Overview of the Lime-Based Spray Dryer Absorber
It is used when water consumption and sludge disposal restrictions are present. Spray dryer absorber (SDA) technology is observed to remove as much as 95% SO2 from high sulfur coals, which is a characteristic reduction outcome for western low-sulfur coals. It is a requirement that the SDA be upstream of a particulate control device so that the sorbent can be removed from the flue gas.
Activities in the spray drier include slow evaporation of water droplets holding lime, in a large vessel. This happens as the flue temperature rises towards that of adiabatic saturation. The design gas residence time in a spray dryer absorber is about a sixth of a minute, to provide enough time for evaporation and reaction with SO2. To allow for this, the spray drier absorber vessel would be close to 40 feet diameter and 65 feet high for both boilers (EPA, 2000).
The mixture of ash from electrostatic precipitators (ESP) and lime that does not react are in turn recycled to provide efficient reagent utilization. This leads to more solids loading to the ESP by a factor of 3. It in turn demands increased ESP capacity and a total reconstruction of the ash handling system. SDA’s are easy to install in new facilities burning western coal, their installation in existing boilers is known to be quite challenging. The alternative is the installation of a stand-alone SDA, outside the existing building. This would require a new structure, a post-SDA baghouse control, added ducting, a new stack and the control equipment (EPA, 2000).
New units should be installed with a baghouse rather than an ESP since reagent utilization is likely to be better on units installed with a baghouse compared to retrofit units installed with modifications to an ESP. A baghouse can achieve 15% to 20% SO2 capture lessening the burden on the dry FGD (EPA, 2000).
Operation of the Spray Driers
Lime is a key ingredient in the removal of acidic gases, including sulfur dioxide and hydrogen chloride, from flue gases. Dry scrubbing requires the lime to be injected directly into flue gas, but in spray driers, the lime slurry is atomized and injected into a separate vessel. The spray drier has a cylindrical top and cone bottom, and resembles the shape of a silo. An atomizer is used to spray the lime slurry into the cylinder near the top, as the hot flue gas flow above. The lime slurry absorbs the sulfur dioxide, while water in the slurry is vaporized by the hot gas. Scrubbed flue gas flows from the bottom of the cylindrical section via a horizontal duct, as it flows to a particulate control device, to get rid of the remaining lime and reaction products. Some of the dried, unreacted lime and the reaction products are removed as they fall to the bottom of the cone (IEA, 2001).
The spray driers introduce an aqueous sorbent slurry similar to a wet system. The only difference to that of the wet system is that it has a higher concentration of sorbent. The hot flue gas mixes with the slurry solution, causing the water from the slurry to vaporize. Any water remaining in the solid sorbent improves the reaction with SO2. The product of this process is a dry waste that is collected using a standard particulate matter (PM) collection device, which could be either an ESP or a baghouse.
The waste product is then disposed, sold as a by-product or recycled in the slurry. The sorbent used in spray driers can be based on either calcium or sodium reagents. Lime is more commonly used when compared to limestone since it is more reactive and much cheaper than sodium-based reagents. Compared to the wet scrubber systems, the spray driers have a finer droplet spray that is created when the reagent slurry is injected through rotary atomizers or dual-fluid nozzles (IEA, 2001).
The performance of a lime spray dry scrubber is sensitive to operating conditions. In order to maximize the removal of SO2, the temperature has to be kept close to that of adiabatic saturation. The limitation on flue gas moisture requires the utilization of lower L/G ratios, such as 1:3. Performance of the scrubber is lowered by high temperatures or SO2 concentrations of the flue gas. When compared to wet systems, the lower reactivity and L/G ratios cause SO2 control efficiencies of spray dry scrubbers to be lower by about 80 – 90%. This implies that the application of a single spray dry absorber is limited to combustion units less than 200 MW (2,000 MMBtu/hr) (IEA, 2001).
Combustion units that are larger require multiple absorber systems. The capital and operating cost for spray dry scrubbers are lower than for wet scrubbing. This is because no equipment is necessary to handle wet waste products. Another reason is that carbon steel can be used to manufacture the absorber since the flue as is less humid. Characteristic uses include industrial boilers, electric utility units that burn low to medium sulfur coal and municipal waste incinerators that demand an SO2 control efficiency of 80% (IEA, 2001).
Characteristics of Emission Stream
The combustion unit size for spray scrubbers to be used ha to be more than 300 MW or 3,000 MMBtu/hr (EPA, 2000). The temperature of flue gas leaving the absorber for spray dry systems should be in the range of 20° to 30° F more than the adiabatic saturation temperature. A reduction of the same magnitude should also be attained before emission of the stream in order to avoid wet solids deposition on downstream equipment and plugging of the baghouse. This process is made possible by using a heat exchanger, an evaporative cooler or a heat recovery boiler (EPA, 2000).
