Overview of Sensor/Transducer Usage in the 3-Axis Computer Numerical Control (CNC) Machine
Working Mechanism
The principle of operation of CNC systems is to issue a control action by the microcontroller – electrical impulses of a strictly defined duration, to the actuators of the machine, as well as control their movement of the feedback type to implement the movement of the cutting tool according to a given program (Suh et al., 2019). Using the CNC, the computer controls the servos that drive the machine (Suh et al., 2019). Thus, constant human attention is not required, although operators still need to start the machines.
Input Devices
The input devices used for this particular system are employed to enter the part program on the machine. There are three types of input devices that are commonly used: a punched tape reader, a magnetic tape reader, and a computer operating through an RS-232-C port (Suh et al., 2019). The machine control unit has multiple roles, including decoding and reading code instructions, generating axis movement commands by interpolating linear, circular, and helical movements, controlling axis mechanisms by transmitting axis movement commands to amplifier circuits, and receiving feedback signals about each drive axis’s position and speed. It also performs additional functions, such as turning the cooler or spindle on or off and changing tools.
The actuator and drive system, along with the sensors and controllers, are connected to the control unit through an amplifier circuit (Suh et al., 2019). The feedback system, also known as the measuring system, consists of transducers or sensors that continually monitor the position and speed of the cutting tool. The control unit obtains signals from these converters and utilizes the difference between the original signals and the feedback signals to produce new signals to correct the position and speed.
Functions of Sensors
Instruments of the measuring system are used to set up the working mechanism, measure the part, and accurately touch or connect to the workpiece. By purpose and principle of operation, CNC machine sensors are divided into non-contact type photo sensors used to track the movement of a part; sensors that determine the angle of rotation; linear; terminal; sensors for determining the position and search for a tool; and altitude sensors (Suh et al., 2019).
The presence of sensors provides automatic clamping of the workpiece, reduces the wear of the working tool, excludes the operator’s presence as much as possible, reduces the percentage of rejects, and increases productivity. The sensor is connected to the spindle and can take the necessary measurements of the workpiece (Suh et al., 2019). In the case of serial production, it ensures that the settings remain unchanged when moving from part to part.
Functional Explanation and Types of the Sensor/Transducer
Functions and Characteristics
The device’s purpose is to determine the height of the cutter, that is, its calibration. The CNC height sensor sets the tool’s working height. The principle of operation is based on the connection of two parts using a program via the Internet. When the contact of one part touches the surface of the edge of the workpiece, the signal is transmitted to the other part to adjust the tool’s working height.
The sensor is compatible with MACH3, LinuxCNC, and GRIZLIcnc systems, well protected from noise, and equipped with a reliable battery with continuous operation for up to 6 months. The calibration accuracy is 0.01 mm, the device is triggered at the moment of touch, and the voltage during calibration is not more than 5 V when the tool height sensor is triggered – 250 V.
Classification
There are several types of height sensors: positioning module NC Studio V5, PLTLS-01, and DT02. The first device sets the height between the tool and the workpiece. It consists of two parts that communicate with each other via Wi-Fi—triggered by pressing a contact pad on one of the parts. The other two are designed to work in automatic mode (Suh et al., 2019). They differ from the first by the required voltage and among themselves by the current indicators.
When the height sensor’s contact pad makes contact with the surface of the workpiece, an electrical signal is produced. During normal operation, this signal is processed to set the cutting tool at the optimal operating height. Height sensors, such as the positioning module NC Studio V5, PLTLS-01, or DT02, might produce somewhat different signals and undergo slightly different processing based on the sensor’s specifics. It is possible that the signals and approaches to signal processing used by each of these sensors will vary. The essential function of all height sensors, however, is to guarantee exact machining by calibrating the operating height of the cutting tool.
Input-Output Relationship of the Sensor/Transducer
An approximate diagram of the input and output signals is shown in Figure 1.
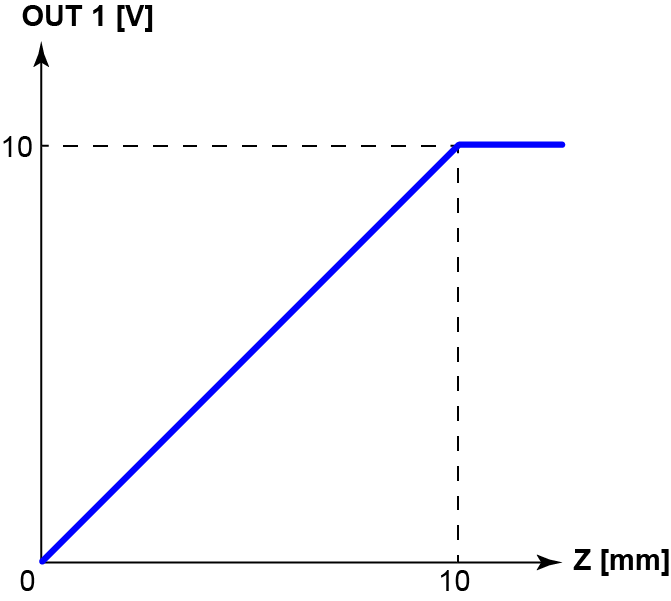
In view of the relative ease of use of this sensor, the equation has a clear form. On the one hand, the specified limit of the length of movement l along the Z axis is indicated; on the other hand, the transition of the output signal to a constant one is indicated. For a complete comprehension of a height sensor’s operation, it is necessary to grasp the connection between its input and output. CNC machines use a height sensor to calibrate the cutting height. The sensor is functional because of the Internet connection between its two components. Adjusting the tool’s operating height is triggered when a contact on one component makes contact with the edge of the workpiece. The sensor’s job is to measure the space between itself and the workpiece to determine the optimal operating height for the tool.
