The article, “Ultralight, Ultrastiff Mechanical Metamaterials” by Zheng et al. (1373-1377) presents the results of a study that was aimed at examining the mechanical characteristics of artificial cellular materials. Specifically, the authors note that in the natural environment, there are many cellular materials such as honeycombs and plant parenchyma, which have excellent mechanical attributes despite their relatively lightweight. These natural materials have inspired human beings to develop low-weight and mechanically strong cellular materials using different solid components including metals and polymers. These artificial cellular materials have found a wide range of applications in the production of structural components, heat exchange materials, and biomaterials (Zheng et al. 1373). However, Zheng and colleagues argue that the mechanical properties of both natural and artificial cellular materials tend to diminish with a decrease in their mass density. The authors attribute the decrease in mechanical performance at low densities to the random porosity, which is present in both natural and artificial cellular materials. Moreover, in most artificial and natural cellular materials, the relationship between Young’s modulus and the material’s density is given by the following equation, E/Es α (ρ/ρs)n while the relationship between yield strength and material density is represented as, σy/σys α (ρ/ρs)n (Zheng et al. 1373). In these equations:
- E = Young’s modulus,
- ρ = Density,
- σ = Yield strength, and
- s = Bulk value (Zheng et al. 1373).
Based on the foregoing, it appears that many artificial and natural cellular materials exhibit stochastic porosity, which means that they undergo bending and deformation when compressed by weight because their mechanical strength is tightly coupled with mass density. Hence, to improve the mechanical performance of conventional cellular materials, it is recommended that such materials should be well-fabricated so that they can maintain their structural architecture across different mass densities irrespective of their constituent components (Zheng et al. 1374). Accordingly, Zheng and colleagues describe a new variety of artificial cellular materials known as “ultralight mechanical metamaterials”, which have excellent mechanical performance because they retain their structural architecture across different densities. Apparently, these materials have a stretch-dominated architecture as opposed to the bend-dominated