Introduction
It has been observed in many practices that equipments or services remain unavailable or stalled due to lack of spare parts. In most instances, such a situation or occurrence is caused by poor planning and control of spare parts inventories.
Therefore, the necessity for proper spare parts management is prerequisite in order to realize effective maintenance manpower and support systems (Mishra and Pathak 2004, p.167). At the same time, it is common knowledge that breakdowns are generally recurring in nature. Additionally, it can be observed that during the purchase of equipment, large sum of money is used on spare parts inventory which when analyzed keenly, can be better utilized through effective management.
When an audit of various spare parts inventories is undertaken, the previous results have indicated that the primary issues attached to the spare parts management include: high financial commitment to the process of procuring spare parts; the habit of overstocking of spare parts due to unpredictable nature of failures as well as the need to minimize the downtime of the equipment or the facilities; non-availability of suitable type of spare parts due to obsolescence of equipment caused by the advancing technology; non-interchangeability of spare parts caused by the availability of different types of models and specifications; and lastly, purchase of imported equipment causes a lot of problems especially when procuring spare parts in a reasonable time and this affects mostly the lifed components (Mishra and Pathak, 2004, p.167).
To ensure that effective spare parts management system is adopted in an organization, there has been need to craft effective and updated inventory policies which have been key instruments in aiding the management of spare parts.
Warehouse and spare parts storage
The inventory of spare parts for most organizations is stored in warehouses; hence management of the warehouse is an important function whereby it acts as a link between the user and the manufacturer.
To this extent, the management of the warehouse and especially one concerned with spare parts has been seen to be specifically responsible in; receipt of orders, processing of orders, procurement of the spare parts, inspection of spare parts, issuance of spare parts, valuation of stock, inventory control, proper storage of spare parts, coding of spare parts and finding solutions to the numerous store problems (Mishra and Pathak 2004, p.172).
To further ensure smooth functioning of the stores, the items being delivered to the storeroom have to be verified for the quality, quantity and expiry date of the parts, if any.
In many cases, the output function of spare parts has been seen to involve issuance to different departments or sales to the customers. Moreover, to ensure the confidence of clients grows stronger, the lifted items need to be given out on first-come-first-served basis, and when the stock of items reduces to a level that is below the pre-specified, the management needs to be quick in initiating procurement action (Mishra and Pathak, 2004, p.173).
What can be noted is that the company that is involved in the sale of spare parts has the obligation to make sure that there is availability of right quality of spares at the right time to the right users, with minimum investment at the seller’s end; while at the same time the supplier’s credibility relies on pricing of spares, efficient handling of customers’ orders and reliable delivery on schedule with sound after-sales services.
For an organization or a company to live its objectives, it is necessary to undertake and maintain a proper and adequate quantity of spare parts in its stocks, carry out maintenance work efficiently in the outlined and allocated time period and also at minimum cost (Mishra and Pathak 2004, p.173).
Inventory control
Inventory control can be described as a planned approach which is essentially concerned with determining what to order, when to order and what quantity to stock so that the costs of buying and storing are kept at an optimal level without interrupting production and sales (Kumar, 2006, p.67).
Looking at the function of inventory control, it becomes evident that it deals with two main problems; when should an order be placed (Order level) and how much should be ordered (Order quantity).
Objectives of inventory control have been outlined as:
- It ensures adequate and timely supply of products to customer and also it avoids shortages as far as possible;
- It is responsible in ensuring the financial investment in inventories is minimum;
- It operates to ensure there is efficient purchasing, storing, consumption and accounting for materials in an organization;
- It ensures that there is timely record of inventories of all items and also keep the stock within the desired limits;
- The process is responsible to the timely actions of replenishing the stock;
- It operates to provide a scientific base for both short-term and long-term planning of materials; and lastly
- It works to provide a reserve stock for variations in lead times of delivery of materials (Kumar 2006, p.68). From these numerous objectives, inventory control has been seen to have many benefits to the company or a particular concerned organization.
