Background
Galaxy Paper Industry LLC, situated in the UAE, produces tissues and a variety of other related products such as Renown Select Bath Tissue, Renown Select Folded Towels, and Renown Select Roll Towel. The company also manufactures 550 sheets for roll single-ply as one of the varieties of tissues designed to address user needs and expectations. The other varieties include Decorative Floral Design and Premium performance with soft cloth feel. While various tissue production technologies such as the Advanced Tissue Molding System (ATMOS) technology exist, the company’s model is based on the Structured Tissue Technology (STT) technology.
This is in line with Wheelwright’s (2010) operations management optimization policy on tissue production that uses lean manufacturing methods. The company’s management structure hierarchical in nature with the top position held by the board of directors and the chief executive officer. Lower management departments are modeled in a classical and spreadsheet organization with each management level defined by different functions, roles, and responsibilities (Sousa & Voss, 2008). This discourse is on Galaxy Paper Industry LLC‘s operations management in the production of tissues for the UAE market.
Mission
Accordingly, the mission statement reads: to continue providing the market with superior quality paper products through innovation, conformance, and commitment.
Vision
To be looked high upon as a guiding light in terms of excellence in product quality.
Values
Passion for progress, the pursuit of perfection, conformance to the quality commitment to the environment
Philosophy
The world can be a cleaner, healthier, and greener place.
Goals
The company strives to achieve industry success by providing high-quality products by adopting a management structure and a technology platform capable of providing efficient and effective production processes.
Objectives
Provide visibility to the management in decision making with best in class manufacturing technologies
Awards/accreditations/ certifications in the outlook of operations
No awards. The company aims to grow by providing customized products to the market by listening to the customer to address their needs and expectations.
Galaxy Paper Industry LLC‘S Organizational Chart
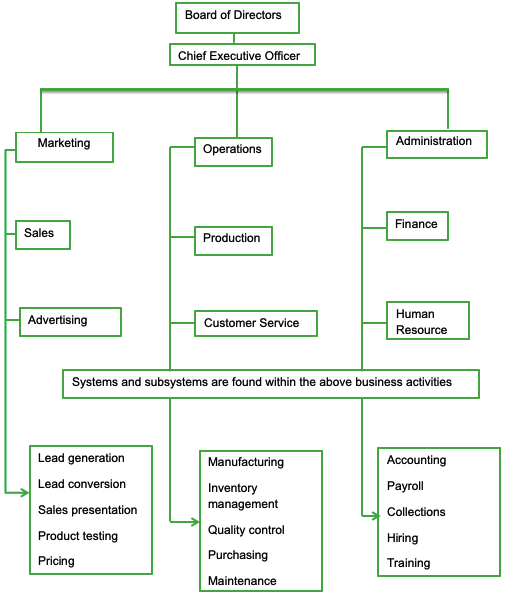
Figure 1 shows the Galaxy Paper Industry LLC’s organizational chart. The organizational chart’s composition or structure is hierarchical, which depicts the tasks, authority, and the relationship among different organizational functions. In accordance with organizational design structures by Jacobs, Chase, and Chase (2010), the company’s structure reflects the nature and functions of each department as well as procedures for executing departmental tasks in a top-down structure. According to Sousa and Voss (2008), the structure adopted by Galaxy Paper Industry LLC, in theory, combines the topmost component defined by a classical organization while the rest is a combination of the upward and spreadsheet approaches (Kalpakjian & Schmid, 2014).
The top of the hierarchy consists of the Board of Directors, which works as a cohesive group that designs strategies to pursue agreed-upon goals and objectives. This is the first decision-making organ where decisions must be agreed on by working in an environment of mutual trust, honesty, and openness that supports the entire organization. Some of the guiding principles that board members ascribe to include the ability to accommodate the other members, listen to others with an open mind, and appreciate the different opinions propagated by the others. The essential management function is demonstrated at the board of directors’ level of involvement, including establishing good public relations, personnel management activities, policy management, planning, program governance, and financial management operations.
Galaxy Paper Industry LLC has employed the chief executive officer (CEO) whose responsibility is to implement the company’s short and long term strategy besides designing appropriate methods for creating excellent shareholder value. Besides, Slack (2015) notes that the CEO communicates on behalf of Galaxy Paper Industry LLC, takes the responsibility of day-to-day management decisions, develop and implement the company’s strategy, control the company’s budget and ensure that it remains within the annual projected budget, and assess the risks the company gets exposed to. According to the organization of tasks and responsibilities by Panneerselvam (2012), the CE takes the responsibility of ensuring the effectiveness of internal controls, put on place effective systems, ensure that the company social responsibility programs and upholds standards of corporate citizenship. Also, the CEO sits in committees of the board and ascertains that the integrity of all public disclosure by the company is appropriate.
At the lower level in the hierarchy are the marketing, operations, and administration departments. At this level, the organizational structure can be defined as a spreadsheet because different departments are at the same level and directly responsible to the Chief Executive Officer (Panneerselvam, 2012). Among the other departments in this category are sales, production, fiancé, advertising, customer services, and human resource. The departments are supported at the systems and subsystems level that is found within the above business activities. The main activities mentioned include the Lead generation lead conversion, sales presentation, product testing, and pricing within the marketing function. The other subsystem activities include Manufacturing inventory management, quality control, purchasing, and maintenance. Lastly, accounting, payroll, collections, hiring, and training constitute the finance department’s bulk of activities.
The Core and Support Functions and Their Nature
Apt support is afforded to the organization through the core and support functions that make it fulfill its business goals and objectives as outlined in the mission statement. Panneerselvam (2012) classifies different functions into core and non-core. As observed in figure 1, the primary or core functions include marketing, operations, administration, sales, production, finance, advertising, customer service, and human resource (Slack, 2015). On the other hand, the support functions are classified into the systems and subsystems within each of the above business activities.
Marketing
This is defined as “marketing is the management process responsible for identifying, anticipating and satisfying customer requirements profitably.” In theory, this is to design new ways of attracting customers by identifying and providing products (tissues) that meet their needs and expectations in line with the mission and vision statements of the organization (Smith, Maull, & CL Ng, 2014). According to Sousa and Voss (2008), marketing is an important function which Galaxy Paper Industry LLC executes through the marketing department as a means to brand a wide range of products that convey messages about the company and its products. According to Sousa and Voss (2008), marketing specialists work by creating product branding and promotional messages and content uploaded on social media for advertising purposes. Employees who work for the department serve as media liaisons, develop market research strategies, and create new programs for overseeing the linkages between the company and different product vendors and agencies.
