Ship Unloader
Proficient, dependable operation
The ship unloader is regarded as a future-oriented investment. Portalino and Portalink from Buhler AG are uninterrupted mechanical ship unloaders developed for dependable and enhanced operational efficiency for unloading of oilseeds, grain, and derivatives (Bühler AG 2-6). Based on the specific qualities of the bulk material, the ship unloader can operate at a maximum throughput rate of about 1400 t/h.
Portalino and Portalink have been noted for their adaptability and uptime, in addition to the cost-to-benefit ratio.
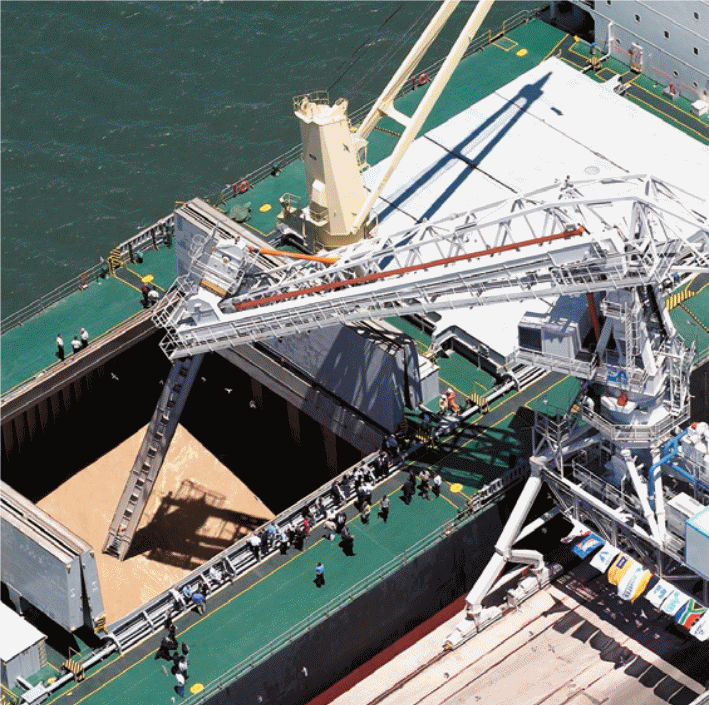
Portalino and Portalink: Design and Usage
These two devices can either be movable or stationary. They are diesel powered or may rely on an electric motor to drive them. In most cases, they can be found in ships with deadweight tons of between 3,000 and 120,000. The designs have been customized to run on rail tracks. Alternatively, rubber tire wheels have been developed to allow for steering.
The delivered bulk materials are moved to the lower section into the conveying systems. In some cases, the materials may be directly transported into rail vehicles or road vehicles.
Some advantages of the ship unloaders include the following. They have low operating costs and are efficient to unload. The unloaders are preferred for their very high uptime, operating dependability, ease of service, maintenance, longer service period, and smooth operations.
Designed to enhance customer value
Efficiency in unloading
These systems have an automatic sink-in device found in the HL-SKT as a component of the marine leg (known as the vertical chain elevator) to ensure the best position when the unloader starts operations and, therefore, automatic unloading can be achieved to the optimal. This unit can do several movements, including ship unloader movement; lifting, lowering, and rotating the boom; and kicking in and out of the marine leg. The system was designed to perform such movements for flexibility within the hold of the ship. Consequently, the unloader can achieve higher unloading throughput frequencies and lessen the berthing period.
Increased uptime and reliability
The unloaders are known for their reliability during operations even with materials with diverse characteristics. They are resistant to foreign materials, provide quick chain link movements, ease of operation, and run on well-established technology.
Low costs of operating
The systems have low conveyor chain speeds, which are also associated with low energy usages, wear, reduced spare parts needs while providing longer service periods, specifically for the conveyor chains.
Well established technology
Operating standard and major components
The vertical chain conveyor, which is the intake boot of the leg, is positioned in the bulk material for unloading. It also has a specifically made endless conveyor chain that lifts the material and creates a compact area for the material within the conveying unit. It moves throughout with a specific speed to the unit outlet. From here, the system is fitted with other chain conveyors leading to the truck loading section or a pier conveyor may be used.
The ship unloader is mounted with a framework on which the rotating top part with trussed boom and kick-in/kick out systems are found. The cylinder with the kick systems is joined with the boom, and it pushes the HL-SKT marine leg to a slanting position of nearly 300 in either direction. The boom movement occurs within the cylinder using hydraulic controlled systems. The rotating movements are also performed using the hydraulic system that draws its power from the swiveling gear.
All movements within the system are protected using the overload valves. It also has built-in comparative control valves to provide smooth and sustained variable motions. Besides, the control unit is fitted with PLC components while the display unit shows all information relating to operating statuses, errors, and preventative maintenance programs.
The gentle movement of the bulk material
A solid component of the bulk material within the casing of the marine leg is put in motion at equal low speed to ensure that smooth conveying action can be attained. Moreover, the system can achieve reduced energy consumption and wear.
Meeting all conditions
Unfastening screws
Sluggish materials are often handled on the ship. In these instances, these materials or products such as biomass, fishmeal, animal feeds, or soy are tightened during shipping. Therefore, the unloader may have optional loosening screws for such sluggish materials. The materials are unfastened near the intake boot and maximize inflow toward the chain conveyor. These procedures improve the throughput rates and reduce operational complexity during unloading.