These benefits are: through an efficient inventory control in a company; the company’s relationship with customers is improved as there is delivery on time of goods and other services; the process ensures there is a smooth and uninterrupted production hence no stock-out is experienced; the process leads to efficient utilization of working capital, enabling the company to minimize its loss that occurs as a result of deterioration, obsolescence damage and preliferage; the process has further contributed to economy especially in purchasing behaviors of the company; and lastly, inventory control is responsible in eliminating the possibility of duplicate ordering (Kumar, 2006, p.68).
Inventory control techniques
Almost in every organization, there exists some kind of inventory. Basically, organizations with large items in inventory require large sums of money to create such inventory, thus it becomes necessary for the management to create a proper control over its ordering, procurement, maintenance and consumption and the control process becomes largely for order quality and order frequency (Kumar 2006, p.68).
In addition, there exists different techniques of inventory control which include: 1) ABC analysis; 2) HML analysis; 3) VED analysis; 4) FSN analysis 5) SDE analysis; 6) GOLF analysis; and 7) SOS analysis, but out of all these techniques, the ABC analysis is the technique that has been preferred and widely utilized by most companies (Kumar, 2006, p.68). The ABC analysis basically involves a procedure where the total inventory is put into three sub-heads categories and later a proper exercise is undertaken for each sub-heads.
Warehousing and activity profiling
It must be remembered that most spare parts storage takes place in a warehouse and in many cases, warehouse managers are versed with the warehouse activity profiling, which is the systematic analysis of item and order activity (Frazelle, 2002, p.15).
Activity profiling in the warehouse is a process that is carried out and is intended to quickly identify the primary causes of material and information flow problems while at the same time discovering the major opportunities for the improvement of the process as well as provide an objective ground for project-team decision making (Frazelle 2002, p.15).
In undertaking the activity profiling in the organization, the objectives of inventory for spare parts will be carried out basing on the advantages of profiling which include:
- When carried out properly, profiling has the capability to quickly reveal the warehouse design and planning opportunities that are present;
- Profiling in many cases eliminates options that presents themselves but are not worth consideration;
- Profiling provides the right baseline to start the process of justifying the new investments; and 4) profiling process has the ability to get together key people involved in inventory management of the organization (Frazelle, 2002, p.16).
Use of the MASTA approach
As it is evident in many inventory classification approaches, the ABC analysis has been favored over other techniques. But this technique has demonstrated numerous limitations which in turn greatly impact the inventory of spare parts in the company.
The ABC analysis technique usually controls items on the basis of their monetary value whereby it portrays the tendency to ignore the importance of items in the production process and secondly, the technique demonstrates the difficulties experienced in storing all the three types of category on which it is based on in the store department and therefore, it always requires adequate and proper codification of materials (Jain et al, n.d, p.322).
These limitations come be overcome by adopting and utilizing multi-attribute classification models that have the capacity to manage multiple criteria and factors that sometimes appear to be in conflict with each other. Indeed, Braglia et al (2004) suggested an approach, the multi attribute spare tree analysis (MASTA) which can be used in the company to answer the pertinent questions of spare parts inventory management (cited in Ketikidis, 2006, p.776).
The approach is established on two consecutive steps and the results are concerned with the establishment of a matrix that identifies the inventory policy with regard to each spare part stock and the supply strategy. The first step is concerned with the criticality analysis that rests on logic trees where each spare part is checked with the aim of identifying its criticality for four major categories; the criticality to the plant, the supply characteristics, the inventory problems and usage rate (Ketikidis, 2006, p.776).
After this, for each major category, there are further elements that are investigated and the criticality of each of these elements can be deduced to be critical, important and desirable. The larger process starts investigating each major category in a systematic order as presented and outlined earlier and within each major category, its key elements are analyzed to be critical, important or desirable (Ketikidis, 2006, p.776).
