PDCA cycle was made famous by Dr. W. Edwards Deming. He was responsible for a variety of Quality Control theories and is considered one of the most important figures in the field. PDCA stands for Plan, Do, Study, Act. These words indicate four stages of quality management that continuously reoccur to build on previous improvements. This cycle is often used to manage work processes that are problematic or require additional improvement within various organizations. This paper will provide an overview of this technique based on an example of a musical instrument manufacturing company and a library; also, they will be compared to each other to find the similarities and differences in the issues that might arise during implementation.
The PDCA Cycle
The PDCA cycle is a relatively simple system that has shown to be effective for many processes (Hibi et al. 2016; Silva, Medeiros & Vieira 2017). Its simplicity lies in the four-step structure that loops back on itself after reaching the final step. Each step of the PDCA cycle serves a specific purpose in the practice of quality management. “Plan” helps inspect the problem by finding relevant data and its cause. “Do” focuses on the development and implementation of a solution to the problem defined by the previous step. Also, this step creates the measure by which the results of improvement will be gauged. “Check” compares the data taken before the improvement, and the data taken after its implementation to confirm the results. “Act” documents the results, spreads the information about the changes caused by the process, and chooses which changes should be made for the next cycle. Throughout these processes, a variety of tools is used (Pietrzak & Paliszkiewicz 2015). These examples should illustrate the implementation of the cycle.
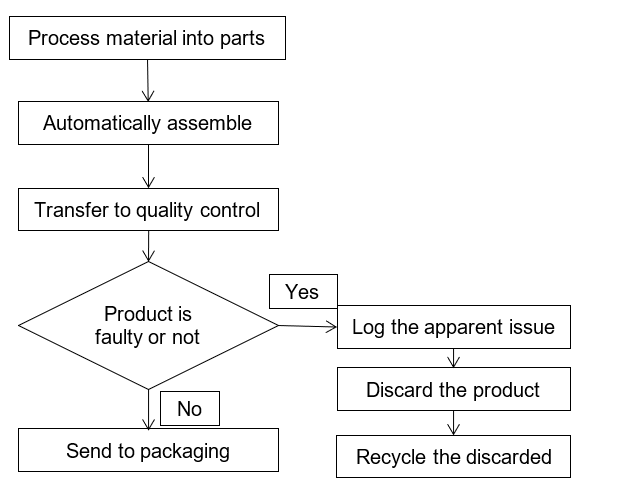
A musical instrument manufacturer utilizes a multitude of work processes within the organization. One of the most important and costly is quality assurance. For example, a factory produces 700 musical instruments a day. To manually check all each one, a person must spend at least a few minutes. This makes the need for employees high and the work process significantly slower than it could be. If a company cannot afford to hire more people, or cannot acquire an automatic checking system, the PDCA cycle can be implemented to determine the optimal solution. In the first step, a process flow chart needs to be compiled. It would serve to understand all the steps involved in the quality assurance process. Then, a cause-and-effect diagram can be created to see which step or component makes this process take longer than it needs to be. This diagram is also called the Fishbone diagram due to its shape. This diagram categorizes all the elements involved in the process, identifies potential causes, and tries to find a possible solution. Next is the “Do” step. For example, the cause of the problem was found to be in lack of quality assurance in different stages of manufacturing. After researching the appropriate positions for gradual quality assessment in the flow of the process, the “Do” process can adjust the positions of current workers according to the research findings. The “Check” step gathers the data collected by the previous step and compares it to the data that was given after the changes. By creating a histogram of the speed of assessment before and after the implementation, this step allows the manager to see the effectiveness of the changes in the form of a simple diagram. After the results are compared, the “Act” process begins. At first, a scatter diagram could be created to document the results understandably. It would compare before and after statistics along with the axels of speed and quality of assessment.
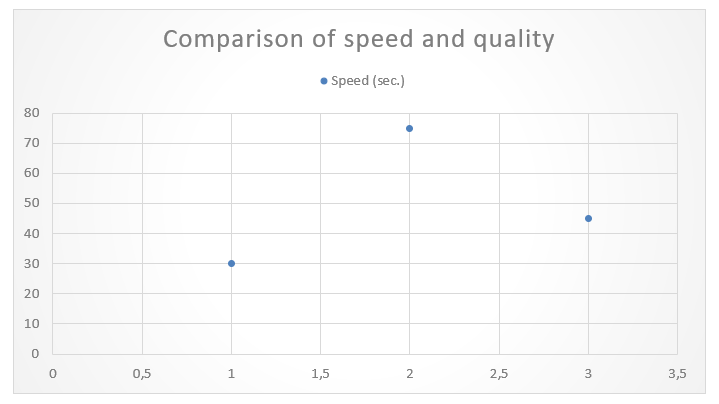
Then results are shared between the group and adjustments are made to create a more optimal quality assessment system. The desirable result is to have every part checked before it is fitted to the musical instrument to reduce the time of quality assessment by spreading it throughout the production line (Shah, Shamail & Ahmad 2015).
