Harley Davidson Motor Company was established in 1903 and has grown to become one of the leading manufacturers of motorcycles globally. The company produces up to 28,000 motorcycles annually. The motor bikes are then sold by dealers in over 67 countries around the world. The company has an ambitious plan to increase its production capacity.
As a result of company’s growth and enlarged global presence, the management has realized that the future demands for an integrated management system that will not only improve the company’s processes but also fit within its budget and enhance its returns growth. This underlay the start of the process to identify the most appropriate information management system for Harley Davidson Motor Company.
The process was largely reliant on teamwork, which played a leading role in the structuring of the Information System function. The organization, rather than have a Chief Information Officer, constituted a team of three directors to offer leadership on information systems integration. The three directors play an internal consultancy role to the team engaged in the identification of the appropriate software that meets the needs of the organization.
Additionally, they provide direction as to how well the technology will fit into the organization’s endeavor to create business value. The group was empowered to make technology investment decisions that are beneficial to the organization. The group was considered to have more exposure to the needs of the business, considering their day to day interaction with it.
Considering the technical aspect involved in integrating the software into business operations, the purchasing team was structured to work closely with the engineering department (Thomas, William, Berry, and Clay 56). The case, therefore, emphasizes the importance of building an all-inclusive Purchasing operations group, which was located alongside their manufacturing counterparts at the plants and facilities.
Additionally, planning and control group was situated at the Corporation’s headquarters, with leadership derived from various purchasing managers. The purchasing managers were drawn from numerous Harley-Davidson sites.
Representatives from various departments including Maintenance, Repair, and Operations (MRO), Original Equipment (OE), Parts and Accessories (P&A), as well as General Merchandising (GM) purchasing activities were also included. The scenario highlights the importance of having all stakeholders on board to ensure that the process is all-inclusive, and addresses the needs of all quarters of the organization’s operations.
Other than team identification and inclusion of stakeholders in the process, the case defines the whole process necessary in selecting the suitable enterprise software (Escalle and Austin 78). The process is described by flow-chart below:
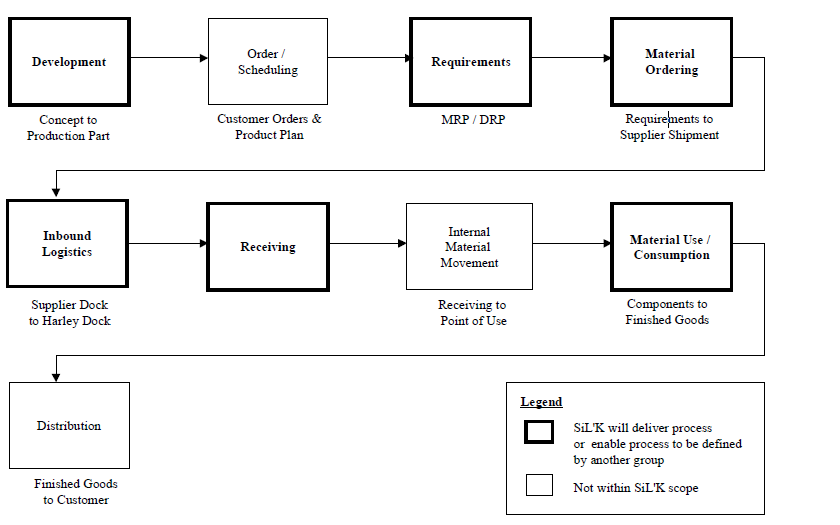
The process began with the stage being set for brainstorming of ideas that exposed the organization to greater technological advancement. It also defined the importance of leadership in any change process. Leadership emerged as a crucial step in jump, starting the process (Thomas, William, Berry, and Clay 56). The processes involved in the identification of the right supplier information link software involved the following:
- Project team formation
- Mapping out the existing processes
- Projecting the desirable process
- Identifying the people, the processes and the technology involved
- Process of selection the software supplier
- Explaining requirements to prospective suppliers
- Receiving proposals and presentations
- Narrowing down the bidders
- Coming up with the last three
- Assessing each of the last three
- Making the final decision
From the case study, the processes above are identified as those that led the group to come up with a final decision about the most appropriate supplier to provide the software to the organization. The fundamental guiding factors in the selection of the final provider were based on three key factors. These included: the ability to speed time to market, ability to reduce costs, and ability to improve product quality.
Key factors considered in justifying the need for the software
The case also emphasized the importance of coming with factors that justify the need to bring on board the software. These have defined about the people involved, the processes involved, and the technology. About people, it is important to highlight how the software’s implementation will improve people’s work to a more efficient manner.
On the other hand, about processes, it is important to illustrate how the software will improve the process. This is done by answering whether the process will reduce time; reduce costs, and complexity, among others. Finally, about technology, this illustrated how the software would enhance technology.
Generally, the case study defines the elements that constitute problem identification and the gap that software needs to fill, the persons involved in the processes and the overall process involved in the selection of the software. It offers all the information that a planner may require to develop a project schedule.
Based on the existing supply processes, the team was able to come up with a proposal for software that would fill in all the gaps. This formed the basis for evaluation and determination of the appropriate software supplier that will meet the needs of the organization in line with its strategic objective.
Works cited
Escalle, Cotteleer, and Austin, Ryan. Enterprise Resource Planning (ERP), Report No 9-699-020, Harvard Business School, Cambridge, MA, USA, 1999.
Thomas, Vollman, William, Berry, L., and Clay, Whyberk. Manufacturing Planning and Control Systems for Supply Chain Management, London: McGraw Hill, 2005.