The development of electronic warfare systems is becoming the most effective, rapidly realizable, cost-effective, and sometimes the only possible means to neutralize the technical superiority of the opposing side in the information and technological spheres. The main increase in combat capabilities in the near future will be possible through the use of intelligent troop and weapon control systems (U. S. Army War College, 2019). First of all, such means of warfare include electronic warfare equipment, which is a complex object characterized by high science intensity. Modern means, complexes, and systems of radio-electronic warfare at the present stage of development are in a state of intensive improvement (U. S. Army War College, 2019). In the long-term prospect, the volume of tasks assigned to means of electronic warfare will not decrease but even will increase at the expense of quantitative increase of objects of influence. Equipping the armament with electronic warfare facilities and complexes can multiply their combat potential and reduce the possible losses.
The introduction of a new technological base requires high performance and commitment on the part of the employees. However, despite military training and strict adherence to job descriptions, civilian personnel are also involved in the brigade’s tasks. In this regard, the need to optimize workforce activities arises. In Figure 1, the main types of electronic warfare are shown, which explains the high professional requirements for the operators of this equipment (“Types of electronic warfare,” n.d.). Moreover, maintaining the stable operation of this equipment should be respected, and the necessary performance appraisal measures are to be promoted.
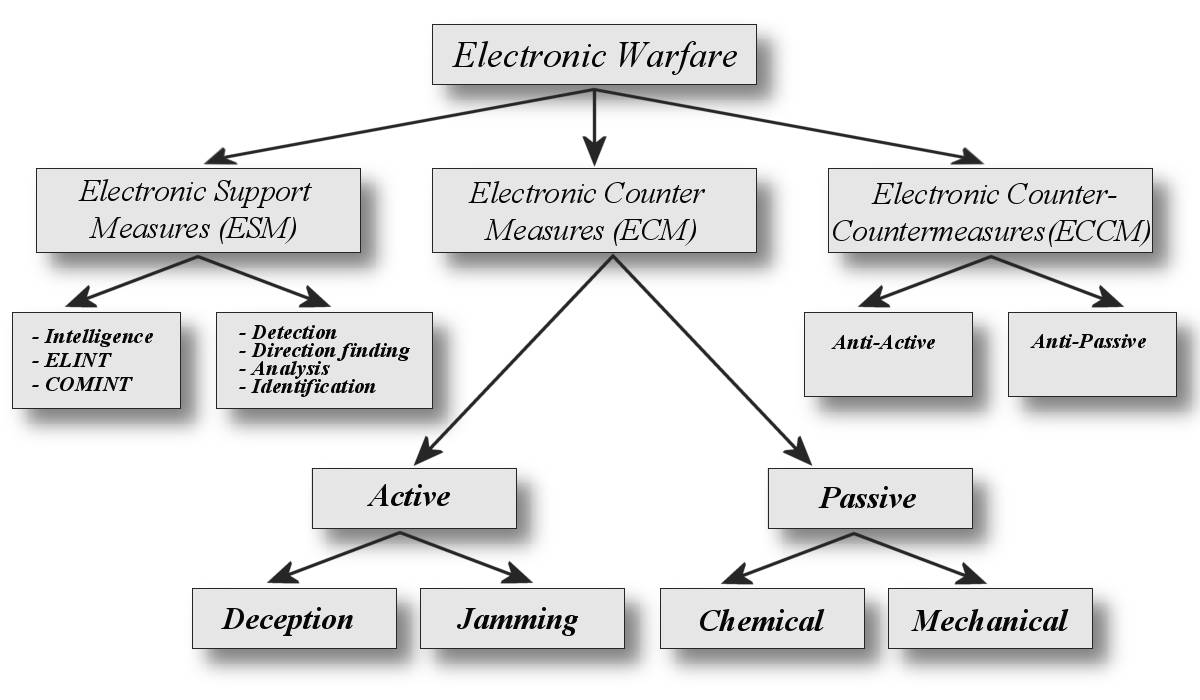
Establishing a program to engage with the staff and develop a sustainable performance management strategy is the goal of the intervention. As a theoretical core, the Six Sigma concept will be utilized, and the Lean Management model will be reviewed as a valuable methodology. Optimizing the work of the specialists of the 106th brigade will allow addressing productivity issues at different levels and create an environment for the implementation of innovations.
