Introduction
Among the most renowned world architectural and engineering masterpieces is The Empire State Building (ESB). In spite of its massive nature, a 103-storey and 1453-foot monolith, the EBS was constructed in slightly over 13 months. It is also alleged that the company that carried out this daunting task had virtually nothing at hand in form of equipment and supplies necessary to venture into such an enormous project.
Successful execution of the project could only have been made possible because of the firm’s expertise in commercial constriction management. The era when this project was undertaken, when New York and Chicago were in cutthroat competition for the construction of the highest skyscrapers, was also quite significant.
Successful completion of this project, consequently, gave New York a competitive edge in the rivalry. For more than forty years, The Empire State Building remained the most prestigious and tallest building in the entire world. This position was only challenged when the World Trade Centre was completed in 1972.
The execution of the masterpiece that is The Empire State Building is credited to a leading firm of architects, Shreve, Lamb, and Harmon Associates. A steel frame was chosen by the architects as the primary construction technique. The only firm that had perfected the use of this technique, Starrett Brothers and Eken Incorporated, was given the contract to complete this project.
The size of the building demanded for the erection of 64 elevators that could be used to convey people and materials up and down the construction. Upon completion, the building was 1472 feet or 448 meters in height.
Though it had originally been proposed that the antennae would provide direction to docking ships, the proposal was later shelved when it was established that people would not be comfortable disembarking an airship tethered to the building, at over one thousand feet above. The building is estimated to have cost well over £40 million at the time of the great economic depression.
Some people felt that this building was undesirable and should not have been built in the first place. The rapid pace at which the project was executed would make it appear that the owners were in a rush to get rent from the available space.
The contractor used what was considered the most current technology of the time to construct The Empire State Building. A massive concrete base was used to lay the base in order to support the equally massive weight of the massive steel framework. The steel sections were prefabricated at the steel plant and conveyed to the construction site.
Care was taken to ensure the holes through which bolts, nuts and rivets were to be fitted accurately matched. It would take only three days to manufacture, transport, and position the steel frames into the entire framework of the building. An outer skin of stone was used as finishing on the already fixed steel framework and the entire structure.
The techniques used to join the steel work that finally went into the making of the building were rather complex. The sky boys, the name given to the laborers, would walk up and down as they put the structure together. Their task was to fix together the individual steel sections into a framework using bolts and nuts. Though the job was dangerous, none of the sky boys died in the course of the construction.
Hot rivets were also used as a joining technique. This technique had successfully been used in the ship building industry, and its choice in fixing large steel plates was therefore quite appropriate. After heating, the red hot steel rivets would be passed through the holes or other openings of the two sections. A unique rivet gun was used to shape the hot soft rivets and round the plain ends to permanently secure them in place.
A project of this magnitude has definite risks that could arise either in the course of its construction, or during its use. Whatever the level at which the risks arise, it is not in dispute that a number of people, sections of the building or the whole of it could be in danger.
This demands for the institution of an effective risk management program. A proper risk management program would assist management to identify, assess, prioritize the risks and come up with well-coordinated and cost effective methods of minimizing, monitoring, and controlling the impact of such risks, or maximumly realize the opportunities presented. Risk management can adequately be done using fault trees.
This is applicable to many major projects, including Empire State Building.