Efficiency and Reliability of the Process
The most significant component in the SDA system is the GEA Niro rotary atomizer. It atomizes a mixture of lime and recycles slurry into a fine spray. The spray droplets are uniformly dispersed and blended with the hot, untreated flue gas. SO2, SO3, HCl and HF are removed from the flue gas through a series of chemical reactions. During the reactions, water is also evaporated. One atomizer, centrally placed, enhances even dispersion of the fine spray all over the chamber. In addition to this, it reduces the chances for wall wetting and deposition. The alkaline slurry becomes a dry free-flowing powder of calcium and sulfur compounds. Flyash from the boiler and the dry reaction products are collected downstream of the spray chamber (Babcock & Wilcox, 2009).
The primary reagent feed to the atomizer is formed from the mixture of low quality waste water to some of the solids assembled downstream of the absorber. These solids contain un-reacted lime and alkaline minerals from the flyash. To maintain the appropriate level of alkalinity in the feed slurry, fresh lime slurry is added directly to the atomizer feed. This helps to attain the required level of SO2 removal. The correct outlet temperature is maintained by controlling the total amount of slurry fed to the atomizer. The solids recycle process reduces the consumption of fresh reagent and maintains a favourable drying performance in the spray chamber. The cooled and treated flue gas exits the SDA before being directed to a particulate collector or fabric filter. This collector is designed and operated as an integral part of the acid gas removal process, as the solids continue to react with, SO3, HCl and HF in the humidified flue gas (Babcock & Wilcox, 2009).
Disposal of Waste Products
The waste products of the flue gas desulfurization processes contain CaSO3, CaSO4, CaCO3, unreacted calcium hydroxide, and fly ash. While these materials can be disposed in landfills, there is potential usage in soil conditioning for agricultural processes as well as for the preparation of bricks or light weight aggregates. The combination of dry FGD/baghouse after the fly ash particulate collector is necessary for ash collection where a market for the ash exists. The landfill disposal cost for the non-fly ash portion of FGD by-product is about $ 12 per dry ton (IEA, 2001).
Features of the Spray Drier Absorber
They have reliable rotary atomization with the highest slurry atomizer capacity in the industry, which is beneficial in that it reduces the number of atomizers to maintain. Its components are also resistant to abrasive action and corrosion, which makes their maintenance operations minimal (Babcock & Wilcox, 2009).
The spray drier absorber has an efficient flue gas dispersion system that does not require a damper or vane adjustments to follow the boiler head. This is advantageous in that it optimizes the mixing of flue gas and reagent while maximizing the atomizer-to-wall spacing (Babcock & Wilcox, 2009).
They have optimized performance observed in high solids reagent recycle, modern process control, large SDA chambers and control of drying conditions to lower the occurrence of deposition and corrosion (Babcock & Wilcox, 2009).
Benefits of the Spray Drier Absorber
The SDA has numerous advantages including high SO2 removal efficiency, integral SO3, HCl, HF, PM2.5 and heavy metals emissions reduction, low capital cost, low auxiliary power use, high system availability, low operation and maintenance costs, low fresh water consumption, inherent oxidized mercury emissions reduction, and integral consumption of plant waste water streams for zero liquid discharge (Babcock & Wilcox, 2009).
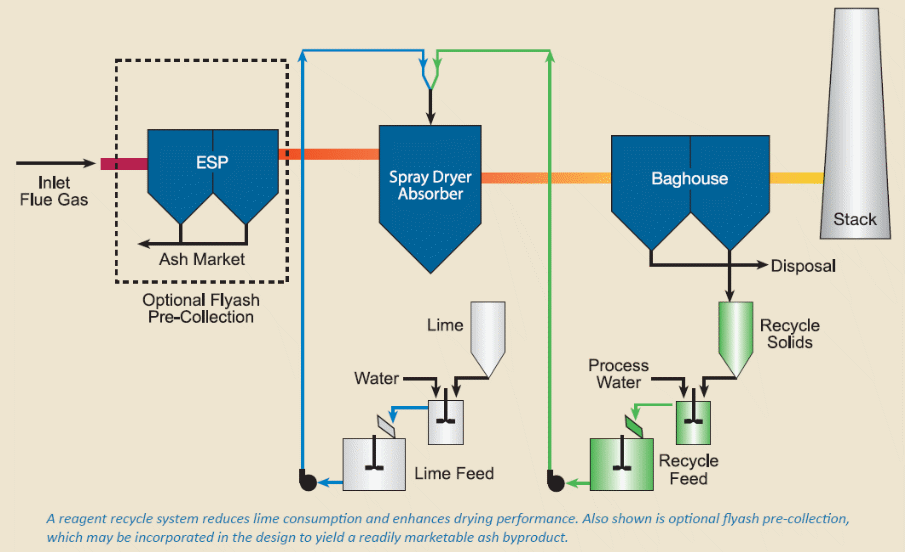
References
Babcock, & Wilcox. (2009). Spray Dry Flue Gas Desulfurization Systems. Barberton, Ohio: Babcock & Wilcox Power Generati on Group, Inc.
EPA. (2000). Controlling SO2 Emissions: A Review of Technologies. Washington, D.C.: US Environmental Protection Agency, Office of Research and Development.
IEA. (2001). Coal Research, Sorbent Injection Systems for SO2 Control. Clean Coal Technologies.