Overview of the Subject Company
The subject of the analysis is the 106th Brigade of the U.S. Army, which is a unit of the Signal Command. The brigade’s primary activity is to secure the Army’s networks, but there are also other tasks that fall under the description of EOD (“106th Signal Brigade – JBSA, TX,” 2021). Thus, the brigade’s main problem is the sheer number of tasks that need to be performed and managed, which puts a great strain on Soldiers and civilian personnel (“106th Signal Brigade – JBSA, TX,” 2021). This is necessary to optimize the operations and management of the brigade so that the work becomes easier for each individual but remains at the same level of efficiency. Since the activity of the team is closely related to information, technology, and engineering, improvements and innovations in this area should be considered (Poisel, 2019). In addition, this is also essential to consider the human factor because employees are the main labor force. As mentioned earlier, workers are divided into two main groups – military and civilian (“106th Signal Brigade – JBSA, TX,” 2021). Accordingly, for each group, this is crucial to develop a special approach that corresponds to the specifics of their activities. In view of the above, optimization will take place in three areas: technical, military, and civilian, which will contribute to covering the entire operating spectrum.
Assessment of the HRD Opportunity
The information specificity of the brigade’s activities implies using technical equipment, databases, and specialists responsible for each process. The fact is that the tasks in the field of information security of the brigade are security and encryption, storage, decryption of transmitted data, intelligence, jamming of external sources of information, mobility, and flexibility of databases. As additional factors, one also needs to mention the U.S. territory signal monitoring, control of weapons control complexes, radio-electronic protection of facilities, and the development of new areas and ranges (Poisel, 2019). Each task requires a large number of processes and, consequently, specialists to control the activity. The information issues are caused by the fact that the technical characteristics of the existing system of radio-electronic reconnaissance often do not allow organizing the information support of systems and means of radio-electronic reconnaissance on a proper level (Poisel, 2019). First of all, this concerns the reliability of the objects of influence definition and assigning appropriate service priorities to function in a difficult, dynamically changing radio-electronic environment.
One of the possible ways of solving this problem is the improvement of databases and technical equipment. The merging of some tasks into single ones is another option to take into account. The key problem is technical limitations in memory capacity, which can be addressed through the introduction of new systems of information collection and storage (Poisel, 2019). Thus, the development of the electronic warfare technology is largely determined by two interrelated scientific and technological directions of the development of modern radio-electronic element base. One of them is creating high-speed processors and computing systems while taking into account the latest achievements in microelectronics (Poisel, 2019). The other one is expanding digital signal processing capabilities, which ensures the transformation of a set of electronic warfare means into high-speed digital systems (Poisel, 2019). These directions may be considered the ways of optimizing the current element base.
This is worth noting that staff optimization can be achieved in two ways. One of them is the redistribution of employees in accordance with their duties, and the other is the reduction of the redundant workforce. Personnel reductions in the military are a complex task, which is difficult to accomplish painlessly for the organization. This challenge can be explained by the fact that military activity and service is a highly specialized job, and effective performance requires both experience and knowledge. In addition, there is the institution of ranks in the military sphere, and, for instance, an ordinary soldier cannot perform the tasks of a commander. Therefore, one can assume that the downsizing method is an ineffective way.
Design of the HRD Plan
The proposed methodology for improving military operations is the Six Sigma concept. This methodology entails, in addition to identifying inefficiencies in processes and unnecessary costs, strict discipline (Caforio & Nuciari, 2018). This explains the applicability of this system to the military since discipline is one of the main social institutions in the brigade (Caforio & Nuciari, 2018). In addition, the system seeks to improve the efficiency of processes and the quality of results (Cheng et al., 2019). The brigade’s main problem is the frequent change in the tasks assigned to the team; therefore, Six Sigma can quickly optimize the workflow without the loss of efficiency. In addition, this is worth noting that the Army already had a successful experience with this methodology (Antony, 2020). In 1993, one of the founders of the Six Sigma concept, Michael Harry, was invited to the Allied Signal Corporation.
The methodology was successfully applied, among other things, in the production of avionics and auxiliary power units of combat and military transport aircraft. During the first two years of using the concept, the company achieved savings of two billion dollars (Antony, 2020, p. 94). Over five years (1994-1998) of the Six Sigma application, the company’s stock increased five-fold in value (Antony, 2020, p. 98). In 1999, market success allowed Allied Signal to take over one of the oldest and most famous U.S. industrial corporations Honeywell; today, the company operates under that brand.
Another pioneer in the use of Six Sigma among defense-industrial enterprises was Texas Instruments Inc. By the early 1990s, the company was a manufacturer of guidance units for guided bombs and other precision weapons, thermal imaging devices, and computers for military use (Antony, 2020). Texas Instruments was sold to Raytheon in 1997, and the new owners quickly took advantage of the experience with the Six Sigma concept, expanding it to all of their manufacturing programs. According to estimates in their 2004 annual report, the first five years of Six Sigma brought Raytheon about $3.8 billion in additional revenue (Antony, 2020). The savings in manufacturing processes allowed Raytheon to significantly expand its investment in R&D, enabling it to gain technological leadership, primarily in missile production.