At the end, the entire category is analyzed and according to the analysis of each category, a different route is adapted. At the conclusion of the whole process each part is evaluated against all categories and sub-elements and then allocated to a particular class. According to the class of each spare part, the inventory policy matrix indicates the inventory policy strategy.
Instituting management information system (MIS) in inventory
MIS is a control and feedback system which usually starts with maintaining the stock ledger that, in most cases, incorporates the receipts, issues and balance stock on hand at any time. With regards to spare parts, the system can be utilized in various ways, for example, purchases orders need to be entered into the system in turn it can allow for follow-up and know when to make the next ordering. Indeed, the process can follow the reorder level or the periodic review system.
Managing the inventory of spare parts
Spare parts are necessary in the repair and maintenance of a mother unit throughout its life. In some observable instances, it will be seen that some of the parts never breaks down during the operating life of the machine, while at the same time other parts will experience failures repeatedly. What is true is the fact that there is generally no certainty as to when a part would experience failure and therefore require replacement.
Generally, the parts that are used frequently are kept in the inventory for replacement and this ensures that the machine downtime is kept at the lowest point (Saxena, n.d, p. 408). Many organizations have classified spares in a variety of ways, for example, regular, fast-moving, emergency, critical, insurance, major, minor, mechanical, electrical, instruments, moving, slow-moving, non-moving, budgeted, and mandatory and so on, which is done for purchasing purposes (Gopalakrishnan, 2001, p.315).
But to realize what can be termed as ‘scientific control’, the spares need to be classified as maintenance, ratable, capital, insurance, overhauling and commissioning spares which should depend on the nature of usage (Gopalakrishnan, 2001, p.315).
Inventory control of spare parts has been analyzed and conclusion reached at has shown that the process continues to play an increasingly vital role in modern operations management. With regard to long time experience of operations and maintenance, the demands for spare parts in many cases are usually uncertain and excessive stocking is generally very expensive (Cao, 2007, p.601).
Such scenario has resulted into outlining key distinguishing feature of the spare parts inventory system as largely involving the need to specify the criticality class of the spare parts (Cao, 2007, p.601). In utilizing this key feature, generally, there is the identification of the optimal control parameters that is done in accordance to the criticality class and this is usually associated with the setting of target service level and other constraints conditions.
From such a process, the procedure of identifying criticality class for a new spare part in an accurate and efficient way has become a challenge for inventory management and many experts in the field have suggested that the best way to carry out the management of inventory is through development of better technique that will have the role of identifying the criticality class (H, M or L) of a spare part and management inventories from the point of view of their necessity in production and maintenance operation (Cao 2007, p.601).
In some cases, the decision procedure outlined above appears complex but to ensure its workability, the decision support system (DSS) which has the ability of easy storage and retrieval of the necessary and much needed information has been utilized as a powerful instrument to give support to the decision-makers in the process of decision making.
Inventory policy for spare parts
When it comes to spare parts management, many companies usually have inventory policies, stock taking policies, cataloging policies, warehouse policies, issue and usage policies and also disposal policies. Policies have enabled companies to have adequate plans and control measures which in turn have led to realization of benefits from such policy frameworks (Slater 2010, p.68).
The company needs a spare parts policy which when fully and adequately implemented will see: the prevention of excessive purchases of items; improvement of the timeliness of availability of items; reduction in the level of obsolesce and write downs; faster recognition and clean up of the items spares that do become obsolete; and lastly, the policy will generally save money by ensuring reduced expenditures while at the same time improving reliability through reduced downtime.
According to Silver et al. (1998) the major objectives of an inventory analysis is to answer three main questions: how often should the inventory status be determined; when should the item be ordered for restocking; and how much of the item should be requested at order instance (Ben-Daya, Duffuaa and Raouf 2009, p.202).
For the person responsible in making decisions to fully answer these questions, he or she needs to sets out the following conditions: what is the importance of each item in consideration; does the inventory position have to be checked regularly or periodically; of which type the inventory policy should be; and what are the service level targets and costs (Ben-Daya, Duffuaa and Raouf 2009).
