DMAIC Methodology
Define
Measure
In the measure phase of the DMAIC approach, the issue is refined further, and possible root causes are identified. A fitting tool for accomplishing this is the cause-and-effect diagram, as shown in Figure 1.0 below (Junqueira et al., 2018). The image shows four likely causes which may contribute to the delay of the delivery of new aircraft. They include quality control, rework of defects, production bottlenecks as well as a temporary shutdown of production. Study reveals that the aviation industry is currently in the recovery stage from the COVID-19 pandemic (Kovalchuk, 2022). This means that the associated shutdowns and production bottlenecks, which were temporary, have already started to improve. Therefore, this project seeks to focus on the rework of defects and quality control as areas of improvement since they are internal processes that may continue to affect productivity.
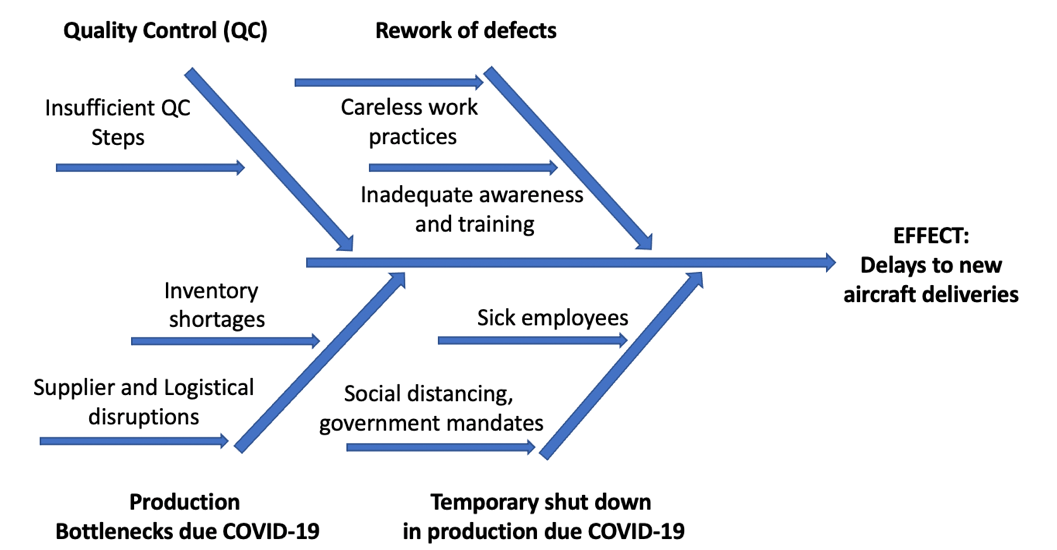
Looking at the financial statements of 2020 and 2021, it is clear that there is a drop in revenue when comparing the fourth quarters of both years. According to Bombardier (2022), on the one hand, the company recorded in millions of U.S. dollars, six thousand four hundred and eighty-seven in 2020. According to Bombardier (2022), on the other hand, it recorded in millions of U.S. dollars, six thousand and eighty-five in 2021, which is a six percent drop.
Analyze
Reworking the defects is one of the main causes of delays in the delivery of new aircraft to customers. This can happen as a result of inadequate awareness and training and careless work practices. Majority of the defects occur due to the lack of motivations which can be due to particularly carelessness and forgetfulness (Ramamoorthy, 2007). In the aviation industry, it is important that the final product, which is the aircraft, to be at its best.
There is a reason why there are so few recorded accidents when it comes to air transport and it is due to firms’ commitment to produce the best since human life is dependent on that. Therefore, when there are defects realized, they have to be fixed, which takes time. Lack of enough training can result in defects in the final product. This can happen in any industry but when it comes to the aviation sector, companies are more careful and, thus, have to rework to ensure the faults are eliminated.
Another main cause of the delays in delivery of new aircraft is inefficiency in quality control. The QC system has the processes to guarantee that every maintenance work complies with the procedures outlined in this GMM to ensure that the aircraft is safe to be used by humans (Kovalchuk, 2022). When this process is delayed or has issues, the delivery will most definitely delay since a particular level of quality is needed before the product is availed to the customer.
Another of the delays in the delivery of new aircraft include production bottlenecks due to the COVID-19 pandemic. With the coronavirus still a threat and numerous countries in lockdown in 2021, the disruption to the supply chains proved severe. Top leaders in the aviation industry had to make rapid decisions and take actions immediately to sustain operations in order to serve clients, customers and communities. As it may be easier for companies in other industries, it is not in the aviation sector.
