Strategic Plan
A brief history of the organisation
Twenty-five years ago, in 1987, four friends formed a small company “ABC Manufacturing Company” in the United Kingdom, but three owners decided to retire and sold their shares three months ago. A foreign investor has recently bought 75% shares of this company from three friends and invested £10 million with the intention to achieve a 10% return of his investments in the next four years. He appointed a new manager and purchased two brand new large and modern CNC centres with all essential tools and software for the future development of the company by managing human resources and increasing productivity and quality.
However, the purpose of this report is to recommend the company by analysing strengths, weaknesses, opportunities and threats, leadership and management, and organisational structure with emphasis on grouping and teamwork, organisational culture along with the importance of information systems, performance and motivation, training and development program, and so on.
SWOT Analysis of ABC Manufacturing Company
Strengths
- Foreign investor: seventy-five per cent shares of this company have purchased by the foreign investor, which will strengthen the financial position of the company to increase profit margin;
- Sales Volume: According to the case study, sales revenue from the sales of the products have increased from last year, for instance, the turnover has increased from £20 to £30 million;
- Research and Development: The management of this company has concentrated more on the research on the company to identify the loophole of the leadership, human resource management, internal controlling and production system. However, the research outcomes will help the management to take proper decision to change organisational structure and other strategic plans;
- Knowledge: Though the business was not profitable enough to compete with the competitors, the old owner has 25 years experience to operate this company. So, the owner has vast knowledge in this sector, which helps him to contribute the company for future development;
- Resources: Now, the company has two brand new large and modern CNC centres with all essential equipment and software. However, these modern equipment will play a vital role to produce quality products and develop the brand image in the national and international market in the future;
- Relationship: The old manager of this company maintains a good relationship with some of factory floor employees particularly with the operators and engineers, which will help the company to increase production capacity and ensure quality;
- Integrity: the company survives in the competitive market for a long-time because the owners and managers controlled the company with integrity.
Weaknesses
- Decision-making Process: According to the case, the new foreign investor holds 75% shares of the company, which indicates he has the rights to make a decision as a majority shareholder;
- Communication: The other manager is manufacturing engineer and has broad knowledge on the technical issues; therefore, he can manage the employees in this field more efficiently, but it can also create communication problems with other staff of this company. In addition, the employees are not aware of their function, the overall objectives of the company and strategic plans; therefore, the management cannot implement the strategy properly;
- Coordination: the success of the business depends on the team spirit and coordination of all the departments. However, the managers of this company are not working as a team since another manager has no interest in sales, marketing, and customer negotiations;
- Staff turnover rate: one of the main internal problems of this company is a high staff turnover rate because new employees have no job satisfaction for various reason;
- Low performance: the old employees blame that the new and young staff are not efficient to produce quality products for the company, for instance, over 20% of them is performing much below satisfactory level;
- Workload: As the company has no separate department for different sectors, the owner faced a serious workload with dealing with the tasks of financial, logistics and human resource department;
- Old Machinery: As the company is paying no attention to modernise the equipment, it is not possible to change the quality of the products.
- Recruitment policy: the entire recruitment and selection policy is not effective for the company, which decrease staff retention and engagement min efficient employees;
- Remuneration policy: many large companies restructured their remuneration policy to reduce operating costs to sustain in the competitive market whereas this small company is double paid weekends and night shifts in some cases in this recessionary economy;
- Lack of Training: This company has no staff qualified to operate or work in a new CNC centre, but the managers of the company had not arranged any training program to develop their efficiency;
- Other: this company has faced many other internal problems including the presence of considerable, but unofficial unions, less interest on small-batch highly profitable orders, and so on.
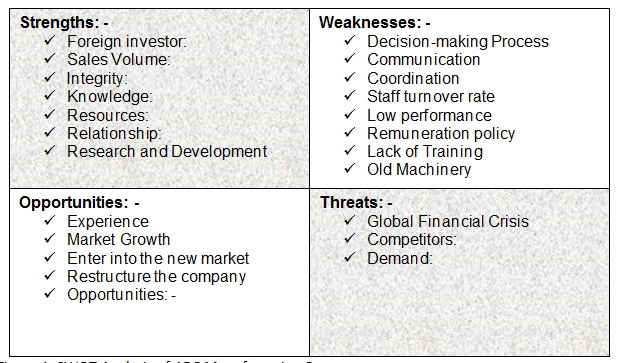
Opportunities
- Market Growth: Financial investment by foreign investors increase the opportunity of market growth;
- Enter into a new market: As 75% share of this company has owned by the foreign investor, it can assume that it would be possible for this company to penetrate the business in the new country by using the knowledge and experience of the new investor about his country;
- Restructure the company: It has already prepared a budget to restructure of this company to become a successful company and gain a competitive advantage over the competitors;
- Experience: The owners of this company had long experience (25 years) to operate this business, which will help the managers to improve the present condition in the future by changing strategies and implementing development plans.
