Project Structure
The first section of the project presented introduction and literature review about engineering capabilities and house of quality in the oil and gas industry. These studies show that a focus o house of quality can improve engineering capabilities and customer requirement outcomes.
The second section of the paper presented research objectives with a focus on the relationship between engineering capabilities and customer requirements, which forms the research hypotheses.
The research method section shows the research design. The is a mixed methods approach that combined both qualitative and quantitative research methods in order to understand how high standards of engineering capabilities would affect operational efficiency and customer satisfaction at Emirates Gas LLC.
It also has data collection method. The researcher collected relevant data through questionnaires and interviews with operation managers and supervisors.
The data analysis and study result section showed that the researcher used descriptive analysis for tables, percentages, and frequencies while SPSS was used to show the correlation between improved engineering capabilities and improvement on customer requirements.
This analysis also confirmed the research hypotheses. Finally, the paper presented recommendation on house of quality and conclusion by showing that improved engineering capabilities led to increased customer requirements, satisfaction, and retention.
Research objectives
- To address and examine the company’s technical capabilities (engineering capabilities).
- To understand and prioritise needs of customers.
- To understand operational challenges and recommend methods of enhancing them.
- To explore the relationship between engineering capabilities and customer requirement.
Research hypotheses
- high standards of engineering capabilities would not lead to operational efficiency and customer satisfaction.
- high standards of engineering capabilities would lead to operational efficiency and customer satisfaction.
Research Method
This study used a mixed methods approach that combined both qualitative and quantitative research methods in order to understand how high standards of engineering capabilities would affect operational efficiency and customer satisfaction at Emirates Gas LLC. The researcher used a mixed methods approach in order to achieve the following advantages.
First, the study achieved the research validity by using triangulation. Triangulation entails verification of evaluation results. For instance, the researcher would use both qualitative and quantitative approaches in order to assess impacts of high standards of engineering capabilities on operational efficiency. Second, the researcher ensured validity and interpretability of the process through a mixed methods approach.
Qualitative study
A qualitative approach allows for an effective way of understanding research aspects when not much is known about the research issue (Creswell, 2008; Johnson and Christensen, 2010).
A qualitative approach ensured that the researcher gathered information for in-depth analysis of impacts of engineering capabilities and formulated effective ways of developing appropriate interventions for house of quality for customer service enhancement. In other words, the researcher was able to offer a comprehensive view of the research (Steinberg, Bringle and Williams, 2010).
The qualitative research approach is an iterative method to study the engineering processes, house of quality, and customer satisfaction at Emirates Gas LLC. Thus, the researcher relied on discovery methods in order to find effective ways of gathering the needed information.
In this regard, the researcher reviewed available studies in order to identify a general theme or pattern in engineering capabilities and customer service outcomes. Still, this method allowed the researcher to change the study in order to provide new points of view based on emerging themes.
This was an iterative process, which the researcher conducted several times before data analysis and interpretation of the findings. It ensured that the researcher collected only relevant data in the study as the process unfolded. Patton suggests the use of an open-ended approach in this type of study (Patton, 2002).
Nonetheless, the researcher specified what areas of the study to focus on prior to the beginning of the study, but he noted that these areas of the study were subjected to changes as the study progressed and new methods of inquiry emerged.
The study design was exploratory in nature. The approach was suitable for the research because the researcher aimed to explore and understand impacts of quality practices at the firm. As a result, the researcher interviewed operation managers and supervisors to understand technical capabilities and customer satisfaction.
Qualitative study accounted for non-numerical factors in study. Hence, this approach provided descriptive and interpretative data for the study. On the other hand, quantitative method addressed numerical data collected for the study (Trochim, 2006). In addition, it allowed the researcher to offer high-levels of confidence in the study inferences.
How data were collected
The researcher conducted several interviews with the company’s operation managers and supervisors. In addition, there were also other interviews with employees, who work at the House of Quality. These interviews allowed the researcher to gather relevant data for the study.
The information and the sources of information
Key people at operations, supervision, and house of quality provided relevant information for the study. The researcher also gathered data from the company’s database about customer service outcomes.