The company has adopted different marketing strategies to reach the market and take tissue products to consumers. This includes Close Range Marketing (CRM), where text messages are sent to the target market through their mobile phones. Besides, the company uses relationship marketing to build a relationship with the consumers and increase consumer expenditure. The approach has proved quite successful in increasing the marketing share for its product san has led to a positive brand image (Slack, 2015). A close assessment of the company’s marketing plan shows that it combines different marketing strategies for market penetration and product branding. The strategies include email marketing, which is done by sending emails, especially to potential customers. PR Marketing is done in combination with other marketing strategies to develop effective public relations with customers. In theory, many marketers use the media and other broadcasting methods to reach customers and propagate a good image of its products (Slack, 2015). Besides, the company uses seasonal marketing techniques to reach new markets and customers. However, seasonal marketing is used to a minimal extent.
Product/service development function
This is an essential function the company uses to manage to be assured of becoming successful in its products. The company has invested in well-trained marketing management staff that collects, develops, and maintains a good quality product mix. According to Sousa and Voss (2008), a skilled marketing team uses tools such as affinity diagrams to organize different ideas and data for better and effective product development. Once the right products have been released into the market, the companies put in place programs for monitoring the products’ performance, the response rates of the customers and sales channels, the demand for the products, and better still the return on investment (Wheelwright, 2010). The rationale is to measure market response levels and determine whether the profits are sustainable. In accordance with the marketing concepts proposes by Wheelwright (2010), each time the company launches a new product, the marketing team monitors the intensity of competition and the revenue generated to determine the appropriate product mix, product line (by price and distribution channel), width (number of substitute products to offer to the market), and depth (the distinguishing characteristics that are unique to each tissue).
It is important to stress that the quality function deployment plays a significant role in the product planning mix, where tissues are designed to meet unique customer attributes and production, parts, and process planning matrices.
Operations function
The operations function in Galaxy Paper Industry LLC is defined by several theories and practice activities. In theory, Sousa and Voss (2008) note that the function defines the processes used to produce products and services. Operations are concerned with the organization’s core function, which includes the production of tissue papers for the end-user or consumer.
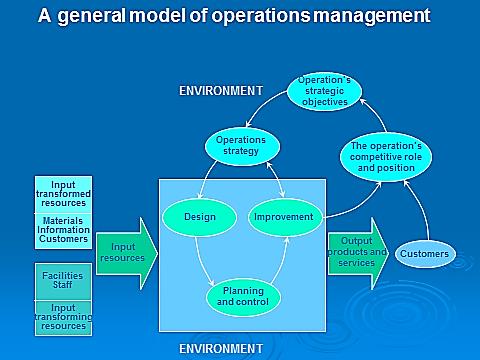
Figure 2 depicts a conceptual framework for inputting the resources necessary for the transformation process to produce the desired end products for the end-user, who is the customer. Typically, the framework consists of input transformed resources, facilities, staff, and input transforming resources, converted into the input resources.
According to Sousa and Voss (2008), the production environment consists of planning and control, design, improvements, and operations strategy. The whole process then transforms the resources into tissues as finished products that are supplied into the market. Typically, strategic objectives are laid down, and product positioning is done on the end product.
The accounting and finance functions
Sousa and Voss (2008) note that the accounting function enables the company to aggregate financial transactions on a day to day basis in a general ledger to make the necessary accounting adjustments and develop appropriate trial balances to create basic accounts that show the profitability of the company. Typically, the process results in the balance sheet and profit and loss statements that enable the company to make future short term and long term strategic decisions. Often, the company uses a global accounting standard double-entry system to unify different accounting functions together.
Usually, the accounting function consists of assessing and determining the accounts payable, which enables the company to establish good working relationships with vendors and identify appropriate opportunities to save money, such as discounts offers on raw materials (Wheelwright, 2010). Besides, the department keeps track of revenue and accounts receivable. This is to ensure that invoices are acted upon to make actuate financial records for the organization’s smooth running. To carry out the finance department’s activities, the company has employed an accountant, who undertakes the roles of the accounting manager and carries out chief counting activities and accounts supervision.
Companies find the finance function as essential because those working in the department usually prepare and issue the company’s audited semi-annual and annual statements, evaluate the management accounts monthly, and put structures and techniques to comply with the tax laws and financial reporting standards of the UAE. According to Slack (2015), the function is responsible for developing internal and external controls besides ensuring that the organization maintains the management information system effectively.
The human resources function
An organization’s critical assets include trained employees. Galaxy Paper Industry LLC, the tissue producing company, ensures that it employs appropriately skilled and trained personnel to carry out the management, production, financial, and other control activities (Slack, 2015). One activity that enables the organization to fulfill its obligations is to flawlessly carry out the recruitment and selection functions. The human resource function creates an appropriate job description document that is used both during the recruitment and selection process and in assigning duties and responsibilities to the employees. Besides, the human resource function provides opportunities for career development through training and development programs designed not only to motivate employees but also to provide them with the hope of future career opportunities.
Another activity is performance appraisal. The company conducts performance appraisal activities regularly to determine the training and development needs of the employee. This is designed to identify existing gaps so that new skills can be imparted to perform better (Slack, 2015). Here, the performance appraisals system’s objective use is to evaluate employees’ ability to fulfill the job requirements. Among the performance appraisal skills, evaluation approaches include the ability to bring out the best in employees, make optimum use of the employees and their qualifications, develop an environment for motivating employees, and encourage their participation in the organization’s core activities besides using effective conflict resolution mechanisms.
The results show the technical skills requirements by building a strong sense of teamwork and practical time management abilities and the ability to convey sincere appreciation at every opportunity (Slack, 2015). The department is responsible for amicably managing disputes besides developing good public relations. An assessment of the company’s human resources function shows that its scope consists of the procurement, maintenance, establishing good industrial relationships, and employee remuneration (Slack, 2015). Also, HR ensures that the rights people are employed to do specific jobs. The department also designs appropriate methods for motivating employees besides putting in place safety laws and ensuring that the labor practices within the organization are acceptable.
Operations Management and Its Role
Previously, operations management was called production management before the name was changed to that it is today. This function is defined “as the process whereby resources, flowing within a defined system, are combined and transformed by a controlled manner to add value in accordance with policies communicated by management” (Panneerselvam, 2012). It is imperative that, in theory, the definition consists of systems, resources, value addition activities, and transformations. In theory, operations management entails the decision-making practices of identifying the activities, decisions, and responsibilities necessary for optimal execution of the company’s tissue producing activities. Here, the company uses the operations manager to define the cost-effective way of using the available resources to manufacture tissues to ensure optimal return on investment and generation of sustainable profits that are sufficient to run the company (Panneerselvam, 2012). On the other hand, the system consists of the components that work together to achieve the organization’s long-term and short-term objectives. It is essential to ensure that each element makes an appropriate contribution to the organization.
The resources are modeled in figure 2 are the people, capital inputs, and the production processes (Panneerselvam, 2012). A summary of the functions shows that external suppliers provide raw materials for the production of the tissues for making the finished products.