Threats
- Global Financial Crisis: The recessionary impact is one of the main external threats for this company as the managers seem that the profit margin is decreasing gradually (from £6.0 million to just £1.0 million in 2011) due to lowering the purchasing power of the customer for the financial crisis;
- Competitors: According to the case study, the presence of large competitors in the international market is a serious threat for the existence of this company; particularly Chinese and Indian companies are the great threat for this small firm. Actually, Chinese and Indian companies have enjoyed some competitive advantages, such as the availability of low-cost, efficient labours, and low production costs;
- Demand: In addition, the decrease in demands is also threats to the company.
Vision & Mission Statement
ABC Manufacturing Company has a mission to restructure the company to develop leadership skills, the performance of the employees for good organisational culture to gain a competitive advantage. However, the long-term vision of this company is to establish ten CNC centres within the next five years and to be one of the most successful companies in the global market by competing with the Indian and Chinese competitors.
Improvement initiatives
As the company fails to maximise its profit margin due to high operating costs, old machinery, the low performance of the employees; thus this report suggests to shifting production facilities, B2B e-commerce integration, outsourcing from emerging Asian, market, changing recruitment, selection and remuneration policy, restructure organisational chart and integrating of the information system, arranging training program and developing organisational culture.
HRM issues
Resourcing and legal issues
Resourcing means assigning actual resources to the project; here, ABC Manufacturing Company has 96 employees including two managers, four maintenance engineer, ten qualified refurbishment engineers, and 80 operators; however, most of them do not understand their job responsibilities to complete the project or deal with the problems of the company by bringing organisational change to develop its profit margin. Therefore, the human resources department of ABC Manufacturing Company should consider the following the recruitment and selection process to appoint new engineers, designers and other workers –
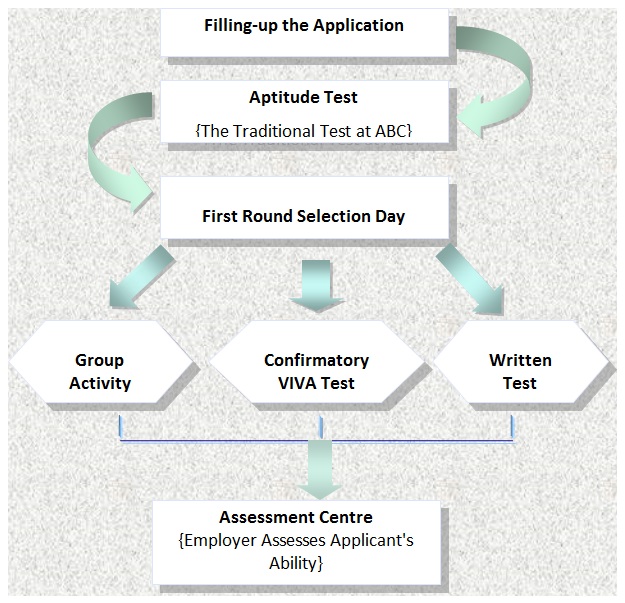
The new employees of ABC Company had no job security and responsibility, which increase the staff turnover rate here and reduce the efficiency level as well. Therefore, the management of this company had to spend lots of money for the continuous recruitment process, and now it has almost no employees qualified to operate or work in new CNC centre; in this context, it is essential to change the recruitment process and some common, but important factors need also consider, such as –
- This company must recruit new members on the basis of technical knowledge and long-term experience;
- The initial test has to consist of some aptitudes, and psychometric assessment test and qualified candidates get the opportunity to sit for a written exam;
- Selection team must consider interpersonal skills, patience, attitude, and communication skills;
- All the candidates must be selected on the basis of merit irrespective of gender, race, or ethnic minority;
- Finally, management would recruit such a candidate who will work for a long-time for the ABC Company to reduce staff turnover along with developing work specialisation.
This company follows local rules and regulation, including taxation policy, Companies Act 2006, corporate code of conduct along with memorandum and articles of association.