In general all items do not have the same importance and since large number of different parts is kept in stock and resources are limited it becomes important to adopt decision guidelines that classify all the items in a limited number of manageable groups. Numerous classifications methods are used that include: Pareto (A-B-C); multicriteria; variance partition and many more. Independent of the method used, it is always good to limit the number of classes to three up to five.
In formulating policy for Forklift spare parts, the A-B-C type of classification will be utilized where (A) items receive most personalized attention, strict control policies and have priority over B and C items. With a continuous review strategy the stock level is usually known and with the periodic review, the stock level is determined at predetermined instants kR(K=1, 2,3….) and the main usefulness of constant review is that it needs less safety stock and therefore lower holding costs than the periodic review (Ben-Daya, Duffuaa and Raouf 2009).
The main inventory management parameters to be used will constitute the order point (s), the order-up-to level (S), the review period (R) and the economical order quantity (Q). The below is a proposed inventory control system for Forklift.
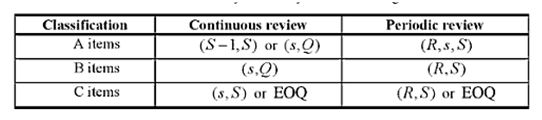
The policy also will address the several inventory control models taking into account the spare parts elements such as long lead-time, slow and random demand, risks of shortage and obsolescence.
The (S-I, S) inventory policy for Forklift
It is also called the base-stock and very useful in inventory control of A items and expensive spare parts like forklifts that have lifetime longer than replenishment lead-time. In its operation, the Forklifts will be kept in stock and random independent demands due to replacement at failure arrive at a rate of λ per unit time. After each forklift request, one replacement unit will be ordered and the replenishment lead-time has a general probability distribution with mean (t). When the nominal stock (S) get exhausted before the replacements are received, a penalty cost (L) will be incurred for each demand that must be filled by an emergency order or lost due to shortage. A holding cost (h) per unit time will be incurred for each item in stock.
Conclusion
The modern manufacturing system is steadily becoming complex, putting a lot of pressures for many organizations to device more sophiscated spare parts inventory management systems. Generally, the aim of keeping spare parts in stock is to reduce the unavailability of the system or parts of the system due to an unexpected failure of a component.
Therefore, the organization of spare parts should be carried out with view of trying to get balance between the cost of keeping spares in stock and the cost of unavailability of the manufacturing or the service system. Today, many software programs have been developed and which can be used to manage spare parts inventories more effectively.
Reference List
Ben-Daya, M., Duffuaa, S. O. and Raouf, A., 2009. Handbook of Maintenance Management and Engineering. NY, Springer. Web.
Cao, B. Y., 2007. Fuzzy information and engineering: proceedings of the Second International Conference of Fuzzy Information and Engineering (ICFIE). NY, Springer. Web.
Frazelle, E., 2002. World-class warehousing and material handling. New Delhi, McGraw-Hill Professionals. Web.
Gopalakrishnan, 2001. Purchasing and Materials Management. New Delhi, Tata McGraw-Hill. Web.
Jain, T. R. et al. Industrial Sociology, Economics & Management. New Delhi, FK Publications. Web.
Ketikidis, P. H., 2006. E-technology and manufacturing enterprise competitiveness. UK, Emerald Group Publishing. Web.
Kumar, S. A., 2006. Production and Operations Management. New Delhi, New Age International. Web.
Mishra, R. C. and Pathak, K., 2004. Maintenance Engineering and Management. New Delhi, PHI Learning Pvt. Ltd. Web.
Saxena. Production & Operation Management. New Delhi, Tata McGraw-Hill. Web.
Slater, P., 2010. Smart Inventory Solutions: Improving the Management of Engineering Materials and Spare Parts. NY, Industrial Press Inc. Web.