Abstract
Manufacture of writing paper is a world wide industry and the products include items such as stationary items, bond paper, kraft paper, hand made paper and other grades. The products are available in different grades and quality as determined by the gsm value of the paper. This paper provides an analysis of different aspects that have to be considered in setting up a writing paper unit. Taking a fictional company called United Paper Co. Important aspects such as Business Model, Product Design and Description, Facility, Quality Parameters and Total Quality Management, Supply Chain Management System, Just-In-Time Manufacturing, Product Planning, Inventory and other aspects.
Business Model
The business model proposed is designed to ensure that the products are manufactured as per the required quantity and quality and at the right time. The company can offer products made from recycled paper as well as from fresh pulp. The plan will consider that paper manufacturing has become unpopular since trees have to be cut down and there is an increasing awareness of the environment. The model would be demand driven and attempt will be made to keep the overlap between supply and demand as smallest.
In the proposed business model, raw material would that would be used would include recycled paper pulp made of newsprint and other stationary paper; bagasse that is formed as a residue in sugarcane crushing units; use agricultural pulp and waste. The cost of procuring and transportation have to be considered but they should not be more than 20% of the cost price. The machinery that is used can be semi automated and be able to handle pulp of different grades and mesh sizes. Manufacturing will be made as per batch runs and a work schedule, based on the number of advance booked orders or sales forecast figures have to be drawn.
The rolling mills would be designed to handle paper from 80 to 230 gsm. Both in process and final inspection and testing would be used. Web thickness would be monitored on a continuous bases by using adequate web strain measurement gages and photo sensors. The company would be selling products through a network of dealers, booking agents and to organizational consumers such as government bodies, super mart chains such as Tesco, Wal-Mart, companies and others. Production would be driven by demand and sales forecast and delivery would be made by using freight courier companies. An inventory of more than a month would not be recommended (Dias, 2006).
Product Design and Description
Writing paper is available in different grades and a discussion of the grades. Recycled paper has become increasingly popular and products with 30 to 100 percent of recycled content are available. Please refer to the following table that gives details of different grades of writing paper. The use of recycled fibre has been growing steadily since 1984 and today stands at a figure of around 50% (the recycling rate is calculated on the basis of recovered paper used in recycling compared to total paper consumption) of the fibre mass used in paper production. Graphic paper and this includes writing, printing and stationary grades make up around 50% of the EU’s paper production, packaging paper grades account for 40% and hygiene and specialty papers for around 10%. The European industry consists of more than 1,000 paper mills and 220 pulp mills with Germany leading the field as the largest paper producer in the EU, followed by Finland, Sweden and France. Finland and Sweden are the main pulp-producing countries (F-BI, May 2006).
Table 1. Writing paper grades (McKinney, 1995).
As seen in the table, paper grades such as Sud. Ultra Shine Maplitho of 80 – 140 gsm and SS Pulp Board UHB 140 – 230 gsm would seem more appropriate as these grades have higher volumes. The premium segment would require a higher grade of technology and it might prove to have higher initial costs. (McKinney, 1995).
Facility
The manufacturing facility would different machinery such as pulping, cooking, rolling, drying and others. An aerial view of the proposed facility is shown as below.
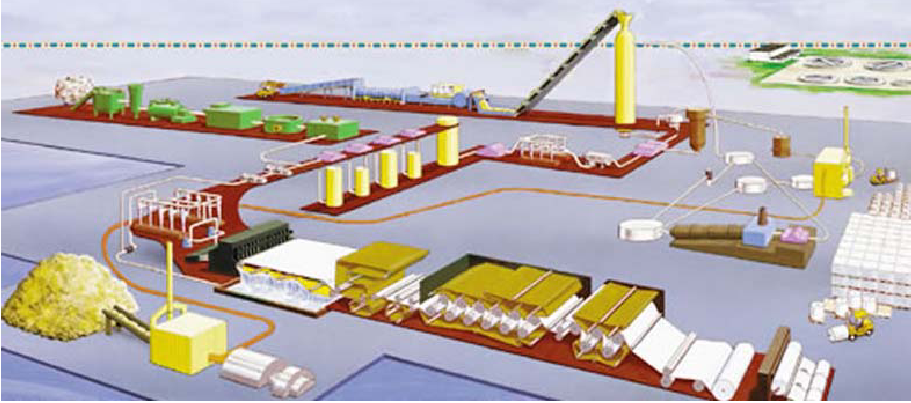
The pulp is created with a mix of vegetable fibers and cooking them in hot water until the fibres are soft but not dissolved. The hot water also contains a base chemical such as lye, which softens the fibres as they are cooking. The cooked material is forced through a sieve and the water is dripped off. The mix is also evaporated and squeezed additional water. A layer of paper is left behind. Essential to the process are the fibres, which are never totally destroyed, and, when mixed and softened, form an interlaced pattern within the paper itself. Modern papermaking methods, although significantly more complicated than the older ways, are developmental improvements rather than entirely new methods of making paper Please refer to the following figure for an illustration (Paper, 2007).