Researcher also reviewed available publications, which acted as secondary sources of information for the study. On the same note, the researcher also reviewed information available on the company’s Web site and compared them with information from other sources in order to draw conclusive outcomes.
The researcher did not collect data from other stakeholders outside the company.
The measures were developed
The researcher provided a detailed background account of the study, objectives, and questions of the study. The study concentrated only on participants who could provide relevant data in order to answer research questions and objectives. The researcher used purposive sampling in this study.
Steinberg and fellow authors observe that qualitative researchers “purposefully sample the specific documents, artefacts, people, and programmes that are illuminative and that they believe will provide a great deal of information related to the purpose of the research” (Steinberg et al., 2010).
The researcher generated measure or questionnaires for the study. The researcher used contents from research outcomes to develop measures for the study with the aim of linking the study instruments with the study purpose i.e., to measure the success of the engineering capabilities against customer satisfaction at Emirates Gas LLC.
These involved analysis of customer satisfaction, competence, skills, and application of such technical capabilities to enhance efficiency at the company. Hence, the researcher defined what the study measured in terms of employees’ knowledge, skills, attitudes, opinions, behaviour changes, and perceptions in relation to the service environment of the company. These different areas of study formed key study variables.
The researcher used Likert scale to quantify some aspects of study instruments.
The researcher established validity of the questionnaire by reviewing instruments with a panel of experts on the field of study and conducting a test. The researcher ensured that the questionnaire was valid, i.e., the questionnaire had to “measure what it was intended to measure” (Norland, 1990). It also represented the study content, was suitable for various participants and comprehensive to gather enough data for the study.
The researcher also obtained approval from faculty and ensured that the study met all ethical standards (Pimple, 2006). He then conducted a test with different participants and made changes to questionnaire based on the test outcomes.
The researcher used pilot test results to establish reliability of the study questionnaires. The aim was to ensure that the questionnaire was consistent with what it was designed to measure. Overall, the researcher followed “appropriate and systematic procedures in questionnaire development, testing, and evaluation to avoid undermining the quality and utilization of data” (Esposito, 2002).
The data collection methods
The researcher used an interview to collect information from operations departments, supervisors, and house of quality because it was an effective method for exploratory qualitative research. He carried out the interview in person. Interviews provided the researcher with the chance to collect in-depth information from relevant respondents.
The study had open-ended questions, and the researcher made sure that respondents were free to say anything (Steinberg et al., 2010). The researcher recorded responses from the respondents by using a tape recorder. Afterwards, the researcher transcribed data for analysis (Patton, 2002).
The study also relied on a focus group from the company to collect data. The focus group offered the advantage of interaction among study respondents and review of comments by the group. The researcher eliminated problems of uneven contribution. In addition, focus group discussion saved time for data collection. Members of the focus group contributed as a team towards the study objectives.
However, Steinberg and colleagues point out that a focus group has some challenges. For instance, certain members of a group could dominate others from active participation while in some instances, the study design may be time-consuming because of comprehensive contents and subsequent lengthy discussions.
The researcher kept data safe. All collected data remained confidential throughout the study. The researcher would publish results of the study in the evaluation report.
The methods of data analysis
The researcher shall clean data collected and determine data accuracy. He then proceeded to code data into emerging patterns or themes depending on participants’ feedback.
The researcher applied methods used in both quantitative and qualitative methods to analyse data collected. The researcher used frequency, graphs, and tables for quantitative data analysis. SPSS software was used for this process (Pallant, 2005).
Conversely, the researcher applied qualitative methods such as content analysis for reviewing customer satisfaction and engineering capabilities for themes and patterns in the company. Content analysis is the hallmark method in “social science methodology that deals with the understanding of the content of the message” (Steinberg et al., 2010).
Table 1: Data Analysis Plan.
Data Analysis and Study Results
Address and examine the company’s technical capabilities (engineering capabilities)
The study result indicated that Emirates Gas LLC faced challenges from three core areas, which included price volatility, technology changes, and regulatory requirements. From the perspective of quality improvement, technology changes affected engineering capabilities within the organisation.
