Introduction
The production system is a definite source of competitive advantage to the national industry. Traditionally, sources of competitive success have been manufacturing technology, market regulations, exclusive access to financial resources, or economies of scale. Therefore, traditional literature seems to endorse that the production system has the possibility of providing competitive leverage to a nation or industry. Xerox gained production system leverage as it developed the first plain paper copier in 1995 and by 1972 enjoyed 90% market share (Pfeffer, 1994). As the product life cycle declined, there was a greater demand for better and technologically advanced production processes to gain a competitive advantage. The potent question that therefore arises is if nations have been able to gain a competitive lead in production and operations management? Have analysts overlooked more important differences between industries and companies? This paper argues that a production system can deliver competitive lead to a company operating globally (as in the case of Toyota) but may not be successful in delivering competitive advantage to the nation.
The production system is believed to provide a substantial competitive advantage to the company in helping the company gain a competitive edge. However, transposing these systems to another company in a different country may pose substantial alterations and problems. This point is argued by considering the case of the production system followed in the automobile industry in the US, Germany, and Japan. Given the recent popularity of lean production (a Japanese brainchild) the article tries to ascertain if this system is better and different from Taylorism and Fordism and if it can provide a competitive advantage to the nation and/or company.
Further, the article also discusses issues related to the adoption and implementation of the model in other national settings, for instance in US and German automobile companies. Therefore, the paper aims to understand if one process is good for all countries or companies and how they affect the performance of the companies. This is done with examples from three automobile industries in three different countries –Japan, the USA, and Germany. The paper will first discuss the popularity of the Japanese production system gaining unprecedented popularity and then enumerate using academic and industry-based literature on the strengths and weakness of such adaptation in other countries. The paper will provide a comparison between the three production systems i.e. lean manufacturing, Taylorism, and Fordism. The processing system will be evaluated concerning other management areas like human resources, supplier management, production strategy, and management techniques.
Comparison between Taylorism, Fordism, and Lean Production
The production system of Japanese automobile companies like Toyota has been believed to have a source of success for the company as well as Japanese automakers for a long time. Japanese production system had been adopted in entirety or partially by companies from other nations. Different processes like kanban cards and quality circles have been implemented by automobile makers in other countries. American companies like GM, Ford, and Chrysler have made the initiative to establish a Toyota-like production system, but few have been successful in adopting the system successfully even though the company has kept the system no secret. Spear and Bowen (1999) point out that other Japanese companies, like Honda and Nissan, have been able to replicate the success story of Toyota even when many academicians and practitioners believe that the unique success of Toyota’s production process is embedded in its culture. Organizational sociology suggests that organizational processes and their success are closely united to their environment. However, Toyota has successfully replicated its Japanese production system in its production plants in all other countries, including North America. This shows that the success of a production system as competitive leverage is more organization oriented rather than nation oriented. This is so because other Japanese companies like Honda and Nissan have not been successful in adopting the same production system followed by Toyota.
Taylorism was based on the division of work. Jobs were deconstructed into simple, routine tasks. The system made a definite distinction between the planning and execution process. The main aim of the system was to derive maximum possible profit for the owners, and minimum possible improvement for the workers. Therefore, in the case of Taylorism, laborers do not get any possible opportunity to innovate as they are bound to their tasks that usually are highly specialized, routine work.
In the case of Fordism, the system brought forth mass production through the implementation of the concept of the assembly line production process. These processes were operated by semi-skilled workers. Here too, not all branches of the business were associated with the production process. Further, Fordism presents a growth cycle process based on mass production. Like Taylorism, Fordism propagates separation of ownership from control. Usually, Fordism has decentralized organizations wherein lies multiple divisions and the control is centralized. Fordism encouraged the division of work like Taylorism and creating specialty skills. Further, it had a heavy reliance on machines for the completion of tasks. Fordism was a model developed in the US and created large, vertically incorporated firms. Like Taylorism, this system too had clear demarcation between intellectual and manual work. The difference between the two lies in the stress of Taylorism on management and control of the production process, and that of Fordism on the production line.