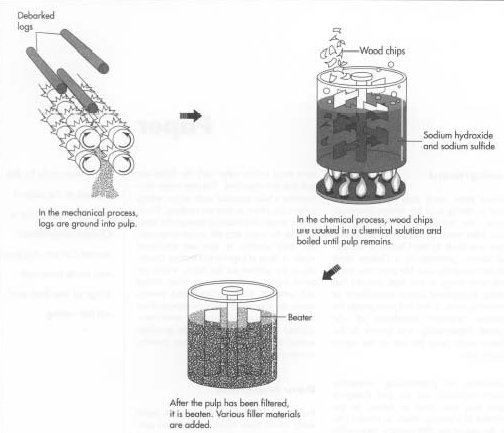
The pulping process that would be employed would consume the least energy. Please refer to the following figure.
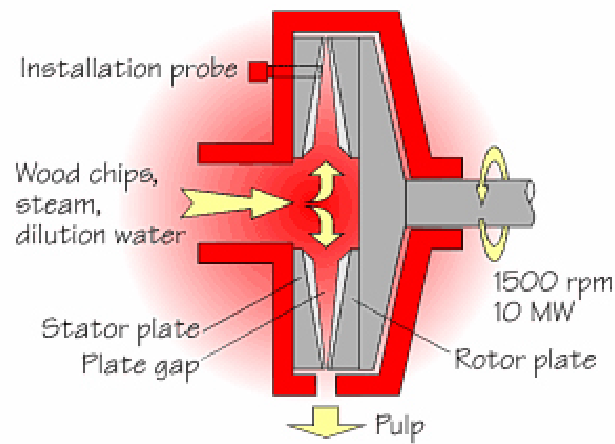
In order to finally turn the pulp into paper, the pulp is fed or pumped into giant, automated machines. One common type is called the Fourdrinier machine, which was invented in England in 1807. Pulp is fed into the Fourdrinier machine on a moving belt of fine mesh screening. The pulp is squeezed through a series of rollers, while suction devices below the belt drain off water. If the paper is to receive a watermark, a device called a dandy moves across the sheet of pulp and presses a design into it. The paper then moves onto the press section of the machine, where it is pressed between rollers of wool felt.
The paper then passes over a series of steam-heated cylinders to remove the remaining water. A large machine may have from 40 to 70 drying cylinders. Finally, the dried paper is wound onto large reels, where it will be further processed depending on its ultimate use. Paper is smoothed and compacted further by passing through metal rollers called calendars. A particular finish, whether soft and dull or hard and shiny, can be imparted by the calendars. The paper can be further finished by passing through a vat of sizing material. It may also receive a coating, which is either brushed on or rolled on. Coating adds chemicals or pigments to the paper’s surface, supplementing the sizings and fillers from earlier in the process. Fine clay is often used as a coating. The paper may next be supercalendered, that is, run through extremely smooth calendar rollers, for a final time. Then the paper is cut to the desired size ((Paper, 2007).
Quality Parameters and Total Quality Management
Quality parameters that would be monitored and maintained would include the temperature of the pulp and its mesh size, thickness and quality of the paper, paper gsm, thickness, colour, strain of the web and others. Disposal and waste management will ensure that the chemicals used in paper manufacture such as dyes, inks, bleach, and sizing that are harmful to the environment, water bodies and land are properly treated to remove the harmful chemicals. The system proposed is illustrated in the following.
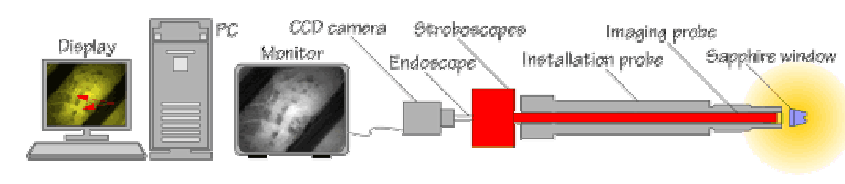
The following quality inspection tests and systems are proposed as shown in the following table.
Table 2. Quality and Inspection Tests (Ecnotech, 2008).
In addition, a number of tests would be done for environmental impact assessment due to the activity of the plant.
Table 3. Quality and Inspection Tests for Environmental Impact (Ecnotech, 2008).
