Kaizen can be defined as a tool of lean management. It was a part of the Japanese concept of quality improvement originally, and can be translated as “changes for good”. It secures the process of continuous improvements in an organization focusing on waste eliminating. It can be applied to any area that requires improvement and involves both management and employees. To make an improvement, a special team is formed to evaluate the process and distinguish its main bottlenecks. The purpose of the following paper is to explain in details how Kaizen process improvement tool can be implemented in an organization, and what improvements can be achieved by this implementation.
It is a general opinion that customers require products and services of sufficient quality. Therefore, it is crucial to constantly improve the quality of the delivered services and goods. The organization discussed in the given paper is an IT company that provides services and consultations concerning the specific business software to multiple clients.
To identify main problems, the team consisting of the key specialists and management representatives should be formed. The main purpose of involving employees in the Kaizen process is to understand the current situation in the workplace and the needs of the workers. Some researchers state that “the advantage of using concrete tools and artifacts to facilitate the participatory, iterative problem-solving process, which is a feature that has been called for but rarely tested in the intervention literature” (Von Thiele Schwarz, Nielsen, Stenfors-Hayes, & Hasson, 2017, p. 969).
Therefore, the team should detect the pilot area for the improvement activities. To improve the quality of the services in the given company, the bottlenecks of the client support are to be detected. The employees emphasize the huge time losses and a psychological pressure caused by the phone calls from the users involved in the process of software implementation. It is possible to save time and workforce efforts by using the electronic system for registering the incidents from users. At the present moment, the employees have to register the incidents in the system themselves after an incoming phone call. It is expected that implementing an improvement might assist in reducing the number of unimportant calls and the time spent on filling the incident forms. Nevertheless, the effectiveness of the steps of the Kaizen process can be evaluated only by a comparison of the implementation results with the previous process utilized by the company.
The process flow diagram below shows the steps that the incident processing involves. It also includes improvements required to achieve a better quality in service delivery. Kaizen tool seeks to eliminate waste in the process.
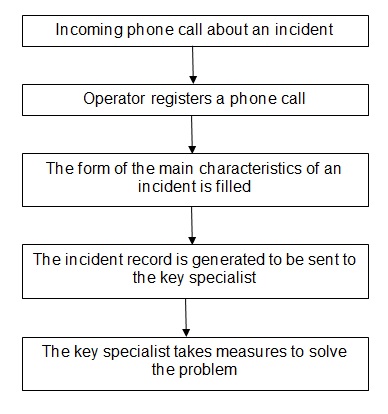
The given process flow proves that Kaizen utilizes visual tools of management to display the processes, which allows the employees to understand and view the process easily. Kaizen steps usually mean some small efforts and investments to make improvements oriented on people. The changes are expected to be gradual and permanent involving the substitution of the phone calls coming to the key specialists by the incident notifications. It might lead to the decrease of small unimportant incidents because in the process of talking to an operator a user may come with the problem decision oneself. Therefore, the saved working time may be spent by specialists on more crucial problems.
The paper dealt with the notion and identification of Kaizen process improvement tool. The details of the implementation of Kaizen approach in the selected organization were discussed. The potential improvements that can be achieved by this implementation were identified.
Reference
Von Thiele Schwarz, U., Nielsen, K. M., Stenfors-Hayes, T., & Hasson, H. (2017). Using kaizen to improve employee well-being: Results from two organizational intervention studies. Human Relations, 70(8), 966-993.