Risk management could easily be analyzed on the basis of what are referred to as fault trees. This is a top down deductive approach in which an undesirable system failure is analyzed by applying the Boolean logic that combines a series of events at the lower level (Ericson, 1999). The following diagrams illustrate how fault tree analysis could ne conducted:
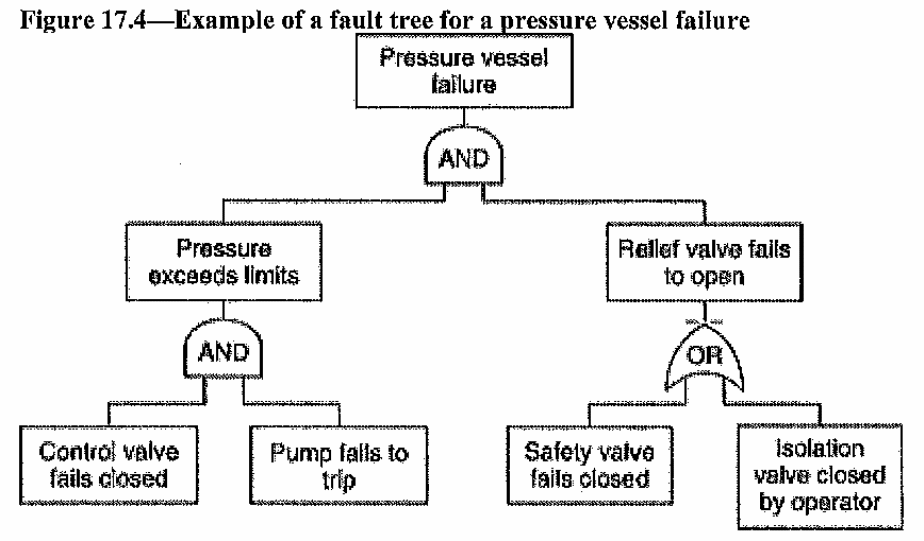
Source: Project Risk Management Guidelines
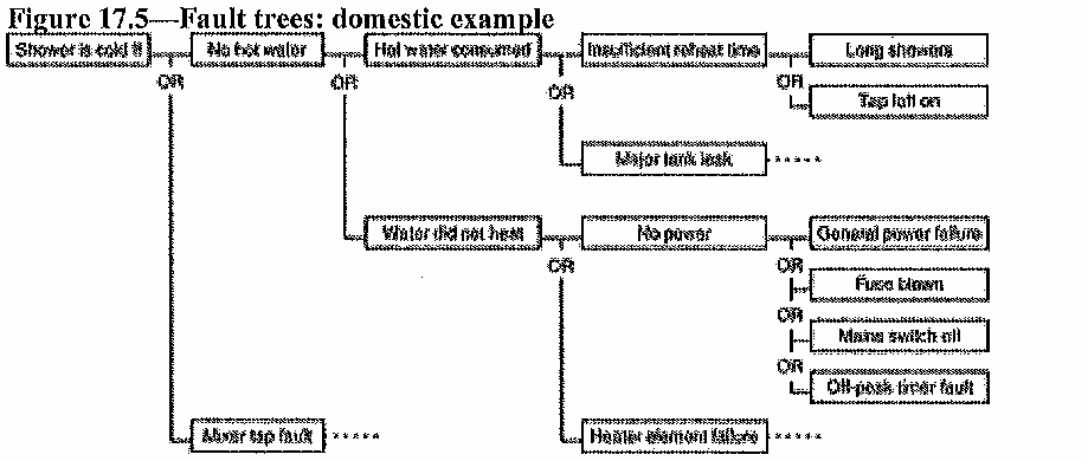
Source: Project Risk Management Guidelines
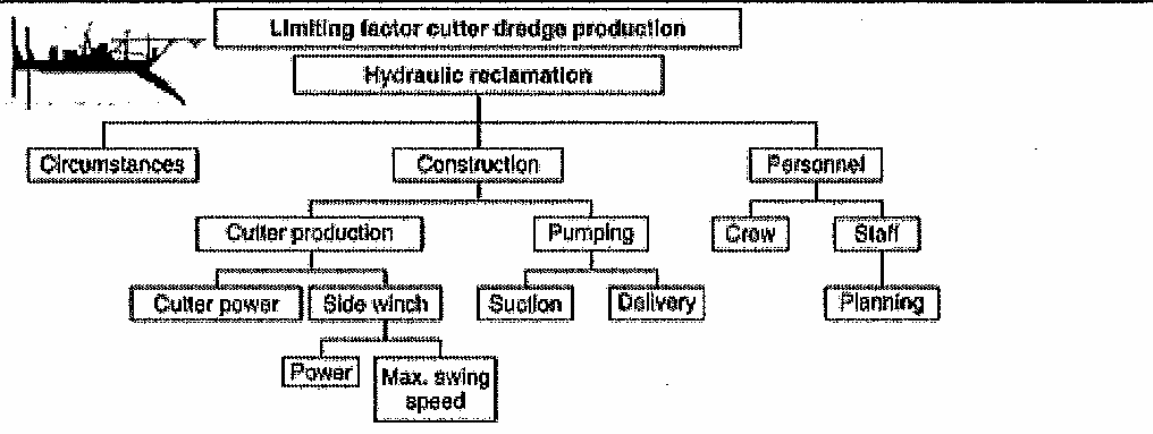
Source: Project Risk Management Guidelines
The next section of this paper examines the fault trees that could be used to manage risks at Empire State Building.