Ten participants took part in the study. From the data collected, they attributed frequencies of general factors that influenced the oil and gas industry as shown in figure 1. Many supervisors and managers believed that technological changes had major impacts on their operations (32%) while regulatory conditions (11%) had least effect on their operations.
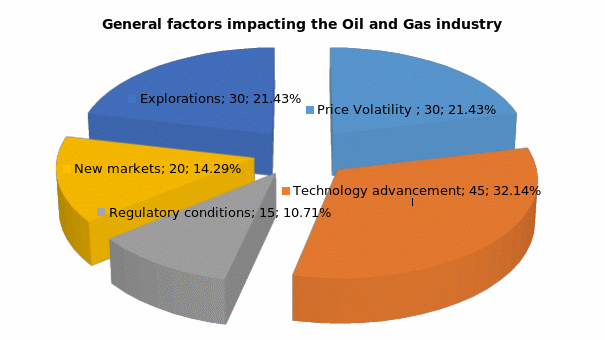
The company’s engineering concentrates on product development and support, plan design engineering, explorations, new market opportunities, field services for customers and accessory systems design. All these factors contribute to risks and challenges for Emirates Gas company.
With these new challenges, the researcher established that operation departments, supervisors, and house of quality were working together to offer the best plan design engineering and product development related to gas and oil products, equipment, and accessories.
The focus of the company has been on improving upstream accessories for exploration, accessories for midstream applications related pipelines, gas supplies, and power generation, and downstream accessories for oil and gas refineries and petrochemicals.
Today, Emirates Gas LLC believes that it has trained engineers with key knowledge and good communication skills. In addition, the company maintains that its team can manage and execute technical engineering projects that meet global standards, drive projects through all stages to maturation, and ensure quality deliverables for efficiency.
Value Proposition
From these technical capabilities, Emirates Gas aims to create value propositions that would enhance the quality of supply, lower costs of product developments and delivery, increase revenue growth, customer loyalty and acquisition, reduce time for product delivery to markets, grow its capacity, engineering capabilities, and sustain technical engineering skills.
These are the core areas, which the company concentrates on as value chain in service and product provisions.
Understanding and prioritising needs of customers
Emirates Gas LLC faces new challenges related to customer needs and opportunities to offer efficient and innovative customer service. In addition, there are also changing energy regulation requirements in Dubai, limited technical knowledge, pressure to deploy sustainable supply chains and specialisation in products.
In addition, the company has a challenge of collecting and maintaining one source of real-time customer information. This inhibits EMAS from making and changing customer needs to its core business priorities.
Customer needs
- Timely delivery of products, especially LPG.
- Reliable pipelines for LPG.
- Cost effective products.
- Effective communication and relationship management.
- Affordable products.
Operation managers and supervisors prioritised customer requirements on a scale of 1-5. The most common need was timely delivery of products or LPG as shown in Figure 3. Many customers (46%) showed that the company had not met this requirement adequately.
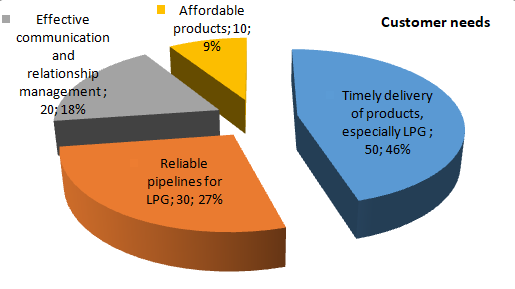
Although the company has identified several customer needs, prioritising these needs remains a major challenge because of technical challenges and capabilities. Moreover, the company systems are fragmented and do not support a single point for managing and prioritising customer experience and needs.
The company needs to understand and prioritise needs of its customer from a technical point of view by managing engineering technical capabilities effectively.
