Introduction
Total Quality Management (TQM) is a strategic management concept that believes in building quality into the cultural fabric of an organization. A proper implementation of quality will ensure high product quality, increased productivity, lesser rejections and improve the bottom line of the company along with increasing the customer satisfaction. The concept has been increasingly used in diverse industries such as manufacturing, service and hospitality industries, government organization, defense and so on.
- Discuss your performance in the simulation. List three areas of quality management in which you increased your knowledge, and explain why.
The simulation was run to assess the impact of decisions on various manufacturing and process techniques. The three areas that were of quality management in which my knowledge was increased was: manufacturing using Pareto and Control Charts, Analysis of suppliers and training of employees and their involvement in various quality management initiatives by forming work groups. The manufacturing areas were analyzed to understand the defects in the four stages and this helped us to find out the exact areas of defects by using the fishbone analysis tool. We were able to examine the trends for each stage and understand how much each stage contributed to the defect. The analysis of vendors helped us to determine which supplier was good and could be retained and which had to be dropped. A breakup of the employees helped us to determine the skill level of the employees and understand their training needs. The employees survey helped us to assess the employees understanding and acceptance of quality improvement goals and devise suitable training methods.
- What steps would Seguro take to implement a TQ process?
Seguro should take a look again at its key stages of manufacturing, supplier evaluation and employee training and involvement in quality systems. The company should adopt the system of Plan > Do > check > Act. The four key problem areas are: Stamping, Welding, Riveting and injection molding. A screen shot of the problem areas is shown.
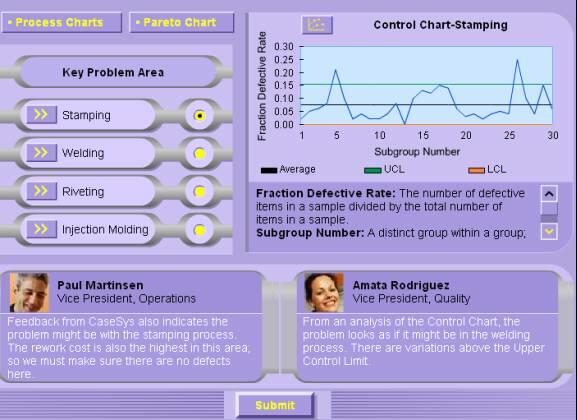
The following Pareto chart shows the extent of rework caused by the Stamping process is the highest. Hence this process is considered as the key problem area.
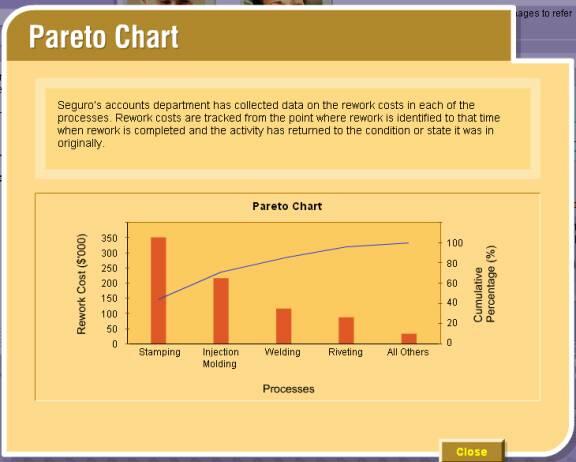
- Four progress summaries in the simulation
Stamping process was taken up as a key problem areas since the The four progress summaries are:
For the Stamping operation
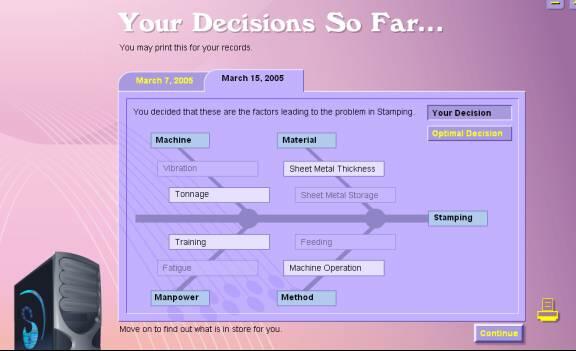
The cause and effect diagram is a means of visualizing how the various factors associated with a process affect the process’s output. Manpower, machine, materials and methods are the cause categories and stamping is the effect.