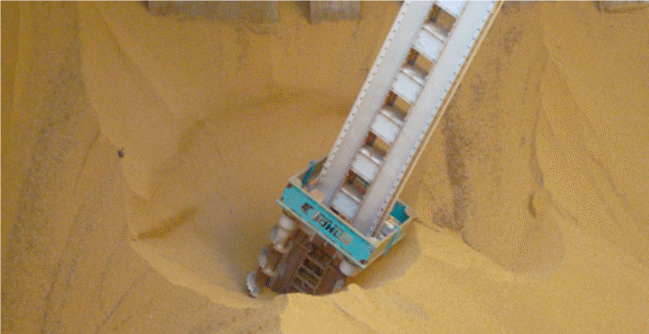
Clean-up screws
The clean-up is performed to remove the remaining materials inside the ship. During this process, the ship is held at the unloading cycle while its unloader cannot attain full throughput capacity. The clean-up process, therefore, requires efficiency to attain reduced unloading time.
The Buhler clean-up screw is designed to send the bulk material to the marine leg and remove the ship’s hold. Consequently, the clean-up screw reduces unloading time and simplifies clean-up processes.
Enhanced unloading with a software application
To enhance unloading efficiency, a software application has been introduced to display the maximum unloading processes. Currently available terminals may use a software application to enhance unloading rates by identifying the best possible hold for unloading successions, considering the ship inclination and the current unloading system. Optimal processes result in enhanced traveling distance while the throughput capacities are attained completely. By considering new terminals, it is necessary to demonstrate the effect of various system layouts and specific machine and their respective volumes of materials handled. In this regard, terminals can be customized to meet the required needs.
Portable
The portable clearing shovel allows the system to create a space for clean-up front-end loaders while the same tools inside the ship’s hold. The hydraulic system is responsible for shifting the shovel to ensure that it is positioned in the clean-up position. Consequently, the user may remove materials from the bottom of the ship’s hold and bring the front-end loader closer to the bottom into the hold.
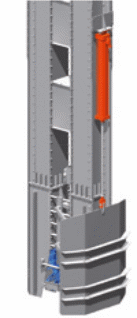
Bucket Elevator
Belt-and-Bucket Elevator MGEL
Use
The belt-and-bucket elevator is used for vertical conveying of dry, floury, and mealy fine and course materials. The materials can have a temperature of up to 70°C (Bühler AG 2-3).
Design
The system design is straightforward with a dust-tight encasing to ensure a high level of cleanliness. Besides, it is designed to ensure ease of maintenance, reduce energy consumption, and ensure that it meets the coating meets the FDA standards required for all food-grade materials. Stainless steel type may be used, but this is normally optional.
Safe operation and explosion control
For safety control, the system is fitted with off-track and zero-speed features, backstop, and operator safety features that meet the European Union, CSA, and UL safety standards. Optional antistatic; fireproof plastic buckets; pressure relief; and round, shock-pressure-resistant casings may also be installed in the bucket elevator.
There are also other additional components of the bucket elevator, including the belt installation device, inlet and outlet ports with a dead box for lessening wear, and aspiration connection.
The system surface is also expected to meet the standards for handling food. Hence, it has a food-grade paint coat, specifically white NCS 1000. The bucket elevator also consists of several layers, which are anti-corrosion suitable for outdoor usages. An optional coat of customized paint may be applied.
Elevator head
The elevator head consists of a material deflection plate made of strong durable steel materials to resist wear. It also bears deflection tongues with abrasion-resistant rubber, a split hood for ease of installation and maintenance, and a backstop.
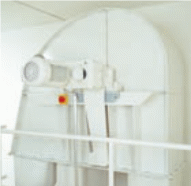
Off-track detector
The off-track detector is installed in the system to detect any issues during operations, monitor the system for operational safety, and control potential explosion. Also, the off-track detector is useful for preventing damages to any parts of the bucket elevator.
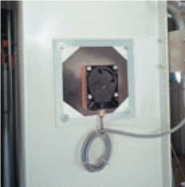
Elevator boot
This component consists of a material inlet made of wear-resistant steel. It is simple to operate, ensures accurate belt positioning and tension by controlling the screw engagement. Finally, it is also made of a large cleanout to allow for maximum sanitation.
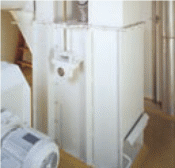
Efficient design for optimal throughput
Some major design components of the bucket elevator that enhance operational efficiency and increased volumes of materials handled include the following.
Drive
The drive is a direct-coupled Gearmotor that can be attached to either side of the system. It is easy to install and maintain. The power consumption is rated at 22 kW while higher output may be supplied with an electric soft start gadget. An optional drive with a frequency converter may be installed for maintenance purposes.
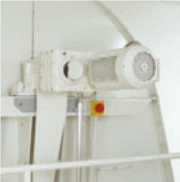
Tensioning part
This part of the elevator is designed to be opened from any side of the system. It allows for easy installation of belts and buckets while providing a location for inspection and monitoring of operations. The tension area is designed to be safe, clean, and reliable.
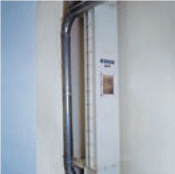
Belts and buckets
Appropriate belting and an adequate number of buckets are required for any materials and enhanced throughput. Standard buckets made of steel are necessary for a wide range of bulk materials and ease of replacement. Besides, only food-grade, antistatic, non-combustible rubber is used while buckets of antistatic, non-combustible plastic may be used as an alternative.
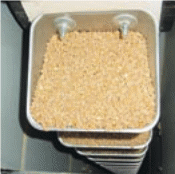
Speed monitor
The monitor is useful for detecting operating issues, ensure the safety of operations, and control potential explosions.
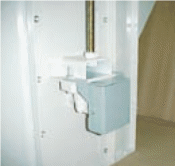
Works Cited
Bühler AG. Belt-and-Bucket Elevator. n.d. Web.
—. Mechanical Ship Unloaders from Buhler. n.d. Web.