Fault Tree One
The first fault tree that one could consider is the completion and successful handover of the project. When the project commenced, there were certain expectations that the owners had about it. There was, for example, the need to complete the project on time so that it could be rented to people to earn the owners revenue. There are however certain events that could happen along the way that could adversely affect the completion date.
Discussion of Fault Tree One
Delay delivery of materials
One of the factors that could inordinately delay the completion of this project is delays in shipping materials to the site. The company does not manufacture its own materials, and has to rely on external suppliers for these supplies. Among the critical material is cement, steel, and general hardware. These materials can fail to arrive in time because of problems originating from the supplier.
If widows and doors fail to arrive on time, for example, the interior of the building cannot be kept dry during a rainy season. The electricians cannot therefore start wiring the building on time, and this will delay the initiation of other processes that can only be done after wiring.
Other materials that could cause a major delay if they are not brought to the site on time include appliances, cabinets, and other special items. The subcontractor’s schedule can be thrown off balance completely by the late delivery of only one item (RSA, 2011). A delay in the delivery of these materials could cause temporary work stoppage.
The contractor of The Empire State Building could take certain measures aimed at averting this risk. It could, for example, guide the client towards gong for in-stock items. These are items which the supplier already has and will not need to start manufacturing special ones for the client. He could also use suppliers who are reputed to maintain large volumes of local stocks of the required items.
The contractor could alternatively double the estimated time within which the items can be delivered for planning purposes. In case the client feels like placing the order for items himself, the subcontractor would have to specify the exact dates, with a possible buffer, to ensure the items are available when they are needed.
Inspections
Though it is desirable to carry out project inspection on a continuous basis, too much inspection can inordinately delay the completion of The Empire State Building. Conducting inspections when the project is ready or very late within the project cycle can easily cause a delay. This is the same case when inspection is not conducted at all.
Inspection that is done too late could identity an error that may take too long to rectify before the project proceeds. Apart from delaying completion, it may also eat into the financial resources of the organization and interfere with the budget.
Early inspection may not identify sufficient flaws worth fixing, and may just be a waste of time. If inspection is done after the project is completed, flaws of massive proportions could be identified. Fixing them may be quite complex and costly to the client (Loosemore, Raftery, Reilly & Higgon, 2012).
The contractor can take certain measures to prevent unnecessary inspection that could lead to delays in project completion. He must, for example, be able to determine when a given segment of the project is ready for inspection. Once that segment is complete, he could allow for the flaws to be fixed, as he looks at another segment.
A good contractor may need to acquire as much working knowledge and as many skills as possible so that he can assess the progress of various stages of the project. Spending more time with subcontractors would enable the contractor to monitor the progress of their work.
If the contractor fails to inspect, the project may end up taking more time than projected, eat into more of the funds, and necessitate the recalling of the subcontractor. At worst, the stability of the building may be compromised by belated inspections and reworking on an advanced project.
Subcontractor Delays
The completion of the construction of The Empire State Building could be delayed if the subcontractor delays to start or complete any of the phases of the project. Whereas a general contractor may take just a couple of projects to complete at a time, a subcontractor can take as many projects as possible at a time. The events taking place in one of the projects may easily delay work on The Empire State Building.
