There are various internal combustion engines in existence. These engines are usually categorized according to their physical layout (inline/ straight, flat/ boxer, V, and W), the number of cylinders they contain (single, twin/ two, four, six, eight, ten, twelve, and sixteen), and the type of fuel they use (petrol/ gasoline, gas, and diesel).
So for example, one may come across a ‘V12 petrol engine’ or a ‘four cylinder diesel engine. As can be seen from the two examples aforementioned, all the defining aspects/ attributes of the engines have been captured in their names.
Due to the different characteristics (e.g., weight, size, number of cylinders) and working principles (e.g. magneto, coil, number of strokes per cycle, fuel injection or carburetor systems) of internal combustion engines, the different engine types are used for a varied number of applications. The following is a small summery of the five most common engine types according to the type of fuel that they use.
Gasoline Engines
They are also referred to as petrol engines, and as the name suggests, run on petrol. They are commonly used to propel small and medium sized motor vehicles, motorcycles, aircraft, motorboats, lawn mowers, portable electricity generators, and chainsaws. These engines have several advantages which include:
- are cheaper to produce and acquire compared to their diesel equivalents
- they are not as noisy as diesel engines
- their spare parts are cheaper to buy
The disadvantages on the other hand include:
- they are less efficient over longer journeys
- they usually have a lower resale value
- heavier petrol engine vehicles need to be driven harder to enable overtaking maneuvers. This leads to increased fuel consumption.
Gas Engine (Spark Ignition)
The term ‘spark ignition’ refers to the use of electric sparks to ignite/ cause fuel to combust. These sparks are developed when a high voltage current is forced to ‘jump’ across a small gap.
The phrase ‘Gas Engine’ however, is an ambiguous term which could imply/ refer to an internal combustion engine which runs on either petrol, Liquid Petroleum Gas (LPG), Compressed Natural Gas (CNG), hydrogen, bio-ethanol, methanol, ethanol, or nitro-methane. The advantages and disadvantages of these engines vary slightly from one fuel type to the other, but some common similarities do exist, i.e.:
Advantages
- are cheaper to produce and acquire compared to their diesel equivalents
- they are not as noisy as diesel engines
- their spare parts are cheaper to buy
The disadvantages on the other hand include:
- they are less efficient over longer journeys
- they usually have a lower resale value
- heavier spark ignition engine vehicles need to be driven harder to enable overtaking maneuvers. This leads to increased fuel consumption.
Oil Burning Diesel Engines
These are basically just normal diesel engines that can be found on an ordinary vehicle. However, instead of running them purely on diesel, the owners of such engines usually add a small amount of used engine oil to the fuel (diesel). This process is commonly done to ships, big/ heavy duty trucks, and tractors. Such engines have various advantages like:
- they help in reducing wastage by recycling used engine oil.
- they are cheaper to run as they use oil which most people have no use for and thus attach no value to them.
- they are more flexible as they can run on either diesel or petrol, or even a blend of the two.
The disadvantages are that:
- they produce a lot of smoke which contributes to environmental pollution.
- they require special care due to the possibility of damage which might be caused by metal particles in the recycled oil.
Gas Diesel Engines
The idea of such an engine was necessitated by the need for a fuel efficient engine with minimal resulting harmful emissions. This led scientists to develop an internal combustion engine that incorporated the highly fuel efficient technologies found in diesel engines but ran on the more environmentally friendly petrol.
The result is a ‘gas-powered diesel engine’ that is about twice as economical as a petrol engine and cleaner than a diesel engine (Nguyen, 2011). This engine is not commonly used commercially as the technology behind it is still in the research and development phase. The advantages of these engines are that;
- it is almost twice as economical as a petrol engine
- it has much few carbon emissions than a diesel engine.
The disadvantage is that:
- it is about twenty five percent less powerful than a regular gas/ petrol or diesel engine at full throttle.