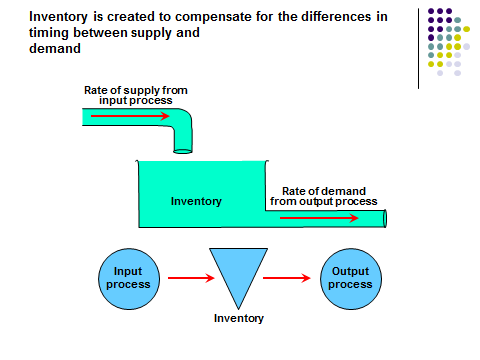
Operations management is an essential component because it enables the company to add value to its products by controlling the transformation process (Panneerselvam, 2012). This resonates well with the theoretical position that the customers are ready to pay for the products, which are taken through the activities transform the tissues into new and appealing products by doing the value addition activities right in the first place (Sousa & Voss, 2008). The value addition activities enable the company to reduce wastes, reduce waiting time, reduce extra processing work, and remove defective products in time. The underlying objectives include the ability to configure different production methods and facilities for future survival, efficiency, and to effectively impart the quality dimension on each product.
Galaxy Paper Industry LLC has employed an operations manager who collaborates with the finance and the human resource manager to ensure effective inventory management.
This enables the company to keep appropriate stock inventory levels to reduce the costs, increase cash flows, optimize labor services, and enhance the supply chain systems (Sousa & Voss, 2008). Different inventory management models have been proposed. In theory, inventory is designed to compensate for any differences between supply and demand, as illustrated in figure 6.
The next inventory system is the single-stage and the two-stage inventory appropriate for the local retail and the automotive spare parts distribution methods.
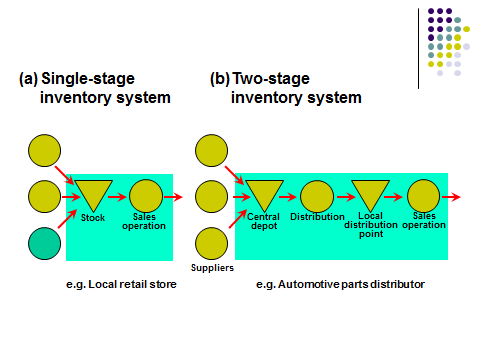
The company uses the ABC analytical method, illustrated in figure 8, by dividing the on-hand inventory into different categories according to the 80-20 rule, where different groups are managed separately (Sousa & Voss, 2008). Based on the ABC analysis, the company identifies and categorizes high-value products, constituting 70% of the high-value items into 10% by volume. According to Sousa and Voss (2008), moderate value items are categorized into 20% and classified into 20% by volume. On the other hand, small value items consist of a 20% category and 70% by volume.
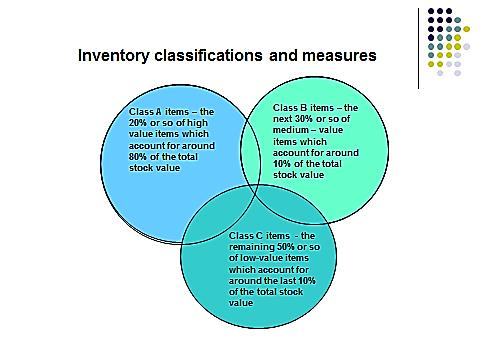
It is important to note that the supply chain function is a critical component in inventory management. The company uses the best combination of supply chain management approaches to ensure that inventory replenishment is done in time at the lowest cost. The integrated approach is widely adopted to ensure local optimization to ensure high profits. Besides, the approach enables the company to make effective utilization of existing space. Studies show that the type of inventory management system adopted by a company is used to determine the type of supply chain strategy. Typically, the low costs strategy is appropriate for situations that are designed to maintain high average utilization with minimal inventory. The response strategy provides the foundation for investing in excess capacity utilization and allows for buffers to be created, ensuring a constant supply. On the other hand, the differentiation strategy is used to avoid obsolescence by creating modular processes to address market needs.
Types of Production Processes
A list of the five types of production processes includes project, continuous production, mass production, batch production, and job-shop production. Each of the production processes is uniquely characterized by specific advantages and disadvantages that make each of them applicable in particular manufacturing environments.
Job-shop
The job-shop is characterized by the processing of a few products designed to meet the specific needs and expectations of particular customer segments or individuals according to the customers’ technical specifications. Typically, the production process consists of different machines in different rooms customized according to job demands and unique technological requirements (Sousa & Voss, 2008). The production is characterized by low volume and high variety products, use of facilities and machines classified as general-purpose, and require highly trained and skilled personnel. Job-shop is appropriate for environments that manufacture woodwork products and metal fabrication shops. However, this method’s main disadvantage includes complex production planning, significant space requirements, costly because of frequent changes, and higher inventory costs.
Batch Production process
Batch Production is characterized by shorter and single production runs that are, in theory, less than 100 units with the possibility of switching to new products in the batch that follows. This implies that the production equipment is designed with a high degree of flexibility to accommodate late changes in the production process (Sousa & Voss, 2008). In the company’s context, the batch processing method is inapplicable because of the several pitfalls associated with the technique, such as the complexity in material handling and higher inventory costs.
Project method
The third approach is the project method. This method is characterized by low volume operations but highly flexible approaches. The production is done in one place where the processes are done, and the materials brought to the place. This approach is used in situations such as large machinery production, shipbuilding, and bridge construction (Sousa & Voss, 2008). An evaluation of the project method shows that it is inappropriate for the production of tissue papers. However, the mass production process is appropriate for the manufacture of tissue papers.
Mass production
It is imperative to note that the company has adopted the mass production and continuous production processes combined with batch production, and job-production approaches (Sousa & Voss, 2008). Mass production is an appropriate model for the specialized production of tissues because the production processes are standardized, making them less expensive.
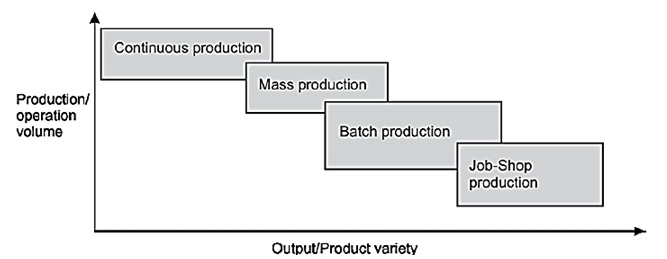
Also, the approach allows for the use of dedicated special purpose machines to fulfill the production function. This leads to lower process inventory, automated material handling, easy control of the production processes, and shorter production lifecycles (Sousa & Voss, 2008). The results include lower production costs per unit, use of less skilled and cheaper labor, effective implementation of line balancing because of higher capacity utilization, reduced cycle time that leads to higher rates, and high production volumes. The overall expectations are higher efficiencies as well as low investment costs with higher profits.