structures that are present in most conventional cellular materials (Zheng et al. 1374). In addition, these low-weight yet mechanically efficient materials have b struts and j joints, which enable them to carry loads when compressed instead of bending as in the bend-dominated structures (refer to Figure A and Figure D). A typical example of a stretch-dominated structure contains an octet-truss unit cell, which exhibits isotopic characteristics when exposed to compressive loading. In theory, the relationship between the relative compressive stiffness and the stretch-dominated material’s yield strength is usually linear, and it is represented by these equations, E/Es α (ρ/ρs) as well as σ/σs α (ρ/ρs) (Zheng et al. 1374).
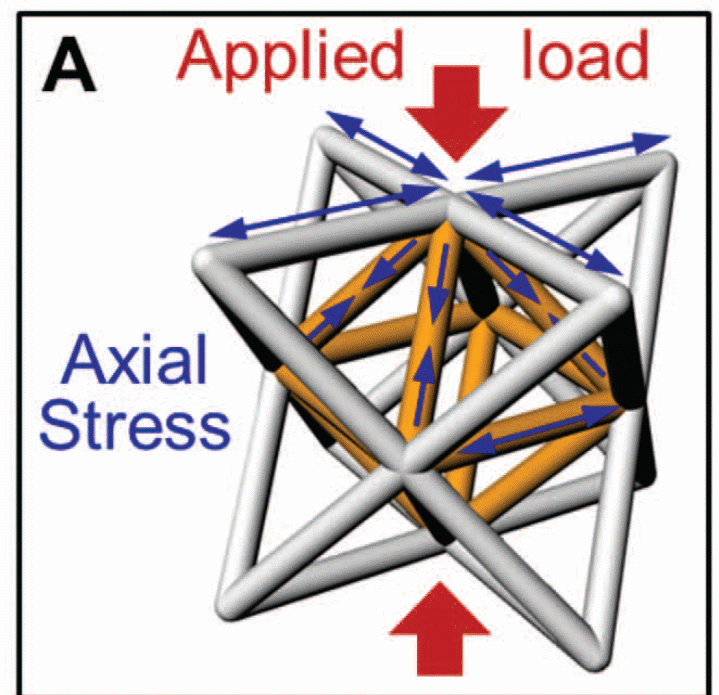
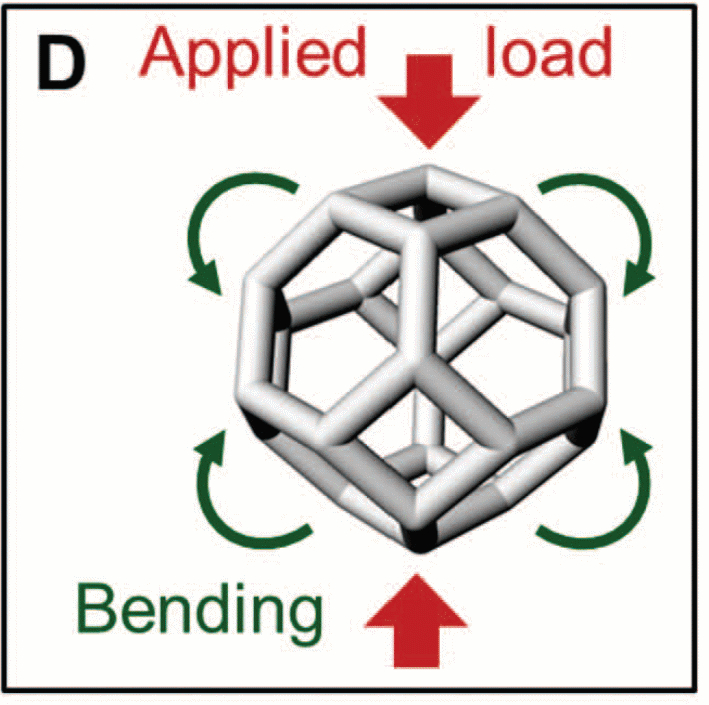
The production of stretch-dominated structures follows the cyclic packing of cell units in three different directions to form cubic lattices (refer to Figure B and Figure C). Moreover, the cells can be packed side-by-side to produce bulk lattices. On the other hand, the stretch-dominated micro-lattices are fabricated using the projection micro stereolithography technology in which microstructures are manufactured through layer-by-layer addition of cells and other constituent components (refer to Figure G). Unlike other technologies such as three-dimensional (3D) printing, the projection micro stereolithography technique is very efficient in the manufacture of 3D lattices, which tend to have greater structural complexities (Zheng et al. 1374). During the fabrication of stretch-dominated microlattices by projection microstereolithography, other constituent components such as metals and ceramics can be added through nanoscale coating. The combination of various techniques to manufacture mechanical structures may help to guarantee the production of lightweight and mechanically efficient materials, which withstand compressive loading without deforming (Zheng et al. 1375). In conclusion, based on the findings of Zheng and colleagues, it appears that the lightweight “mechanical metamaterials” do not suffer substantial mechanical losses with decreases in mass density as opposed to conventional cellular materials.
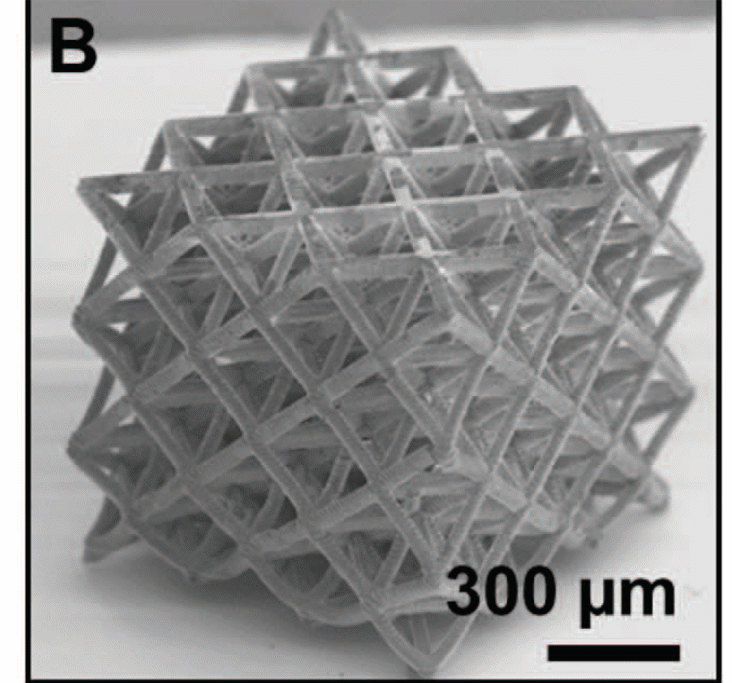
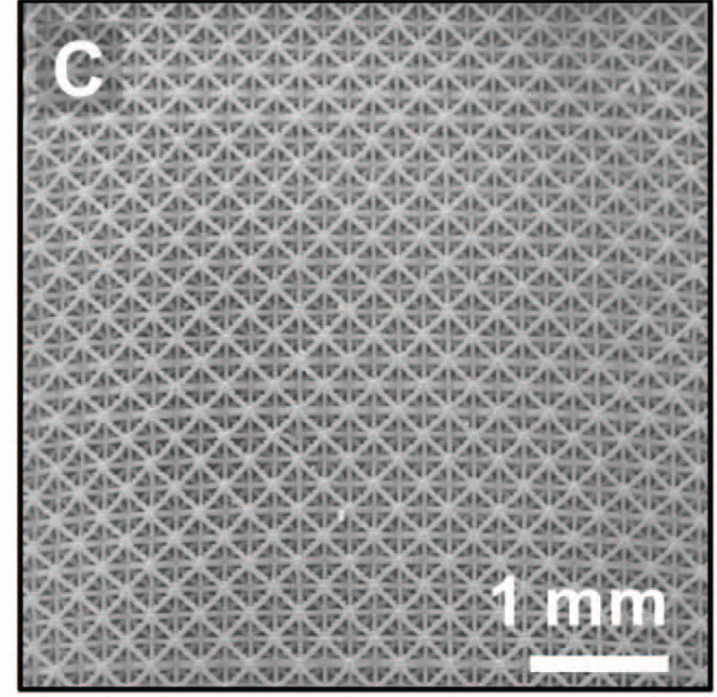
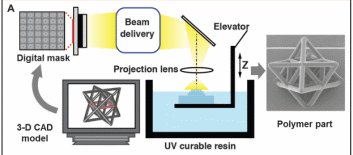
Work Cited
Zheng, Xiaoyu, et al. “Ultralight, Ultrastiff Mechanical Metamaterials.” Science 344.6190 (2014): 1374-1377. Print.