Subcontractors hold their projects on priority basis, with the highest priority given to larger and more lucrative projects. If a subcontractor holds The Empire State Building project as a low priority project, he may give it less attention as he works on high priority projects. By the time he comes back to The Empire State Building project, massive delays will have been caused.
This risk can be managed by having a contractor who has considerable leverage and clout with subcontractors. A general contractor could use future contracts as leverage (Kendrick, 2003). When a subcontractor knows that securing future projects with the contractor will depend on timely execution of The Empire State Building project, he is likely to allocate sufficient time and resources to its completion.
Contractors could also impose penalties to subcontractors who fail to commence their work on time. This should be spelt out ion the contract, though this clause could scare away many subcontractors.
The best strategy would be for the contractor to get on board only those subcontractors he knows well, whom he understands better, and with whom he will remain in clear and continuous communication about project deadlines.
Client Change of Mind
The shape of the project usually becomes clear once it takes off. The client gets a clear picture of the project and may ask for certain changes to be made, after all, the final product must be appealing to him (National Research Council, 2005).
Similarly, the client is the one paying for the project and any changes he requests for, so long as they will not compromise the quality of the finished product, must be considered. The contractor must however inform the client about the consequences of the changes sought, including late delivery of the project.
The contractor can overcome the risk of the client proposing many or major changes to The Empire State Building by engaging in proactive communication with him before commencement of the project. The contractor could, for example, anticipate the likely changes the client may request for and share them with him advance.
The contactor could also share with him the time and cost considerations if such changes are to be effected.
The contractor should make the client understand that implications of apparently minor changes because they could massively alter the design and reengineering of the building, demand for re-filing of documents with the municipal authorities, besides necessitating the reordering of more materials. All these will consume time and money.
The contactor could also explain to the client the chain effect of some of the changes he may request for. He could, for instance, tell the client that moving a window from one position to the other could position could necessitate the recall of the electoral or plumbing subcontractor who may work with their own schedules.
The contractor could also avoid massive and time consuming alterations by working with a good designer well versed with construction technology.
Both of them will have to think through the project before commencing it. A firm agreement could then be made with the client before the project commences, complete with a signature. This may not necessarily rule out any changes, but spell put clear mechanisms under which such changes may be effected.
Weather
Weather could be another event in the construction of The Empire State Building that could pose serious risks. Weather changes may not be as predictable as meteorologists may want to.
The client may also not want to delay construction of the building because of unpredictability in weather patterns. If, for example, a heavy storm comes and makes it difficult to continue with construction work, there will be need to stop the work and wait until such a time as the weather will calm. The weather could also delay the delivery of construction materials from other far flung regions.
Flooding could for example interfere with transport channels and delay the delivery of building materials. Snow, storms, rains and other weather elements can interfere with the ability of workers to report on duty on time. This interference could easily delay the timely completion of the project.
The risks associated with weather can be mitigated in a number of ways. Work could be scheduled so that outdoor projects are done when the weather is fine, while indoor jobs could be done when the weather is not conducive for outdoors activities.
Though there could be delays, they will not as extreme as they would be if unfavorable weather patterns found most of the outdoor jobs incomplete. Pouring of concrete could, for example, be problematic if done in frosty conditions. This could be overcome by having it done during warm seasons to avoid delays. Painting could be messy if done in humid weather, so this should be done when the weather is less humid.
If outdoor jobs are to be done in severe winter, then the contractor may need to cover his work using super-structures, which may be costly. The cost-benefit analysis may have to be carried out to establish the viability of this option. Generally, the contractor will need to plan and take account of the unexpected weather patterns before commencing the constriction of The Empire State Building.
Accidents
Accidents are another form of risk that could cause delays on the completion of the project. If sky boys fall from the tall building while fastening the steel frames, other workers are likely to stop working so as to mourn the dead.
Getting replacement may also take time because of the risks involved. Other accidents could involve broken limbs, motor accidents, among others. Investigating such accidents could take a long period, within which work will have been stopped.
