Abstract
Different types of cement should be used for different construction specifications. Portland cement refers to the commonly used types of cement. The cement reacts with water in a process known as hydration. Hydration may take a longer time depending on the amount of tricalcium silicate or dicalcium silicate found in the final product. Tricalcium silicate, dicalcium silicate, and tetra calcium alumina-ferrite are the main compounds at the end of the kiln. Tricalcium silicate takes a shorter time to hydrate and gain strength. It also evolves a lot of heat. Dicalcium silicate reaction takes a longer period to gain strength. It may take about a year to gain significant strength. The types of cement are based on the amount of tricalcium silicate, dicalcium silicate, and tricalcium aluminate found in the end product. Tricalcium silicate starts to gain strength a few hours after being laid. Dicalcium silicate starts to gain strength after 28 days. Low levels of tricalcium aluminate prevent reaction with sulfate ions.
Introduction
Portland cement is manufactured through a dry process and a wet process. The chemical reaction in the kiln starts with the breaking down of calcium carbonate into calcium oxide and carbon dioxide using heat. The second stage is a chemical process that results in the formation of dicalcium silicate. In the third stage, dicalcium silicate reacts with calcium oxide, ferrous oxide, and aluminum oxide to form tricalcium silicate and tetra calcium alumina-ferrite. Cooling follows after the kiln. A small percentage of gypsum is added to the two compounds before the mixture is ground into fine powder to increase the hydration rate. The cement reacts with water in a process known as hydration. Hydration may take a longer time depending on the amount of tricalcium silicate or dicalcium silicate found in the final product. The types of cement depend on the amount of tricalcium silicate, dicalcium silicate, and low tricalcium aluminate constituents. They give early strength, low heat generation, and sulfate resistance respectively.
Cement production
Cement is produced from raw materials collected from limestone (calcium carbonate) and clay (aluminum silicate). The raw materials also contain other impurities and must be checked to ensure that they do not exceed acceptable levels.
The limiting percentage of various oxides found in raw materials

Calcium oxide forms the major chemical component of the raw materials used in cement production.
Portland cement is manufactured through two methods known as the wet method and the dry method. In the dry method, the raw materials are dried after they have been crushed. They are put in the kiln after drying. In the wet process, water is used to pulverize the mixture. It is put in the kiln when still wet and drying occurs in the initial stages of the kiln (Ghosh, 2003). A common kiln has a length of 60 meters for the dry process, and 100 meters for the wet process (Wansbrough, n.d.).
In the kiln
The raw materials are heated in the kiln at high temperatures up to 14500C when the contents contain ferrous oxide. It is heated above 15000C without ferrous oxide (Ghosh, 2003). When the raw materials are heated, they form 3CaO.SiO2 (tricalcium silicate), 2CaO.SiO2 (dicalcium silicate), 3CaO.Al2O3 (tricalcium aluminate) and 4CaO.Al2O3.Fe2O3 (tetra calcium alumina-ferrate) (Wansbrough, n.d.).
In the first phase, calcium carbonate is heated at temperatures between 8000C and 11000C for about 35 minutes to give out calcium oxide and carbon dioxide (Wansbrough, n.d.).
In the second phase, the calcium oxide reacts with silicon dioxide to form dicalcium silicate. The mixture is heated at 11000-13000C between the 35th minute and the 40th minute of the heating stage (Wansbrough, n.d.).
In the third phase, temperatures are between 13000C and 14500C. It occurs between the 40th and 50th minutes in the kiln. Dicalcium silicate reacts with calcium oxide to form tricalcium silicate. It occurs during the sintering process. The sintering process refers to the melted mixture. Part of the tricalcium silicate reacts with ferrous oxide and calcium oxide to form tetra calcium alumina-ferrite compound (Wansbrough, n.d.).
The fourth stage occurs between the 50th and 60th minutes. It involves cooling and crystallization of the mixture that has formed in the kiln from 13000C to 10000C.
The mixture is moved from the kiln into a cooler. The cooler causes the temperature to drop from 10000C to 1500C. The mixture that comes out is known as clinker which reacts in the same way as cement when it comes into contact with water.
Pictorial presentation of the process
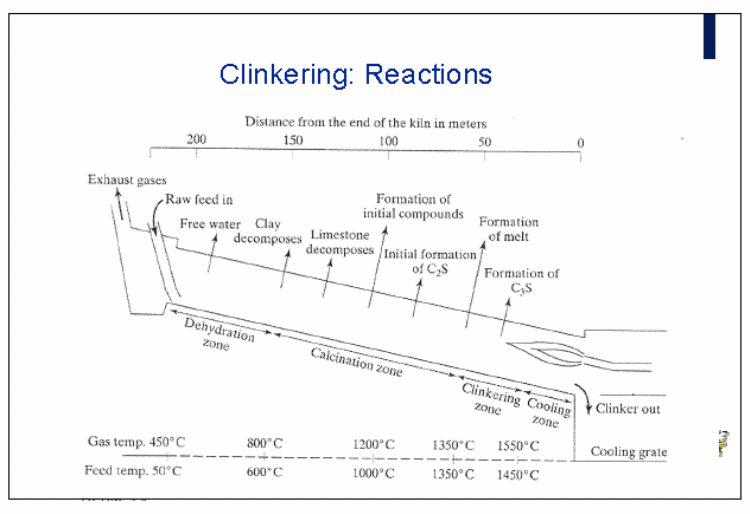
The clinker is formed of particles that are between 1cm and 3cm in diameter. Gypsum (CaSO4.H2O) is added to the mixture before milling. Gypsum is added to “prevent the flash set of cement” (Kurtis, n.d., p. 14). The clinker is ground into fine powder to increase the rate of hydration when water is added to the mixture.