Presently there is a transformation that is in place in these countries moving from the classical ‘Taylorist’ or ‘Fordist’ production system (Morris & Wilkinson, 1995). There is a break from Taylorism and re-emergence of the importance of labor. Taylorism was associated with machine bureaucracy, lack of autonomy, centralized control over the production system, and deskilling. Therefore these apparent drawbacks are replaced with re-skilling of laborers and assigning of core production responsibilities (Morris & Wilkinson, 1995). The new form of a lean production system that is the brainchild of the Japanese production system is believed to do away with the Taylorism. Therefore the production regime that was earlier followed in auto production in the US and Europe is shifted towards extreme labor flexibility and work based on teams. A few characteristic processes therefore adopted in this respect are just-in-time (JIT) production, total quality control (TQC), kaizen (meaning continuous improvement), and waste elimination (Morris & Wilkinson, 1995). Therefore there is a shift towards greater autonomy and skill-building for laborers (Morris & Wilkinson, 1995). This is believed to be predominantly a Japanese production system.
Production
Academic research has shown that the Japanese model of production thus popularised through the Toyota success story has not become a universal success (James-Moore & Gibbons, 1997; Spear & Bowen, 1999; Lewis, 2000; Cooney, 2002). In many cases, automobile companies in other countries like the US have tried to adopt the Japanese system and have not been completely successful (Williams et al., 1995). In the case of Japanese
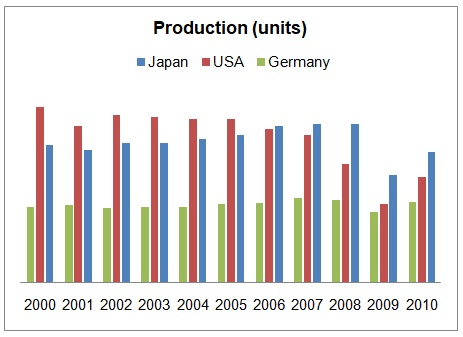
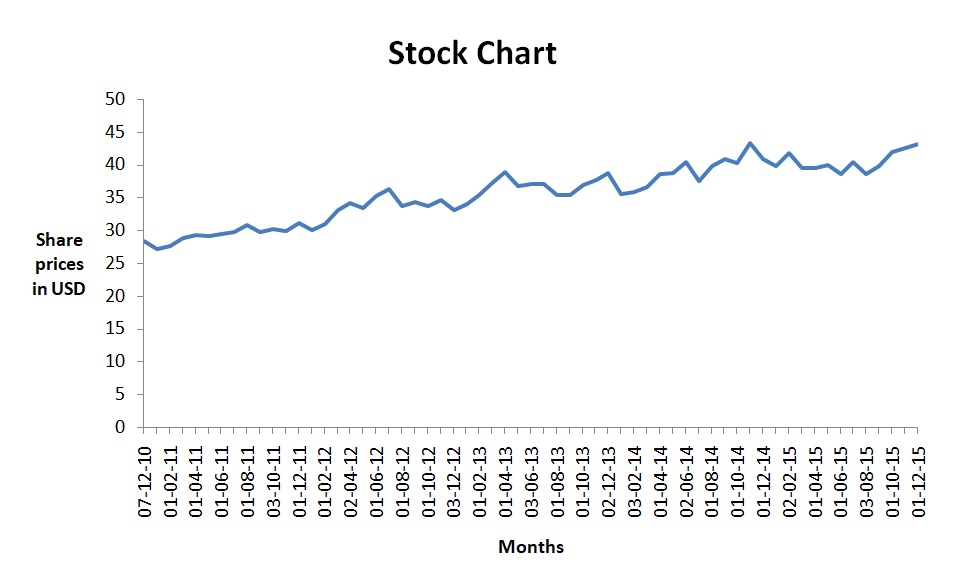
Comparing the total automobile production in the three countries over the last decade demonstrates that the US was the leader in total automobile production in the early half of the twenty-first century. However, in 2006, the production of Japan surpassed that of the US and continued to grow steadily. The percentage change in total automobile production (figure 2) has been stable for Japan but that of the US has been falling since 2004. German change in production has been stable mostly. However, all three countries experienced a decline in automobile production since 2007, as there was a slump in the auto industry due to the dampening of consumer demand and the global financial crisis. However, the industry recovered from 2009. The comparison of the production of the three countries is indicative of the present automobile industry’s position in the global industry. Presently Japan is the leading producer of automobiles, with Toyota being the world’s largest automaker.