Accidents could be addressed using a number of measures. Employees could be given protective gear to reduce their exposure to accidents. These include helmets, gumboots, and overalls, among others. Special facilities such as hooked boots could be used by the sky boys as they maneuver to fasten the steel frames. Elaborate health and safety standards and policies should be put in put in place.
Employees should be taken through elaborate training sessions to reduce their exposure to accidents. Those who are unfortunate enough to fall victim could be taken care of by the company to restore faith among the employees. Adequate compensation packages could also be given to the victims.
Work Stoppage
Workers could also constitute a risk to the completion of The Empire State Building. Employees may have grievances over a number of issues at the work place.
Such issues include poor payment, frequency of accidents, and insensitivity on the part of the contractor, among others. Such employees may choose not to report on duty, or report but engage in a go-slow.
The contractor could avert the risk of work stoppage by ensuring employee health and safety standards are put in place to protect employees from accidents. He could also ensure the employees are paid well so that there is harmony among them. Supervision could be done in a manner that motivates employees so as to keep them stimulated to come on duty without cases of absenteeism acting as delays to the completion of the project.
Fault Tree Two
The second fault tree associated with The Empire State Building is the safety measures. The mere fact that the building is one of the tallest in the word makes it a potential safety hazard (Djoen, Santoso & Takayuki, 2003). The magnitude of safety risks are such that they can have serious impacts on the people, the building itself as well as the environment.
Under fault tree two, a number of safety factors will be considered, and how the contactor could go about managing them in the course of the construction or thereafter, what the users and owners of the building could do reduce their effects.
Fire
Fire is a major threat to structures, more so, high-rise buildings like The Empire State Building. Fire can cause the death of individuals residing within the building, or destroy part or the entire building. Fire can be sparked by a number of agents. A common one is an electric fault when electric appliances malfunction, or when there is a power surge that messes up the wiring system.
The Empire State Building could also face the threat of fire arising from the use of highly inflammable materials in its construction.
People who smoke cigarettes within the building and fail to dispose the glowing filters in an appropriate manner or those who smoke in places with highly inflammable substances could also pose a threat. If the building is constructed without proper fire exits and warning systems, fire could become a major threat to its safety.
The risk posed by fire could be reduced by the contactor if he puts certain measures in place. In the first place, the contractor could opt to use materials that are not very flammable. This will reduce the surface area that could ignite fires when a glowing object comes into contact with them.
The subcontractor dealing with electrical fittings would have to be supervised keenly to ensure stability of the connections so that no section of exposed wires comes into contact. High quality materials would also have to be bought. Fuses would be used in most places to cut out connections incase wires come into contact. Warning signs would be put in very strategic places to warn people not to smoke in open places.
Smoking zones will be designed for smokers in sections of the building which are less predisposed to inflammable materials. Automatic fire alarms and sensors will be installed to warn people in the event that fire breaks out. Fire extinguishers will be put at strategic places where people can easily access and use in case there is a fire outbreak (RSA, 2011).
Safety manuals will be printed and placed in every section of the building where users can easily access and read them. Escape routes will be included in the design of the building and clearly marked. These measures, among others, will help reduce fire-related risks in The Empire State Building.
Earthquakes
The earthquake is a natural phenomenon that poses a major risk to high-rise buildings, including The Empire State Building. The height of the building makes it a likely target. The situation is compounded by the fact the New York City does not have any policy on the use of constriction materials and technology that can absorb the effects of earthquakes.
Secondly, most of the structural elements that are meant to absorb the impact of earthquakes are the same ones that are meant to provide support to the structures against gravity. If they are messed up by the earthquake, the entire building could collapse.
The effects of earthquakes can be dealt with by using heavy or reinforced concrete in most of the structures. There will be the need to avoid lean structures and glass slabs that are known to provide a good panoramic view (Harrison & Lock, 2004). Safety will have to take center stage, while matters of aesthetics will take the back burner. This is not, however, to mean that the building will be one monolith of concrete.
Materials and Workmanship
The materials used in the construction of high rise buildings such as The Empire State Building could pose a major risk if they are not carefully sourced and used. Some suppliers could supply low quality materials to maximize their profits and minimize the costs. If used without verifying the quality, there is the possibility of compromising the safety of the building by use of substandard materials.