Strategies for employee improvement
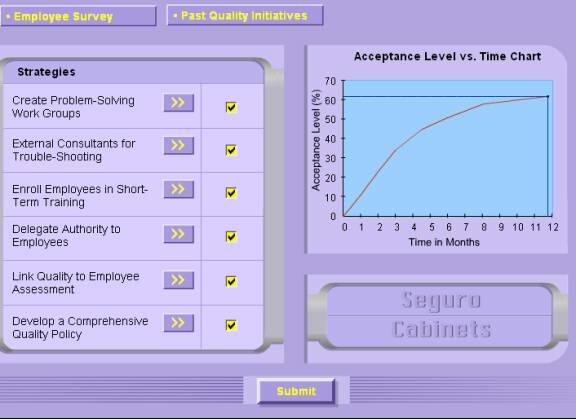
Creat problem solving working groups, external consultants for trouble shooting, enroll employees in short term training, delegate authority to employees, link quality to employee assessment and develop a quality policy.
Decision for employee involvement
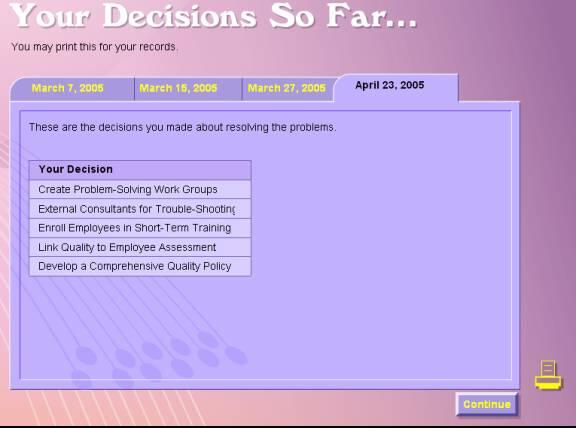
Supplier Evaluation
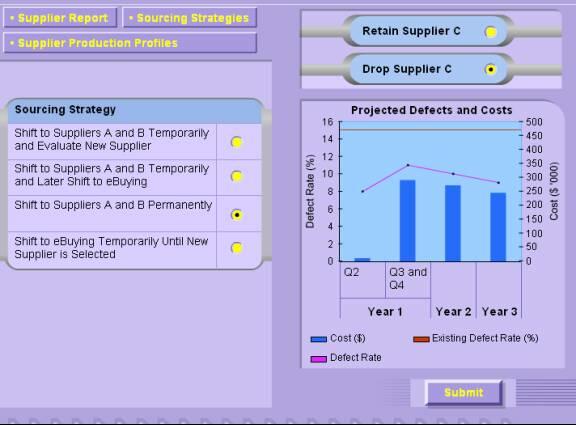
Supplier C has a high defect rate and needs to be dropped a s the sheet metal quality supplied is bad.
Conclusion
We have identified Stamping as the key problem area and the machine tonnage and sheet metal thickness as the main causes. The Supplier C is supplying sheet metal and needs to be dropped. Also employee participation needs to be ensured by involving them in work improvement teams. The employees should be empowered to take a decision regarding quality.
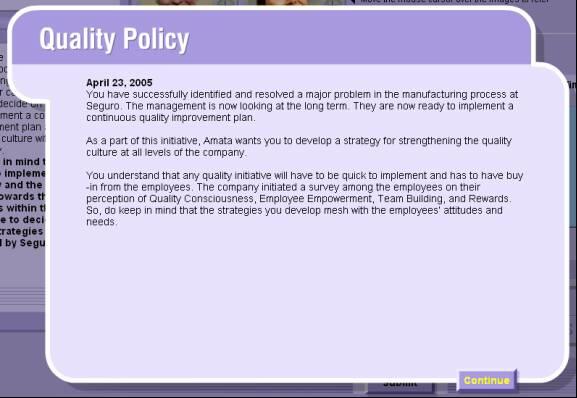
References
Burrill Claude W., Ledolter Johannes. (1999). Achieving Quality Through Continual Improvement. Web.
Steve Melnyk. Morgan Swink. (2007). Value-Driven Operations Management: An Integrated Modular Approach 1/E.
Wadsworth Harrison M., Stephens Kenneth S. (2002). Modern Methods For Quality Control and Improvement, 2nd Edition. Web.