Management as a scientific discipline originated in the United States at the beginning of the 20th century. It was facilitated by a number of factors, among which the democratic nature of the country, the industriousness of citizens, the high prestige of education, as well as the absence of state intervention in the economy should be noted. The country was free from the conservative dogmas of the old world, and the creation of monopolies led to the complication of their management.
Under these conditions, the emergence of scientific management was a response to business needs. Steel management is treated as a subject of scientific study. Business processes began to be carefully analyzed, primarily technological processes, including the movement of workers during work. Management policy, namely managerial economics as part of the microeconomics of market leaders, is a necessary issue for study. The management policy of companies such as Ford, General Motors, and Chrysler is the basis of the heyday of the automotive industry and still remains relevant.
Literature Review
The international and national situation significantly impacts the sale of products. Accordingly, macroeconomics makes a significant contribution to managerial economics. The combination of macroeconomic theory and microeconomics is very effective since the practical component is often based on economic methodology while applying analytical tools and principles of marketing and accounting, finance, and personnel management. The close relationship between management and economics has led to the development of managerial economics (Samuelson et al., 2021). Economic analysis is needed for various concepts such as demand, profit, cost, and competition. Thus, managerial economics is seen as economics applied to problems of choice or alternatives and firms’ allocation of scarce resources.
Methods of Managerial Economics
Management economics uses the methods of mathematical economics. Their use is due to the fact that they help to see problems that cannot be identified with a descriptive approach. The mathematical approach makes it possible to determine the boundaries of the analysis. The main methods used in mathematical economics are statistical methods (Samuelson et al., 2021). Static methods explain economic relationships; for example, statistical methods allow you to identify the relationship between the demand for products and price.
Mathematical methods are used:
- To determine the factors that influence demand,
- To determine the dependence of price on demand.
The listed methods are used in national and international economic conditions. That is because the market is undergoing a process of internationalization. For effective actions in the global and national market, the manager needs to take into account this process; however, this does not always help. The internationalization of production has an effect on conditions different from national ones. For example, American firms that open their production outside the United States adapt their products’ management, marketing strategy, and development to the political and cultural environment of the country where this product is located (Samuelson et al., 2021). It is quite logical; in particular, adaptation helps with personnel management.
Research on the theory of organization began to be carried out systematically in the period 1890-1940, along with deepening developments in scientific management. These studies focus on the whole organization and not the work performed by individual links or members of the organization. The principles of organization, criteria for the formation of organizational structures, the creation of a system of divisions, the definition of manageability, and the delegation of rights and responsibilities were formulated.
Many scientists and practitioners have developed the ideas and concepts that form the scientific theory of organization. One of the first attempts to analyze the organizational aspects of management was made by F. Taylor (Samuelson et al., 2021). The ideas and methods that flow from Taylor’s research are known as scientific management, which focuses on the work done at the bottom of the organization (Samuelson et al., 2021). The development of this school took place in two directions – the rationalization of production and the study of management problems. The main concern of the representatives of this school was efficiency in relation to the work of the entire organization as a whole.
An essential function in managerial economics is decision-making: it includes a complete course of choosing the most appropriate action from two or more alternatives. The primary function is the most beneficial use of limited resources, such as labor, capital, land, and more (Samuelson et al., 2021). The manager is very cautious when making decisions because the future is uncertain; it ensures that the best possible plans are made efficiently to achieve the desired goal of maximizing profits. Table 1 presents the main areas of analysis of companies’ effectiveness of microeconomic processes.
Table 1. Main areas of analysis of companies’ effectiveness of microeconomic processes
Due to globalization’s intensifying processes, there have been trends in the division of automotive enterprises into car manufacturers (OEM – Original Equipment Manufacturer). These are industry enterprises that produce final products under their brand by assembling components (Abdel-Basset et al., 2019). As well as auto component manufacturers (OES – Original Equipment Supplier), these industry enterprises specialize in producing automotive components and assemblies.
The methods of structural modernization used as part of the restructuring of automotive enterprises are as follows: organizational optimization of enterprises; withdrawal of non-core assets; optimization of property complexes; increasing the efficiency of existing production; optimization of business processes; change of competence centers (business units) (Abdel-Basset et al., 2019). As it can be seen, modernization at automotive enterprises is fragmented. The concept of cost management today is one of the central business development paradigms (Abdel-Basset et al., 2019). In accordance with the concept, inefficient accounting criteria for the successful functioning of enterprises are replaced by one criterion, the simplest and most understandable for shareholders and investors of an enterprise – added value.
There is a merger of a number of manufacturers. The main reasons for this are the intensification of competition in the market, the rise in the cost of developing new cars, the development of unified automotive platforms, the tightening of regulatory requirements, and the need to unify automotive equipment, especially trucks, as well as commercial vehicles. The increase in the importance of non-material factors of growth in the value of an enterprise, primarily related to human, technological, and information resources, necessitates studying the automotive industry in a complex from the point of view of its systemic nature.
