Vestas Wind Systems
The company headquarters is in Denmark, and as a result of enormous growth of the company since its founding in 1945, it has set up manufacturing plants in several countries including Germany, United kingdom, India and US. When the company initially started, it used to manufacture household electrical devices but drastically changed their manufacturing through years making agricultural appliances, intercoolers, hydraulic machines and turned their focus to wind turbines since 1989.
Fairly writes that, “For the last eight years, the company merged with NEG Micon, another Danish company specializing in making wind turbines.” The two companies put their efforts together to establish the worlds biggest manufacturing plant of turbines using the brand, Vestas Wind Systems.
The company recovered in the year 2006 after a drop in sales the previous year making it be ranked the number one top green company in 2006. Towards the end of 2008, the company embarked on expansion plans in their plants in Colorado and Oregon. While the company is aggressively looking for new markets, it has been closing some of the plants in regions that their demand is low.
Fairly (43), states that, “Some of the closed manufacturing plants include the one in Scandinavia and Isle of Wight in the United Kingdom.” Todate, over forty thousand wind turbines have been installed by vestas worldwide with its workforce which is estimated at around twenty three thousand people globally. The new expansion targets include countries like China and US where its products are on high demand.
The company is gradually shifting production to China and US because of reduced demands in Europe. The companies goal when making their turbines is to provide customers with turbines of high quality, they don’t look at market share and prices when designing them. One of the products manufactured by Vesta is V112-3.0MW. It is designed in a manner that it can adapt to areas with low and medium wind.
The company projects that such areas will be shift to wind power in future. This device has the ability to produce more electric power than other turbines in that category of 3MW. This turbine is reliable, easy to service and offers greater efficiency than other turbines in the same class.
According to the company website, “Another product designed for areas with light winds is Vestas V90-2MW.” This one is mainly designed for European countries because of its light weather conditions. Another product from Vestas is Vestas V90-3MWwhich is used all over the world to generate electricity. The distinctive feature of this product is that is uses pitch control.
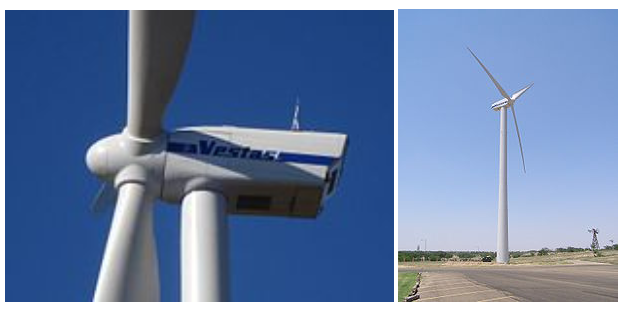
Vestas company spends a substantial amount of its revenue in research and development. Recent statistics indicate that it spend in excess of one hundred and thirty million in the year 2009 in research. Some of its recent research findings is unveiling a stealth wind turbine in collaboration with QinetiQ which can offer solutions of radar reflection to the aviation industry. According to financial statements of 2010, the company is doing well as it collected profits in excess of 156 million Euros (Reddal, 77).
Sinovel Wind Group Company
The company is the largest manufacturer of turbines in China, and its headquarters is in China. Globally, it is ranked number three in production of wind turbines. The company targets to be the leader of turbine production by the year 2015 with major target market being foreign countries. Sinovel employs approximately 200 employees and has a capacity to produce eight hundred units per year presently. Its manufacturing plant is in Dahlia, China though it intends to open other plants in China and other countries.
Sinovel aims at making wind turbines that are adaptable to all types of weather and environmental conditions around the world. The company has been growing steadily since its inception and has managed to make big milestones in production of electricity using wind turbines.
In the year 2008, the turbine installations of Sinovel produced almost 1500MW of electricity making it the leader of Chinese green energy production and seventh in the world. By the year 2010, it had more installations done in China and other parts of the world with total estimation of power generation being put at around 4400MW, thereby leading the Chinese market and becoming the world’s number two.
Sinovel has a mission that is based on its historical formation which is to localize production of important electrical equipments and the focus to provide green energy to the whole population of China and the world. Its long term strategy is to provide innovative products, in large scale to meet international demands.
Sinovel has been a leader of the Chinese market in producing innovative turbine equipments in the sense that; it is the first to introduce an advanced wind turbine in the world, it was the first to make and supply the turbine equipments locally, it was the leader in developing 1.5Megawatt turbines that can suit all conditions of weather in the world and many other achievements.
