Introduction
For a long time, UPS has been a major actor on the delivery market. However, in the 2010s, it started to struggle against newer competition such as FedEx and Amazon. The primary reasons for it are the outdated equipment in UPS’s facilities, as well as the necessity to modernize them instead of buying new technology outright. However, the recent modernization has helped UPS to improve and show that to successfully compete, a company must fully embrace technology and not try to use an outdated machine with cosmetic modernization.
Discussion
UPS’s problem is mainly a technological one, as its facilities used to lack automation. For example, in Mesquite, human workers have many functions, as they align each box, pick packages, package down chutes, and fill trailers. As a result, human mistakes add up, causing crises in the factory. Meanwhile, the competition such as FedEx or Amazon has automated facilities. Some of UPS’s buildings, such as the one at Fort Worth, have higher automated capacities, but still fall behind the tools of Amazon or FedEx.
UPS tried to catch up with the “band-aid” approach, adding extra shifts, working hours, or retrofitting parts of older buildings. However, this was just a temporary measure, and now UPS has taken the more radical direction. In the last three years, the company has invested $20 billion to new facilities to modernize them in accordance with the shopping and shipping trends. According to an online article by Dekhne et al. (2020), UPS only expands slowly, but so do FedEx and Japanese Yamato Holdings. The reason for this that electronical technology needed for automation is dealt by these companies’ competition such as the aforementioned Amazon or Alibaba, which develop their own delivery systems. Thus, spending too much on their technology will fund their competitiveness in delivery, which UPS or FedEx definitely do not want.
Another reason for the slow developing of automation is that UPS’s workers are unionized, unlike FedEx’s, and oppose bringing in new technology as they are afraid of losing their jobs. Namely, an organization called the International Brotherhood of Teamsters vehemently opposes the technology, correctly mentioning that it streamlines jobs and eliminates them. Instead, such organizations offer to hire more workforce to handle the increased packages demand.
Despite these shortcomings, automation performs well for UPS. The upsurge of packages during the coronavirus pandemic has been handled easily. The number of shipped packages in that time period had increased dramatically, by 65% compared to the year before (Mims, 2020). Active usage of Bluetooth technology turned out to be effective, further simplifying the workers’ tasks and delivery processes. Thus, the radical solution of spending billions on automation proved to be beneficial.
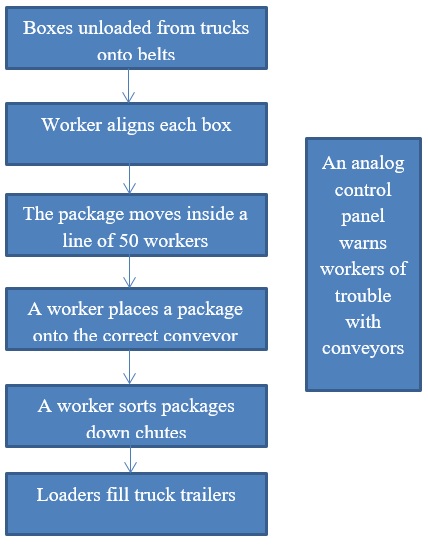
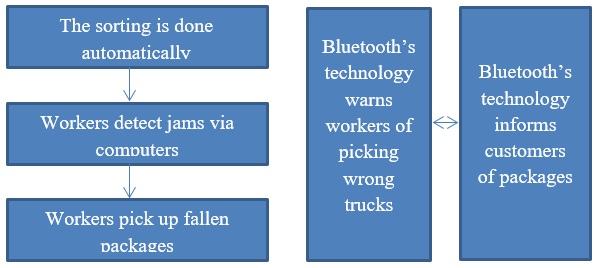
Conclusion
As seen on the diagrams, automated package sorting has significantly changed operations and decision making at UPS. Instead of working on package sorting by themselves, workers only supervise machine’s work. In addition, new technology has allowed creating new jobs, such as the new UPS center in Houston creating 575 part-time jobs. In conjunction with using Bluetooth technology for minimizing truck delivery mistakes it has allowed to reach the pandemic success mentioned above. Still, UPS claims that automation is not enough for development and has created a software layer to further improve management of package flows, including connection between modern and outdated facilities (Ziobro, 2018). Thus, it is important for companies to keep their automation up to date and not try to compete by trying to modernize outdated equipment.
References
Dekhne, A., Hastings, G., Murnane, J., & Neuhaus, F. (2020).Automation in logistics: Big opportunity, bigger uncertainty. McKinsey & Company.
Mims, C. (2020). As e-commerce booms, robots pick up human slack. WSJ.
Ziobro, P. (2018).UPS’s $20 billion problem: Operations stuck in the 20th century. WSJ.