Introduction
Vibration in mechanical equipment and machine is a sign of trouble before failure. A machine foundation either experiences static loading condition or a combination of static and dynamic loading conditions. The latter is the focus of present article which focuses on the vibration of rotating equipment such as turbines, compressors, fans, motors, and pumps. Vibration in rotating machines occurs because the centre of rotation of a machine does not coincide with center of mass (Figure 1). Vibration is undesirable for a number of reasons in many domains, especially in engineering. There are a lot of methods that have been developed to prevent vibration in engineering systems. It has been found out that some mechanical linkages are able to conduct vibrations more effectively than others.
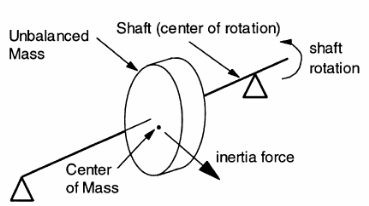
To reduce the magnitude of unbalanced forces all the rotating components of reciprocating components of a machine should be balanced. Machine foundation needs special consideration as it acts as a link between rotating or vibrating machine and soil (Derrick and Derrick 3). Based on vibration theory all the mechanical machines can be divided into three types namely,
- Reciprocating machines: This type of machines transmits unbalanced force periodically to the foundation.
- Impact machines: This type of machines impart impact loading.
- Rotary machines: This type of machines impart dynamic load that fluctuates from minimum to maximum in a periodic manner.
The vibration from a rotating machine transfers to the foundation and surrounding equipment in the form of noise and spatial vibration which degrade the performance of surrounding machines. This article focuses on identifying how the foundation of rotating machines gets affected due to vibration. Further, this article considers design consideration of rotating machines.
Machine imbalance is the most common cause of vibration in rotating machines. Imbalance is special situation where the rotating axis does not coincide with weight distribution or the weight is unevenly distributed. There are three kind of mass imbalance:
- Static imbalance or force imbalance: Static imbalance occurs when a heavy lump of mass is located away from the axis of rotation.
- Couple imbalance: Couple imbalance occurs when the weights are distributed unevenly across the axis of rotation. Though the axis of rotation and centre of mass coincide, when machine starts to operate, the unevenly distributed weight develops an unbalanced force. This unbalanced force causes the vibration.
- Dynamic imbalance: This combines the two cases above when static and couple imbalance leads to vibration.
Most common causes of machine imbalance are corrosions, uneven mass distribution or electric winding, dirt deposition, manufacturing defect, crack, incorrect keyholes, or machine errors.
Engineers engage in the design and repair of machine foundations. As vibration reduces the efficiency of machinery, these heavy rotating machines require support structure to resist static and dynamic forces (Edwards et al. 8). In this respect, the design of machine foundation is important in order to reduce the unnecessary vibration in machines. The scope of present study deals with vibration generated in rotating equipment and design of suitable foundation to control vibration.
Methodology
This section discusses methods used for vibration isolation in rotating machine. Figure 1 shows a schematic diagram of an unbalanced force in the rotating machines. The unbalanced force in rotating machine is produced because the center of mass of machines does not coincide with the center of rotation. This dynamic force is a function of the magnitude of the offset between the center of mass and center of rotation, the speed of rotation, and the mass of machine.
First, an analytical spring-dash pot model is considered for a rotating machine as shown in Figure 2. This analytical model comprises of a rigid rotor in a bearing house, which is attached to a rigid foundation by means of isolator such as springs. Consider that the rotating machine has a static unbalanced mass mr e, where e is the rotor eccentricity and mr is the mass of rotating component or machine rotor. According to D’Alembert principle states that this is equal to the force experienced by a stationary rotor which has a radial force of magnitude mr eW2 where W is the angular velocity (Nelson 13). To simplify the calculations only vertical motion of the machine is considered i.e. the model has single-degree-of-freedom (SDOF) in the vertical direction and it is constrained from the sides as shown in Figure 2. Another assumption of this model is that this model has viscous damping of ratio of z. The forces acting on the rotating machine can be represented as shown in Figure 2.
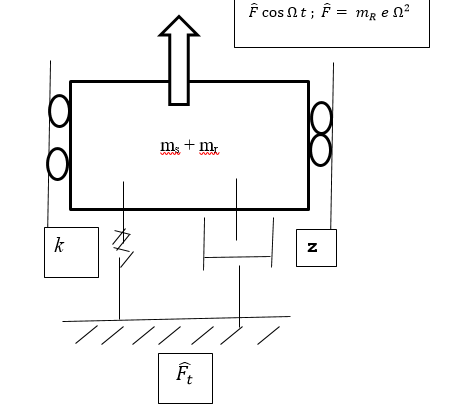
Model analysis gives following
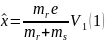
Here, x is the vertical displacement response due to unbalanced forces, V1 is the dimensionless function represented by equation (2), e is the eccentricity of machine, mr is the mass of rotating machine, and ms is the mass of stationary part.