Improve
To help improve the situation when it comes to the rework of defects, it is important that the company considers further training of its employees. Human resources being the essential resource in the company, needs to be equipped in a manner that productivity is high as there are few or no errors. When the workforce is declared as properly trained, it will be near impossible to experience defects after the final product is released. This will thus reduce the amount of time spent on the rework process and therefore prevent delays. Additionally, the firm should ensure that the workers are well supervised to reduce the rate of carelessness that may result in defects at the end of the process. Lastly, the company needs to ensure that the quality control steps are properly followed (Kovalchuk, 2022). All these steps will be key in Bombardier fulfilling its obligation to the customers which in turn improves their satisfaction. This will be aimed at preventing the customers from purchasing aircraft and other services from competitors.
Control
To witness an improvement in the last quarter of 2022, the company will have to monitor the work performance of employees throughout 2021. Those that register a low score as compared to the standard or average will be fired and replaced. Individuals that remain will undergo compulsory training for at least three months. The course will focus on the various operations according to their lines of work at the organization. The management will employ experts in quality control that will work close with the other staff. Their main role is to ensure that final product released for the market meets the demand of the customers.
Project Plan
Stakeholder Register
A stakeholder register refers to a project document with relevant data concerning the project stakeholders. It is responsible for identifying individuals, groupings or organizations that have interest in the outcome or project. These are the most important individuals in terms of what the company is trying to achieve. In this case, these are the people that focused and observant to the creation of measures that will improve the situation at Bombardier. The aim of the file is to record who is affected by the project and their impact on it. It will become an essential tool towards planning, formulation of the team, developing, defining success criterion, governance, communications, and describing duties and responsibilities. To increase the possibility of success of a project, it is important that this document is created early as it assures that engagement from people involved is available. Some of these people include the management of the aircraft company, the customers, and the workforce such as experts in quality control, technicians, and trainers.
Input into the document will come from various sources, including the sponsor, senior management, business case, research, experts in the industry, and interaction between stakeholders. The project manager will be responsible for the creation of the stakeholder register. The latter needs to be reviewed by the team, business analyst, sponsor as well as project owner for correctness and completeness. The manager will start by filling out the document during the initiation with a high level list of stakeholders as well as any data that may be known at the moment. This is critical as it ensures that the proper collection of individuals will be invited to the project meeting. During planning, more information might be added to the register.
Study will be conducted with the intention of understanding project stakeholders by reading any documentation as well as speaking to the project sponsor and other people. The artifacts library will be an information resource to investigate similar activities by other companies within the industry. The next step will be to complete the register with information from the sponsor and applicable stakeholders. For accuracy and completeness, the document will be reviewed before being uploaded to the repository. Through the entire execution, the review will be done for any alterations in the stakeholder impact particularly in the event there are modifications in the requirements. After the preliminary list is identified during the initiation of the project and approval of the charter, the first meeting will be scheduled. The list of the individuals involved will be utilized to guarantee the right people or groupings are contacted and participate in forming the team.
Scope statement
Even prior to the project manager developing a detailed plan and the team executing the plan, it is important that every individual understands what work should be done and its importance. This is where the scope statement will come into play in this case. It offers an in-depth description of the tasks that ought to be accomplished to deliver the outcome on time and within the allowed budget. The document as well places the aims of the project as well as its output which is the product that the firm is releasing to the market for its customers. Bombardier will add more suppliers to decrease production bottlenecks, strategically increase inventory to reduce the bottlenecks and assess production task planning to create more significant efficiencies. Additionally, it will train technicians to better the standards and outputs, add quality control to alleviate re-work, and increase production capacity to meet the demand.
Risk register
A risk register is a documentation that contains every of an organization’s known risks, the possibility and effects of one happening. It as well defines the actions the company is taking to prevent such and the individuals responsible for the management of the circumstances. It is useful since it enables one to store all of the risk data in a single and easily accessible location. Its consistent and simple format makes it easier for others to comprehend the available information presented and to offer feedback.