The 4 Basic Types of Layouts
In theory and practice, Wheelwright (2010) and Slack (2015) note that four types of layout are widely applied in the design of company production machinery. Plant layout, according to Moore, is “plant layout is a plan of an optimum arrangement of facilities including personnel, operating equipment, storage space, material handling equipment and all other supporting services along with the design of the best structure to contain all these facilities” (Wheelwright, 2010). Accordingly, plant layout objectives include the facilitation of the organizational structure, optimum use of the production time, and ensure employee convenience, safety, and use of flexible manufacturing approaches. Also, flexible and streamlined flow of materials, The layouts include process layout, fixed layout, product layout, and reduce the cost of handling materials, and effective utilization of resources such as people, equipment, materials, and space. Each of the layouts has unique attributes and application areas.
Process layout
The layout is appropriate for batch production, where machines designed for similar production activities or functions are grouped in one area to optimize the production processes and procedures. According to Wheelwright (2010), the process layout’s key features are the short path the material used in the production of tissues flow through. In the case of Galaxy Paper Industry LLC Company, the flow paths of materials are from different functional areas optimized by the use of a different layout. The rationale is that this method is appropriate for low production volumes, which is not the case for the company. In practice, this method applies to the job-shops that specialize in low volume products designed to meet specific needs with specific technical details.
However, the key advantages of the process layout are better utilization of machines, low investments in fewer machines, the ability to afford flexibility in employees and processes, and better optimization of production facilities. However, because of the limitations associated with the layout process, the Galaxy Paper Industry LLC Company does not use its production processes (Sousa & Voss, 2008). Among the limitations associated with this method are long movements and backtracking, poor mechanization of material handling capabilities, lower levels of productivity because of a large number of set-ups, longer processing time and inventory activities, longer throughput, and capital and space are always tied up by the work in processes.
Product Layout
This method is appropriate for a layout consisting of machines and auxiliaries organized according to the functions performed by each component. The arrangement is based on the volume of goods produced and required in accordance with the desired product flow efficiency. In this case, special purpose machines are used to fulfill the production function (Sousa & Voss, 2008). The key advantages are characterized by a smooth and logical flow of products, less throughput time, low material handling costs, ability to manage production by less skilled employees, low space usage, and fewer space requirements, and low in-process inventory costs. It is also easy to avoid idle machines because the layout provides the flexibility to do line balancing. Also, high volume productions justify the reason for an additional production line, which makes the investment expensive (Sousa & Voss, 2008). However, the layout is inappropriate for use in a situation where continuous production is required. This is because due to the possibility of severe limitation where a machine could break down and bring to a standstill the rest of the production process. Besides, the layout requires high investment costs besides lacking in flexibility.
Fixed-Position layout
Different layouts are appropriate for various processes. Typically, the fixed position, in theory, is more suitable for the project type process. This is where the main production components are put in one place so that the resources used for production purposes are quickly brought in (Sousa & Voss, 2008). the sequence of operations and the batch size are critical components to consider when designing the fixed-position layout. To optimize the layout and increase production efficiency, two approaches are crucial in implementing the system (Sousa & Voss, 2008).
The first approach in the process is to determine the group and family of components installed in the production layout. That is followed by arranging the parts according to the production needs and the family of components. The overall outcome is a representation of small production units within the manufacturing plant. It has been established that the approach is appropriate when the company wants to reduce the time taken in production planning (Sousa & Voss, 2008). This type of production layout is appropriate for shipbuilding and the production of other heavy components and machinery. The method is cheaper besides allowing for greater flexibility, job enlargement skills, and providing the foundation for worker specialization.
Cell Layout
Often referred to as group layout, this method is suitable for flexible manufacturing where the sequence of operations and batch size are essential. Usually, a group of components is aggregated into one area to be optimized in the production processes (Sousa & Voss, 2008). Each cell is designed according to the production process needs. It is crucial to design the cells in such a way as to ensure effective flow control and movement of resources. A critical analysis of the layout shows that it combines the process layout and the group layout and combines the advantages of both layouts.
The basis of group layout is group technology. This aims to use different cells in the production process by factoring each cell’s needs to design and arrange the cells according to the production needs. The objective is to optimize the production processes and minimize the costs associated with time and material handling procedures (Sousa & Voss, 2008). It has been noted that this type of layout is appropriate for minimal material consumption in its design and implementation. It is also imperative for the managers to ensure that the materials and equipment are utilized appropriately for the cost benefits to be realized. One of the critical objectives is to ensure that the cost of handling materials is kept to a minimum. A typical material handling optimization process is conceptualized in figure 4.
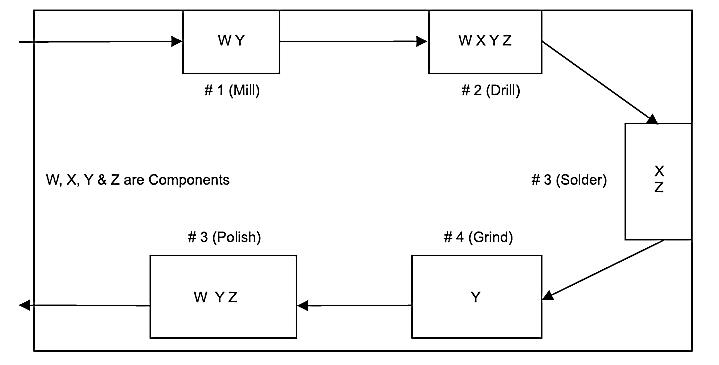
Figure 4 is a conceptual view of the group layout. The layout shows the processes and accompanying activities in each step of the component production process. Milling is done on the product in the first step, which is followed by the second step (WXYZ), where the milled product is drilled before it is taken to the third step (XZ) where soldering is done. Subsequent steps include the grinding of the product (Y), which is followed by the final step (WYZ) of polishing the product before the final product is released for sale and use in the market. The approach has various advantages, including the ability to make reliable estimates, highly efficient production processes that utilize the machine and layout functions, less paperwork and low production time, effective component rationalization and standardization, and better customer service provision. However, the main disadvantages with the layout are higher overall costs, sometimes it involves a lot of paperwork, and the nature of work movement and work-in-progress can be restricted by the layout design.
Manufacturers do not recommend this type of layout, especially for mass production purposes. Besides, the layout is meaningless for the production of dissimilar products.
Galaxy Paper Industry LLC Company Layout
A critical assessment of the production processes and machinery layout adopted by Galaxy Paper Industry LLC Company shows that it has settled on combining the process and product layouts. The layout was done according to the layout principles in accordance with the principle of integration, the principle of minimum distance to optimize the movement of materials and other resources, the principle of cubic space utilization that enables the company to utilize both the vertical and horizontal space, and the principle of flow, which is appropriate for the optimization of movement nether the forward or backward directions. The other principle that has been optimized is flexibility, which allows the company to change the layout without many costs because of new changes to the production processes or new machinery. A close assessment of the layouts adopted by the company reveals the principle of safety, security and satisfaction, and minimum handling of materials and products.