Now the question that arises is what has helped Japan become the market leader and a stable producer of the automobile? Further, what procedure in production does Japan follow that has helped the country become the leading automobile maker in the world and helped it gain its reputation for quality? The third question that will be dealt with is if the other countries can replicate the production system of Japan and reap the same success? The next section answers the last question – is the production system of Japan replicable by the US or Germany?
Technology
Another break from the Taylorism is observed, however, that arrived from the German context (Morris & Wilkinson, 1995). This system provides a “technological fix” that provides great skill, training, and autonomy for the labor (Morris & Wilkinson, 1995, p.720). Further, the production system encouraged in Germany was based on “diversified quality production” (Morris & Wilkinson, 1995, p.720). This system is more dependent on technology. As new technology provides greater scope for organizations, there is the dilution of the line between small and large batch production and hence companies need not choose between mass and craft production and can be involved in both the processes (Morris & Wilkinson, 1995). Further, the German system helps in the production of a high volume of customized goods.
Given these two basic differences in the production system of Japan and Germany, it is observed that there is a greater acceptance of the Japanese system of ‘lean production’. Many German and American companies have adopted this system. The outcome of this move was that the Japanese automakers had attacked the niche markets that were dominated by the German cars in the 19990s such as the luxury auto market (Morris & Wilkinson, 1995).
Production system
The Japanese production system underwent a revamp in the 1950s with the help of American quality experts and ideas from the American “supermarket system of stock control” by Taiichi Ono who brought forth fundamental changes in Toyota’s production system (Morris & Wilkinson, 1995, p.722). This system was characterized by TQC and JIT that began diffusing in many western countries through the expansion of Japanese automakers globally. Technically, TQC and JIT are based on the ideal production condition of zero defect, inventory, and waste (Morris & Wilkinson, 1995). This opposed the western conventional production system that emphasized the cost of quality and operating cost of inventory (Morris & Wilkinson, 1995). The five elements of the Japanese system are as follows:
- The devolution of responsibilities to front-line workers;
- Their organization in work teams;
- Employee involvement in continuous improvement
- The use of visual factory controls; and
- The use of just-in-time to eliminate in-process buffers and eliminate waste. (Cooney, 2002, p.1132)
Therefore, this process makes the batch process and mass process outmoded. The proponents of lean production believe that it is in the flow concept of the system that makes its diffusion possible universally (Cooney, 2002). However, there has been considerable debate in Europe, especially the German automobile industry, and the effect it may have on the labor, as it usually requires de-unionization or single union contract, have become a problem for adoption (Lewis, 2000). German automobile manufacturers that adopted lean production in the 1980s and 1990s were less productive than their Japanese counterparts (Lewis, 2000).
It is believed that cultural impediment is a major setback for western automakers in the adoption of the Japanese system. James-Moore & Gibbons (1997) believe that the unique institutional environment makes the Japanese model more successful in Japanese than in German or American companies. Spear and Bowen (1999) believe that the main problem in adoption of the Japanese system is not culture or environment, rather it is the unwritten codes that are embedded in the system that makes “people capable of and responsible for doing and improving their work, by standardizing connections between individual customers and suppliers, and by pushing the resolution of connection and flow problems to the lowest possible level” (p.106).
Performance Comparison
The relevant question arises is that if one production system provides a sustainable competitive advantage to a company? In understanding this, we must first look at the change in the market share of the automobile companies in the market to understand the performance of each. Table 1 provides the market share of automobile companies in the US market (Ward Auto, 2011). The table shows that the
Table 1: Market Share of Automakers in the US Market, Source: Ward Auto.
The table demonstrates that American auto companies like GM, Ford, and Chrysler had demonstrated a decline in market share in the US market. In 1970 the market share of GM has been 38.93% that declined to 35.17% in 1990 and 25.59% in 2005 and then to 18.81% in 2010. Therefore, GM experienced a decline in market share in 2005 from 1990 by 27.2% and by 26.5% in 2010 compared to 2005. Ford too experienced a decline in market share in 2005 compared to 1990 by 28.4%. German companies like BMW and Volkswagen too experienced an increase in market share in 2005 from 1990 291.1% and 60% respectively. Japanese companies like Toyota experienced an increase in market share by 70% in 2005 from 1990 and 15.6% in 2010 from 2005. Therefore, it is apparent that Japanese companies have been doing well in the US market, and better than the American companies. These Japanese automobile companies especially Toyota have implemented the Japanese system of production in their American and European plants and have successfully implemented it. However, American companies like GM and Ford have adopted the Japanese production system and have not been able to replicate the model completely.