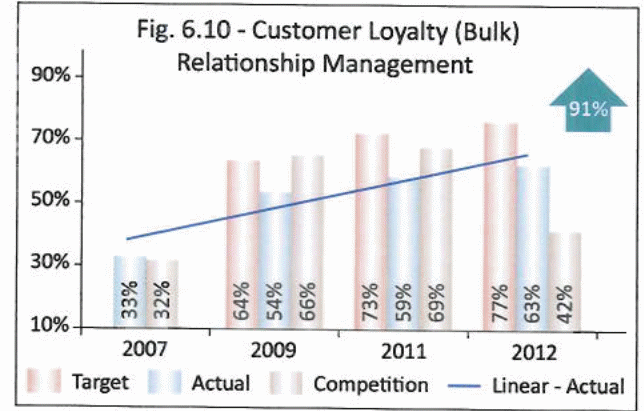
For instance, the company has noted challenges with LPG and customer relationship management. This situation has affected customer loyalty. Although EMGAS has not been able to meet relationship management, it has made significant improvement, which has positioned it above competitors.
The company has prioritised relationship management through customer segments, recruitment of additional marketing executives, dedicated customer care, and frequent visits to customer places. These initiatives have improved relationship management at EMGAS.
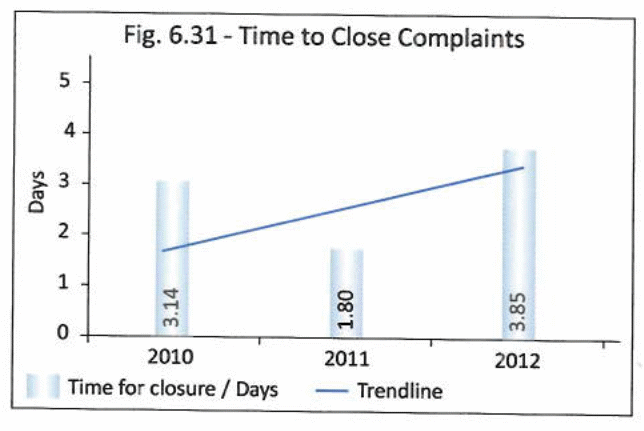
The company’s time to close customer complaints has increased significantly. For instance, in 2011, it took an average of 1.8 days to close a complaint while in 2012, it required 3.8 days to close a complaint. The challenge has been due to fragmented processes in different departments of the company.
Although the nature of customer complaints may differ, the company must conduct site visits and understand the problem within different departments. On this note, EMGAS needs to streamline its operations by improving its engineering capabilities.
Understanding operational challenges and recommending methods of enhancing them
From the study results, the company’s major operational challenges include regulatory requirements, market volatility, cost reduction and optimisation, infrastructure, and knowledge gap.
Regulations
The oil and gas industry experiences changes in regulatory requirements, which constantly change across different geographical locations. These changes affect EMGAS operations. As a result, it is necessary for the company to prepare for constant changes and uncertainties that affect its business processes and conform to emerging standards on a continuous basis.
EMGAS has not been able to manage these constant changes and uncertainties because of a lack of flexibility, tribal slow processes, inadequate problem documentation, process repeatability, and poor operational change management, which result in high costs for the company.
Cost control
EMGAS wants to reduce costs and optimise in all departments. This situation could lead to compromised customer service, service delivery, and quality of products. Customer service should remain a top priority for the company. Hence, the engineering department should enhance its technical capabilities in order to assist in customer service improvement.
Infrastructure
Although EMGAS tends to have sufficient infrastructure to support its operations, constant changes, environmental regulations, and equipment break down have made it difficult to maintain the necessary assets for continued operations. The company has pipelines, cylinders, trucks, IT systems, and gas chambers among others, which require constant maintenance. Maintenance of these assets results in huge costs and time.
Knowledge
While many people may retire in a company with over 40 years of operations, new technologies present challenges to engineering capabilities in the company. People who are likely to retire will go with their knowledge and experiences. The company will strive to fill these gaps with a younger generation of workforce. This is a significant change, which will affect operations of the company.
EMGAS has a challenge of capturing, storing, and sharing knowledge. In addition, it has not automated knowledge into Web based applications that can enhance operation processes and leverage business across different departments.
Market volatility
The oil and gas industry experiences constant market volatility and price changes. These factors require high-levels of agility that EMGAS may find difficult to sustain. For instance, it is extremely difficult to understand or predict sales patterns and manage sales revenues and profitability.
Customer related challenges for the company
EMGAS believes in a strong customer perception. Although some customers perceive the company has reliable, professional, and trustworthy firm that delivers products and services as required, this is not the case across different market segments. There are several complaints in the LPG industry. Safety is a fundamental concern for the company.
