The past few decades have witnessed a major re-organization in the engineering field. New technological advancements have changed the scope of work and practice in various engineering fields, especially in Design Technology. But perhaps no technology has rejuvenated the field of Design Technology more than the introduction of Computer Aided Design (CAD). The technology has found wide acceptance and usage in Design Technology’s fields of Fashion design, Architecture engineering and construction, Mechanical engineering (Automotive, Aerospace, Consumer goods, Machinery, and Ship building), Electronic and electrical engineering, Civil engineering, and Manufacturing process planning (Chaszar, 2006; Daynes, 2008). This paper aims at comparing and contrasting the different fields in Design Technology, detailing how AutoCAD plays a role in each of the field.
According to Voisenet (2001), Computer Aided Design (CAD) basically entails the use of a variety of computer-based tools to help architects, design professionals, and other engineers in their design activities. Design is a primary component in nearly all engineering fields, and therefore CAD comes in handy as the main geometry authoring tool in designing a product of any magnitude. In many instances, CAD involves both special purpose hardware as well as software. According to Chaszar (2006), CAD entails the use of cutting edge computer technology to assist in the design process, particularly in engineering and technical drawing, otherwise referred to as drafting. It is both a visual and symbol-oriented method of communication whose limitations are specific to a particular technical field. All engineering fields comprise a component of drafting, and that’s where the CAD technology proves important. Subsequently, AutoCAD is a full-fledged CAD based program that can be used on most Macs, UNIX, and PCs workstations, and have numerous features that serve to make it more functional than its predecessors (Buehrens, 2004). It was originally developed in the early 1980’s for CP/M machines (Raymond, 2005).
To stakeholders in Design Technology, drafting often comes in two methodologies; two-dimensional (“2D”) and three-dimensional (“3D”). Accordingly, drafting can be defined as the fundamental communication of engineering or technical drawings, and is the “industrial arts sub-discipline” that inspires all technical undertakings (Wedding & Probert, 2008). CAD is often deciphered as Computer aided or computer assisted drafting. Various acronyms have been coined in reference to CAD in the various engineering fields it affects. For example, in Architecture, the technology is known as Computer Aided Architectural Design (CAAD), while in Industrial Design, it is known as Computer Aided Industrial Design (CAID) (McKissick, 2007; Daynes, 2008). Both systems are essentially synonymous though there exist some delicate differences
To understand how the CAD technology affects various engineering fields in Design Technology, it is imperative to talk about the current CAD software packages found in the market. There is a diversity of CAD computer packages found in the market today ranging from 2D vector-based drafting instruments to 3D surface and solid modelers (Chaszar, 2006). According to Wedding and Probert (2008), modern CAD systems have the capability of frequently allowing rotations in 3D, facilitating the viewing of an ongoing design work from any preferred angle. CAD is utilized in the design of machinery and apparatus used by engineers in drafting and designing of all types of structures, from the smallest residential structures to the largest industrial and commercial facilities. It is also used in manufacturing structures used in engineering works. It is particularly helpful in designing comprehensive 2D drawings of physical structures and 3D models (Callicott, 2001).
As already mentioned elsewhere, AutoCAD or CAD technology has contributed to the marked growth of Design Technology in fields of Architecture, Civil, Mechanical, and Manufacturing engineering. CAD technology has been extensively used in these fields to design and develop goods and products that may be used by end consumers or in the manufacture of other essential products (Chaszar, 2006; Raymond, 2005). In the engineering technology, CAD is overwhelmingly used from the conceptual layout and design, through a comprehensive engineering and analysis of constituents, to the definition of the various manufacturing methods used (Buehrens, 2004). Within the scope of Computer Aided Technologies (CAT), CAD has become an important constituent, benefiting users through shortened product design and low product development costs. Engineering work can now developed on a computer screen, printed and saved it for future editing, thereby saving a lot of time. Below, this paper attempts to look at the specific roles that the technology has played in each of the mentioned fields, while drawing heavily on their differences and similarities.
Computer Aided Design in Architecture
Architecture, originally a Greek word, can be used to relate to a process, documentation, and a profession. Architecture is used as a process to refer to any action of designing and constructing physical structures and buildings by individuals and machines aimed at providing some socially purposeful shelter (Callicott, 2001). Broadly put, Architecture entails the practice of designing a structure from the macro level consisting of how the structure integrates to the surrounding landscapes, to the micro level of construction and architectural details. Architecture has also been used to document drawings used to define the structure and behavior of any kind of system that is in the process of construction, or has already been constructed (Chaszer, 2006; Daynes, 2008).