Leadership and Management
Pearce & Robinson (2006) and Lewin, Lippit & White (1939) described leadership as the capacity to influence the staff to achieve the vision or set of common objectives; however, the source of influence may be formal. However, Bolden, Gosling & Marturano (2003, p.5) and Pitt (2001) stated that leadership is a complex procedure as it is significant to clear visions and to inspire the staff to achieve competitive advantage over the market players. On the other hand, Robbins & Judge (2008), Pitt (2001), Bolden, Gosling & Marturano (2003) and Rowstrom (2011) further expressed that organisations need strong leadership and strong management for optimal effectiveness. However, Lewin, Lippit & White (1939) provided three leadership styles, which will help to discuss the leadership approach of ABC Manufacturing Company, for instance –
Participative Leadership Style
Lewin, Lippit & White (1939) defined this democratic leadership approach and pointed out that it is more applicable to the contemporary firms because the leaders notify the workers about their strategic plan and consider the feedback of the staff for decision-making and implementing strategies. At the same time, Lewin, Lippit & White (1939), Weihrich & Koontz (2005) and Cherry (2012) stated that democratic approach motivates the workers to take part in decision-making along with crisis or stress management process in a broader context.
However, the present research on the ABC Manufacturing Company identified that old employees have two main options for improvement, such as, modernise and improve with NC (numerical control) and operators’ training and development costs. On the other hand, new employees are the least influential group and leaving within first two years of employment; however, they have some opinions, which can also play a vital role for the development of the efficiency level of the employees.
For instance, new employees stated that there are no clear career progression paths for workers and no clear hierarchy in the company; therefore, they feel alienated, unrepresented and unimportant in the job place. In this context, the top management team of the ABC Manufacturing Company must follow democratic leadership approach in some cases and consider the feedback of the employees to coordinate the functions of the members and the managers would train and assist the human resources (particularly new workers) to balance their family and work life to attract and maintain professional ability;
Autocratic Leadership
On the other hand, it is a customary view where leaders enjoyed ultimate and unlimited power to make their decisions and implement of the plans without consulting with human resources; however, they can provide rewards and penalties for the performance of the employees (Lewin, Lippit & White 1939; Johnson, Seholes & Whittington 2006; and Katzenbach & Douglas 2000).
On the other hand, the workers have to strictly follow the command of the managers and the higher authority would never take into account the comments of the employees for the future development because the leaders think they have a better understanding on the management system (Johnson, Seholes & Whittington 2006; Nader 2012; and Katzenbach & Douglas 2000).
The employees of ABC Manufacturing Company are not aware of their job responsibility, and young staff are not motivated; therefore, this approach would not be fruitful at this stage while managers need to motivate them applying several policies and taking many technical decisions where the opinion and feedback of proficient workforce play an imperative role in administrative control.
Delegative (Laissez-Faire) Leadership
Lewin, Lippit & White (1939) stated that it is well known as the “hands-off¨ style, and this approach provides the scope to the staff to make their decision using discretionary power and perform their own technique. However, this approach would not be effective for the ABC Manufacturing Companies because the efficiency level of the old and new employees are not the same standard; so, quality and sales of the product will fall immediately if the unskilled human resources enjoy decision-making power in some extent.
In addition, there are many other leadership styles to influence the firms’ members, for instance, Great Man and Trait theories, behaviourist and contingency theories, situational leadership style, transactional and transformational leadership theory, and so on (Pitt 2001; Robbins & Coulter 2008; Hellriegel, Slocum & Woodman 2002; and Katzenbach & Douglas 2000); however, some methods are effective for the company, for instance –
- Transformational: According to this style, it is executive leadership, which incorporates a social change to improve motivation, assurance and performance level of the employees (Bolden, Gosling & Marturano 2003; Johnson, Seholes & Whittington 2006 and Holman, Devane & Cady 2012). Moreover, this approach can transform an employee’s self-interest for the good of the team, raise their expectations along with moral values and enhance the confidence of the staff to achieve the vision of the company (Booth 1996; Orlikowski 1995; Kotler & Armstrong 2006; Mellahi & Wilkinson 2012). However, the ABC Manufacturing company should follow this approach because the workforce would like to work with a transformational leader due to above-mentioned advantages;
- Situational Leadership Style: This style does not consider any precise approach of leadership rather leaders take the style considering several factors related with the present condition of the company (Bolden, Gosling & Marturano 2003; and Weihrich & Koontz 2005). For instance, the leaders may require to follow an autocratic approach in some condition and others may need to adopt a participative approach to manage different levels of employees in the same firm considering the employees’ forces, the situational forces and leader’s forces (Bolden, Gosling & Marturano 2003; Weihrich & Koontz 2005; and Holman, Devane & Cady 2012)
Organisational Structure
It refers to how job responsibilities are properly divided, grouped and coordinated (Hitt, Ireland & Hoskisson 2001; and Johnson, Seholes & Whittington 2006). However, there are mainly six elements those managers need to consider to design organisational chart, and these are –
- Work specialisation: The owner of Ford motors had provided same tasks with small size repeatedly to the employees to specialise the workers in a single sector, which reduced the time to manufacture goods with ensuring high quality and making the most efficient use of its employees’ skills (Robbins & Coulter 2008, p.367; Robbins & Judge 2008, p.539).