The main advantage of the combined layout is that both layouts’ advantages are optimized, and it allows for the production of tissues with different sizes and shapes. Machines are laid out to allow for different processes to be grouped to make a cost-effective production process. Typically, process and layout optimization is due to line balancing that is done in a precedence relationship. This allows for behavioral responses to be observed in terms of job satisfaction among employees and a reduction in cycle time, which depends on the desired output rate.
Galaxy Paper Industry LLC Company Transformation Process
In practice, the transformation process in the production of tissues and the paper’s winding is done to make the transportation process flexible, effective, and cost-effective. Typically, the conversion includes the raw materials’ embossment to make it soft and induce absorbency properties. The process is followed by a perforation to separate the resulting sheets and rolled into the required thickness and sheets to complete the process. However, typical analyses of the company’s transformation activities in the process and product layouts are discussed here in detail.
Based on the product layout paradigm, in the first step, the company has designed the assembly line in a way that defines the way materials are handled for the transformation process to be effective. One observes an assembly line which consists of interlinked material handling phases that allow pacing and processing time to be optimized for each workstation. The works are strategically positioned within the plant to allow for easy and efficient movement of raw materials and products. The raw materials consist of recovered fiber that is collected as post-consumer wastes. Additional raw materials are usually obtained from Chemi-thermo-mechanical pulp (CTMP), mechanical pulp, the thermo-mechanical pulp (TMP), and the chemical pulp sulfate process. This is done before the bleaching process that converts the products into high-quality outputs.
The layout can best accommodate the transportation and movement of materials from one point to the next to be done in real-time. A critical analysis of the assembly line shows that the aspects of the process layout principles have been amalgamated with the product layout during the design process and equipment implementation process. The design aspects shown include functional work centers and an estimate of the time required for the movement of people and materials across the processing plant resulting in a generally accepted layout. The layout accommodates belts, conveyors, and workstations that are characterized by sitting and standing employees.
The ranges of produced and conveyed products include facial tissues and hygiene tissue rolls, among others. A more important consideration is that each stage of the production process is loaded to ensure optimum production facility utilization. A typical example is an operation that produces soft tissues. Estimates show that the first step or operation takes 3 minutes for each unit to execute the transformation activity before moving to the second operation that takes 1 minute. The third step requires that the transformation will take 2 minutes to complete.
Production process
In line with the framework, the Galaxy Paper Industry LLC’s operations framework consists of the raw material acquisition process, which in this case, is cellulose, which is taken into the paper mill boiler and converted into the paper before it is dried using steam. Besides, the primary inputs include personnel and finance, as depicted in figure 3.
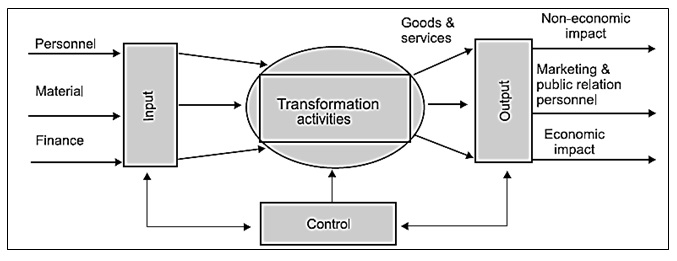
Figure 3 shows the production system that changes the inputs through the processes of conversion into outputs. As illustrated in figure 4, the inputs are not only raw materials but employees who execute the input activities, materials, machines, information, and capital. However, figure 2 illustrates the transformation activities and the control function that is detailed in figure 4, which shows the transformation processes include product design. This function is under the product/service development of the company (Kalpakjian & Schmid, 2014). The transformation process includes product design, planning, control, and maintenance. Products are designed to address the needs and exceed customer expectations. However, Galaxy Paper Industry LLC provides the necessary control mechanism to ensure inventory, quality, and cost controls remain within the company budget. The company has implemented the control function to ensure that each production process’s objectives are achieved, as shown in figure 4.
In theory, the transformation process is done to ensure that the outputs have more value than the inputs. The outputs are the finished product, while the inputs are the raw materials used in the transformation process. It is imperative to note that at the transformation process point, the series of activities that occur within the industry include product design, process planning, production control, and maintenance. The company ensures that the ratio of the input to the output is high on an hourly basis. This translates to high productivity and better transformation efficiency.
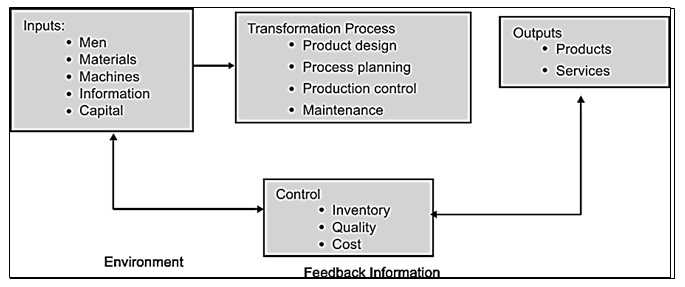
Product design
A visit to the industry allows one to go around and make observations on the key processes that transform raw materials into finished products. One of the key areas of interest vital to the transformation process is the product design phase (Kalpakjian & Schmid, 2014). The importance of this phase cannot be underscored. The rationale is that a wide range of products is manufactured by the company with unique features, which are meant to address specific customer needs and expectations (Johnston & Clark, 2008). The product features are integrated into the tissues based on market needs. Market needs are identified by collecting data through the marketing department on the tissues’ technical details and the needs they are designed to address. Examples include facial tissues that are designed for facial cleaning, as shown in figure 7.
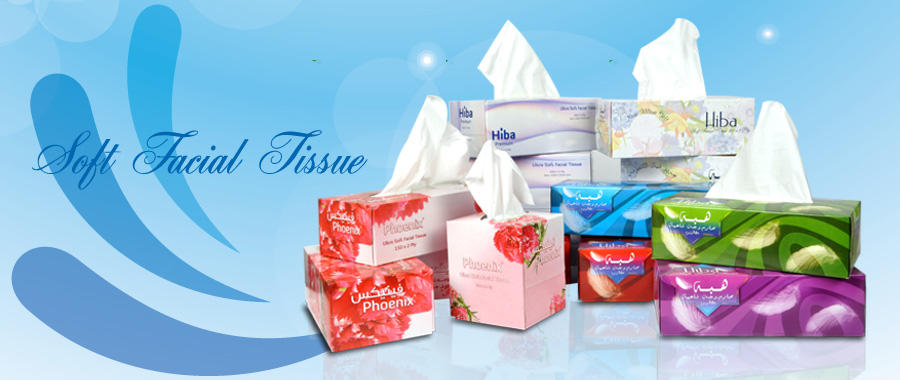
It is imperative to note that the transformation process creates a wide variety of soft facial tissues to respond to different customer segment needs and expectations. The link between customer needs and the production or transformation activities merge to meet the company goals and objectives.