According to Buehrens (2004), the AutoCAD technology has professionally being used by Architects to draft engineering and architectural drawings, as well as to make technical illustrations of any kind in the process of developing a building or any other structure. It has enabled them to design accurate and fast drawings, which can be changed to fit various needs with minimal effort. This functionality offers the engineers the much needed flexibility to change drawing designs with ease. To Architectures, CAD technology offers a graphically-based medium which can effectively be used to develop concept sketches that can be assessed and approved to become working drawings (Voisenet, 2001). For example, Architects are known to use the structural design package in CAD to evaluate the integrity or suitability of a steel-framed structure or building through executing all the calculations needed to establish the strength and size of the components, and the consequences of things such as wind-loading that may affect the building at a later stage. Through the technology, architects can be able to schedule for needed materials, and come up with essential sketches that can later be reassigned to a Computer Aided Drafting software package for ultimate development of the working drawings that will be used to construct the building (Callicott, 2001).
To be able to perform such roles, architects can now use design software packages readily available in the market such as AutoCAD Architecture 2009. This software enables Architects to create and share construction drawings more efficiently through the use of the software’s intuitive architectural design and drawing tools (Callicott, 2001). This has often brought instantaneous productivity benefits for professionals in the field. In Architecture, AutoCAD is also used in the Drafting process, otherwise known as the definite technical drawing module of the architectural project (Chaszar, 2006). Rather than using the traditional drawing board, the technical drawing is developed using a computer, thereby simplifying the whole process and saving time. Input into the technical drawing component of the Architectural design process comes from graphical images such as photos and maps, pre-existing component drawings, complex calculation packages, and hand-drawn sketches created by the architect. What’s more, Architects have been able to utilize the AutoCAD software package to bond all the pertinent constituents together to create specifications and drawings that can then be utilized to determine the initial cost of the Architectural project, estimate quantities of materials to be used, and ultimately provide some comprehensive drawings that can be used in the building construction (Voisenet, 2001).
Architecture is aptly related to other engineering fields such as civil and mechanical engineering. In this context, AutoCAD is used across the board. An Architect can perform Civil Engineering roles such as roads, drainage, and grading design, site design, mapping and cartography using the AutoCAD software applications.
Computer Aided Design in Mechanical Engineering
According to Voisenet (2001), the discipline of Mechanical Engineering entails the application of the doctrines of physics for the design, analysis, manufacturing and maintenance of mechanical structures. Engineers in the field use the core principles of physics to design and analyze heating and cooling systems, motor vehicles, watercraft, aircraft, industrial equipment and machinery, manufacturing plants, medical devices, robotics, and many more. Just like Architecture, Mechanical Engineering utilizes AutoCAD technology in its drafting, design and manufacturing processes. Mechanical engineers utilize drafting or technical drawing just like architects to develop instructions for the process of manufacturing components (Buehrens, 2004). In many countries, a drafter or draftsman is the name given to a mechanical engineer who develops a technical drawing. In essence, a draftsman can create a two or three dimensional computer schematic showing all the proportions essential for the manufacture of a component, a list of requisite materials, assembly notes, as well as other applicable information using CAD programs. To this extent, AutoCAD can be evaluated as an effective tool in both Architecture and Mechanical Engineering as far as creation of working drafts, technical drawings, and project budgetary allocation are concerned.
By comparison, Computer Aided Drafting is used in almost every sub-discipline of Mechanical engineering. It has enabled the creation of three dimensional models commonly referred to as Computational Fluid Dynamics (CFD) and Finite Element Analysis (FEA) through the use of various CAD software packages (Callicott, 2001). It should be noted that technical instructions for the manufacture of a component must be fed to the required Computer Aided Manufacturing (CAM) or CAD software package. With the advent of Computer Numerically Controlled Manufacturing (CNCM), Mechanical engineers can now be able to do more in the field. Mechanical engineers can now effectively draft, design, plan, and develop equipments and machines ranging from minute instruments used in surgery and medicine to jet engines using various CAD applications (Chaszer, 2006).