Dual-fuel diesel Engines
Dual-fuel is a device/ gadget that have been developed by ‘Clean Air Power’ to work with the standard original equipment manufacturers of standard diesel engines. Dual-fuel works by injecting a mixture of natural gas and air into the combustion chamber of the diesel engine.
This mixture cannot ignite spontaneously like diesel under compression by the cylinder; therefore, a small charge (about 10 percent of the total energy of the fuel) of diesel is injected to the main mixture of gas and air to act like a multitude of microscopic spark-plugs that ignites the mixture (Richard, 2010). This technology has been confirmed to work on DAF’s and Mercedes’ heavy duty diesel truck engines.
Advantages of these engines are:
- they have fewer carbon emissions than standard diesel engines.
- they can run entirely on diesel alone.
- they can run on gas.
- they are more efficient than diesel engines.
Despite all the differences in working principles of the above mentioned engine types, they all share a significant number of key elements and components. The most obvious element shared by internal combustion engines is the aspect of compression and ignition of a fuel charge.
Although the processes involved may vary for different engine configurations (e.g. in a four stroke engine this process occurs over a 720 degree revolution of the crankshaft, where you have the ‘intake stroke’, followed by the ‘compression stroke’, next is the ‘power stroke’, and finally you have the ‘exhaust stroke’, with each engine stroke taking place over a 180 degree revolution of the crank shaft.
In contrast to this, in a two stroke engine this process occurs over a 360 degree rotation of the crankshaft, owing to the lack of dedicated ‘intake’ and ‘exhaust strokes’.), these two elements exist over all engine configurations and fuel types. The most important parts of internal combustion engines (all engines) are the crankcase/ engine block, the pistons, connecting rods, cylinders, and crankshaft.
The crankcase is usually cast or drilled from a light-metal material (usually iron pr aluminum) in order to keep the overall weight of the engine down hence increasing its efficiency. The crankcase, in addition to housing and protecting the crank shaft and connecting rods, also serves as an oil container and a rigid structure for connecting the transmission to the engine (John, 2004).
A piston is a part of the engine that moves in a reciprocating manner inside the cylinder/ combustion chamber. It is responsible for the transfer of power produced by the exploding gases in the combustion chamber, to the crankshaft through a connecting rod that is usually attached to it. It also acts as an intake and exhaust valve in a two-stroke internal combustion engine. Earlier pistons were made from cast iron, but the need for lighter engine components resulted to the adoption of cast aluminum alloys (Nazrul, 2013).
The cylinder is the top hollow part of the engine block. It is mostly cast from aluminum and iron to minimize on weight. The cylinder in an internal combustion engine acts as a housing for the piston. It also guides the movement of the piston during the various engine strokes, and it is where the combustion of fuel charges takes place.
The other component is the crankshaft. It spins in a circular motion in correspondence to the connecting rods’ movements. They also normally act as the output shaft in a reciprocating internal combustion engine, and either be connected to a gearbox/ transmission or be bolted on directly to whatever device that needs to be driven. Crankshafts are usually either forged or cast from iron and steel (McFarland, 2009).
With the information that has been highlighted in the foregoing documentation, it suffices to explain how internal combustion engines work. First off is the ‘four-stroke petrol engine.
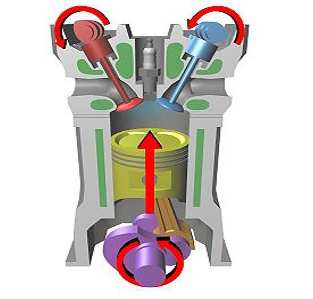
When the piston (the yellow part of the image) moves downwards, a vacuum is created inside the cylinder, the intake valve opens (the blue part of the image), and a charge of petrol mixed with air is injected into the cylinder. This is called the ‘intake-stroke’. After reaching the Bottom Dead Center (BDC), the intake valve closes and the piston starts to ascend, thereby compressing the air-fuel mixture in the process. This is the ‘compression stroke’. At Top Dead Center (TDC), a spark is introduced by the spark-plug and the fuel charge is ignited.