Some vital components such as the steel frames could also be prefabricated in a manner that compromises their strength and therefore, safety of the building. If the people working on the project do not have the requisite technical knowhow, the manner in which they put the steel frames and other materials together may be shoddy.
Lack of commitment on the part of the supervisors may lead to a situation where poor workmanship and faults pass unnoticed and uncorrected. If the workers are not experienced and knowledgeable enough, they may not be able to identify substandard materials brought to them (Edwards & Bowen, 2005).
Generally, using poor quality materials and poor workmanship could be a major security risk to the construction The Empire State Building.
Airplanes and other Flying Objects
The height of The Empire State Building exposes it to risks associated with flying objects such as airplanes. If such a plane losses control and crashes into it, the consequences could be grave. The magnificence of The Empire State Building makes it a target of terrorist groups that may want to punish the United States of America for reasons best known to them.
If they hijack and crash a plane into the building as happened with the World Trade Centre, the consequences could be catastrophic. Flying objects like birds could also mess up the building, though their impact could only be reduced to nuisance value.
The contractor would have to advise the client to install technological gadgets that can detect and warn users of any impending impact between the building and a foreign object.
If possible, he may have to invest in buying missiles that have the potential to sense if a foreign and potentially risky airplane is coming to crash into The Empire State Building and if possible intercept and neutralize it, even if it means destroying it together with its occupants. This will save the building together with its innocent occupants from destruction.
Evacuations
It is not in doubt that The Empire State Building, at 103-storey, is still one of the tallest buildings in the world. This makes it a risk in itself in case of emergencies. At times, incidents such as outbreaks of fire or other security threats may call for urgent evacuation of people to safety.
It is scaring to imagine how somebody on the 103 floor can run to safety when a fire breaks out, or when there is a security warning. Matters could be made more complicated for the disabled.
This threat could be countered by including elevators, lifts, and broad staircases. Elevators will be quite handy when there is need for evacuation during fire incidents. There could also ne sufficient passages that can allow the use of wheelchairs for the disabled.
Lifts must be in good working condition at all times, and if possible, with adjustable velocity bottoms to increase the frequency with they move up and down in emergencies.
The building must have emergency power generators to power the elevators in case other sources of power malfunction. There will be need to install a good communication system by means of which people in the building will be given instructions, information, and warning in case of emergencies (Royer, 2001).
Conclusion
From the foregoing, it is not in dispute that the kind of risks that could face The Empire State Building are many.
Whereas some of the risks outlined in fault tree one could arise in the course of project execution, others outlined in fault tree two could arise when the project is complete and in use. Irrespective of the timing of the risks, there is need for the client, contractor, and subcontractors to work together and put in place sound risk management strategies.
References
Djoen, S., Santoso, S.O., & Takayuki, M. (2003). Assessment of risks in high rise building construction in Jakarta. Engineering, Construction and Architectural Management, 10(1), 43–55.
Edwards, P., & Bowen, P. (2005). Risk Management in Project Organizations. New South Wales, NSW: UNSW Press.
Ericson, C. (1999). Fault Tree Analysis – A History. Proceedings of the 17th International Systems Safety Conference. Web.
Harrison, D., & Lock, D. (2004). Advanced Project Management: A Structured Approach. London: Gower Publishing Ltd.
Kendrick, T. (2003). Identifying and Managing Project Risk: Essential Tools for Failure-Proofing Your Project. New York, NY: AMACOM Div American Mgmt Assn.
Loosemore, M., Raftery, J., Reilly, C, & Higgon, D. (2012). Risk Management in Projects. New York, NY: Taylor & Francis.
National Research Council (U. S). (2005). The Owner’s Role in Project Risk Management. Washington, DC: Academies Press.
Royer, S. P. (2001). Project Risk Management: A Proactive Approach. Houston: Management Concepts.
RSA (2011). Risk Management Guidelines. Royal and Sun Alliance Insurance Publications, 2(12), 102.