Hence, the company strives to deliver high standards of safety without comprising qualities. These customers have appreciated such safety standards by the company. EMGAS conducts pre-delivery inspections and offers customer training and technical support to customers, contractors, and others. These capabilities have established EMGAS as safety-oriented company in the industry.
The company supplies gas to customers through pipelines. However, break down in pipelines coupled with failures to repair them in a timely manner have affected operations and customer loyalty.
The company aims to eliminate such challenges with fleets of trucks for delivery. In addition, the company strives to use well-trained and knowledgeable employees who are able to assist customers. Overall, the company’s capabilities offer several features and benefits.
The company has nearly 40 years of experience. It should be able to offer reliable, customised, and high standard solutions. These are competitive advantages for EMGAS.
Reliability is a challenge in the oil and gas industry because of the issue of constant changes in the market. The public perceives government entities as ineffective and highly bureaucratic. Many consumers believe that private firms are highly competitive than public firms.
The company aims to enhance reliability through an efficient supply system, heavy investment in infrastructure and working closely with regulators who set environmental and safety standards for LPG.
Another challenge from customers’ perspective is dependability. EMGAS is a certified company, which should offer quality products and services. Engineering capabilities of the company should account for environmental friendliness, quality products and services, efficient processes, reliability, and safety.
However, the company has not been able to utilise an integrated system, which could enhance product features and safety. Concerns for safety and professional procedures remain the hallmark for a professional company in the oil and gas industry.
EMGAS strives to be the best oil and gas firm in the region by offering different products and services. These efforts have enhanced customer acquisition, retention, and loyalty to the company. However, the global challenges and a focus on clean gas have presented significant issues to EMGAS.
EMGAS aims to develop strategic partnership with other stakeholders through its products and services. For instance, the company aims to offer periodic testing, site storage for LPG, and a fleet of road tankers for efficient services to ensure product availability. Despite these efforts, customers still complain about delayed product deliveries and pipe connections.
Engineering capabilities of the company has allowed it to offer several services to consumers and distributors. For instance, EMGAS offers technical advice and consultancy services at no costs. In addition, there are also safety training on LPG, audits, prevention of dry-outs, cylinder maintenance, and efficient night delivery system for public safety.
These are service-oriented approaches to LPG services. However, they are extensive and costly in nature to the company. Therefore, the company should use its engineering capabilities to maximise efficiency, reduce costs, and provide high quality services to customers.
Innovation remains a major challenge in the company because of constant changes in technology and customer needs. However, EMGAS strives to use modern technologies to manage customers’ orders and booking. The system offers instant confirmation, tracking, and processing for customers. Remote monitoring of LPG levels minimises risks and prevents low stock levels and business interruption.
The company also has Customer Care System for prompt management of customer concerns. However, such services have remained challenges because EMGAS has not been able to deploy a single system that can integrate all customers’ issues across various departments. Hence, constant delays in solving customers’ issues are common.
Exploring the relationship between engineering capabilities and customer requirements
The engineering capabilities of EMGAS have improved some of the customer requirements significantly. This confirms the research hypothesis that high standards of engineering capabilities would lead to operational efficiency and customer satisfaction.
For instance, a focus on In time Every Time-deliveries increased significantly due to increased focus on meeting customer requirement on LPG deliveries. The company has been able to surpass the target by five percent within two years consistently. This shows that improved engineering capabilities could enhance operational efficiency and meeting customer requirements.
Multiple regression between relationship management and improved focus shows a linear increase in relationship management/customer loyalty.