Organizational Business Environment
Changing the culture of an organization has never been an easy task because it entails changing behavior. The organization must involve every person in the process, which means that it requires commitment and loyalty from employees, management, and other stakeholders. Organizational culture is a complex structure of assumptions about roles in a group (Abdel-Basset et al., 2019). In this case, all the values that guide behavior are expected to be learned, but the process must follow a set procedure to prevent conflicts.
One of the challenges an organization may face is adapting to external change. Members of the organization were never willing to accept new ways of doing things, especially old ones, as they saw it as a violation of the normal work schedule. Another challenge an organization may face is creating a survival mechanism that requires developing and maintaining an integrated, solid, and internal identity.
Ford Motors
The Taylor system received the most significant effect from the introduction at the enterprises of Henry Ford. Thanks to the scientific organization of labor, he achieved a revolutionary increase in productivity, and already in 1922, he produced every second car in the world at his factories (Ford reduces manufacturing impact). As a talented mechanical engineer and inventor, Henry Ford, once called the ‘automobile king,’ borrowed from Taylor the basic principles of the rational functioning of the enterprise and practically implemented them in full in his production for the first time.
Ford built a production organization system based on the over- specialization of workers, the maximum fragmentation of technological process operations, and the location of technological equipment and jobs in strict accordance with the sequence of operations performed. He introduced an unprecedented form of production process organization – a production line (Brown, 2021). First used by him in 1913 in the form of a conveyor belt, such a line proved to be highly effective for mass production conditions (Albert, 2019). It made it possible to drastically shorten the cycle of manufacturing cars and reduce the cost of their production. Experts believe that thanks to the invention of the conveyor in the production of cars, G. Ford made a “revolution in the shop” (Albert, 2019). He created a system where the first place was occupied by technique and technology, in which a person was fitted.
He applied maximum specialization, the regulated rhythm of work, mechanization of transport operations, developed the enterprise as a complex providing itself with everything necessary and separated the main production from its maintenance. However, Ford did not share all of Taylor’s views, as he was more inclined toward practice and, therefore, was against excessive enthusiasm for organizational charts and structures (Ford looks to the future, 2019). He demanded strict observance of discipline without personal communication of workers at the enterprise and introduced an absolute division of labor on the assembly line.
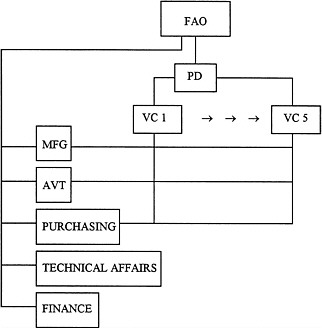
General Motors
Significantly lagging behind the Ford company in the production and not trying to compete with him in this area, Durant tried to expand his niche in the market by combining as many firms as possible. He acquired independent companies or exchanged blocks of shares with them, because of which he constantly needed cash and owed money to several large banks (Heitmann, 2018). Although, since the demand for cars was high, this business was considered promising. Durant made extensive connections in financial and industrial circles, and representatives of the most considerable chemical concern Dupont de Nemours were among the corporation’s directors.
As long as the demand for automobiles remained stable, the corporation’s position looked satisfactory on the surface, but management became its Achilles’ heel. After the end of the First World War, all its branches aimed to expand production and purchase massive amounts of raw materials (Hargrave, 2022). However, in the second half of 1920, due to the economic depression, the demand for cars fell sharply (Heitmann, 2018). Ford’s company suffered relatively little loss as he quickly and forcefully cut off purchases, diverted existing inventory to making cars, which he sold at a reduced price, then stopped production, fired workers, and reduced management costs. On the contrary, the business has fallen on hard times at General Motors.
Once change management has taken place in an organization, the question now is how best to manage change. According to the Levins model, an organization must successfully complete three steps to manage change (Albert, 2019). Unfreeze: the status quo changing to overcome the pressure of both individual resistance and group conformity. Movement: desired end state, the process of change that takes the organization from the status quo to the desired end state. Then re-freezing new change to make it permanent, stabilizing change intervention by balancing the driving and holding forces.
With the support of DuPont, a senior management team was formed and given its power. Two committees were created under the board of directors – financial and executive. The prominent investors were able to control the receipt of income and the distribution of dividends and assess the quality of the business (Albert, 2019). The Executive Committee dealt with general logistics, production, and marketing issues (Groysberg et al., 2021). It was composed of vice presidents responsible for relevant functions, heads of central departments, as well as a vice president of finance.