Process design
Processes are conceptualized as transformation steps that convert inputs into the finished products under the transformation process (Wheelwright, 2010). The key elements that the company has factored into processes as the man divers of the process design include short, efficient, and effective process phases for the conversion of raw pulp into different types of tissue (Kalpakjian & Schmid, 2014). The company’s operations manager provides accurate data on process layouts, which shows the workflow and controls. Each workstation is designed to perform specific functions critical to the production of tissues and a variety of other tissue papers.
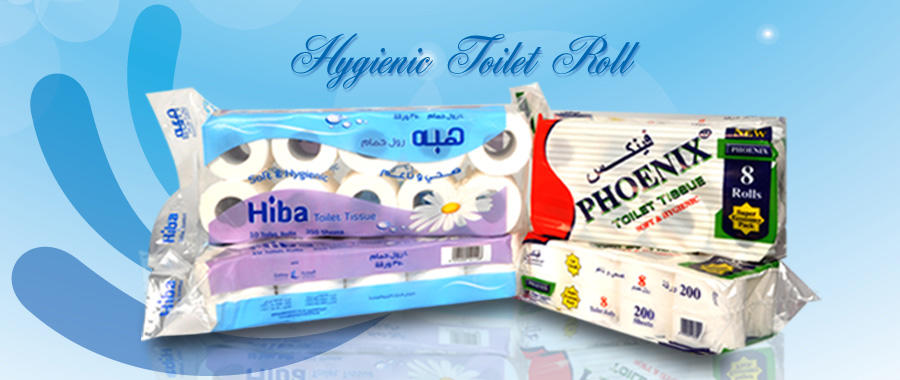
The pictures indicate the samples of the tissues manufactured by the company.
An assessment of the company’s production processes shows that the production objectives, which include manufacturing of the right quality tissues that meets and even exceeds customer needs and expectations, which are offered at competitive prices have been achieved (Johnston & Clark, 2008). The other objectives that have been fulfilled include the timely replenishment of the supply chain system, production of the right quantities to replenish the supply chain systems, and ensuring that the company establishes and incurs the right manufacturing costs. A typical example of one of a variety of products by the company is shown in the picture.
Production planning
A detailed analysis of the production processes shows that production planning is done in advance to set the exact approach used to handle each element in the production line. The raw materials are handled according to plan and ordered for optimal utilization of machinery and the process flow. It is imperative to note that the principle of planning is applicable at this point because planning takes center stage before employees and machines get engaged to work on the plan. The entire process includes “Planning, Routing, Scheduling, Dispatching and Follow-up” (Kalpakjian & Schmid, 2014).
Planning is done to ensure that all activities performed by employees and the entire organization are defined well in advance before they are executed and the manner and approach of executing the production activities (Johnston & Clark, 2008). The planning function plays a critical role in the production of tissues because it provides an efficient path on materials transformation and handling at each stage of the conversion process.
On the other hand, routine activity is a critical component in manufacturing tissues within the company production plant because each step in the entire process consumes time and other resources. However, the raw materials and products are processed most efficiently and shortly to ensure that the routes’ optimal use is achieved (Kalpakjian & Schmid, 2014). On the other hand, the company schedules the production activities according to the time and resource requirements and the prevailing demand for the tissues and other products in the market to fulfill finished product replenishment requirements. This is in accordance with the movement of raw materials as inputs and finished products as outputs. Besides, the company has designed its processes such that dispatches of raw materials into the production process are done in accordance with activity schedules. The beginning of each new activity is in accordance with the start and end of each production process.
Quality assurance
Galaxy Paper Industry LLC is always conscious of the quality of its products. One of the key components that have been integrated into the process is quality control. Here, quality control can be defined as ‘a system used to maintain a desired level of quality in a product or service.’ Typically, the process is to ensure that the quality of tissue paper meets varied customer needs. The quality enhancement activities include coloring, appropriate printing, and a better creping process. Besides, the fiber fragments are designed into the tissue as a property that improves the production process’s quality. The other key quality improvement activity is the wet end process designed to achieve a consistency of 0.15% – 0.25 % solids in a piping process. The entire quality control process is designed into the product manufacturing steps to increase the company’s income, reduce the probability of losses occurring, reduce the frequency of defective products, and ensure that the products satisfy customer needs. Besides, the quality control process is in place to ensure better confidence and company reputation.
The other activities that occur within the production processes include maintenance management. This is done under the operations management department to ensure that machinery runs with the minimum breakdown and excellent working conditions. In theory, this is designed to make the machines operational with optimum capacity at minimum costs. This is also designed to make the machine operations and performance optimal.
Product testing
Delivering products that are safe, compliant, and effective is one of the company’s objectives. Despite not being regulated by the government to a big extent, the company is self-regulated and ensures that company products are safe and of good quality. To ensure that the product meets the quality requirements, its products are subjected to continuous testing to meet the quality requirements. The testing process consists of physical testing strategies by evaluating the mechanical properties of the tissue papers. Chemical testing is done to ensure appropriate ingredients and the right chemical combinations to measure the required product standards. This is in accordance with the requirements for chemical standards requirements. The company conducts microbiological testing to determine the degree of microbial contamination and the percentage of yeast, pathogens, bacteria, and mold in the products. Ecotoxicological and biodegradability testing are done to determine the degree of compliance with the UAE’s environmental laws and regulations and the global market.
Packaging testing is done to determine the type of boxes as well as other packages the company uses. Cost, aesthetical appearance, solid wastes, and ease constitute the factors to consider when conducting a packaging test. Besides, auditing and inspections are done to ensure that proper controls and are practiced and followed appropriately. Both quality and quantity are factored into the process, and such audits are done on the environment, the factory processes, and social audits. Quality control is an ongoing process that enables the management to provide the quality products and processes in each production step.
Material Processing Technologies
Material processing and management and associated technologies are designed to fulfill the production objectives of tissues as a core manufacturing function. Typically, material management is “the function responsible for the coordination of planning, sourcing, purchasing, moving, storing and controlling materials in an optimum manner to provide a pre-decided service to the customer at a minimum cost.” This defines the scope of material management and handling scope. However, various material production technologies have been integrated into the tissue manufacturing process. In practice, the advanced tissue molding systems are widely used manufacturing systems for soft tissue that has been high rate because it leads to 35% energy savings and requires very low investment costs. The Advanced Tissue Molding System (ATMOS) module works as a normal conventional crescent works.