Within Mechanical engineering firms, CAD technology can be used in numerous other ways apart from the ones mentioned above. It can be used to create Mechanical engineering drawings using a two dimensional Wire-frame package. A Draftsman can also use three dimensional Parametric Feature-based modeling technologies such as Solid Modeling or Freeform Surface Modeling, or a combination of the two to come up with design components for a mechanical engineering job (Callicott, 2001). Individual components or parts can then be uniquely assembled using a comprehensive 3D illustration to represent the final product, a process known as Bottom-up design. The computer aided assembly models can therefore be used to conduct a deep analysis to evaluate if the parts can fit together if assembled as well as imitating the dynamics and working relationships of the finished product (Voisenet, 2001). Through the use of AutoCAD technology in mechanical engineering, a Finite Element Analysis (FEA) can be conducted on the assemblies and components to assess their strength and durability in real life situations.
Technological advancements in the last few years have enabled a Top-down design to be performed within the field of mechanical engineering using CAD applications. In this process, draftsmen and mechanical engineers are able to subdivide a product using its layout diagram and come up with a detailed account of the subsystems that make up the product at the individual component level (McKissick, 2007). Through using the system, a detailed design of the individual parts that are needed in creating the product is analyzed before assembling the final product. Mechanical Engineering therefore utilizes Computer Aided Engineering (CAE), Computer Aided Design (CAD) and Computer Aided Manufacturing (CAM) for its products and machine elements. Mechanical engineers rely heavily on various CAD applications such as SolidWorks and COSMOSWorks to draw, design, and optimize complex mechanical components, minimizing costs, complexity, and mass, and at the same time ensuring the displacement and strength requirements of finished products (Chaszar, 2006). Below is a visualization of a Delta Robot.
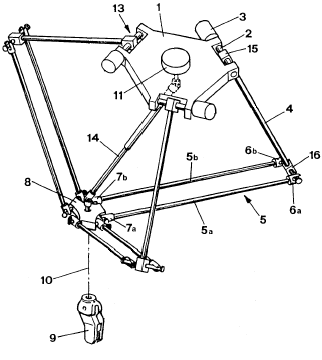
Computer Aided Design and Manufacturing
The field of computer Aided Manufacturing (CAM) is fast gaining a strong foothold in Design Technology. Simply put, machinists and engineers are increasingly using computer-based software packages to manufacture or prototype product parts or components (Callicott, 2001). To this effect, engineers are utilizing CAM as a programming tool that allows them to manufacture or create physical models using CAD software packages. CAM was first used in 1971 for vehicle body design and tooling, and it’s credited with creating real life versions of various body parts within a computer software package. CAM is perceived traditionally as an NC programming facility which utilizes the three dimensional models of the parts created by CAD software to develop a CNC code that is used to drive numerically restricted machine tools (Voisenet, 2001). Just like in Architecture and Mechanical Engineering, CAM must utilize skilled professionals such as NC programmers and Manufacturing Engineers.
CAM basically involves the use of computers in the conversion of engineering designs into finished items. It has a distinct similarity with other CAD applications in Architecture and Mechanical Engineering in that the production process must require the development of production schedules and process plans that must explain how the product will be developed, how resources will be utilized, the costs of the resources, when and where these resources will be positioned, and the coordination and control of the requisite physical procedures, materials, equipment, and labor (McKissick, 2007). CAM assist manufacturing engineers, managers, and other production workers in the automation of many production chores in the same way CAD applications assist engineers in drafting and technical drawing in Architecture and Mechanical Engineering. It has enabled the manufacturing process in monitoring production schedules, creation of process plans, and in ordering and tracking materials. Other CAD applications perform these functions in fields of Architecture, Mechanical, and Civil Engineering. CAM is however used in manufacturing to control industrial robots, machines, test equipments, and other systems that are used to move and store materials in industrial factories (Buehrens, 2004).
In CAM, computers are synchronized to communicate some fed work instructions directly into the manufacturing machines. The technology behind CAM arose out of the 1950’s numerically controlled machines which received instructions from a set of codified briefings put in a punched paper tape (Voisenet, 2001). In modern times, a single computer fitted with the desired CAM software can manage banks of lathes, robotic milling machines, welding tools, and other machinery used to move the product from one machine facility to another so as to complete the steps involved in the manufacturing processes. Just like in other CAD programs used in Civil, Architecture, and Mechanical Engineering, CAM permits a fast integration of design changes in a product, in the process allowing a fast and easy reprogramming from the computer (Callicott, 2001). In factories with complex CAD systems, the technology can take care of such activities as scheduling, ordering, and tool replacement.