Six Sigma has been used to optimize manufacturing processes in all of Raytheon’s critical defense programs, from combat simulators and simulators to AMRAAM air-to-air missiles, Patriot air defense systems, and Tomahawk cruise missiles (Antony, 2020). The implementation of this system will help analyze both the technical and the human parts of processes in the brigade under consideration. The fact is that troubleshooting the problems and unnecessary costs is the first step to optimizing the work process. In addition, the savings that appear in the course of revealing the shortcomings of workers’ activity will help buy new technical equipment and increase employees’ wages, which will serve as motivation for better work.
Implementation Strategy
For Six Sigma, the most important success factor stands out as being highly organized. High labor organization is one of the most distinctive features of military business, which is expressed in various forms. All activities are conducted within projects, each with established goals, timelines, budgets, allocation of responsibility and authority, risk identification requirements, and record-keeping. The knowledge and skill requirements for the personnel involved in the projects are clearly defined and categorized. The progress of each project is regularly monitored by using an established system of measurable indicators, or metrics (Bruce, 2020). Using the service of an in-house facilitator may contribute to maintaining a sustainable implementation process due to the good awareness of the team’s problems and goals.
This is essential to outline in more detail the main objectives of work optimization. Firstly, the implementation of the Six Sigma system will be introduced in the work of the team with the help of specialists. The goal of this incentive is troubleshooting, along with avoiding faulty or resource-intensive equipment and redundant workers (Bruce, 2020). Integrating intelligence and information flow controls into a single electronic database will make information storage less costly. Creating additional systems of equipment maintenance, information processing, and information range control will optimize and protect the digital intellectual base. Outdated equipment will be substituted with advanced one, and alternative database systems will be created to optimize and accelerate the multitasking of the team.
When conducting optimization, the brigade needs to understand what the purpose of the measures and the anticipated results are. Before decisions are made, all risks are to be identified so that at the end of the implementation process, the opposite effect does not occur (Cheng et al., 2019). The algorithm of optimizing the personnel’s work includes several stages. Firstly, the strategic goals and the objectives are determined to build an evidence-based and reliable working plan. Secondly, the current business processes should be analyzed to obtain the general picture of gaps and areas to optimize. Thirdly, a new staffing schedule needs to be compiled to change the activity regime. Further, workforce needs should be identified to meet employees’ expectations and not to violate their rights. After that, a downsizing action plan needs to be developed in accordance with the objectives set. Employee dismissal is the following step to take, and finally, a new staffing schedule should be approved. Staff reduction should not affect the quality of production processes. To avoid risks and maintain as high-performance indicators as possible, even before the optimization measures, this is critical to think about labor rationing.
The Lean Management concept does not establish requirements for the form of the implementation of the concept and the infrastructure required for it. Therefore, the success of Lean Management largely depends on the initiative and organizational abilities of managers. However, when supervisors change, everything can collapse due to distinctive control principles. The Lean Management concept lacks formalized commitment from senior management, formalized training, planned resource allocation, and tracking success with corrective actions.
The concept is not focused enough on customer demands. Their satisfaction is not directly related to the strategy’s primary goal of eliminating waste and unproductive costs. In the Six Sigma concept, the focus on consumers is a key element. This is caused by the fact that all its key metrics are based on tracking the relationship between process parameters and product characteristics and the specifications set by customers (The Borden Institute, 2018). The key principle of the Six Sigma DMAIC concept begins with the definition of customer requirements: Define, Measure, Analyze, Improve, Control.
The Lean Management concept recognizes defects and inconsistencies as one of the main sources of losses in the enterprise. At the same time, it does not consider methods of statistical management of processes for the elimination of losses (Skelton & Pais, 2019). The concept is not focused on finding sources of process variability and ways to reduce variability, which is one of the main elements of the Six Sigma concept. Defects, the main target of the Six Sigma concept, are only one of many types of losses in enterprises (Skelton & Pais, 2019). Process improvement within the Six Sigma methodology is carried out mainly by reducing process variability by statistical methods and redesigning processes using the DFSS method (Design for Six Sigma). Six Sigma methodology misses such opportunities for process improvement as reduction of nonproductive activities, reduction of waiting time, reduction of inventory and transportation costs, optimization of workplaces (Skelton & Pais, 2019). All of these opportunities are fully realized by the Lean Management concept.
This is also worth analyzing multitasking, which is typical for the activity of the brigade. The fact is that frequent changes in tasks and courses of work negatively affect both the productivity of professionals and their psycho-emotional state. When working in the multitasking mode, the time required to complete cases increases significantly. For this reason, many people feel exhausted at the end of the workday (Tannenbaum & Salas, 2020). When an individual is constantly switching from one task to another, the quality of work decreases due to the very high likelihood of making a mistake (Tannenbaum & Salas, 2020). The deterioration of thinking and emotional processes negatively affects the assimilation of knowledge, comprehension, reasoning by analogy and inference, the ability to see from another person’s point of view, empathy, and critical analysis (Tannenbaum & Salas, 2020). The constant dynamic switching among goals contributes to emotional burnout and may be a constraint. Involving a psychologist in the team can be an alternative solution. The presence of this specialist will allow controlling employees’ conditions, managing the emotional load, and maintaining a favorable microclimate.