The company is majorly involved in manufacturing products for commercial and industrial use. On the list of several products manufactured by Sinovel is SL600 turbine. According to the company website, “This turbine was developed independently by Sinovel group with its own intellectual rights.” It designed in a manner that it uses modern technological generators with Sinovel’s expertise.
Acher writes that, “SL5000 is a type of wind turbines that they make which utilizes variable pitch and double power generation technology.” SL300 is another product that they have developed using their own expertise. Its average power rating is 3000kW with a rotor diameter that ranges from 90 to 113 meters. The advantage with this product is that it is adaptable to all weather conditions.
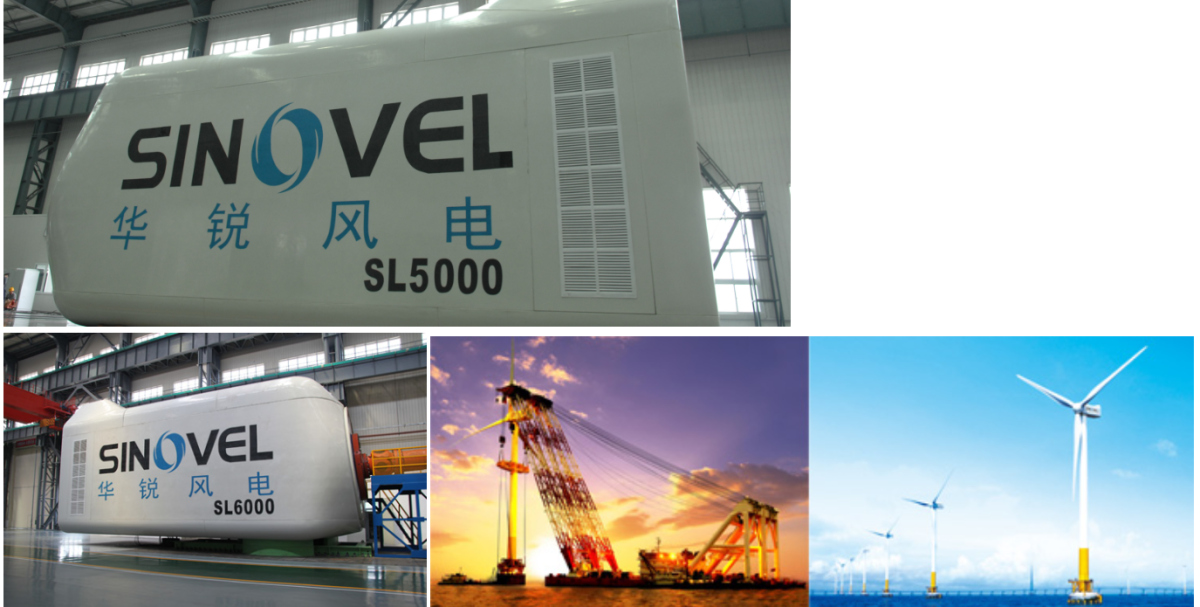
Since the company was started, it has given priority to provision of quality customer service and technical support. It continuously strives to provide services with an aim of meeting customer’s satisfaction.
As a technique of enhancing scientific skills in order to sustain itself with the competitiveness of the market, the company has employed experts from China and other parts of the world with specialization in wind power to form part of research and development team that consists of almost 700 personnel. The operation of the company has also been boosted by cooperation with China Development Bank to a tune of six and half billion dollars.
Xinjiang Goldwind Science and technology Company
Lou (22) describes Goldwind Company as “One of the largest companies manufacturing wind turbines in world and one of the leaders in China.” Its manufacturing plants are in Urumqi, Xinjiang, China. Lou further states that, “The Company was established in 1986, which marked the start of wind power energy in Xinjiang, China.”
The companies aim is to research and develop large sized wind turbines for commercial and industrial use. Some of the products that the company produces are 600kW to 1.5 MW permanent magnet wind turbine products.
Apart from these products, it is also involved in developing and selling wind power plants. In the year 2009, the company installed close to three thousand seven hundred wind turbines of 750kW and sixteen hundred 1.5 MW turbines. The main market of the company is China though it installed some turbines in Minnesota, United States.
For the last eight years, the companies’ market share in China has been growing steadily and is said to supply its products to over twenty five percent of the market. By the end of the year 2008, the company had sold more than three thousand wind turbines that have the capacity to produce two thousand eight hundred and ninety five mega watts of electricity. In the following years, the market demand in China grew making them receive enough orders.
The company receives a good number if orders for all the products that are made including 750kw and 1.5MW turbines. The company also made a breakthrough to the International market when it received orders from United States and Cuban company, Energoimport.