- Departmentalisation: After grouping the employees through work specialisation, it is essential to group the employees on the basis of common tasks, for instance, the production manager of the manufacturing company has a responsibility to separate engineering, accounting, manufacturing, personnel, and supply specialists into the common department, which is absent in the present case;
Table 2: Departmentalisation by type. Source: Self-generated from Robbins & Coulter (2008).
- Chain of command: It is an unbroken line of authority that extends from the top of the organisation to the lowest echelon and clarifies who reports to whom (Robbins & Coulter 2008, p.369; Robbins & Judge 2008, p.541). Otherwise, employees have to cope with conflicting demands or priorities from several superiors (Robbins & Judge 2008, p.542);
- odernSpan of control: This is a significant factor as it determines the number of levels and managers a firm has; however, a manager can maintain close control by keeping the span of control to five or six employees (Robbins & Judge 2008, p.543; and Pearce & Robinson 2006);
- Centralisation and Decentralisation: Some firms are highly centralised while top managers make all the decisions and lower-level managers just carry out top management’s directions; on the other hand, Some firms are extremely decentralised in which decision-making is pushed down to the managers (Robbins & Judge 2008, p.543);
- Formalisation: It indicates the degree to which jobs within the firm are standardised (Robbins & Coulter 2008).
Organisational Structure of ABC Manufacturing Company
The main characteristics of the previous organisational structure of ABC Manufacturing Company were –
- It has a low degree of departmentalisation.
- Wide-span of control.
- Authority centralised in the owners; thus, they enjoyed the right of decision-making power.
- Little formalisation.
- It usually has only two or three vertical levels.
- A loose body of workers.
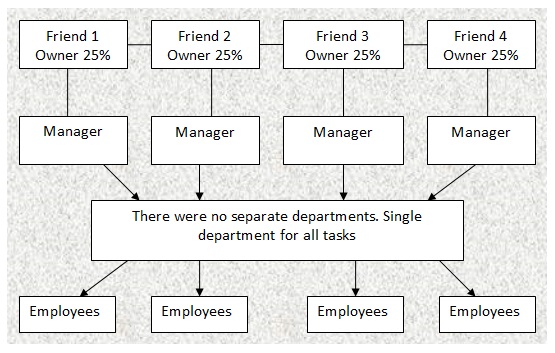
However, the advantages of the previous organisational structure were –
- It was fast, flexible and inexpensive to maintain.
- The managers are accountable to the Chief Executive Officer.
The previous organisational structure had many disadvantages, such as –
- It becomes ineffective when the company expands its business because of low formalisation and high centralisation, which creates information overload at the top;
- At the same time, decision-making becomes slower as it becomes difficult to consider all issues.
Grouping and Team Working
However, the managers of ABC Manufacturing Company should try to specialise the employees and consider this issue while preparing organisational chart as the employees of this company are not efficient to produce quality products particularly more than 20% of the new and young employees are performing below standard.
Here, it is important to note that usually, ABC Manufacturing Company provided double remuneration who works in the weekend or night shift, but the managers do not discriminate between the efficient and inefficient employees to develop a team; so, I will differentiate skilled and unskilled labour to reset organisational structure along with remuneration policy, which would influence all members to work as a team.
ABC Manufacturing Company is a small company, which needs to change organisational chart in order to develop strong administrative control to become successful; however, this report suggests a new simple organisational restructure because though it would not bring a major change in the hierarchy. As foreign investor holds 75% shares and old owner hold 25% share of the ABC Manufacturing Company, this report recommends to forming a chief management team consisting of two owners who will be responsible for controlling the entire company and taking major decisions for the future development; however, the following figure shows suggested organisational chart –
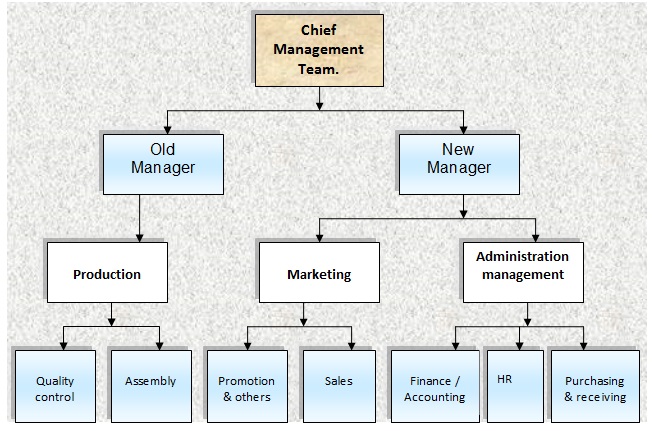
The old manager will control only production and other related departments as he has maintained a good relationship with the factory floor employees (mainly old operators and engineers) and he has no interest on other departments; in this condition, he must try to ensure the quality of the products by developing the efficiency level of the employees by giving the same task repeatedly. On the other hand, a new manager would control two departments (marketing and administration management) and these departments have also sub-departments like HR, sales, finance, promotions and so on; however, the managers must contact CMT at any time when they need to take major decisions.
