years the use of a suspended tile ceiling as covering has become very popular. The steel structure requiring protection is left bare. Buildings with floor ceiling assemblies, particularly where the columns are unprotected passing through the plenum space above the ceiling, can present a serious menace to the safety of fire fighters who are, generally, not aware of the dangers. Apparently, the observations and considerations that lead to this opinion are many. The building trades sometimes disregard detailed instructions, particularly when they do not understand them or find them inconvenient. The value of listing is dependent upon the assembly being accomplished exactly as performed in the laboratory. First of all, few building inspectors have sufficient expertise and time to follow and examine every item. The ceiling is at the mercy of all owners, operators, tenants, trades people, and mechanics with reasons to remove ceiling tiles. Access to utilities and additional storage space for tall items such as rugs or ladders, are only two common reasons to remove ceiling tiles. Where the plenum space is part of the air conditioning supply, employees soon learn that displacement of a tile improves airflow at their location. Finally, there are no legal provisions requiring that the cover protection be maintained. Even if there were, enforcement would be difficult. Replacement of acoustical tile, which appears to be identical to the original tile, may be combustible, rated for fire hazard only, or rated as part of a fire resistance system. All electrical fixtures, air duct openings, and other options of entering the ceiling must be rated as part of the ceiling system. Proper fire protection and building codes require that fire ratings be maintained. Unfortunately, there are many lapses between code directives and actual practice that must be effectively addressed. Some code provisions provide for fire-stopping, particularly around columns. The use of plenum space for various services, however, makes it probable for the fire-stopping to conform to the legal fire-stopping requirements. In some buildings, the use of deep long-span trusses to provide clear floor areas creates plenum spaces several feet in height. Wasted space is often intolerable.
Not all floor-ceiling arrangements are intended to be resistance to fire. A steel bar-joist floor with concrete topping may appear to be fire resistive. In fact, it may only be non-combustible construction. Arguably, the fact that ceiling tiles left out does not necessarily mean that a fire resistance system has been violated. The building may not be required or intended to resist fire. It may be simply a non-combustible construction. In such a case, ceiling tiles are at the option of the owner and need merely to meet flame-spread requirements, if any. The building may also be of concrete construction. There are some listed concrete assemblies in which suspended ceiling tiles are incorporated, but, in general, the suspended ceiling is installed to provide a hidden void for utilities, as well as an acoustical and artistic treatment.
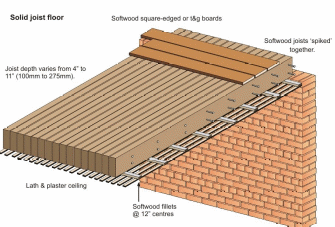
Figure 4
Water has also been used on various occasions for fireproofing (Paloma para. 6). An example is the fireproofing of internal combustion engines with water. The heat of combustion is removed from the cylinder wall by water, thus preventing any alterations. The water releases its heat to the atmosphere and thus is then recycled to the engine block. The columns in the building are usually designed to be hollow boxes. Water with antifreeze added is usually placed inside the columns to facilitate the cooling process. Columns are cross connected with piping so that heated water can circulate by gravity. Though not formerly rated, the columns probably have an almost infinite fire resistance. The structural supports of tanks containing flammable liquids present serious problems of possible collapse during a fire. It would thus advisable to design such supports as piping systems and provide for water circulation inside the pipes.
The architectural interest in exposed steel elements and the constant search for methods to reduce weight and cost, have led to a design in which important steel elements are located out of reach of fire.
Fireproofing Costs
By and large, building fireproof structures is a very costly affair. In addition, the principle upon which such buildings are constructed is not easily adaptable for the common purposes of life. In London, fire disasters prompted the government to pass laws requiring construction firms to include specific materials in their construction. There have, however, been numerous efforts to look for less expensive and more practical ways of constructing fireproof buildings. According to Webb (para. 1), labor and material costs fall under different categories.
Labor costs for fire-stopping installations are calculated based on the quantity of material that can be installed by a single individual per day. Consideration must be given to critical factors that affect productivity, such as accessibility or room to perform the work. Productivity for fire-stopping of a penetration can range from 8 to 20 units per day per individual installer. The amount of fire-stopping material installed by a single installer, however, depends on individual conditions.
Labor costs for sprayed fireproofing are based on the production of the crew and the equipment (Services para. 4). Apparently, productivity varies based on the application of sprayed fireproofing. Other cost considerations include accessibility, surrounding conditions, and staging requirements. Sprayed fireproofing can be extremely messy and requires ample time to be done. Costs for protection of supporting work of other trades must also be included, along with detailed cleanup. It is important to consider the impact of sprayed fireproofing on work done by other trades.
In the same way, materials used in construction come in different forms and their costs are generally determined based on the quantities that are required. A major cost is that of concrete and accessories used for fireproofing. Coating to provide endurance to fire is usually made from inorganic materials. Ordinarily, costs assume a 10,000 board foot (BF) job (Determining Timber Cost Basis para. 4). One BF is equivalent to one square foot. For smaller jobs, it is advisable to increase the overall cost by 5% for each 500 BF less than 10,000 BF. For scheduling purposes, it is estimated that a crew of two plasterers and 1 helper can apply between 200 and 250 board feet per hour.
Flexible doors are generally suitable for interior or exterior use and their costs are calculated based on a square foot of flexible strip area. The costs generally vary for different materials. Typical uses of flexible doors include truck dock door openings, railway car entrances, freezer doors, and positive draft protection to check the flow of unwanted air.
Conclusion
As has been explained in this paper, the desire to have fireproofed buildings has been growing over the years. This is further reinforced by legal requirements by governments in different countries. Construction firms must thus ensure that all structures are designed to meet the required standards.
Despite the steady progress made to come up with fireproof structures over the years, fireproof construction must not be understood to imply a mode of constructing buildings in which no fire can arise. It does not mean that buildings that are referred to as fireproof are absolutely safe from destruction or damage by fire. Rather, fireproof construction is the form of construction whereby only incombustible materials are used to build structures. Fireproofing is generally undertaken to ensure that construction firms follow the standards set for building structures. The cost involved in constructing fireproof structures is, however, quite high and constructors must pay careful attention to all the critical requirements in order to avoid disappointments that may be encountered once the building project is initiated.
Although most building materials are designed to be durable, it is important to note that they can be destroyed when exposed to certain harsh conditions. Using a mixture of materials and different approaches is thus recommended if fire resistant structures are to be built. Steel, for example, is known to be a very strong and reliable building material that can withstand unfavorable conditions. It, however, gets affected when exposed to temperatures that are above 5400C. It is thus advisable to have steel reinforced with materials such as concrete.
References
Bingelis, Tony. Rust Protection. n. d. Web.
Determining Timber Cost Basis. 2002. Web.
N.Y. LAB. LAW § 264 : NY Code – Section 264: Fireproof Building n. d. Web.
Paloma, Richard. Asbestos Found in City Water Tank. 2013. Web.
Quarles, Stephen P. Fire Ratings for Construction Materials. 2013. Web.
Services n. d. Web.
Tile Map n. d. Web.
Webb, Candance. Labor Cost vs. Material Cost.n. d.Web.