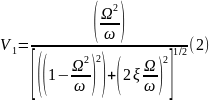
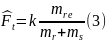
Here, Ft is the reaction force on the foundation. Now based on the analysis of equation 1 and 2, the foundation can be designed by selecting suitable damping ratio (z). Equation 1 shows that to reduce x engineers need to carefully select damping ratio (z) corresponding to the natural frequency (ω) of rotating machine. Next section discusses the foundation design and its implications on vibrations transmission to the surrounding. It should be noted that the discussion in the following section is based on the derived relationship between damping ration, natural frequency and vertical displacement due to vibration of rotating machine as shown in equation 1 and 2.
Discussion
Vibration causes failure of rotating machines due to its high-frequency; this high frequency vibration can even damage structural components and loosen the fasteners associated with the rotating machines. Continuous vibration in rotating machines can induce fatigue in the mechanical component which might go unnoticed and lead to sudden machine failures. Therefore, it is important to isolate vibration from machine using an efficient foundation design. Foundation design requires machine and foundation analysis which helps in identifying the required foundation stiffness to avoid any kind of resonance condition (Pyrhonen et al. 51).
Foundation design also requires determining soil properties of the foundation on which machine foundation is installed. In addition, the vibration induced displacement depends on multiple factors as discussed in section 2. Figure 3 shows the criteria for vibration isolation based on the force transmissibility (Tf) to avoid resonance condition. For a rotating machine transmissibility is defined as,
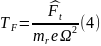
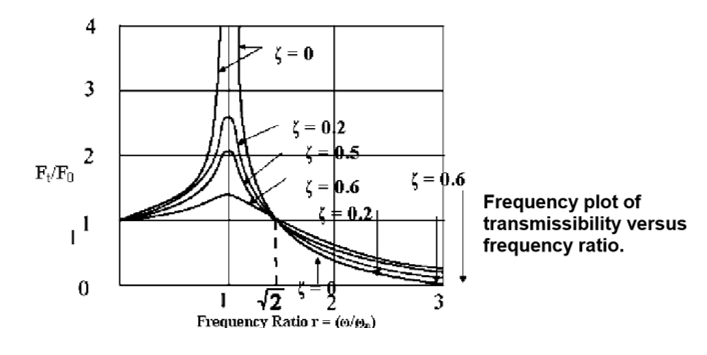
Following guidelines can be deduced from the above curve:
- The transmissibility ratio remains unaffected by the rotation speed for a rotary machine whose frequency ratio =√2. It should be noted that for all the values of frequency ratio less than √2 isolation will increase the vibration i.e. for rotating machine with frequency ration less than √2 rigid mount or rigid foundation works effectively in reducing vibration.
- The mass ratio is not related to the transmissibility force. Inertia mass has no direct impact on vibration.
Figure 3 can be used for isolation of rotating machine. Engineers can design a foundation of rotating machine such that its damping ratio will either be zero, less than 1, equal to one, or greater than one. Based on the resultant damping ration three scenarios of vibration are possible (Karnopp et al. 623, Magalhães et al. 1302):
- Undamped rotating machine have damping ratio equal to zero. It is a situation of no damping.
- An under damped machine has damping ratio ranging from 0 to 1.
- Over damped machines have damping ratio greater than one.
- While critically damped machine has damping ratio equal to 1.
Foundation type and its effect
Engineers use two type of foundation to control vibration of rotating machines namely block type and frame type foundation. Foundation design of dynamic loading requires the total mass of machine, the radius of gyration of the machine, operating speed, the center of rotor from foundation base, the footprint of the machine base, and dynamic forces for consideration. ISO/Machine manufacturers follow a standard of allowed eccentricity which value depends on the speed of the machine and rotating mass. All the rotating machines are balanced based on an ISO standard, known as the balance quality grade.
Machine foundation may be either under-tuned or over-tuned (Bhatia 2, Srinivasulu and Vaidyanathan 17). Under-tuned foundation is defined as the foundation which vertical vibration remains lower than operating machine frequency. On the other hand, over-tuned foundation has vertical vibration greater than operating frequency of the machine. Over-tuned foundations are suitable for low-speed machine, while the under-tuned foundations are suitable for high-speed machines.
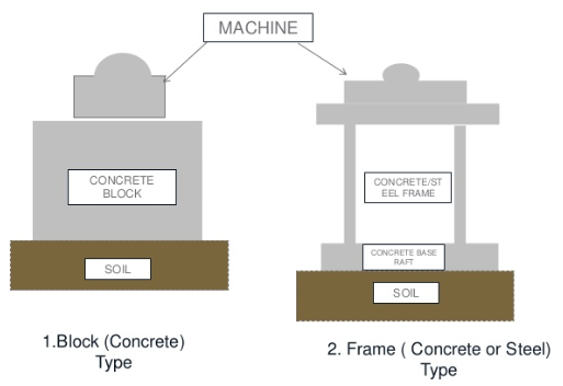
The design of foundation should be such that it does not allow vertical vibration more than acceptable. This acceptable vertical vibration varies based on the speed of rotation of machines. Table 1 lists the permissible vertical vibration based on the speed of rotation.
Table 1 Rotating type machine and its permissible vertical vibration (Fattah et al. 3).