Organisational Culture
Reiman and Oedewald (2002) mentioned that during the eighties, the business communities were deeply concerned with corporate climate, and at the end of eighties, it has turned into the organisational culture. There is no single recognised definition of any of the two terms corporate climate and organisational culture, but from practice, it has generally accepted that they indicate organisation’s values or the operating philosophy of an organisation. Schein (2004) defined organisational culture is a framework of the shared presumption that the members of an organisation put into practice to resolve its concurrent problems and achieve the long-term vision in a correct way and the new members are trained to feel, think and practice in the same direction.
Reiman and Oedewald (2002) pointed out that in the modern corporate world; organisational culture has to consider the external adaptations and their internal integrations as a learned consequence of group experiences that each of the member encounter in their regular practice. Schein (2004) explored that the organisational culture has three-layer attributes demonstrated in the following diagram –
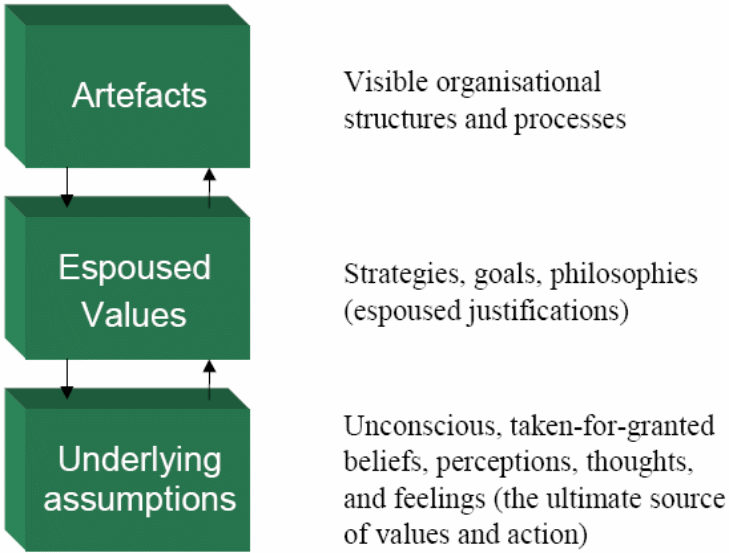
The above figure demonstrates that organisational culture has three-level clusters that balance the culture to explore and progress in each layer. At the first layer ‘Artefact’, culture represents the detectable organisational course of action along with various works of art, for instance, dress codes of the organisation, its common carefulness at the workplace and standard behavioural norms that the organisation emphasis. The first layer of culture also integrates individual performance recording system for their success factors, the correctness of interpretation, corresponding indicators, sickness leave, and accidental statistics along with information system concerned with safety, monitoring, and control as an internal dynamics of organisational culture (Adhikari 2010).
Schein (2004) added that at the second layer ‘Exposed Values’ of culture would integrate the organisational values that the organisation upholds for its operation, for instance, its official objectives, and affirmed customs, along with operating philosophy. Although the advocated values those are exposed may not always reflect it on regular operational standards, but it is the most significant concern of the organisational culture.
The third layer of organisational culture is ‘Underlying Assumptions’, which communicates with the learning method of problem-solving complexities, how the group members would deal with external adaptations along with internal integrations in their regular practice. The group members necessitate carrying on their skills to communicate with the dilemmas of external adoption to assess and identifying the solution to bring success over the complicated situation. At the same time, dilemmas of internal integration concerned with common conception development, essential group limits, relationship with authorities, internal interactions, along with reward and punishment process that the organisation put into practice as an internal dynamics of culture.
Organisational Culture and Information Systems
As the manager of ABC Company, first of all, it is essential to investigate how information systems (IS) integration would be proficient for cultural change of the organisation that would assist ABC to achieve its desired goal for sure success. The manager would urge for modernisation programmes for ABCC connecting with technological rationalisation as well as the modification would aim to construct the organisation further approachable to the up-to-date customers demand both at home and abroad. As a new manager, I have gone through the history of the company. There is no evidence on the implication of IS. Thus, I urge to have an immediate design and development information system for ABCC with the aim to assist the improvement of the manufacturing effectiveness connecting with the change of its organisational culture.