Supply Chain Management System
The supply chain management would cover raw material and consumable inward flow as well as the finished product to the marketing network. The process would be triggered by the sales forecast and the sales order for specific grades of paper. After the order quantity and schedule is fixed, orders would be sent to the raw material supplier. The material that would be purchased includes recycled paper and shredding, wood shavings and chips, bagesses, jute and hemp fibre and other materials. The supply chain would ensure that there are no stocks out situations. In addition, consumables such as dyes, bleaching and softening chemicals, inks and other additives. Fuel would also be considered. Based on the plant location, the power used would be steam, gas or electricity. After the paper is packed and ready for disposal, the supply chain will ensure that the labelling is done with machine bar code and if possible RFID tags. Against purchase orders from the dealer network, the products would be despatched in economic order quantities. (Scovell, 1981).
Please refer to the following illustration that gives an overview of the supply chain.
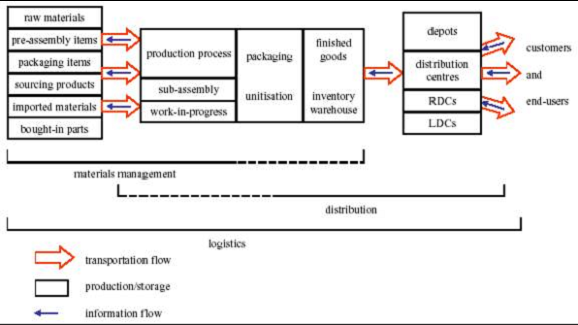
Just-In-Time Manufacturing
Just In Time (JIT) is an inventory and production optimisation technique that whose goal is ‘producing the right quality and quantity of work at the right time”. It focuses on reducing waste and on continuous improvement. JIT also uses quantitative and statistical methods and tools in monitoring a process. Taiichi (Taiichi Ohno, 1995) described waste as anything that does not add value to a product. The earlier concept of waste was limited to rejected parts and the efforts were concentrated only on getting the right quality of parts. He identified several areas of waste and they are:
- Overproduction – producing more that what is needed or earlier than when needed
- Transportation- movement of products and raw materials further than what is needed
- Waiting- idle time spent by parts and products that wait for the next operation or idle time spent by workers because they have no work
- Inventory – keeping more items than what is actually needed or excess inventory
- Motion – movement of people and the extra motion of their hands and limbs as they move about to complete tasks
- Processing – stand-alone processes that do not link to forward or backward processes
- Defects – number of error that occur in produced parts and require extra efforts to set them right
- Safety – of the environment and machines that cause injuries and cost money
To implement JIT, all activities in the system would be mapped out. Where possible technology changes would be introduced to remove bottleneck operations and efforts taken to eliminate extra processes and some processes would be merged with the others.
Product Planning, Inventory
Economic Order Quantity (EOQ) is the basis for controlling inventory systems. EOQ is an accounting formula that calculates the point at which the combination of inventory carrying cost and order cost are the least. EOQ states the most cost effective quantity to order. In purchasing terms, this is known as the order quantity and in manufacturing domain it is known as the production lot size (Zhu Zhiwei, Meredith Paul, 1995).
There a number of formulas that are used in finding the EOQ.
Stock consumption constant rate = R units per year
Order Costs = Co
Variable holding cost per unit per year = ch
Annual holding cost = ch(Q/2)
Batch or order lot size= Q
Average Inventory Level = Q/2
Number of order per year= R/Q
Annual order cost = co(R/Q)
Total annual cost = ch(Q/2) + co(R/Q)
A costing system would be introduced to allocate different cost heads and budgeting would be done for each cost head based on its expenditure, work orders and other details.
Summary
The paper has examined details of key factors that would help the company to set up operations. Areas such as Business Model, Product Design and Description, Facility, Quality Parameters and Total Quality Management, Supply Chain Management System, Just-In-Time Manufacturing, Product Planning and Inventory have been examined in detail.
References
Dias Ana Cláudia. September 2006. Life Cycle Assessment of Printing and Writing Paper Produced in Portugal. Scientific Journals. pp: 30-38
Ecnotech. 2008. Pulp & Paper Testing. Web.
F-BI, May 2006. Pulp and paper manufacturing. Web.
McKinney R. January 1, 1995. Technology of Paper Recycling. Springer; 1 edition. ISBN-13: 978-0751400175.
Paper Process. 2007. Paper Production Process. Web.
Paper. 2007. How paper is made. Web.
Rushton A, Oxley J, 1989, Handbook of Logistics and Distribution Management. Kogan.
Scovell Clinton Homer. February 1981. Cost Accounting and Burden Application (Dimensions of Accounting Theory and Practice). Arno Press. ISBN-13: 978-0405135446.
Taiichi Ohno, 1995, Toyota Production System: Beyond Large-scale Production, p.p. 47 – 65; Productivity Press Inc., ISBN 0-915299-14-3.
Zhu Zhiwei, Meredith Paul, 1995. Defining critical elements in JIT implementation: a survey. Industrial Management & Data Systems. 95(8). pp. 21-28.