This results to expansion of gases inside the cylinder, thereby pushing the piston downwards. This is represents the ‘power stroke’. The piston then begins to ascend, aping the compression stroke. The exhaust valves (the red part of the diagram) open during this stroke to allow the expulsion of burnt gases from the cylinder. This is called the ‘exhaust stroke’. These engine strokes occur over a 720 degree revolution of the crankshaft (the purple part).
A four-stroke diesel engine works in the same manner, the only difference being that during the intake stroke, only air is injected into the cylinder. The air heats-up during the compression stroke, and at TDC diesel is injected into the cylinder and spontaneously combusts when it comes into contact with the hot air. This is the reason why diesel engines do not have spark-plugs.
For a two-stroke petrol engine, the previously mentioned processes of intake, compression, ignition, and exhaustion are accomplished with only two revolutions of the crankshaft.
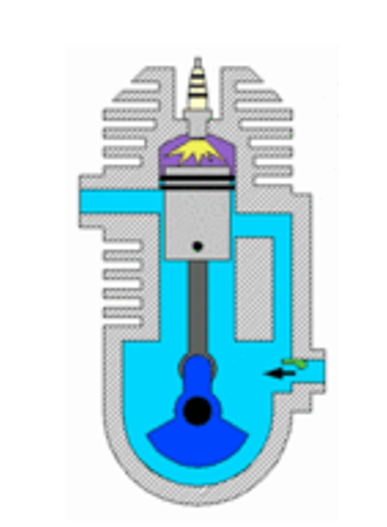
During the intake stroke (which is also the power stroke), a vacuum is created inside the cylinder and this forces a mixture of petrol and air to rush in to occupy the empty cylinder as shown by the arrow on the above diagram. The mixture is compressed during the compression stroke (which also serves as the exhaust stroke). At TDC, a spark is introduced and the charge is ignited.
The two-stroke diesel engine works in a similar manner, the difference being that only air is injected into the cylinder during the intake stroke, and that instead of a spark being introduced at TDC, diesel is injected into the cylinder leading to spontaneous combustion of the fuel charge.
A fundamental component of the internal combustion engine is the fueling/ fuel system. For a diesel engine, it comprises of a fuel tank, injection pump, and injection nozzles. The injection pump is responsible for delivering highly pressurized fuel to the injection nozzles, which atomize the fuel before injecting it into the combustion chamber.
The basic fueling system of a petrol engine employs the use of a carburetor like the one shown below.
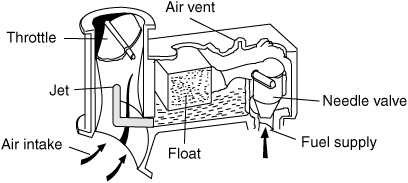
Air rushes in through the air intake manifold creating a region of low pressure when the throttle is opened. The pressure difference forces a fine jet of atomized petrol to flow from the float chamber, and mix with the incoming air. This mixture then flows into the cylinder where it is ignited by a spark to produce power.
The spark is produced by the ignition system which usually consists of a source of electric current (either a battery or a magneto), a condenser, and a spark plug as shown below. The coil draws and amplifies current and the passes it to the condenser which further amplifies it to about 25000 volts before it is sent to the spark plug.
References
John, K. (2004). FPO IP Research & Communities. Crankcase for an internal combustion engine – DaimlerChrysler AG. Web.
McFarland, J. (2009). Crankshaft Tech – Let’s Torque About Crankshafts. CIRCLE TRACK. Web.
Nazrul, I. (2013). Academia.edu – Share research. Design and construction of a piston for four stroke single cylinder S.I. engine by die-casting | AKM Nazrul Islam -Academia.edu. Web.
Nguyen, T. (2011). SmartPlanet – Innovative Ideas That Impact Your World. Gas powered diesel engine may double fuel efficiency | SmartPlanet. Web.
Richard, H. (2010). Clean Air Power dual fuel technology natural gas components. DUAL-FUEL TECHNOLOGY. Web.