From the managerial views, the apparent needs for the cultural change of ABCC linked with the application of sophisticated information technologies for all-encompassing departments from the top management to the lower-level employees. The suggestive system would be designed to support ABCC to shift from the traditional method of record keeping to the Enterprise Resource Planning (ERP) software integration customised with the needs of modern CNC centres. The new system would integrate a complete structural flow starting from the employee’s attendance, performance, orders entry, all sorts of payment, manufacturing, and delivery including Customer Relationship Management (CRM) and Supply Chain Management (SCM) as a single process (McGrath 2003).
The system would potentially contribute the ABCC to observe the entire process from production to delivery and allow the management to control and monitoring the different checkpoints from a single platform without any hard effort, but just a few clicks of the mouse. It is predicted that the expected outcomes from the new information system would support the company to manage its inventory, production, HRM, marketing, sales and accounts schedule the work process with a dynamic way that ensures the company for the right use of resources that may deserve a change in the organisational culture. As the new manager, I would suggest the company integrating SAP for ERP software that would provide a higher degree of integrity ABCC.
The modernisation programme of ABCC would require cultural change that IS integration has regarded mostly in terms of attaining the target of performance that the modernisation scheme has inspired, although; the organisational alterations are uneven somewhere else. The organisational culture of ABCC, which prolonged to the manual practice of scheduling, planning, and management would require to come out immediately and to accept the digital process of organisational culture, and it would necessitate to conducting a training program for employees motivation. Here, the role of leadership is very crucial to explore how the IS implication would attempt to bring organisational cultural change as part of new technology integration and would acceptable to all levels of the organisation.
Skills; training and development as well as an appraisal
The employees of this company cannot represent their problems to the leaders due to having serious communication gap or lake of information about the concerned person to mitigate the situation; so, about twenty per cent employees are performing much below standard. However, there are some industries where communication is considered one of the most important factors, for instance, miscommunication or misunderstanding of a few words can have a deadly consequence or cause serious disaster in the aviation industry (Robbins & Judge 2008, p.367).
In addition, communication has four important tasks within the company, such as control, motivation, emotional expression, and information (Gilley, Gilley & McMillan 2009; Bolden, Gosling & Marturano 2003 and Solomon, Bamossy & Askegaard 2001). However, communication takes place in various forms including verbal (words, either spoken or written) and Non-verbal (Visual, Aural or Gestural) those essential to use consistent with the circumstances to deliver the message and convey the information (Gilley, Gilley & McMillan 2009, p.3; and Bolden, Gosling & Marturano 2003). At the same time, leading change needs the implementation of various set of communication methods to inspire the workers to make flexible the decision-making process to achieve the objectives (Gilley, Gilley & McMillan 2009, p.3; and Bolden, Gosling & Marturano 2003).
In addition, old managers had a good relationship with the factory floor employees, which gives the opportunity to members of this department to share their views, but it was difficult for all other members to convey their feedback, inform market-related issues and take proper guideline from the old manager. This communication gap is one of the most substantial causes of decreasing performance standard, failing to use the equipment and dropping profit margin of the ABC Manufacturing Company.
As a manager, I suggest the chief management team of this company to consider, the following stem to motivate the employee, for instance –
- Participative management: Employees would share their view with immediate superior, would be considered at the time of decision-making;
- Rewarding employees: the management should restructure remuneration policy to encourage their performance, for instance, it should provide merit-based payment and provide rewards for specific and outstanding performance;
- Downsizing: Some employees are not skilled and qualified to operate or work in a new CNC centre. So, the company should follow the strategy of downsizing new give the opportunity to the managers to recruit qualified candidates, which will help the managers motivate them easily;
- Teamwork: in addition, the managers should follow Belbin’s Theory to develop a team and set up their responsibilities
In addition, form the assessment of the performance of new employees of ABC Manufacturing Company, it is clear that the management should arrange development program and appraisal plan to ensure the right behaviour and performance of store operators, engineers and other human resources, for instance –
- Development requirements should be different in nature for the different workers, but everyone required behavioural training to develop a good organisational culture. In the given case study, the young employees require training on skills and old staffs need training on behaviour development so far they can give their highest efforts to develop performance;
- From the motivational perspective, every employee of ABC Manufacturing Company required the motivational program for all the employees as they have lack of confidence;
- An outstanding performance appraisal program should undertake for the workforce in ABC Company like 360-degree evaluation method and for young employees require to using the behavioural rating scale method.