The company employs more than one thousand five hundred people and its profits have continuously grown over the years. For instance, in the financial year of 2010, it made profits worth RMB 4.02. More than ninety five percent of the revenue of the company is collected from sale of wind turbine generators.
According to the company sources, Goldwind intends to benefit greatly when local companies offering green energy and expand their markets to foreign countries. They believe they would have good chances of growing. According to its mission of growth, it intends to acquire technology companies that can design highly efficient generators that can be transported easily. It also intends to buy other renewable electric devices.
Siemens Wind Power
According to Wessel (10), “Siemens Wind Power is a manufacturing company of wind turbines with main offices and manufacturing plants situated in Brande, Denmark.” It specializes in designing products for commercial and residential use. The company was fully acquired by Siemens groups of companies from Germany through its division of renewable energy from the year two thousand and four. By the year 2009, Siemens Wind Power had a market of six percent worldwide with a large market in the shores of Europe.
Wessel (9), further worote, “The Company was first established in 1980 by Danregn.” The name of the company was changed later to Bonus energy in nineteen eighty three but was later sold to Siemens in 2004. According to Wilkes (26), “The main manufacturing plant is in Brande, Denmark with other subsidiaries in several countries.”
As part expansion plans, the company opened other offices for research and development in Colorado. One of the products of the company that is unique is the Hywind. It is a wind turbine that is designed in a manner that it can float in the sea while it functions. It is designed to utilize the winds of the sea to generate electric power. The main products of the company are SWT 2.3MW and 3.6MWwind turbines.
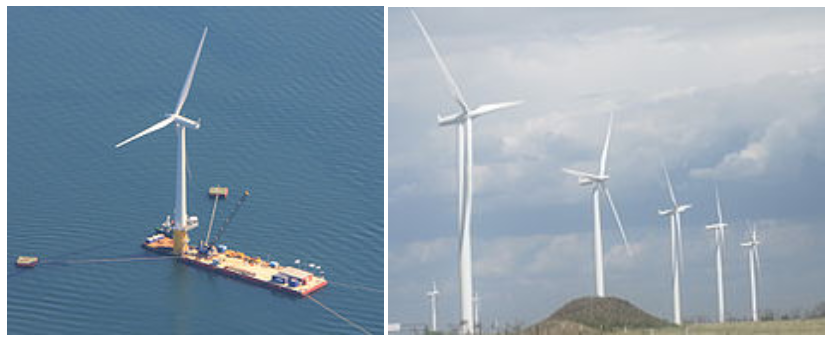
By the end of the year 2009, the company had employee capacity of about six thousand. Since the company started, its focus was to develop wind turbines that would remain competitive in the market and it has evolved from making 22kW wind turbines to the current Megawatt ranges.
In order to realize its vision, the company has employed experts in the field of wind turbines technology and using conventional technological devices. The output of their efforts is development of high power wind turbines that match the demand of the market. Siemens Wind Power is proud for the effort of its more than five thousand employees who have contributed to realization mission of the company.
Siemens Wind power provides customers with their products by giving them guarantees of the investments they have undertaken. They offer guarantees so that customers can be sure of the services during that period. The recent order from United States wind firms is to boost by a big margin profits of Siemen Wind Power.
Wilkes describes that, “This is a confirmation that that the company is the leading provider of wind power in off shores.” One of the most recent projects of Siemens wind power is the construction of DanTysk wind farm in Germany that covers seventy square kilometers with a capacity to supply electricity to over five thousand households.
Enercon
The company, Enercon, is a leading provider of green energy in Germany and the 4th largest globally. The company specializes in manufacture of wind turbines and the main plant is situated in Aurich, Emden and Magdeburg in Germany. Other countries they have manufacturing plants include Portugal, Turkey and Canada.
Enercon mainly produces its wind turbines for commercial purposes and domestic use. By mid this year, it is estimated that Enercon had installed over seventeen thousand wind turbines that has an excess of 24 Gigawatts of power.
Their most common product is the E-40 wind turbine Model which is a modification of the 1993 design. As of mid this year, its market share was estimated to be slightly above seven percent globally, while in the German market, it controls sixty percent of the market share. One of its main foreign users is Ecotricity, from Britain.
A distinct feature of its wind turbines is the technology that uses gearless drivers, with an annular generator. According to Enercon at a Glance (55), “This is different from other wind turbines because the other wind turbines use gears to increase the speed of rotation of the gearbox. The other difference with this generators is the housing which is drop shaped in addition to their towers that are painted green to march the surrounding.”