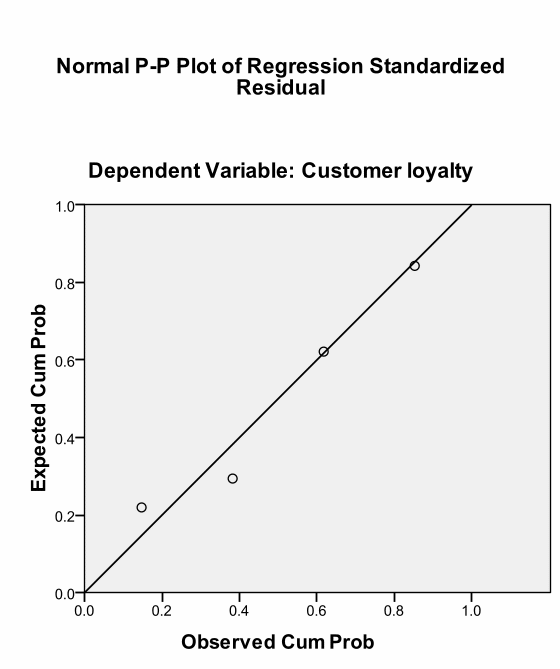
[F (1, 3) =10.8, p<.081).
Although p value is <.081, which indicates no statistical significance between improved in engineering capabilities and customer relationship management/loyalty, the relationship remains linear to show that changes in customer requirements and improved engineering capabilities affect each other.
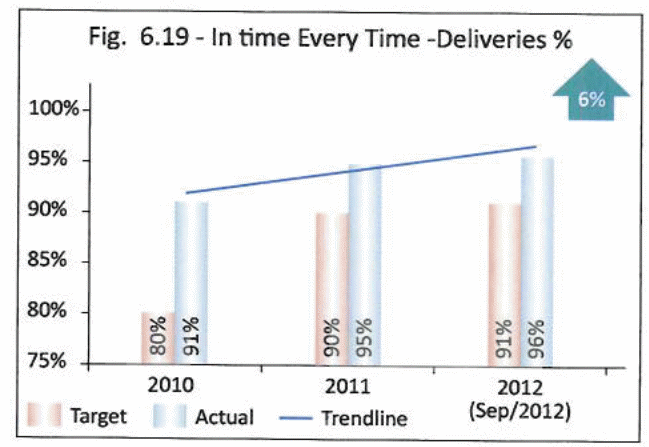
Compliance and regulations
The engineering capabilities should include updated processes and automated document management system. The company should be able to access and deploy the system globally to enhance business agility and processes. At the same time, it should be able to respond effectively to regulatory requirements fast.
In addition, engineering capabilities should allow the company to identify process challenges and non-conforming procedures and provide updates in an efficient manner. It would be simple for EMGAS to change processes and resources as required in order to operate in safe, efficient, and profitable manner.
Market volatility
EMGAS will have to focus its engineering capabilities on identifying systems or approaches that work and those, which do not work and identify how to improve business decision making and enhance business productivity in a volatile global market.
Knowledge gap
Engineering capabilities should allow the company to capture and document knowledge in the company gained over several years of operations. Such knowledge could be transferred to other employees, who may deploy it to enhance business operation processes.
Cost reduction and infrastructure optimisation
Engineering capabilities of the company should provide online platforms that should allow different departments and external partners to understand and indentify different infrastructures for changes, expansion, upgrade, replacement, or retirement.
Data collected over the years could help the company to manage these processes with minimal interruption to customers and at low costs. Such engineering capabilities enhance effective decision-making within the company.
Potential Benefits of engineering capabilities on customer requirements
The major aim of this research is to identify how EMGAS can improve operations, performance of the production systems, customer services, and reduce costs through quality management processes. Improvement on engineering capabilities would lead to the following advantages for the company (Shillito, 1994).
- The plant would operate efficiently at optimum pace as possible
- It would optimise operational costs, reduce risks, enhance safety of LPG observe product development processes, and environmental concerns and government regulations
- Improvement in engineering capabilities would result in automated business processes and procedures. This would enhance efficiency across departments, in the supply chains, and among different stakeholders.
- Improved engineering capabilities within the organisation would lead to improved decision-making processes, enhanced productivity through process management, and provisions of relevant data. These activities would enhance customer service.
- Data captured would provide new insights for improving overall business processes, response time, and infrastructure management.
- Enhanced engineering capabilities would drive the business globally and empower management team to increase business presence and operations
- Deploying relevant quality management infrastructure, skills, and knowledge help in protecting investments and stakeholders, including customers.