Performance and motivation
According to the case study, this company has almost no workers qualified to operate or work in new CNC centre and 20% employees performed below standard level; so, the managers need to motivate them with proper training –
- Hierarchy of Needs Theory: Abraham Maslow defined this hypothesis and concentrated on the importance of motivation to get proper outcomes from the employees; therefore, he considered five levels of needs of the employees to fulfil the demands, for instance –
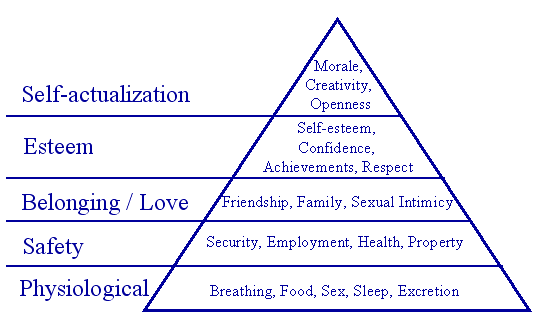
- Equity Theory: It based on the assumption that employees want to treat fairly in relationship to others and inequality arises when employees believe that the inputs (labour, training, and efforts) and outcomes (salary, benefit, and bonus) of particular employees is less than the other employees;
- Motivation-hygiene theory of Herzberg: Herzberg (2003) provided this hypothesis to identify what does the workforce want from their jobs and he interviewed 200 respondents to measure when they felt good or bad to measure job satisfaction.
Future directions (20 per cent)
Change management plan
Under the existing scenario of ABC Manufacturing Company, there are 96 employees consist of two managers, four maintenance engineer, ten qualified refurbishment engineers, eighty operators with 20% below standard performance level without enough workload that has failed to utilise full production capacity. Moreover, lack of coordination, leadership, job clarification, absence of good remuneration and promotion plan along with the high rate of employees’ turnover has seriously distressed the company’s growth. Thus, HRM planning, leadership, development and training is very crucial for the company to overcome the excising dilemmas.
The core essence of HRM planning is to reduce the production cost, reduce a high rate of employees turnover and maximise profitability. To implement such policy, shifting all heavy production in Bangladesh would reduce at five times less than the UK production cost while there is very fewer employees turnover rate. The UK production site would only handle with small and urgent orders with rework and after-sales service a small number of staff with a high payment that ensure employees retention. The headquarters would integrate all orders through B2B platform while the online marketing service would be outsourced from Bangladeshi IT companies. To bring mobility and dynamism within the company, it is essential to employ a competent general manager, two factory manager for two production sites along with a marketing manager and financial manager. All four managers would be authorised to restructure their own department and conduct necessary training.
Organisational Development
Although the global financial crisis has seriously distressed the volume of capital machinery market, the demand for CNC products has been growing tremendously from the introduction of computerised numerical control. Although CNC products have an ever-increasing demand and higher profit margin, it is no longer advantageous to produce in the countries with a high cost of labour and to sustain huge profitability number of companies are shifting their production facilities to the countries where labour cost is lower. On the other hand, to address the global demand for CNC products, numerous CNC machining centres already established several production facilities in many countries other than the home country. As the works of CNC machining centres involved entail coping with numeric programming specifications, it is very crucial to organise composite manufacturing model with most up-to-date facilities along with skill human resources familiar with the systems of CNC and relevant software (Nassehi et al. 2006).
From the above highlights of the prospect of CNC machining centres, it is clear that the operation of ABC Manufacturing Company in the UK market has to face hard constrain to maximise its profit margin with the high-level of labour cost. As the company has 25 years operation in the UK market, it has a more or less satisfied customer base with a traditional supply chain which further modification. It has also demonstrated in the case study that the company could not handle all orders that it gets, rather it performs very selective orders. At the same time, it has fixed up the target of 10% return on the UK £ 10 million investment within next four years, while the UK CNC products market is under serious pressure from Chinese and Indian competitors. Thus, the company has emergence to shift one of its newly purchased CNC centres to a country with low labour cost and to renovate another one in the UK for revision, rework and after-sales service including emergency services to customers.
To set up production facilities other than the home country, it would suggest that Bangladesh is a country with high population density, low labour cost, tax-free zones and port facilities and a large number of IT graduates with CAD, CAM, CAE, PLM, and other prototype development software. There are also shaded areas available in the export processing zones for rental to the foreign investors, with gas electricity and water supply and it would save time for infrastructural development, with this arrangement the company could just ship it newly purchased CNC centre in Bangladesh and start operation with fewer efforts.
The estimated investment to set up the production facility in Bangladesh would involve £3.75 million. The renovation of production facilities in the UK with numeric control (NC), staff training, leadership development, B2B development along with management change would be covered with £1.25 million considering the total budget of £5 million for investment and change management. There is also another cost involved for the company for some of the old employees would to for retirement and their pension and other costs would be covered by running income.
Recommendations
Outsourcing from Emerging Asian Market
To setting up production facilities other than home country and recruiting competent candidates, it would take at least one year or more. As the company is under pressure to return the UK £ 10 million, it would be more effective to take orders for all short of products from the local market and manufacture them from Asian emerging countries like China India or Bangladesh. For the interim period, through outsourced manufacturing, the company would be able to retain its customers until the new production facility would start production and the production facilities in the home country would be renovated.