Chrysler
Chrysler has emphasized business restructuring towards merging with other enterprises: the operations of Fiat and Chrysler are converging. More than half of their supply chains are shared. The two companies have created a single management team to oversee business performance (regional markets and operations), brands, and line and HR processes (Gutierrez-Gutierrez et al., 2018). One of the main criticisms was that Fiat-Chrysler was run by one team of only one person: Marchionne, who had hitherto relied heavily on the strength of his personality to achieve goals. The new management structure took over some of the CEO’s powers (Gutierrez-Gutierrez et al., 2018). Even though the executive board is dominated by executives who grew up on Fiat, 14 out of 23 (Chrysler Group LLC). Employees of both companies work side by side in all production units, avoiding the ‘colonization’ effect that arose during Daimler’s control.
Chrysler’s steady decline was partly due to its inherent weakness. It was that it is less than half the size of Ford Motor Company and about a quarter the size of General Motors Corporation, the two largest Big Three Detroit companies. Mr. Ricciardo insists his company has “a good track record of innovation and delivering what the public needs” (Chrysler Group LLC). In a hugely capital-intensive industry, most say the smaller Chrysler lacks its competitors’ financial strength and agility to respond to changing market demands.
Chrysler suffers from the weaknesses of traditional organizational culture, given that top management is reluctant to embrace change, even as things move at an unprecedented pace. Ford and General Motors preferred producing products without considering new marketing, manufacturing, and public relations methods. Unfortunately, the dynamics of today’s society require the adoption of more effective ways of solving problems if an organization is to achieve its goals. At Chrysler, management has achieved the same results as the cars, regardless of the fact that much has changed, and it is time for management to apply a new strategy.
Mopar brands, each with entire profit and loss reporting. Branded organizations established general commercial, industrial and corporate functions to support the development, production, distribution, and sale of Chrysler, Jeep, and Dodge products and Mopar parts (Escoda, 2018). The new company’s leadership structure was designed to rebuild and grow Chrysler’s four iconic brands. With a simplified organization designed to give leaders ample control, a company can increase the speed of decision-making. It will also improve the flow of communication, ultimately bringing Chrysler Group management and employees closer to customers.
Conclusion
Ford’s conveyor technology was accepted and appreciated by all industrialists. Still, based on low prices and product immutability strategy, the company’s authoritarian management did not find followers – otherwise, it would lead the industry to a dead end. The automotive industry leader in the early 20s was the General Motors Corporation, reformed by its president Alfred P. Sloan. He and the management team he led developed methods and principles of management that competitors, including Ford, had to learn in order not to be left on the sidelines. Chrysler has successfully exploited economies of scale through collaborative manufacturing, which they combine with price discrimination to maximize their venture’s profits.
In conclusion, despite the challenges faced by domestic auto manufacturers in the United States of America, there is room for growth for these firms. One such opportunity discussed here is the full-size automotive market, in which they continue to hold a significant market share. The substitution effect is on the rise as energy costs increasingly push the cost of inefficient SUVs. In addition to the purchase price, other costs and factors have a significant impact on car sales. The analysis showed that throughout the history of the existence of all three leading automobile manufacturers in the United States and around the world. Any changes made at the level of the managerial economy of automotive enterprises affect the cost of their products, methods of structural modernization, and more. In all cases, a system upgrade is required, full-scale and comprehensive. This can increase the level of competitiveness of automotive enterprises and will allow the production of a modern, high-tech and high-quality product that meets all the requirements and needs of customers.
References
Abdel-Basset, M., Mohamed, R., Zaied, A. E.-N., & Smarandache, F. (2019). A hybrid plithogenic decision-making approach with quality function deployment for selecting supply chain Sustainability Metrics.Symmetry, 11(7), 903. Web.
Albert, D. (2019). Are we there yet? The American automobile past, present, and driverless. W. W. Norton.
Brown, K. F. (2021). New 2020 Ford escape illustrates efficiency improvements continue with hybrid powertrain technologies. LinkedIn. Web.
Chrysler Group LLC announces organizational structure focused on Chrysler, Jeep(R), Dodge and mopar(r) brands. auto123.com. (n.d.). Web.
Escoda, R. (2018). Leadership and change management in Fiat Chrysler Automobiles. Grin Verlag.
Ford looks to the future in Europe: Business redesigned for profitability, efficiency, more new EVs and SUVs. Ford Media Center. (2019). Web.
Ford reduces manufacturing impact on environment. Reliable Plant. (n.d.). Web.
Groysberg, B., Lee, J., Price, J., & Cheng, J. Y.-J. (2021). The leader’s guide to corporate culture. Harvard Business Review. Web.
Gutierrez-Gutierrez, L. J., Barrales-Molina, V., & Kaynak, H. (2018). The role of human resource-related quality management practices in new product development.International Journal of Operations & Production Management, 38(1), 43–66. Web.
Hargrave, M. (2022). How to use the Dupont Analysis to assess a company’s Roe. Investopedia. Web.
Heitmann, J. A. (2018). The automobile and American life. McFarland & Company, Inc.
Samuelson, W. F., Marks, S. G., & Zagorsky, J. L. (2021). Managerial economics. Wiley.