Introduction
Reverse logistics encompasses planning, implementing, and controlling efficient flow of raw materials from their stage of consumption to the point of origin with the intentions of regaining value or ensuring appropriate disposal (Pokharel and Mutha 179). The raw materials might take the form of inventory or finished goods. Reverse logistics entails all management processes that occur after the sale of the product. Singapore is a leader in the logistics and supply chain management. The country was ranked first in Asia by a World Bank study on logistics conducted in 2014. The Singaporean logistic companies offer varying services through sophisticated processes like vendor managed inventory and reverse logistics (“International Enterprise Singapore” 9). This paper will focus on the reverse logistics in Singapore.
Current trends overview of recent reverse logistics in Singapore
Reverse logistics is a relatively new field in the management of supply chain in Singapore. The business is growing in the Asia-pacific region and Singapore is thus a major hub of reverse logistics in Asia. The chart below illustrates the current trends of reverse logistics are depicted below.
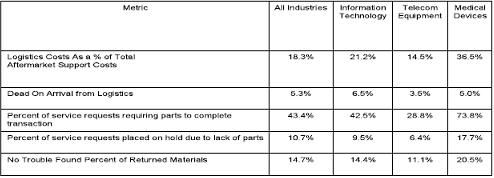
Additional statistics indicates that the supply-chain market progress is estimated at 15% in Asia, 10% in North America, and 7% in Europe. Further, Asian shipping companies have outsourced a mere 2.5% of their logistical function in comparison to at least 25% recorded by their European and the US counterparts.
A typical product lifecycle
All the goods and services provided by any organization have a lifecycle. The cycle refers to the duration between the initial conceptualization of the product and the period when the product is removed from the market. The product lifecycle is characterized by four distinct sequential stages, which include “introduction, growth, maturity, and decline” (“International Enterprise Singapore” 6).
During the introduction, the product is injected into the market through initial launching. The company creates awareness about the new product to the potential consumers through investing in advertisement and promotion activities. At this stage, the sales and competition are low due to the small market size. The company spends huge amounts of money on the product due to expenses associated with research and development, marketing, and consumer testing.
The second stage is the growth stage that follows after the product has been noticed in the market. Sales increase due to the more shares in the market, thus taking advantage of economies of scale. Competition at this stage keeps on rising as the awareness of the product increases. The objective of many companies is to stagnate at this phase for the longest time possible (“International Enterprise Singapore” 22).
The third phase is the product maturity. Sales grow at declining rates and finally reach an optimal level where they finally stabilize. The goal of the company at this stage is to retain the existing market share. Competition at this stage is fierce due to alternative solutions initiated by the competitors. This phase is the longest, and the product can stay in the maturity stage for several decades (Pokharel and Mutha 181).
The final stage is the decline stage, which comes after the sales slide downwards from their previous optimal state in the maturity stage. The shrinkage of the sales is evidenced by market saturation or switching of customer preferences to other alternative products. The item is phased out of the market, as it is no longer in demand.
What are the 4Rs?
The 4Rs are aspects that must be adhered to when meeting the aftermarket service requirements of various manufacturers. The 4Rs provide companies with a variety of options that aid them to handle a variety of returned products appropriately regardless of their working conditions or physical appearance (“SIMS Recycling Solution” par. 1). The 4Rs underscore return management, refurbishment, remarketing, and recycling.
Refurbishment refers to the act of distributing items that have been returned to the sellers or manufacturers for various reasons. Refurbished products must be tested to ensure proper functioning and eliminate any defects before resale. Recycling means the removal of materials from a disposed product or a package for subsequent utilization in the development of a new product (Pokharel and Mutha 182).
Return management is a dominant process in the supply chain that keeps in check tasks affiliated to product returns such as gatekeeping, avoidance, and reverse logistics. The fourth R denotes remarketing, which entails the action undertaken by a company by reintroducing a given product or service as a way to respond to declining sales.
Why 4Rs?
Recycling is done to provide secure asset management services to the initial electronic equipment manufacturers. The systematic approach to managing end life of electronic products ensures overall accountability by the business, thus encouraging environmental responsibility and data security. Returns management enables the manufacturer to spot opportunities that reduce unnecessary product returns coupled with controlling the reusable assets. Additionally, return management aids in effective control of the reverse product flow.
Remarketing is essential as it rejuvenates the customers’ interest in the electronic and medical products that they had foregone previously thereby translating into improved sales and profitability. Remarketing also enables the manufacturer to rectify the product’s defects. Product refurbishment has some associated advantages as it ensures that the workability of damaged equipment is restored, thus allowing products to look better after they have been serviced. Medical equipment can also benefit from the refurbishment aspect of the 4Rs thereby cutting costs for the purchase of new equipment.
Some the disadvantages of the 4Rs are the challenge emanating from how to bring back an open delivery of products after they have been returned to the manufacturers by the consumers. Another challenge is how to pack expensive and fragile products while making sure that they remain intact as one piece.