It is believed that lean production has the capability of producing sustained competitive advantage operating in a competitive environment (Lewis, 2000). It is believed that the system creates an internal business process from which the competitive advantage is derived. In face of competitive pressure, it is believed that these internal resources are thus created in face of the external environment that creates effective barriers for imitation of the production system (Lewis, 2000). This, therefore, helps in the creation of a sustained competitive advantage. The Japanese production system, viz. lean production, has the capability of creating such internal barriers that prevent other firms from imitating the internal processes. In a similar view, Spear and Bowen (1999) point out that it is the unwritten internal code that develops in Japanese companies that are embedded in the whole structure, culture, and management of the organization that is not observable and difficult to articulate. It is purely embedded in the working of the people in the organization, but not even the people can express what it is that makes the Japanese system a greater success (Spear & Bowen, 1999).
Human resources
The concept of lean manufacturing in the case of human resource management demonstrates that the Japanese model adopted a softer approach towards manufacturing. The Japanese approach as compared to the American or German production system provided greater autonomy, skill, training, and “visual control” (Oliver et al., 1996). The Japanese production system brought forth the stress on training, employee autonomy, and teamwork. The lean manufacturing system brought forth innovative HR practices that helped in improving the production of Japanese automobile plants (Macduffie, 1995). The most important aspect is the element of a flexible production system like lean production is that employees can apply their skills at their discretion. This was not present in less autonomous Taylorist and Fordist production systems. In a mass production environment, laborers are employed to perform narrowly defined roles. However, in the Japanese system employees have greater responsibility and job sphere that they can be innovative and have the voice to express their ideas (Macduffie, 1995). The philosophy also helps to inculcate problem-solving and developing the capability of inculcating a learning environment for its employees (Macduffie, 1995).
Conclusion
The production system can become a competitive advantage for a nation. Japanese production system it is observed that it has proven to deliver better performance than auto companies from the US or Germany. They have better manufacturing performance, better management systems, human resource management, and better market performance. Lean production has helped Japanese automotive companies like Toyota to beat US automobile companies like GM and Ford and enter the niche market that the German automakers commanded. Therefore, the production system of a country can gain a sustained competitive advantage.
References
Cooney, R., 2002. Is ‘lean’ a universal production system? Batch production in the automotive industry. International Journal of Operations and Production Management, 20(10), pp.1130-47.
James-Moore, S.M. & Gibbons, A., 1997. Is lean manufacturing universally relevant? An investigative methodology. International Journal of Operation and Production Management, 17(9), pp.899-911.
Lewis, M.A., 2000. Lean production and sustainable competitive advantage. International Journal of Operations and Production Management , 20(8), pp.959-78.
Macduffie, J.P., 1995. Human Resource Bundles and Manufacturing Performance: Organizational Logic and Flexible Production Systems in the World Auto Industry. Industrial and Labor Relations Review, 48(2), pp.197-221.
Morris, J. & Wilkinson, B., 1995. The Transfer Of Japanese Management To Alien Institutional Environments. Journal of Management Studies, 32(6), pp.719-30.
OICA, 2011.International Organization of Motor Vehicle Manufacturers. Web.
Oliver, N., Delbridge, R. & Lowe, J., 1996. Lean production practices: International comparisons in the auto components industry. British Journal of Management, 7, pp.S29-44.
Pfeffer, J., 1994. Competitive advantage through people: unleashing the power of the workforce. Harvard, MA: Harvard Business Press.
Spear, S. & Bowen, H.K., 1999. Decoding the DNA of the Toyota Production System. Harvard Business Review, pp.96-106.
Ward Auto, 2011. U.S. Vehicle Sales Market Share by Company, 1961-2010. Web.
Williams, K. et al., 1995. Management Practice or Structural Factors: The Case of America Versus Japan in the Car Industry. Economic and Industrial Democracy, 16(9), pp.9-37.