The height sensor takes its input from the CNC machine’s Z-axis, which is responsible for the vertical motion of the cutting tool. The height sensor measures the vertical distance between itself and the working surface as the Z-axis is moved. An output signal is then utilized to fine-tune the cutting tool’s height based on the sensor’s readings. The height sensor sends out a voltage reading that changes in response to the gap between itself and the object being measured. Sensor voltage is weak when it is far from the workpiece. Yet, the voltage signal increases as the sensor approaches the workpiece. An amplifier circuit is often used to process the output signal, amplifying the signal so the cutting tool’s height may be adjusted correspondingly.
It is possible to express the height sensor’s input-output connection mathematically as follows:
,
where x is the distance between the sensor and the object being measured, and OUT(x) is the resultant signal (the voltage signal generated by the sensor). As the Z-axis travel distance l is reached, the equation demonstrates that the output signal stabilizes at a constant value. This implies that once the cutting tool is at the proper height relative to the workpiece, the output signal from the height sensor stabilizes.
In summary, a height sensor cannot function without the input-output connection. The Z-axis movement of the CNC machine serves as the input signal, and the voltage signal proportional to the distance between the sensor and the workpiece serves as the output signal. The above equation represents the input-output connection between the sensor and the amplifier circuit that normally changes the cutting tool’s height based on the signal.
Justification of Sensor/Transducer Characteristics from Manufacturer’s Data Sheet
This CNC Plus Tool Length Sensor or Tool Offset Setting Sensor has many essential features for CNC use. First, it is used with tools from 0.2 to 20 mm, a range of commonly used processors in milling machines (CNC Plus, 2023). Secondly, it provides an accuracy of 0.02 mm, which meets the quality standards for developing device parts indicated in the first part (CNC Plus, 2023). Finally, the PA6 aluminum body material is fully anodized, eliminating the risk of magnetization or excessive electrification when processing parts (CNC Plus, 2023). A 3.5 mm jack is standard, and a cable length of 2.4 meters allows streamlining the switching of the entire system, taking into account safety and convenience for the technician and operator.
The CNC Plus Tool Length Sensor has a combination of static and dynamic features that make it a reliable and versatile tool for CNC use. The tool range (0.2 to 20 mm) and the material of the body (PA6 aluminum fully anodized) are static characteristics because they do not change with time or usage. These features are inherent to the design of the tool and remain constant regardless of how the tool is used. On the other hand, accuracy (0.02 mm) and cable length (2.4 meters) are dynamic characteristics because they can change with time and usage. For example, the accuracy of the sensor might change due to wear and tear, while the cable length might need to be adjusted based on the specific needs of the user.
Application of the Sensor/Transducer in Other Engineering Systems
There are two types of altitude sensors in drones: based on the dependence of atmospheric pressure on altitude and based on measuring the delay of an ultrasonic or radio signal reflected from the surface. The barometric one has a significant error because the pressure near the earth is somewhat uncertain (Santamaria-Navarro et al., 2022). Built on the reflection principle, it works at low altitudes and depends on the surface’s reflectivity.
Wind turbines use many sensors connected in a single network and demonstrate the effectiveness of the Industrial Internet of Things. True, the network, as a rule, is built based on Ethernet and not based on wireless interfaces. They perform the following functions: control of various parameters and transmission of information to the control center; vibration level control to provide protection against emergencies; and monitoring of temperature, pressure, and mechanical stresses.
Various displacement sensors are used to monitor the structural integrity of a wind turbine. The foundation on which the windmill is located consists of a considerable amount of concrete. At the same time, the overall height of the structure turns out to be very large, and the gondola and blades have a significant weight, which is concentrated mainly in the upper part of the windmill (Li et al., 2020). Therefore, control of the integrity of the entire structure is mandatory.
Laser sensors can be used to solve this problem. As a rule, height sensors are indicators of structural integrity control built into piles. They can detect minimal mutual displacements of the foundation and the tower caused by constant wind or wave pressure, as well as the resulting structural defects.
References
CNC Plus. (2023). CNC tool length sensor, tool offset setting sensor. Web.
Li, M., Kefal, A., Oterkus, E., & Oterkus, S. (2020). Structural health monitoring of an offshore wind turbine tower using iFEM methodology. Ocean Engineering, 204, 107291. Web.
Santamaria-Navarro, A., Thakker, R., Fan, D. D., Morrell, B., & Agha-Mohammadi, A. A. (2022). Towards resilient autonomous navigation of drones. In Robotics Research: The 19th International Symposium ISRR (pp. 922-937). Springer International Publishing.
Suh, S. H., Kang, S. K., Chung, D. H., & Stroud, I. (2019). Theory and design of CNC systems. Springer Science & Business Media.