Matrix Correlation
Customer requirements have strong relationships with the company’s engineering capabilities. For instance, the study showed that a focus on customer requirements with engineering capabilities led to strong positive outcomes. Hence, when EMGAS improved its engineering capabilities and focused on customer requirements, customer satisfaction and retention increased significantly.
Strong positive correlation exists between improving engineering capabilities on timely delivery. Customers would get their products when needed. However, the company performs poorly on this end.
Strong correlations also exist between pipe repair and safety of users. The evaluation indicates that the company has scored poorly in critical areas. As a result, there is a need to improve engineering capabilities in several areas.
Constant supply of LPG would increase if the company improves on its communication strategies. The major issues remain the reliability of pipes and LPG deliveries. Competition is not severe in the UAE because of monopoly in the oil and gas industry.
Conclusion
The study has shown that improved engineering capabilities lead to improved customer requirements. While EMGAS strives to improve its customer service, the company experiences challenges related to market volatility, regulatory environments, knowledge gap, cost implications, and infrastructures have affected operations and customer service.
The study established that the company faced considerable challenges with LPG, particularly in delayed deliveries and pipeline connections. In addition, the number of complaints decreased slightly while time taken to resolve such complaints increased.
On this note, the study established that several operation processes were highly fragmented in different departments and there was no a single or an integrated platform for managing customer enquiries or complaints. This resulted in elongated procedures for resolving issues.
The researcher noted that investment in the House of Quality, new technologies, and knowledge management would help in tackling different operational challenges in the company. Hence, the company could enhance customer requirements and service through improved house of quality.
References
Creswell, J. W. (2008). Research Design: Qualitative, Quantitative, and mixed methods approaches (2nd ed.). Thousand Oaks, CA: Sage Publications.
Esposito, J. (2002). Interactive, multiple-method questionnaire evaluation research: A case study. Charleston, SC: QDET.
Johnson, B., and Christensen, L. (2010). Educational Research: Qualitative, Quantitative and Mixed Approaches (4th ed.). Thousand Oaks, CA: Sage.
Norland, E. (1990). Controlling error in evaluation instruments. Journal of Extension, 28(2), 1.
Pallant, J. (2005). SPSS Survival Manual. Sydney: Ligare.
Patton, M. Q. (2002). Qualitative research and evaluation methods (3rd ed.). Newbury Park, CA: Sage.
Pimple, K. (2006). Protection of human subjects in non-biomedical research: A tutorial. Web.
Shillito, L. (1994). Advanced QFD Linking Technology to Market and Company Needs. New York: Wiley.
Steinberg, K., Bringle, R., and Williams, M. (2010). Service-learning research primer. Scotts Valley, CA: National Service-Learning Clearinghouse.
Trochim, W. (2006). The Research Methods Knowledge Base, 2nd ed. Cincinnati, OH: Atomic Dog Publishing.
Research Questions
- The company’s technical capabilities (engineering capabilities)
- What does the company consider as its engineering capabilities?
- What are the major challenges in the oil and gas industry from engineering capability perspective?
- How does EMGAS improve its engineering capabilities?
- How does the company support customer requirements through its engineering capabilities?
- Understanding and prioritising needs of customers
- What are the priority needs of customers for EMGAS?
- Please rate the identified needs above on a scale of 1-5, where 1 shows the most common and 5 the least common.
- Does the company adhere to and satisfy customer requirements through its engineering capabilities?
- What are the most common customers’ challenges for EMGAS?
- How would you rate the company’s engineering capabilities and meeting customer requirements [1 represents the lowest score while 5 represents the highest score] please tick within the box
- To what extent do you think improved engineering capabilities have solved customers’ problems
- Understanding operational challenges and recommending methods of enhancing them
- Could you mention operational challenges that EMGAS faces?
- Please rate the severity of these challenges based on the following criteria
- How do different departments of the company handle operational challenges from different units?
- What is the average time it takes (turnaround time) to solve a single a case of customer complaint?
- What do think are the best approaches for overcoming these operational challenges and customer requirement issues?
- The relationship between engineering capabilities and customer requirements
- How does the company incorporate house of quality with engineering capabilities
- Do house of quality activities increased customer requirements
- How should the company enhance its engineering capabilities through house of quality?