Hydration process
The hydration process shows the chemical reaction that cement undergoes when it has been mixed with water during the formation of concrete. Tricalcium silicate forms the major part of Portland cement. It easily reacts with water particles with a moderate evolution of heat from the hydration process (Ghosh, 2003).
It can also be written as
in cement nomenclature (Ghosh, 2003, p. 31).
The formula is an approximation of the main component. The actual C-S-H formed has a longer chemical formula than the one provided in the equation. The main reason is that cement contains many minerals. The end product of the hydration process contains calcium silicate hydrate (also known as C-S-H) and calcium hydroxide (portlandite). Multiple types of C-S-H are formed through the hydration process. C-S-H is the main source of the hardness of cement during the early days (up to 7 days) after cement comes into contact with water particles (Ghosh, 2003). Hardness in the latter days is attributed to β-Dicalcium silicate which has a slow hydration process. The hydration for β-Dicalcium silicate starts after 28 days and may continue even after a year (Ghosh, 2003).
Types of cement and their application areas
Ordinary cement is found in specification C 150 and blended cement in specification C 595. In the types listed below, type I to V is C 150 standard. Types GU to HS, found in the bracket, is C 1157-08 standard group (Gambhir, 2009).
Type I (GU) Common Portland cement
It is used for general construction purposes where cement is unlikely to be mixed with soil or water after the cement has been laid.
Type II (MS) Modified Portland cement
It is a type that provides resistance to sulfate ions after the cement has settled. It is used for general construction purposes in areas where concrete may come into contact with materials that contain sulfate ions.
Type III (HE) High-early strength Portland cement
It is used when early strength is required. High early strength may result in a faster rate of construction. It is used when high strength is required between 1 and 3 days (Gambhir, 2009). It may be used in cold weather where solidifying water raises concern.
Type IV (LH) Low heat of hydration Portland cement
It is a type of cement with a high percentage of dicalcium silicate and tetra calcium alumina-ferrite. Their percentage ranges between 50% and 80%. It is composed of low levels of tricalcium silicate/ aluminate. It is used when low heat generation is required during cement settling. It is used in the construction of dams and retaining walls among other construction work with heavy concrete mass (Kreh, 2003).
Type V (HS) High sulfate resistant Portland cement
The cement has low levels of tricalcium aluminate (C3A) component. It is highly resistant to sulfate ions after the cement has settled (Gambhir, 2009). It is used in areas when cement is likely to come into contact with alkaline soil or groundwater. C3A usually reacts with sulfates to cause the expansion of settling cement (Kreh, 2003).
Types IA, IIA, and IIIA
These types are air-entraining types. They trap a small percentage of air during the hydration process at about 5% (Kreh, 2003). The cement is more resistant to freezing and melting of ice.
Findings and discussion
The different types of cement depend on the proportion of tricalcium silicate, dicalcium silicate, and tetracalcium alumina-ferrite content in the end product. Tricalcium silicate provides early strength which starts several hours after the cement has been laid. It also generates a lot of heat when settling. Dicalcium silicate starts to provide strength after 28 days. It is usually mixed with tricalcium silicate to reduce heat generation. Low levels of tricalcium aluminate reduce reaction with sulfate ions. Construction that involves molding a large mass of concrete should have low proportions of tricalcium silicate to reduce the amount of heat evolving during hydration.
Conclusion
Portland cement types should be chosen depending on the environment where the cement is to be laid, and the need for early strength in construction work. High heat generation caused by large proportions of tricalcium silicate may cause uneven expansion. It becomes necessary that it is mixed with dicalcium silicate to reduce heat generation. Construction works with large masses of concrete use dicalcium silicate of a large proportion to prevent heat generation. They also need to stay for longer periods such as a year before the building can be used.
References
Gambhir, M. (2009). Concrete technology: theory and practice (4th ed.). New Delhi, India: Tata McGraw Hill Education.
Ghosh, S. (2003). Advances in cement technology: Chemistry, manufacture and testing. New Delhi, India: Tech Books International.
Kreh, R. (2003). Masonry skills (5th ed.). Clifton Park, NY: Thomson/Delmar Learning.
Kurtis, K. (n.d.). Portland cement manufacture. Web.
Wansbrough, H. (n.d.). The manufacture of Portland cement. Web.