Essentially, a risk register specifies the manner in which the team commits to managing the known risks and people for doing that. It is one part of risk management, that is, the practice of finding potential risks early, analyzing them and establishing measures to minimize them. It is important to keep track of every risk, analysis, intentions concerning the risks, and more. Many companies already have the processes as well as risk registers. It is worth noting that risk management is the identification, analysis and removal of hazards and subsequent risks that threaten the firm’s viability or a project.
Schedule
In project management, this refers to listing a project’s activities, milestones, and deliverables. Resources and dependencies are often defined for every task, then start and finish dates are approximated from the budget, resource allocation, scheduled events, and task duration. It is commonly utilized in project planning and portfolio management parts of the whole process. The elements that it contains are closely related to the work breakdown structure and statement of work.
It can be described as a calendar that connects the activities to be accomplished with the resources that will facilitate. It is a main part of the project plan utilized in showing the organization of how the work will be achieved, commit individuals to the goal, determine needs in terms of resources, and used as a checklist to ensure all tasks are done. Prior to the creation of the schedule, a work breakdown structure will be availed to the maker alongside effort approximate for all activities and resource list. In the event the components for the schedule are inaccessible, they can be created with a consensus-oriented approximation technique such as Wideband Delphi.
The following will need to be completed to ensure development of a project schedule: project scope, task dependencies map, sequence of activities, critical path analysis, tasks grouped into phases, and project milestones. To guarantee a healthy schedule, the project team will have to consider certain criteria. For instance, it should be updated continuously, the Estimation at Completion value needs to be equal to that of the baseline and the remaining effort be properly distributed amongst team members. The structure may follow closely and include citations to the index of WBS, suing templates or decomposition to define the actions required to produce the deliverables in the work breakdown structure. It may be evaluated for the quality of the schedule development and that of its management.
Cost estimates
Estimating the costs in project management is the procedure of predicting the fiscal as well as other resources required to accomplish the tasks within the project scope. It accounts for all elements needed for the project and computes a total amount that determines the budget. As a design project continues, it is common for teams to produce numerous estimates during the initial design, detailed engineering as well as tendering stages. The finished project estimates become more correct as the level of the work increases. Professional firms throughout the world have established good practices for cost estimation and they will act as examples for this project.
They utilize a 5-level approach or system of cost estimate classifications. Moving up the hierarchy, the classes of estimates become more increasingly detailed and dependent. Obviously, every class as well needs more completed deliverables and effort. To produce a correct estimate, the team will use more than one of several tools. They include a historical cost database and unit prices, stick estimating, an estimation software, labor costs, and market trends. Cost estimates will allow the company to identify whether the project needs to happen or when. This is important since there are already other plans concerning the firm’s expansion into other countries by establishing new plants in those countries.
Communication Plan
A communication plan, in project management, refers to an outline of how one will communicate relevant and critical, as well as ongoing project data to main stakeholders. In this case, it will aid the team members in understanding who needs to be getting what notifications and when to consult stakeholders. Communication is an important part of avoiding conflicts that may arise as a result of failure of one party not knowing what to do at a particular time. Since the project involves many individuals as it is a multinational organization, it is essential that clear communication lines be established. For instance, among project team members, a policy should be set that whenever an issue arises, the supervisor who is the manager, is informed. It would be inappropriate for the senior management to be consulted before the one responsible for the team.
Summary
Many companies were affected by the COVID-19 pandemic, but none felt the impact more than those in the aviation industry. Since various governments wanted to reduce the number of cases of infections and deaths, they decided to stop the flights into their nations. This then meant that air transport was closed until a solution to the pandemic was found. Bombardier was among those that were greatly impacted as the rate of delays with regard to the delivery of new aircraft became high. This in turn, resulted in less revenue in 2021 than the previous year in the last quarter. This project aimed to identify the root causes, find the solution and implement it. Continued customer dissatisfaction can lead to them purchasing or consuming from competitors.
Reference List
Bombardier. (2022). Financial reports. [online] Web.
Junqueira, V.S.V., Nagano, M.S. and Miyata, H.H. (2018) ‘Procedure structuring for programming aircraft maintenance activities’, Revista de Gestão. Web.
Kovalchuk, J.A., 2022 ‘Post-Lockdown flights: new strategies for civil aircraft manufacturers and airlines’, In post-COVID economic revival, Volume II (pp. 131-141). Palgrave Macmillan, Cham. Web.
Ramamoorthy, S. (2007). Lean Six-Sigma applications in aircraft assembly. [online] soar.wichita.edu. Web.