A special vacuum is used to provide maximum dewatering of the products after it has passed through the production stages. There is a very small movement of the component used in the production processes. This is done to ensure that little movement and time is spent in the movement of material and products within the plant for maximum utilization of space and machinery. The plant layout is based on the lean manufacturing concept, where material and technologies are optimally used for production purposes. An assessment of the lines of production shows that ATMOS lines are designed with a 2,800 mm single line having a width of 5,600 mm, which allows the machine to perform various production and tissue upgrade functions. This allows for the production of the normal, premium, and first-grade tissues. The advantage of technology is that it is widely used and adopted because of the low cost of investment and flexibility.
Structured Tissue Technology (STT) has been in use since 2005. A company known as Metso has been quietly using the technology for many years despite very little is being known about it. The technology can produce a wide range of commercially saleable tissues as well as those for conventional use. Besides, the operational efficiency of the technology is high, as well as being cheaper. Typically, the Galaxy Paper Industry LLC company uses this technology because it has been around for a relatively long time. The key advantage of this technology is that breakages are rare, cheaper to install, and cost-effective. The technology also uses the Kraft process in raw material preparation, fiber separation, bleaching, and tissue making.
Information Processing Technologies
In practice, different information processing technologies that serve different purposes in an organization exist. Galaxy Paper Industry LLC uses different information systems that serve different functions across the organization. The management information system was installed purposely to provide services at different levels of the organization by collecting data on daily activities based on the transaction processing system for routine business decisions. Expert systems and neutral systems are used by organizations to provide diagnostic decisions in the event of problems in decision making. However, Galaxy Paper Industry LLC does not use the system in its transactions. On the other hand, the transaction processing system enables the company to collect data on the day to day transactions, stored and processed for future use. Billing data, transaction, wages, and inventory control are executed on the transaction processing system software platform.
The decision support system has been integrated into the organization to provide support services in decision making. Galaxy Paper Industry LLC adopted the decision support system to analyze possible solutions in decision making that the company management wants to make. In theory, the system is based on the key elements, which include input data, decision-making component, and the transformational processing engine.
Customer Processing Technologies
The level and nature of interaction that technology provides with the customers and end-users classify it as customer-based technology in practice. The concept of interaction with technology emerges as either passive or active. Interaction can also be hidden or open. However, technology’s choice to use processing customers can be determined by dependability, speed, flexibility, cost, and quality. That is in addition to the technologies’ capabilities, accompanying constraints, and the cost factor. The Galaxy Paper Industry LLC has adopted an automated ADaM Customer Processing system. A screenshot of the system interface is shown in figure 10.
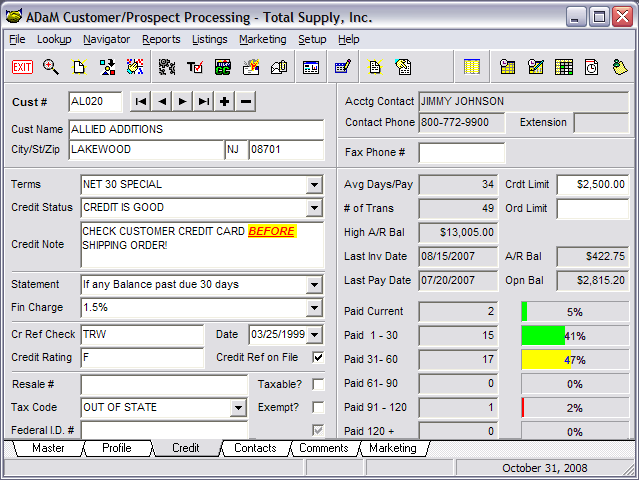
It can be noted that the interface provides a variety of capabilities, which include creating the customer profile, credit checking, strong and accessing customer contacts, viewing customer comments, and assessing marketing information. Marketing information is based on market data and the performance of various tissue brands the company manufactures.
Inventory Management Techniques
Typically, inventory is a critical component in any business and the techniques used to execute the function. Inventory management is defined as a “planned approach of determining what to order when to order and how much to order and how much to stock so that costs associated with buying and storing are optimal without interrupting production and sales” (Smith, Maull, & CL Ng, 2014). This can be interpreted to mean that inventory management uses specific techniques to solve the problems of order levels as well as order quantities.
Each technique is designed to meet the objectives, which include ensuring adequate control, ensure that financial investment in inventories is kept to minimum, objective use of the purchasing function, effective storage and handling of materials, and to ensure timely replenishment of materials. To achieve the objectives, different types of inventory management techniques are used in practice. The techniques include ABC analysis, HML analysis, VED analysis, FSN analysis, SDE analysis, GOLF analysis, and SOS analysis (Smith, Maull, & CL Ng, 2014). However, the ABC analysis is the most preferred technique in the industry because this method allows for the total inventory to be categorized into three sub-heads with each subcategory used to address specific inventory problems as they happen.
ABC analysis
This inventory technique allows for the classification of existing inventory using the annual consumption data and the value of the items. Here, ABC analysis is done by multiplying the unit cost with the number of inventory items consumed per annum to obtain the annual usage cost (Panneerselvam, 2012). This approach enables the management to make effective inventory control decisions because of the differentiated costs of each item. As stated, the inventory is divided into three groups, as shown in table 1.
Table 1.
The results are traced in figure 9.
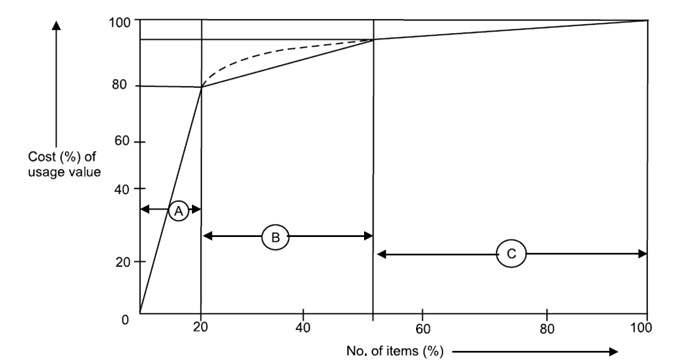
The policy control formulation, as shown below, follows an effective ABC classification.
Table 2.
HML Analysis
This is similar in classification to the ABC analysis except that the existing inventory is based on each item’s unit price. Items are listed in ascending order, making the approach appropriate for controlling consumption at the departmental levels.
VED Analysis
This type of inventory technique is appropriate for classifying critical items and how each item affects the production process and the resulting quality. According to Panneerselvam (2012), this approach is most appropriate for spare part distribution. In the classification process, vital components are assigned a V classification, and essential items are given the E classification. However, those items that are not of much value are classified into D.