Another alternative is to distribute the goals among the specialists. In this way, it is not necessary for individual workers to handle several tasks at once, particularly if the goals are from different areas. The tasks of the team are cyclical, despite the fact that they change. Therefore, for each cycle, this is essential to allocate a highly specialized staff (Wheeler et al., 2020). This will reduce the number of possible errors in activities, avoid the emotional burnout of employees, and increase the productivity of the organization (Wheeler et al., 2020). At the same time, it is possible to avoid unnecessary costs for the maintenance of an increased staff by making the changes of specific specialists seasonal, depending on a particular vector of the team’s activity in a certain period (Wheeler et al., 2020). In other words, the workers’ conditions and their ability to operate should be the main criteria in making optimization decisions because people are the main workforce.
Delivery
There are several success factors for Six Sigma, which should be utilized to deliver the planned changes to the personnel. Its implementation procedure is articulated in the American Quality Engineer’s Handbook as consisting of three stages: project identification, the selection process, and the execution step (Bruce, 2020). Particular attention is paid to the selection of projects, which needs to be justified both in terms of the greatest economic feasibility and feasibility in practice. To achieve the successful outcomes of the implementation, this is essential to deliver to employees the benefits of the system. Firstly, specialists are independent and can make impartial assessments and judgments. Secondly, under a renewed operation mode, employees are not perceived by their colleagues as less experienced. Each team member’s opinion is listened to as an expert in quality improvement issues. Thirdly, workers should be aware of the fact that their reputation and further career are fully determined by the success of the project implemented by them within the Six Sigma concept. This delivery approach is aimed at enhancing the motivation level and engaging each interested party in the change process to build a sustainable change process.
Method of Evaluation
To evaluate the performance of specialists, such metrics as lower and upper tolerance limits are established. For a year of work, a specialist of such a category hired on a full-time basis should bring savings to an enterprise from $500,000 to $1 million. Going beyond the lower tolerance limit means the inconsistency of qualification, and exceeding the upper limit is unlikely. The Lean Management concept, first formed in Japanese enterprises, has other success factors. High labor organization is no longer a success factor, but the result obtained. The high achievable organization of processes, both basic and auxiliary, allows an enterprise to save a considerable amount of resources (Caforio & Nuciari, 2018). Learning the features of the renewed working regime will be evaluated in the context of employee behavior.
In case the reactions to the changes are positive, this will prove the success of the activities performed. In addition, the Lean Management concept addresses organizational-level results and offers a set of tools to make operational processes cheaper and faster. Therefore, the performance outcomes in the brigade will be assessed based on the savings and speed of task execution. Organizational behavior change is seen as one of the ultimate goals, and the aforementioned metrics are useful tools to measure how well the 106th brigade staff has adapted to the new work environment. To retain the results obtained, the personnel’s knowledge can be tested at joint meetings or small-group training sessions. These steps may contribute to enhancing the employees’ awareness of the outcomes achieved and the steps to optimize the workflow further, which are valuable perspectives to accomplish.
References
106th Signal Brigade – JBSA, TX. (2021). Sam Houston.
Antony, J. (2020). Lean Six Sigma in higher education: A practical guide for continuous improvement professionals in higher education. Emerald Publishing Limited.
The Borden Institute. (2018). US Army physician assistant handbook. Borden Institute, US Army Medical Department Center and School, Health Readiness Center of Excellence.
Bruce, K. (Ed.) (2020). Handbook of research on management and organizational history. Edward Elgar Publishing.
Caforio, G., & Nuciari, M. (Eds.) (2018). Handbook of the sociology of the military. Springer International Publishing.
Cheng, C. M., Chan, W. W. L., & Ma, W. W. K. (Eds.) (2019). Shaping the future of education, communication and technology. Selected papers from the HKAECT 2019 International Conference. Springer Singapore.
Poisel, R. A. (2019). RF electronics for electronic warfare. Artech House.
Skelton, M., & Pais, M. (2019). Team topologies. Organizing business and technology teams for fast flow. IT Revolution Press.
Tannenbaum, S., & Salas, E. (2020). Teams that work. The seven drivers of team effectiveness. Oxford University Press.
Types of electronic warfare. (n.d.). Radartutorial.eu.
U. S. Army War College. (2019). How the army runs. A senior leader reference handbook, 2017-2018 (31st ed.). Lulu.com.
Wheeler, A. R., Baur, J. E., Halbesleben, J. R. B., & Buckley, R. M. (Eds.) (2020). Research in personnel and human resources management. Emerald Publishing Limited.