Case studies
Apple’s defective iPods were delivered back to the service centers for refurbishment through express parcel service. The company also undertakes Apple recycle program, which is committed to reducing adverse environmental impacts by prolonging the useful life of the electronics in the secondary market. Often recycled Apple products include any PC Desktops and Notebooks that qualify for reuse.
The HP Company is involved in offering refurbished solutions in all its product lines including printers, desktops, notebooks, and others. The refurbished products emanate from customer returns, overstocks, or damaged products. HP operates take-back programs in more than 73 countries that aim at ensuring hardware recycling by collecting used HP products to ensure responsible disposal. Some of the products that are recycled by HP include the ink and LaserJet Cartridges.
Samsung is also a good example to demonstrate the 4Rs. The company operates Samsung recycling direct program, which is obligated to provide smart ways for ensuring environmental cleanliness. The program converts empty cartridges to usable components like plastics, metals, and cardboards. Samsung also operates a rigorous refurbishment process products returned due to various reasons. Refurbished products are tested, inspected, and repackaged before being released for resale.
Companies managing 4Rs
Various companies around the globe have focused on dealing with products that have been returned to manufacturers by consumers due to various reasons. TES-AMM provides management solutions to synchronized electronic scrape often called e-waste for various leading organizations around the globe. The company helps organizations to regain proceeds from contingent assets, which results from disposals, surplus, obsolescence, and service returns manufacturing rejects among others.
Another company that is involved in the management of the 4Rs is the Semcorp Company. The company provides commercial, industrial, and residential standardized building services. The company is associated with the development of new works and making renovations and alteration on products among any other activities related to the building. Product repair and alteration entail aspects of refurbishment, recycling, remarketing, and return management, thus making the company become affiliated with the management of the 4Rs.
Moving forward and Recommendations
The ultimate objective of reverse logistics is to ensure that any given organization achieves efficient aftermarket activities to pave the way for saving money and other essential environmental resources. In Singapore, manufactures in both the medical and electronic industry should follow the following recommendations regarding reverse logistics.
Business process outsourcing (BPO) is an essential element in solving aftermarket logistical challenges for organizations (Blumberg par. 12). This benefit will help businesses acquire the best and quality consumer complaint processes as opposed to a centralized system that suffers systematic incapability. Third party service provider enabled by business process outsourcing will offer new services to customers coupled with offering expertise on regulatory compliance and quality systems (Blumberg par. 13). Thus, BPO facilitates Medical Device Manufacturer with modern system functionality of high standard and streamlined complaint processes. Moreover, BPO enhances the practicality of resolving Aftersales Logistical Support problems.
Therefore, to ensure effective reverse logistics in Singapore, companies involved in manufacturing can collaborate with each other. Due to the new trends originating from the supply chain, competing manufacturers should work together with the aim of providing new products and services (Sogbanmu par. 4). The union between manufacturers will result in a low cost of shipping products, thus making it convenient to provide the service to end-users.
Additionally, cross-border enablement will ensure that logistic companies improve service delivery to consumers. Complexities emanating from shipping and returning of products will be eradicated by transnational enablement thereby ensuring that proper compliance and returns are attained (Sogbanmu par. 9).
Other forms of Saving the Earth with electronics
Some electronics have no reusable value, and thus they cannot be recycled. In such situations, the waste from those electrical devices should be disposed of properly by using the stipulated methods. Buyers should also consider purchasing reusable devices to reduce potential environmental dangers that emanate from inappropriate disposal of used electrical devices.
Waste Electronic and Electrical Equipment
Recycling of waste electronic electrical equipment is one of the specialist product and recycling sectors. WEEE entails a complex combination of materials that contain hazardous ingredients and it can result in harmful environmental and health consequences if not properly managed. Therefore, it is important to emphasize adequate management of WEEE so that manufacturers can attain resource efficiency through enhanced treatment, collection, and recycling of both electronic and medical equipment. Some of the fastest growing WEEE includes computers, fridges, and cellphones. Consequently, legislations to deal with this menace have been established with the examples of the directive on waste electrical and electronic directive in the UK enacted in the year 2006.
Conclusion
Reverse logistics is an important aspect of every organization. Product life entails the life initiation, growth, maturity, and the decline stages. The 4Rs involved in reverse logistics are the remarketing, refurbishment, recycling, and return management. Some of the future recommendations in reverse logistics include business product outsourcing, collaboration among manufacturers, and cross-border enablement.
Works Cited
Blumberg, Michael. Meeting the Aftermarket Service Requirements of Medical Device Manufacturers 2015. Web.
International Enterprise Singapore: Report of the Working Group on Logistics 2002. Web.
Pokharel, Shaligram, and Akshay Mutha. “Perspectives in reverse logistics: a review.” Resources, Conservation, and Recycling 53.4 (2009): 175-182. Print.
SIMS Recycling Solutions: Electronics 2015. Web.
Sogbanmu, Eva. Five supply chain innovations driving the future of fulfillment 2015. Web.