SDE Analysis
This technique is appropriate where there is a scarcity of supply of items as well as availability. The concept is based on reference letters where S means scarce items, D means difficult items that are difficult to procure, and D category of items comes from distant places (Panneerselvam, 2012). However, the E category of items is that which can be easily acquired. The SDE classification is appropriate for time analysis and accurate purchasing methods.
FSN Analysis
This type of technique is appropriate for different item consumption rates, including fast-moving, slow-moving, and non-moving items classifications. The dates of issue and reception of items are considered by finding the difference to determine the items’ grouping. The approach is appropriate for determining the frequency of supply of the items.
XYZ Analysis
This type of inventory analysis technique is appropriate for use for valuation in stores. XYZ Analysis is usually used as a simple supply chain technique that works on the concept of 70%, 90%, 100% banding. The Y band class items are grouped into the 70% category, the X class is banded into the 70% category, and the class C band is categorized into the 90% category (Sousa & Voss, 2008). It is imperative to note that the items in the X category require close monitoring and tight control. In contrast, Y class requires a standard control mechanism for periodic reviews, and Z requires the least control often issues as free stock.
Technique applied at Galaxy Paper Industry LLC
A critical evaluation of the inventory techniques that have been discussed shows that the Galaxy Paper Industry LLC company uses the ABC analysis approach for inventory management. This is because the ABC analysis is an enabler that operations managers use to calculate the total spending per year based on the annual demand of the tissues, several items demanded, and each item’s unit cost for optimal utilization of resources. Here, the total cost per year is equivalent to or calculated using the formula: Unit cost * total cost per year (Sousa & Voss, 2008). This is followed by the second, where the usage of items is calculated to find the total expressed as a percentage. The formula the manager uses is as follows: % of total usage = usage of the item/total usage. The third step is to sort the items by usage by assigning each item a unique number, determining the cumulative % of items, establishing the unit cost of each item, using annual demand projections, the total cost per year, the usage as a % of the total usage, and calculating the cumulative percentage of the total (Wheelwright, 2010). A typical sample of the results of the ABC analysis process is shown in table 2 for the Galaxy Paper Industry LLC company.
Table 3.
Benefits of Lean Methods
Lean production
Companies always look for the best methods to optimize available resources existing in raw materials and machinery to cut costs and increase production efficiency by removing those activities that do not add value to the manufacturing process (Kouvelis, Chambers, & Wang, 2006). This approach has been implemented in Galaxy Paper Industry LLC production processes conceptualized in a U shaped manner. The approach connects different sub-processes that are conceptualized in process flows consisting of value-add-to-value-add operations. This assures the continuous flow of materials and other resources necessary to produce different varieties of tissues. Besides, the company has installed machines designed to fit into a minimal envelope, which allows for the elimination of excess space consumption and avoidance of the reassembling machine’s components of in extreme cases, relocating the machines and avoid the issue of batch processing which is resource-intensive and costly (Johnston & Clark, 2008). The technology often enables the management to modify processes and sub-processes when needed to ensure efficient and effective utilization of resources. Besides, the approach enables zero defect products through a total quality management mechanism and continuous manufacturing and time-based management.
Just-in-Time (JIT) Manufacturing
This method is appropriate for an organization that intends to improve its responsiveness to the changes happening in the market and ensures optimal utilization of resources by reducing waste of resources and increasing efficiency (Wheelwright, 2010). It has been proved that the method enables the operations manager to reduce waiting time, avoiding excess inventory, and over-production.
This method’s key benefits show that there is a significant reduction in product costs because the manufacturing cycle time is significantly lower besides allowing for the minimum waste to be incurred (Jacobs, Chase, & Chase, 2010). The approach also enables the management to remove operations that do not add value to the organization and the product. Because of continuous communication and quality improvement programs, the resulting products have high qualities. Problems associated with perishing goods, overstocking, and costly inventory of goods are avoided. The possibility of implementing alternative designs that respond to the market needs and expectations is high due to fast response to engineering changes (Johnston & Clark, 2008). This leads to productivity improvement, less administrative time, and flexibility, and simplicity in management execution.
Agile Operations
This method has widely been used to improve processes by focusing on individual interaction with tools, customer collaboration, response to changes in flow plans, and focus on customer value. Studies have shown that agile development combines low-cost service delivery with just-in-time responses to business demands (Akkerman, Farahani, & Grunow, 2010). The key principles are evident in the company’s production processes, where a wide variety of tissues are customized to address end-user needs. Self-organization characterizes the employees working in groups, which allows for intense collaboration of production activities not only across the departments and among the workers, but across integrated teams (Wheelwright, 2010). The teams that work for the organization always strive to achieve continuous improvements on the products for quality assurance.
The company’s adoption of the agile development paradigm is conceptualized and allowing for ease of tracing problems that happen in the production process, which enables the employees to reduce the number of defective tissues, synchronize development and operational data, and allow for the automation of certain key lifecycle production processes for intense resource use (Johnston & Clark, 2008). It is important to note that the approach allows for the integration of development and operational assets, allows for compliance reporting, and enables quick identification of production problems and the ability to provide impact assessment reports.
The approach is people-oriented because it allows the management to work with a lean workforce in an enabling environment. It also enables the management to streamline its operations using its information technology systems, which track the various solutions based on a context-sensitive approach. Business value comes first in this case by enabling effective communication, which allows for effective customer engagement with the manufacturer. This makes customers aware of every step of the production process for their benefits. Payments are made on finished products that meet customer needs and expectations.
References
Akkerman, R., Farahani, P., & Grunow, M. (2010). Quality, safety and sustainability in food distribution: a review of quantitative operations management approaches and challenges. Or Spectrum, 32(4), 863-904.
Jacobs, F. R., Chase, R. B., & Chase, R. (2010). Operations and supply chain management. 2 Pennsylvania Plaza, New York City: McGraw-Hill/Irwin.
Johnston, R., & Clark, G. (2008). Service operations management: improving service delivery. London, England: Pearson Education.
Kalpakjian, S., & Schmid, S. R. (2014). Manufacturing engineering and technology. Upper Saddle River, NJ: Pearson.
Kouvelis, P., Chambers, C., & Wang, H. (2006). Supply chain management research and production and operations management: Review, trends, and opportunities. Production and Operations Management, 15(3), 449-469.
Panneerselvam, R. (2012). Production and operations management. New Delhi, Delhi: PHI Learning Pvt. Ltd..
Slack, N. (2015). Operations strategy. Hoboken, NJ: John Wiley & Sons.
Smith, L., Maull, R., & CL Ng, I. (2014). Servitization and operations management: a service dominant-logic approach. International Journal of Operations & Production Management, 34(2), 242-269.
Sousa, R., & Voss, C. A. (2008). Contingency research in operations management practices. Journal of Operations Management, 26(6), 697-713.
Wheelwright, S. C. (2010). Managing new product and process development: text cases. New York City, NY: Simon and Schuster.