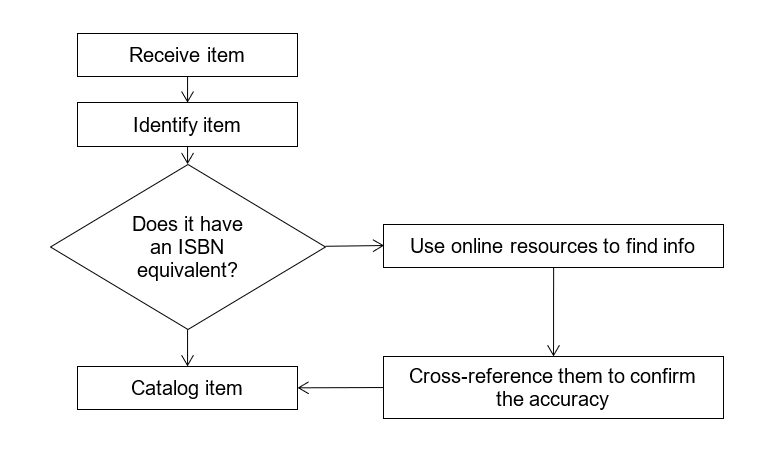
While the function of a library differs greatly from the function of a musical instrument manufacturer, they both can benefit from the implementation of the PDCA cycle. These days libraries have to carry a vast variety of media, including books, films, sound recordings, and even video games. This leads to a lot of work that has to be done to catalog all of them sensibly. The PDCA cycle could be utilized to make this a more efficient process. In the first step, a fishbone diagram could show which specific type of media is causing issues for the library (Bernardo et al. 2015). For example, the cause of issues is the process of game cataloging due to their lack of an ISBN equivalent. During the second step, alternative measures are researched. A possible solution could lie in free APIs (Application Programming Interface) available from online video game databases. Then, a scatter diagram could be used to compare different databases by the measure of response time to requests and the information available to them. The most appropriate one would be implemented. During the third step, the data can again use a histogram to compare the time needed to catalog video games before and after an API based solution is introduced. The last step would publish these results and would adjust the process by perhaps choosing a different API (Wright & Mutshewa 2017).
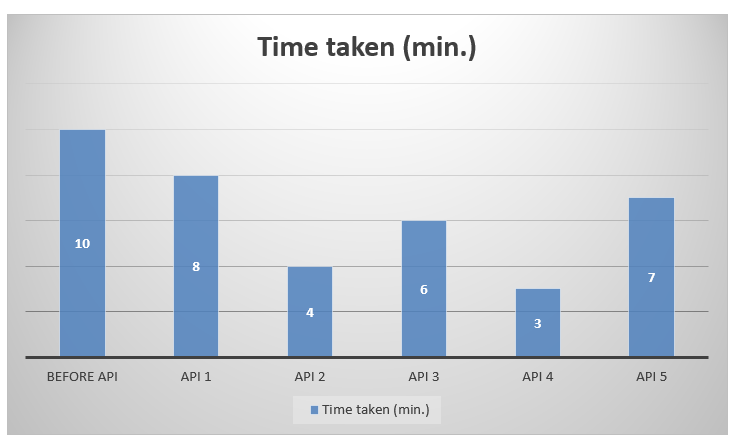
Both organizations would find it difficult to find the optimal method due to several options available. Music instrument manufacturing is a complex process that involves a lot of parts, and to choose the ones that get checked before the complete assembly of the instrument might take a long time (Mahmud et al. 2015). Consecutively, the amount of APIs and similar online solutions are also serious which would make the improvement process longer. However, the nature of these processes differs greatly. One relies on the speed of people and their positioning, while the other is dependent on the speed of the internet connection, and the amount of information available on those databases. Moreover, the library scenario would require outside help to create a cataloging interface based on the selected API, and with each change, it would need to be modified by the same outside party (Persson & Svenningsson 2016).
Conclusion
The PDCA cycle is a useful tool for any organization looking to improve its work processes. Through four simple steps and seven basic tools, it can improve the efficiency of almost any process by analyzing the problem, providing a solution, comparing the results, and adjusting for the next iteration to achieve continuously better results. By presenting it in such a simple way, Dr. W. Edwards Deming was able to create an important technique that does not take a lot of time to understand.
Reference List
Bernardo, M, Simon, A, Tarí, J & Molina-Azorín, J 2015. ‘Benefits of management systems integration: a literature review’, Journal of Cleaner Production, vol. 94, no. 3, pp. 260–267.
Hibi, S, Ina, K, Kabeya, M, Inoue, H, Shirokawa, Y, Nagaoka, M, Yokoi, S, Suzuki, A, Niwa, E, Kataoka, T, & Yuasa, S 2016. ‘Quality management of cancer chemotherapy using the Plan-Do-Check-Act (PDCA) cycle method by chemotherapy team’, Annals of Oncology, vol. 27, no. 7, pp. 2-4.
Mahmud, K, Nasry, M, Hilmy, I & Yusof, M 2015. ‘Development of a quality check station in a pharmaceutical industry to achieve zero defect production using PDCA cycle’, ARPN Journal of Engineering and Applied Sciences, vol. 10, no. 23, pp. 17421-17426.
Persson, S & Svenningsson, M 2016. ‘Librarians as advocates of social media for researchers: a social media project initiated by Linköping University library, Sweden’, New Review of Academic Librarianship, vol. 22, no. 3, pp. 304-314.
Pietrzak, M & Paliszkiewicz, J 2015. ‘Framework of strategic learning: the PDCA cycle’, Management, vol. 10, no. 2, pp. 149-161.
Shah, F, Shamail, S & Akhtar, N 2015. ‘Lean quality improvement model for quality practices in software industry in Pakistan’, Journal of Software: Evolution and Process, vol. 27, no. 4, pp. 237-254.
Silva, A, Medeiros C & Vieira, R 2017. ‘Cleaner Production and PDCA cycle: practical application for reducing the Cans Loss Index in a beverage company’, Journal of Cleaner Production, vol. 150, no. 3, pp. 324–338.
Wright, T & Mutshewa, A 2017. ‘Analyzing critical incidents stories to understand change management process in the adoption of e-resources at the University of Botswana library’, International Information & Library Review, vol. 49, no. 3, pp. 1-17.