Some of its popular products include E-126 model that is widely used in Europe. Initial power rating of this model was six Megawatts but has been modified to generate 7.5 Megawatts. Another product is the E-112 model that was invented in the year 2002, and became the largest in the world for two years because of its ability to generate 4.5 Megawatts. It was later modified to generate 6Megawatts. To date, the company has not embarked on setting up projects on off shores but has instead been critical of the offshore wind parks.
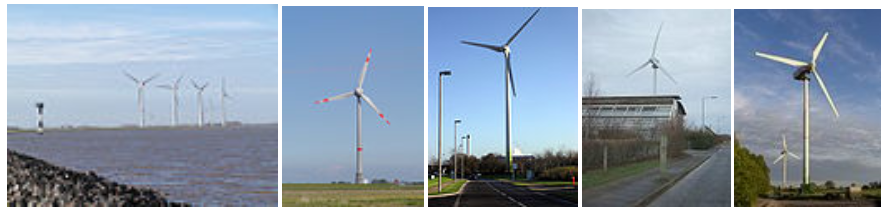
Enercon had been burnt from selling its products to the US market due to an infringement dispute with Kenetech (Hermann, 120). The company employs over thirteen thousand employees. Just like the other companies, Enercon lays emphasis on quality of its products and employs experts of wind turbines so as to meet the expectations of their customers. One of their core values is to consult with authorities and customers so that they can find practical solutions of green energy.
The financial performance of the company has been incremental over the years despite the limitation of US market.
Gamesa Corporation Tecnologica
This company is involved in manufacture and making materials for wind turbines. It makes products for commercial and industrial use. The company is Spanish based and its main plant is located in Biscay, North of Spain. It does business by management of wind farms as well as selling wind turbines.
Before the competition by Chinese manufacturers, Gamesa was the worlds’ second producer wind turbines; currently it enjoys the sixth spot, though, the company has not lost its grip in the Spanish market. According to Barriviera (111), “It is estimated that the company has installed an equivalent of twenty thousand Megawatts of power in 4 continents.”
The company began manufacturing activities in the 1976 with a focus of developing of developing technological devices that meet emerging needs of the society. Among the products that it started making were robots and composite materials. A division of the company was established in 1994 to manufacture wind turbines for commercial purposes.
The company has financial stability and has been listed in the stock exchange since the year 2000. It has assets worth 4.9 billion Euros and made profit worth 50 million Euros in the year 2010, while it employs more than six thousand seven hundred people.
Since 2006, the company changed its strategies and is now focused to manufacture devices associated with green energy, which is wind power. The company is interested in setting up turbines in offshore areas and has begun constructing a manufacturing plant in Britain to oversee this part of production.
The construction of this new factory is estimated to cost around one hundred and thirty four million pounds. The company has received global recognition for its efforts to provide sustainable energy and is listed in the sustainability index. An example of a wind farm project that Gamesa is involved is the Allegheny Ridge Wind farm (Acher, 11).
International sales of its products have helped sustain growth momentum. Among the leading international markets that they benefited from were India and Latin America. Of all the sales in 2011, all orders of MW category were sold to the international market.

Gamesa has employed experts in wind technologists and has been shown by manufacturing of several products that meet customer satisfaction. Among the list of its products is G10X-4.5 wind turbine which is one of the most competitive in the market. It is designed in a manner that it can suit the most complicated Grid connections. Among the advantages of this product is the inbuilt design that enables it reduce noise and ability to be transported with ease.
The G9X-2.0 is another wind turbine in the Megawatt category. It is made in a manner that can suit all wind conditions. Its advantages are reduced noise and ability to predict maintenance. G5X-850kW model is designed to generate electricity in areas with low wind levels.
Works Cited
Acher, John. China became top wind power market in 2009 Reuters. Web.
Acher, John. A Wind Power Market in 2009 Reuters. Web.
Barriviera, Guadalupe; Tobin, Paul. “Gamesa Aims to Control a Fifth of Wind-Turbine Market”. Bloomberg. 2008. “Enercon at a Glance”. Web.
Fairly, Peter. Stealth-Mode Wind Turbines Technology Review, 2009. Web.
Hermann, Simon. Hidden Champions of the 21st Century : Success Strategies of unknown World Market Leaders. London: Springer, 2009. Web.
Lou, Ying. “Goldwind Plans IPO as China Combats Climate Change”. Bloomberg. Web.
Reddall, Braden. Vestas will not chase market share at any price Reuters/BTM Consult, 2010. Web.
Wessel, Lene. Siemens overtakes Vestas (in Danish) Ing.dk, 2010. Web.
Wilkes, Justin. Operational offshore wind farms in Europe, end 2009 EWEA. Web.