B2B Ecommerce Integration
As part of materialisation, it is essential for the company to integrate B2B platform by which the customers could place their order online, upload their required specification, and get an uninterrupted scope of communication with the engineering department. The online presence of the company would also facilitate online marketing along with supply chain management that would assist the company to turn into a global player in the international CNC machining industry.
Product line Diversification
Due to its internal lacking of management, it has demonstrated from the recent studies that the company has involved 45% of its capacity for low-grade, less profitable large quantities shafts manufacturing, 20% orders are single batch metal processing, only 15% wide variety precious small orders, 10% repairing, casting and injection moulds and rest 10% automobile supplies.
As the company would settle new production facilities in Bangladesh and renovate its all-traditional machines in the UK site with numerical control (NC), the company would get an extended opportunity to diversify its product line with moulds and tools for aerospace industry, machining composite for plastic, tools marine industry, timber processing industry, water-jet cutting for wind energy and so on. Such product diversification would automatically boots is annual revenue extremely higher than ever.
Conclusion
Although the provided company has a great prospect in the UK CNC machining industry, it suffered from low revenue generation and lower profitability due to lack of management coordination, unutilised capabilities and misuse of resources. Change in management, shifting heavy production facilities in low labour cost country, integration of B2B e-commerce platform, product diversification and dynamic leadership would assist the company in overcoming the crisis and can turn it into an excellent CNC machining centre in the global context.
Reference List
Adhikari, B. R 2010, Computerized Information System for Small Manufacturing Company. Web.
Bolden, R. Gosling, J & Marturano, A 2003, A Review of Leadership Theory and Competency Frameworks. Web.
Booth, E. M 1996, Starting with Behaviour. Web.
Cherry, K. 2012, Lewin’s Leadership Styles. Web.
Gilley, A. Gilley, J & McMillan, S. H 2009, ‘Organizational Change: Motivation, Communication, and Leadership Effectiveness’, International Society for Performance Improvement, vol.2 1 No.4, Web.
Hellriegel, D. Slocum, J.W & Woodman, R.W 2002, Organisational Behaviour, Thomson Learning, South-Western.
Herzberg, F 2003, ‘One more time: How do you motivate employees?’, Harvard Business Review. Web.
Hitt, M. A., Ireland, R. D., & Hoskisson, R. E. 2001, Strategic Management, Thomson Learning, South-Western.
Holman, P., Devane, T., & Cady, S. 2012, Change Methods: Seven Basic Characteristics. Web.
Johnson, G., Seholes, K., & Whittington, R. 2006, Exploring Corporate Strategy: Text & Cases, FT Prentrice Hall, London.
Katzenbach, J. R. & Douglas, S. 2000, The Wisdom of Teams: Creating the High-Performance Organization, Harperbusiness, London.
Kotler, P. & Armstrong, G. 2006, Principles of Marketing, Prentice-Hall of India Private Limited, New Delhi.
Lewin, K. Lippit, R. & White, R. K 1939, ‘Patterns of aggressive behaviour in experimentally created social climates’, Journal of Social Psychology, vol. 10 no. 2, p.271.
McGrath, K. M 2003, Organisational Culture and Information Systems Implementation: A Critical Perspective. Web.
Mellahi, K. & Wilkinson, A. 2012, Slash and Burn or nip and tuck? Downsizing, Innovation and Human Resources. Web.
Nader, R 2012, Leadership and Motivation. Web.
Nassehi, A. Newman, S.T. & Allen, R.D 2006, Step-NC compliant process planning as an enabler for adaptive global manufacturing. Web.
Orlikowski, W. J 1995, Improvising Organizational Transformation Over Time: A Situated Change Perspective. Web.
Pearce, J. A. & Robinson, R. B 2006, Strategic Management, McGraw-Hill, London.
Pitt, D. C 2001, ‘Leadership and Motivation: The Effective Application of Expectancy Theory’, Journal of Managerial Issues, vol. XIII no. 2. Web.
Reiman, T. & Oedewald, P 2002, The assessment of organisational culture A methodological study. Web.
Robbins, S. P. & Coulter, M 2008, Management 3e, Prentice Hall, London.
Robbins, S. P. & Judge, A. T 2008, Essentials of Organizational Behaviour, Pearson Prentice Hall, London.
Rowstrom, J. W 2011, Organizational Behaviour: Human Behaviour at Work, The McGraw-Hill Companies, London.
Schein, E.H 2004, Organizational Culture and Leadership, Jossey-Bass, San Francisco.
Solomon, M. R., Bamossy, G., & Askegaard, S. 2001, Consumer Behaviour, Prentice Hall, London.
Weihrich, H. & Koontz H 2005, Management a Global Perspective, Tata McGraw-Hill, New Delhi.