Foundation Mass: A safe foundation design must have mass of 2.5 to 3 times the machine mass. In addition, the foundation must extend 150 mm on all the sides. Following are the characteristic feature of a good machine foundation:
- Foundation should be strong enough to carry the machine load with and without loading conditions.
- The centre of gravity of foundation should be in line with the centre of gravity of machine in vertical plane.
- The natural frequency of the foundation material should be either very small or very large when compared to the natural frequency of rotating machine. This is the most important feature engineers should address when designing the foundation to avoid resonance.
- Even machine foundation cannot eliminate vibration; however, the amplitude of vibration should be in the acceptable zone as per the design of machine.
- All the machine component should be balanced before designing foundation. If a given mass cannot be balanced, special consideration should be given to it.
- To change the natural frequency of foundation which might be very close to the natural frequency of rotating machine, the base areas should be altered.
Machine Foundation failure and challenges
Engineers use diagnostic tool to detect rotor imbalance, defects, and shaft misalignment before designing foundation. Operational defects if unidentified can further complicate the design of foundation for rotating machines. Engineers employ predictive maintenance techniques to regularly monitor vibration and its source.
Engineers periodically check health of foundation of rotating machines using sophisticated monitoring and analysis tools. In this respect, they focus on determining the response of soil foundation with respect to dynamic loading conditions. Soil response is modelled using the concept of stiffness also known as impedance. It is represented by six spring damper arrangement. In this respect, different tools are present to represent impedance of soil. Use of numerical methods and tools require in-depth understanding of soil dynamics (Gazetas 33).
The concrete based foundation is widely used vibration absorbers. It comes as one integral part and the total mass of foundation is calculated based on simple rule of thumb i.e. in case of rotating machine the mass of foundation should be 3 times the mass of machine, while for reciprocating machines, the mass of foundation should be 6 times the mass of machine. Experimental results show that one ton of concrete is enough to dampen 1 Kw of vibrating power.
One of the primary cause of foundation vibration is cold joint. This situation arises when concrete is poured in multiple shifts. Use of epoxy bonding resin is recommended to avoid foundation failure. Further, epoxy grouts are also used as an efficient grouting mechanism to hold the machine to the foundation. Special anchor bolts are also being used to hold the vibrating machines to the foundation. Engineers should ensure almost zero shaft misalignment. Over time bother thermal and mechanical factors lead to foundation failure in rotating machines.
Conclusion
Industry widely uses rotating machines. Therefore, dynamic balancing and vibration control of rotating machine is of paramount importance. Vibration leads to loosening of mechanical component and reduces the efficiency of the machine. In addition, the vibration if transmitted in excess to the ground can affect neighboring machines and related components. In this respect, the design of foundation plays an important role in controlling vibration.
Two kinds of foundations are most commonly used namely the block type foundation and frame type foundation. Manufacturers need to recommend a permissible range of vibration for a proper functioning of all the rotating machine. To control machine vibration, engineers need to consider multiple parameters when designing foundation. Some of the most important parameters that affect and help control vibration are
- amount of eccentricity,
- height of foundation from the centre of rotation,
- natural frequency of machine (the frequency ratio),
- transmissibility.
Research studies have shown that relationship between transmissibility and frequency ratio governs machine vibration. Engineers use this relationship to design foundation and avoid resonance conditions.
Works Cited
Bhatia, Krishna Gopal. “Foundations For Industrial Machines and Earthquake Effects.” ISET Journal of Earthquake Technology, Paper, vol. 495, no. 1, 2008, pp. 1-2.
Derrick, William W., and Robert G. Derrick. “Vibratory Screening Machine with Tiltable Screen Frame and Adjustable Discharge Weir.” U.S. Patent No. 4,882,054, 1989.
Edwards, Simon, Arthur W. Lees, and Michael I. Friswell. “Fault Diagnosis of Rotating Machinery.” Shock and Vibration Digest, vol. 30, no. 1, 1998, pp. 4-13.
Fattah, Mohammed Yousif, Ahmed Dl-Azal Al-Mufty, and Hula Taher Al-Bardi. Design Charts For Machine Foundations.
Gazetas, George. “Analysis of Machine Foundation Vibrations: State of the Art.” International Journal of Soil Dynamics and Earthquake Engineering, vol. 2, no. 1, 1983, pp. 2-42.
Karnopp, Dean, Michael J. Crosby, and Robert A. Harwood. “Vibration Control Using Semi-Active Force Generators.” Journal of engineering for industry, vol. 96, no. 2, 1974, 619-626.
Magalhães, Filipe, et al. “Damping Estimation Using Free Decays and Ambient Vibration Tests.” Mechanical Systems and Signal Processing, vol. 24, no. 5, 2010, pp. 1274-1290.
Nelson, F. C. Vibration Isolation Of Rotating Machines. SPIE Proceedings Series, 2002. Society of Photo-Optical Instrumentation Engineers.
Pyrhonen, Juha, Tapani Jokinen, and Valeria Hrabovcova. Design of Rotating Electrical Machines. John Wiley & Sons, 2009.
Srinivasulu, P., and C. V. Vaidyanathan. Handbook of Machine Foundations. Tata McGraw-Hill Education, 1976.