CAM software application can be used to improve profitability, product quality, and productivity in the manufacturing process the same way that CAD applications are used in engineering fields of Architecture, Civil, and Mechanical, (Chaszar, 2006). It has been effective in curtailing waste, inventories, scrap, and waste; eradicating redundant designs and production tasks; increasing the utilization of equipments; improving the efficiency of workers; improving the ability of industrial factories to design and produce various products; and aptly in decreasing the time needed to design and develop products.
In essence, the mere fact that CAM, CAE, and CAD work harmoniously together has led to the collapse of many past barriers between manufacturing and functional units (Voisenet, 2001). Computer Integrated Manufacturing (CIM) also aims at creating and maintaining a database on the industry-wide computer network that can effectively be used for designing, analyzing, optimizing, production scheduling, process planning, materials handling, robot programming, maintenance, inventory control, and marketing. Indeed, CIM appears to be the way to go for CAD/CAM (Chaszer, 2006).
Computer Aided Design and Civil engineering
According to Callicott (2001), Civil Engineering entails designing and construction of buildings, airports, roads, dams, tunnels, water supply, sewer lines and other core facilities. Specifically speaking, it is a professional discipline involving itself with the design, construction, and maintenance of the naturally built and physical environments. In the process of constructing these amenities, Civil engineers must make sure that the structures they come up with will remain intact. They also involve themselves with the initial costing of the amenities. These roles have been successfully taken up by CAD software packages such as Computer Aided Engineering (CAE). In fact there has been no clear dissimilarity between Architecture and Civil engineering until recently.
Just like in other engineering fields, civil engineering has benefited immensely from technological advancements, especially in CAD applications. Civil Engineers effectively use CAD applications to develop and share construction drawings more efficiently through the use of the software’s intuitive civil engineering design and drawing apparatus (Voisenet, 2001). Such tools have effectively been used by civil engineers to draft civil structures such as railroads, bridges, and roads. Rather than using the traditional drawing board, the technical drawings are developed using a computer, thereby simplifying the whole process and saving time. Just like in Architecture and Mechanical engineering, the input into the technical drawing component in the Civil engineering Design process may come from graphical images such as photos and maps, pre-existing component drawings, dedicated calculation packages, or merely from hand-drawn sketches created by the Civil engineer (Callicott, 2001). The engineers have also been able to utilize the AutoCAD software package to bond all the pertinent constituents together and create specifications and drawings that can then be utilized to determine the initial cost of the Civil Engineering project, estimate materials to be used, and ultimately provide some comprehensive drawings that can be used in the construction of the amenities (Buehrens, 2004). In the same vein, CAD applications in civil engineering have been credited with improving profitability, product quality, and productivity just like CAM does in the manufacturing process.
In conclusion, this paper has ably looked at the different fields of Design Technology in relation to the use of CAD applications, detailing the similarities and differences that exist in all of them. What comes through is that CAD applications in the engineering fields have really rejuvenated the scope of work and practice in these fields. The technology have been credited with helping to design fast and accurate drawings, determine the initial cost of the projects or products, estimate the quantities of materials to be used, and develop instructions for the process of manufacturing components and parts. AutoCAD applications have also been credited with eradicating redundant designs, improving the efficiency of workers, and increasing the utilization of equipments especially in Manufacturing, Architecture, and Mechanical Engineering disciplines.
References
- Buehrens, Carol. (2004). DataCAD for Architects and Designers. London: Oxford University Press
- Chaszar, Andre’. (2006). Blurring the Lines: Computer Aided Design and Manufacturing in Contemporary Architecture. Prentice Hall. ISBN: 978-0-470-86849-2
- Callicott, Nick. (2001). Computer-Aided Manufacture In Architecture – The Pursuit of Novelty. Architectural Press. ISBN: -10: 0750646470
- Daynes, P. (2008). Using 3D CAD to optimize plant Design.
- McKissick, Michael Landon. (2007). Computer-Aided Drafting and Design. Prentice Hall.
- Raymond, Landoni. (2005). “Maximum Mobility: CAD options for windows CE Devices” Cadalyst, vol. 22, no. 7, pp. 20-21.
- Voisenet, Donald, D. (2001). Computer Aided Drafting and Design: Concepts and Applications. London: Routledge.